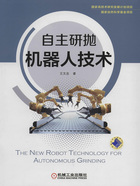
1.1 应用机器人技术精整加工大型自由曲面的背景
进入21世纪以来,对于大型自由曲面零件的加工要求越来越高,如曲面模具、航空镜头及航空发动机叶片等。其中模具成形具有优质、高效、低成本的特点,世界模具市场需求潜力巨大,因此模具制造已成为各工业发达国家制造业中举足轻重的行业。在机械、电子、轻工、汽车、纺织、航空航天等行业得到了广泛的应用,并承担了这些工业领域中60%~90%产品零件、组件和部件的加工生产。在模具的整个制造过程中,各工序工作量所占比例依次为:设计约11%、制造约52%、型面的精整加工约占37%[2]。模具型面的精整加工工作量大,而且是决定模具和制件质量的重要因素,对产品和模具本身寿命影响极大。据统计,模具型腔表面粗糙度改善一级,模具寿命可提高50%[3]。因此,加速研发高精度大型模具自由曲面精整加工技术是必然的趋势。
目前,通过前期的数控加工方法可以实现大型模具自由曲面的自动化形状加工,但是为了获得预期的表面质量,加工后的表面都需再经过平滑加工(Smoothing)、研磨(Lapping、Grinding)或抛光(Polishing)等光整加工工序。当前大型自由曲面精整加工技术的发展落后于曲面形状加工技术,由于大型自由曲面精加工的工艺环节自动化程度相对较低,常常还需依靠耗费大量工时的手工操作方式来完成表面研磨(Lapping、Grinding)或抛光(Polishing)。在美国、日本和德国等发达工业国家,总工时的37%~42%被用于精密模具曲面的手工研磨或抛光加工,在我国达到了50%以上。手工研磨或抛光加工过程中,形状精度与加工质量的一致性差,且效率低下,与降低制造成本、缩短生产周期、提高质量等要求的矛盾越来越突出,模具制造过程中的薄弱环节与发展瓶颈主要集中在对大型自由曲面的精加工阶段。目前,进口模具约占国内市场总量的20%左右,40%以上中高档模具依靠进口。因此研发具有自主知识产权的大型自由曲面精加工技术与装备的需求越发迫切,特别是针对大型、精密、复杂、长寿命的模具生产需求。
目前若干利用机器人技术的研究成果已应用到模具自由曲面研磨或抛光加工的自动化制造领域。出现了各种新颖的研磨或抛光方法、开发了各种实验装置,进行了机器人研磨运动规划、磨削干涉检验、研磨工艺与控制策略及控制算法的研究等[4-6]。
为了实现大型自由曲面的研磨或抛光加工自动化,在对不同加工对象的待加工区域实现加工时,应用传统的数控机床或一般工业机器人技术,必须依靠大型研磨或抛光加工设备。由于机械设备结构增大到一定程度后,其精度、刚度、响应速度、稳定性和动力等方面的问题难以解决,因而大型自由曲面研磨或抛光系统的研发进展缓慢。
另外,如何使固定加工范围的加工系统适应待加工工件尺寸的变化,即如何提高加工系统的柔性,也是一种需要解决的难题。