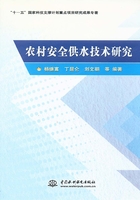
第二节 高氟水处理技术及设备
一、除氟吸附材料研制
(一)粉末颗粒状吸附剂开发
本研究采用的动床吸附法也可称为采用混凝工艺的吸附法,其实质是通过填料床的截留作用,使粉末吸附剂与混凝剂的混合药剂在反应器中的停留时间延长,具体数据取决于吸附剂粒度和填料床特征,正是由于吸附剂颗粒被截留在吸附床中,使得吸附剂浓度和停留时间与吸附剂的吸附曲线相适应,从而更充分地利用吸附剂的吸附容量,大幅减少粉末吸附剂的消耗量。投加粉末吸附剂的除氟工艺具有材料选择范围广和吸附剂无需再生的优点。
1.粉末吸附剂的选择
根据吸附剂的氟吸附容量和吸附平衡时间,可将不同粉末吸附剂分为高效吸附剂、中效吸附剂和低效吸附剂,廉价粉末吸附剂通常是一些低效和中效的吸附剂,不同粉末吸附剂的吸附性能总结见表3-2。图3-1显示了不同吸附材料在吸附性能上的差异。
表3-2 粉末吸附剂的吸附性能及特点

动床吸附法除氟工艺中使用的粉状吸附剂,其选用原则是不需经过复杂处理的廉价材料,使用后弃置,不需再生,可省去再生工序和费用。因此,重点考察了20余种吸附容量在0.2~4mg/g之间的相对廉价吸附剂。表3-3列出了常见及近期研究较多的吸附剂、吸附容量及运行最佳pH值。其中,红砖粉状、煤粉、膨润土、红壤和硅藻土等粉状材料的吸附容量为0.2~4.0mg/g,属于相对廉价的除氟材料。经对比分析,选择了煤粉和膨润土作为除氟吸附粉末。

图3-1 磷灰石、萤石、石英+铁、方解石、石英吸附时间对吸附平衡的影响
表3-3 除氟剂及除氟性能

续表

需要指出的是,大多数除氟剂的性能数据是在“标准”条件下、采用“自配高氟水”测出的,然而,真实的高氟水是“不标准的”,因而,除氟剂除氟性能数据只有采用当地高氟水进行现场测定才具有足够的可信度。除了需要适应当地的水质条件外,除氟剂的应用效果还与除氟剂的形态和采用的除氟装置有关。此外,采用粉末吸附剂的除氟方法对药剂的特别要求是:投加方法简单可靠,当吸附剂饱和后易于从水中分离。
2.含廉价粉末除氟剂的净水剂——HX115型净水粉
HX115型净水粉源于清华大学与南京军区联合研发的LYH-16型快速净水粉,该净水剂主要用于野外水源净化。针对低浓度(<3.0mg/L)高氟水的特点,利用当地廉价粉末原料的水处理药剂,采用市售混凝剂与廉价粉末吸附剂复配的HX115净水药剂,从原料卫生性、稳定性、储存性、除氟/除砷性能、投药性能、分离性能、加工性能、经济指标等八个方面研制出适用于农村的新型净水粉。
水处理剂由除氟吸附剂、混凝剂、稳定剂组成。吸附剂采用膨润土、煤粉和沸石粉,粉末细度在200目以上,用于吸附去除水中的氟化物和微量有机物,吸附剂占药剂重量的50%~75%。混凝剂采用聚合氯化铝,混凝剂的作用是将水中的胶体微粒凝聚成较大颗粒的矾花,以利于沉降和在填料上附着,混凝剂占药剂重量的20%~35%。为使净水剂能够长期储存,并确保药剂在溶药期间水解程度低,药液中的吸附剂和混凝剂不发生混凝沉降反应,可加入适量的稳定剂,稳定剂占药剂重量的5%~15%。复合型除氟药剂的制造方法是,将上述原料粉碎至规定粒度,除湿后按重量比例和规定次序将各组分均匀混合,密封包装。
本研究中,将LYH-16型快速净水粉中的致浊剂替换为膨润土等除氟粉末,并重新优化了配方组成和比例,保证了净水剂原料的卫生性、长期储存性、加工性能、经济性等指标,是一种性能价格比较高的新型水处理药剂。
3.粉状吸附剂加药方法
净水剂可采用干式和溶液两种投加方法。干式投加法需使用专用的粉末加药器,该法的优点是药剂直接投加,省去配药池和搅拌器等设备,并且可利用药剂中混凝剂入水后产生的初生态微小絮凝体对氟的有效吸附能力,提高除氟效果。但是,由于XH115净水剂中配有混凝剂,而混凝剂具有吸潮性,在现场环境多变的条件下,净水剂的吸潮现象严重,致使加药器内部的混凝剂凝结成块,以致无法使用,因此,尽管干法投药具有多种优势,但混凝剂吸潮导致的问题限制了该法的使用。
本研究采用的净水剂湿法投药法则是将药剂配成2