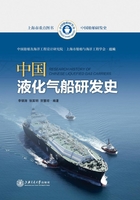
四、建造液化气船需解决的技术难题
1)需将气态碳氢化合物液化后运输
不论是石油气还是天然气,在常温下都呈气态,用船来运输常温下的气体,即使用压力容器运输,气体体积也仅缩小与压力相似的倍数,因此运输量极为有限,经济效益也较差。将其转变成液体来运输,体积将大大缩小,从而大大提高石油气和天然气的装载运输量。发展液化气运输首先要将石油气和天然气液化。
石油气和天然气的液化过程不是一蹴而就的,随着制冷技术的发展,首先可以被液化的是沸点-10摄氏度左右的碳四及-40摄氏度左右的碳三类石油气;其次是沸点-104摄氏度左右的碳二类乙烯气等;最后是沸点-163摄氏度左右的甲烷气体。在制冷技术发展过程中,还利用了在加压条件下石油气的沸点(液化温度)升高的特性,从而降低了对制冷设备的制冷要求,实现了石油气的液化。因此,首先发展起来的是全压式LPG船,然后才是半冷半压式LPG船。当然除制冷技术外,制造出能够耐低温及超低温的液货舱舱壁材料,且保证其具有不泄漏的完整性也是一个难题,这需要冶金技术和焊接技术的发展来解决。
1845年,著名科学家,电磁学奠基人迈克尔·法拉第首次成功地将常压下的甲烷气体冷却到-163摄氏度,使其变成液体。这是一个重要的发明,在理论上证实了随着制冷技术的进步,液化气的大规模工业化生产将成为可能,也使LNG跨洋过海用船来运输成为可能。
1917年,美国西弗吉尼亚州建设成世界上第一座LNG试验工厂,1941年美国俄亥俄州的克利夫兰建成第一座商用LNG工厂,拉开了LNG运输的序幕。在制冷技术进步的推动下,全冷式的LPG船和-104摄氏度的LEG船也相继出现,接着在1959年第一艘-163摄氏度液货舱的LNG船也研制成功,随后,各种新型LNG船也相继诞生。
综上所述,液化气船的发展与掌握液化气的特性息息相关,特别是要掌握液化气的低温特性并攻克其低温储存技术。LPG中液态丙烷、液态丙烯和液态乙烯的舱内最低温度分别为-42.8摄氏度、-48摄氏度和-104摄氏度,而对于LNG而言,舱内液货温度将低至-163摄氏度。对于液化气船的发展来说,这种逐渐降低的储存温度可以说是拦路虎。对于整个运输链来说,将石油气和天然气液化还仅是第一步,液化后温度和压力的保持,易燃易爆特性、一些货物的毒性和污染性的掌握等也是在液化气船发展中需解决的问题。液货舱内的货物蒸气压力因温差和晃荡而不断升高,晃荡引起的局部应力过高还会引起液货舱破损,发生液货泄漏事故。这些也都是液化气船设计时必须考虑并加以解决的问题。
2)与低温有关的问题
除全压式LPG船外,LPG和LNG运输是将液态货物在低温状态下装入液货舱中,运载温度很低,特别是LEG和LNG,这就带来了一系列要解决的问题。
(1)货物蒸发气再液化问题。作为货物的LPG和LNG在船运输途中往往有部分因受热或晃荡等因素变成蒸发气,蒸发气量不断增加,会使液货舱压力升高,产生超压危险,因而需将货物蒸发气加压并冷却,或直接冷却到沸点以下,使其转变为液态才能安全运输,这就是货物蒸气的再液化基本原理。
液化气船液货舱内的储运温度往往远低于0摄氏度,与外界常温的巨大温差和海上航行时舱内液货晃动都会引起液货舱内液货蒸发,时间越长,累积的蒸发气就越多,液货舱内的蒸气压力随之也不断升高,甚至达到液货舱的安全阀设定值,造成货损。所以必须要有与运输货品的沸点温度相适应的制冷技术、制冷设备或其他能处理货舱内蒸发气的设施,以便将液货舱内外界热量传入而自然蒸发出来的货物蒸汽(BOG)处理掉。再液化装置是将货物的蒸发气从液货舱中抽出,再液化后回输至液货舱内进行储存的装置。再液化过程是一个逆正常传热的过程,必须掌握专门的再液化技术,配置必要的设备,对全冷式和半冷半压式液货舱内的温度和压力进行控制。特别是对超低温的乙烯气体、甲烷气体的再液化,消耗的能量大、技术难度也高。
(2)液货舱材料的耐低温。低温环境要求液货舱密封层(屏壁)的金属材料具有耐低温的性能。这就需要找到一种既经济,又易于加工的金属材料,它不但能在液货的沸点温度以下的超低温条件下有足够的力学性能而不会发生损坏,还能解决或通过加工成适当的结构形状来解决低至-163摄氏度的超低温和常温之间巨大的温差而导致热胀冷缩的变形问题。
(3)防泄漏。液货舱的屏壁,不能有任何缝隙,以免泄漏出来的超低温液货与船体结构构件接触,造成其冷脆损坏。一般的船体结构构件,在过低温度下力学性能会下降变脆,船在风浪中航行时,就会发生断裂损坏。因此,液货舱的密封层结构(屏壁)的制作或层数必须要保证低温液货不会漏泄而导致船体结构受损。
(4)液货舱隔热保冷。液货舱的隔热层要有较强的隔热能力,尽可能地减少环境对舱内的热量输入,以控制舱内液货的日蒸发量。对LNG货品,由于液货舱-163摄氏度左右的低温与外界环境温度(夏季大于35摄氏度)的较大温差,外界热量就会传入液货中(或液货的冷量传到外部空间和船体结构材料上),液货的温度就会升高而导致液货蒸发。液化气船与油船不同,货油可与船体结构直接接触,而液化气必须要装在耐低温的专用金属容器中,还要在容器外包覆一定厚度的绝热材料,这种绝热材料要有较好的绝热性能,以控制液货舱和外界之间的热传导,设计时要考虑并计算出这一内外传递的热量。绝热层还要承受一定的负载,如液货和绝热材料自身的重量,船舶在波浪中航行时液货晃荡的冲击力等。
(5)低温液货舱对周围环境温度的影响。由于温差的存在,热量的传递是不可避免的,液货舱内部的液货还是会以一定的速率蒸发,设计时就要考虑液货的日蒸发量不能太大。日蒸发率大,产生的自然蒸发气量就大,需要蒸发气处理设备的容量就大,能耗也随之增大,同时船上需要更大的空间布置这些设备。在运载过程中,还有一定的冷量向周围传递,时间一长,船体内部舱壁上的温度会降低,当相邻的压载舱装载压载水时,就得考虑舱壁温度的降低是否会使压载海水结冰膨胀而导致压载舱舱壁胀裂。
(6)液货舱的热胀冷缩。液货舱储存运输液货时处于-163摄氏度左右的低温,液货舱装货预冷前,液货舱的温度为环境温度。当船舶在夏季进行首次装货,液货舱的温度几乎就是环境温度,如35摄氏度,与装货后的-163摄氏度形成一个约200摄氏度的温差,这个温差对用不锈钢或一般的金属材料制成的液货舱而言,每米长度伸缩2毫米左右,一个长度为30~40米的货舱,伸缩量就是60~80毫米,这样的伸缩量足以使液货舱结构损坏,所以液货舱的结构(包括独立式液货舱的基座结构)的设计和材料的选用必须解决热胀冷缩带来的变形问题。
在设计时除考虑上述因素外,在正常装载工况时,也需注意冷缩问题,因液货舱空舱时,舱壁温度相对液货-163摄氏度(LNG)要高很多,短时间内直接将大量LNG加注进去,舱壁的变形既大又快,也会造成液货舱损坏,所以必须将液货舱预冷至一定的低温,这是在管理及营运过程中必须遵守的事项,设计必须将预冷的要求和过程做出明确规定,预冷时的温度降必须保持一定梯度,严禁短时间内的骤降。
(7)蒸发气利用。对于LNG船,为解决舱内液货不断蒸发和蒸发气积累造成液货舱内蒸气压力升高的问题,可用再液化装置将蒸发气液化,但需花费大量的能量。如果超压蒸发气直接排放至大气会造成比二氧化碳更严重的温室效应,因此在早期的LNG船上,将蒸发气用于船上锅炉的燃料,锅炉产生蒸汽推进蒸汽轮机(透平)运转,从而提供船舶行进中的动力;近年来新型的LNG船上将蒸发气送至双燃料柴油机作为燃料,产生动力或电力供船舶使用。作为燃料使用时,液货舱内的蒸发气,需加压升温后通过专用管路送到机舱。虽然蒸发气是气体,但其温度与液化气一样也处于低温状态,且又是一种易燃易爆的危险气体,所以在设计时,必须准确地计算出蒸发气的产量和利用率,同时还要考虑输送管路的耐低温性能、泄漏防护与检测,以及安全保护问题。
(8)密闭舱室中货品的沸点温度与压力特性。液化气的沸点温度(即液化温度)与压力有关,压力越高,液化温度越高。例如,丙烷在大气压下的沸点温度为-42.8摄氏度,在45摄氏度时饱和蒸气压力为1.5兆帕,即它在大气压下以液态储存于液货舱内的温度为-42.8摄氏度,在外界温度45摄氏度情况下,液货温度可达45摄氏度,比加注时升高了约90摄氏度,这一温差使液货舱内蒸发气大量产生,在此温度下,货舱内的压力最高升高到1.5兆帕。这样大的温差和压力对液货舱的结构强度也会产生不利影响,因此在设计时,必须考虑所装载的不同货品的压力与沸点的关系,并考虑最恶劣的工况。
综上所述,解决低温问题,就是要解决液化气的安全储运的问题。在液化气船的发展历史过程中,曾出现过一些不同结构形式,承受不同温度和压力,不同液货舱材料和不同隔热材料的货物围护系统,都是为了解决液化气的安全储运问题。
3)液化气的易燃、易爆特性
LPG和LNG的热值较高,以LNG为例,1千克LNG的燃烧发热量约为11 950大卡,与1.25千克柴油相当。因此,LNG的一个主要用途是作为燃料使用,因其气化后易燃易爆,如使用不当,危险性也大。按液化气的热值计算,一艘17.4万立方米的LNG船,如果发生爆炸,它释放出的热量约是100万当量TNT
烈性炸药释放的热量。按美国在第二次世界大战后期投放日本的原子弹约2万等级TNT当量计算,那就相当于50个原子弹释放的热量。对于液化气船的设计和建造,安全是放在首位的。液货舱的结构和管路阀门连接都不能泄漏;所有内含液化气的部件及设备,如液货泵、货物压缩机、加热和气化设备等,在工作时也不应有泄漏,更不能让液化气进入气体安全区域,或进入有明火作业的区域以及运转时存在电火花的设备区域。在运输和使用过程中还必须遵守安全规定和程序。如装货前,液货舱内是常温,容纳的还是含氧量约21%的空气,如贸然把大量-163摄氏度的液化气加注进液货舱,不但液货舱的结构会因瞬时巨大的温差而损坏,而且液货蒸发产生的蒸发气与含氧丰富的空气混合还会形成极具爆炸危险的混合气,一旦发生爆炸,将造成船毁人亡,巨额的资产顷刻将化为灰烬,同时船用燃油的泄漏也会给海上环境带来不可逆转的污染。
在液化气船的设计、建造和营运时,无论是舱室和设备的布置,液货舱和设备管路的泄漏检查试验,液化气装卸时的操作程序等,都须牢记液化气是一种极具危险的易燃易爆气体。
4)毒性和污染性
液化气既具有易燃易爆的危险,又有污染大气的问题。如甲烷是比二氧化碳还严重的温室气体,其温室效应是二氧化碳的20多倍;有些LPG还具有毒性,溅入皮肤或眼睛会引起皮肤疾病和眼睛损伤,这就需在船上配置相应的毒性探测设备和冲洗设备;具有毒性的LPG进入大气和水中会引起大气和水体污染。
5)液货舱和系统运行参数的监视和控制
因为液化气过低的温度和过高的压力都会对液货舱结构造成损坏;液化气与空气混合成一定比例后,达到爆炸极限,遇到明火或电火花就可能会爆炸;部分LPG货物蒸发气还有一定的毒性,一旦泄漏,后果严重。所以船上管理人员及操作人员必须牢牢掌控液货舱及相关设备与管路中的温度、压力和液位等,同时还应监测船上相关处所的可燃气体和有毒气体的含量等,一旦出现异常情况,必须迅速找出原因,及时修复,防止事态扩大。如液货舱内压力升高,达到设定值时,液货舱安全阀就会自动开启,超压的货物蒸汽就会通过安全阀排入大气,一方面造成了大气污染,另一方面造成了货损。
为保证液货舱的安全并避免不可控的货损,在液货舱安全阀开启以前,船员可以通过船上配置的货物处理系统设备来控制液货舱温度和压力,如通过再液化装置将液货舱内过量的货物蒸发气抽出并液化冷凝后,通过液货舱内顶部的喷头喷入达到给液货舱降温降压的目的;或通过气体燃烧装置直接将液货舱内过量的货物蒸发气抽出升温后燃烧来降低液货舱内的货物蒸气压力;还可以将液货舱内的蒸发气抽出,加压升温后供给机舱内的燃气发动机或锅炉作为燃料使用,从而也达到了使液货舱恢复正常压力的目的。对一些沸点较高的液货,还可以直接将液货舱内的液货抽出直接冷却后回输至液货舱内,达到降温降压的目的。因此,为了保证船舶的安全性以及提高货物运输过程中的经济性,需要对液货舱内的液位、温度和压力等物理参数和相关设备及管路工作状态进行实时监控,确保液货舱各项参数、设备及管道的运行参数都在设定值范围内。
相关参数的监控分为远程监控和现场监控。现场监控以就地仪表以及手动控制阀门为主,而远程监控是通过具备远程传输功能的传感器及仪表将信号传送至控制室,控制室根据信号的运行范围来调节系统中的调节阀或遥控阀,从而实现对设备及管道的远程控制。当然,部分设备出于对自身的保护以及保证正常的工作状态的需要,也可能会设置自动控制功能,进行自控。所有这些传感器及仪表以及控制的逻辑关系,都应符合IGC规则和相关船级社规范的要求,这样才能确保所有液货舱、设备及管路都正常安全运行。
上述监控主要是对航运中的船舶,对靠泊码头或进行LNG加注的液化气船,对船和码头,或两船之间的位置移动也必须监控,以防止位置移动过大,造成加注臂或加注设备的损坏。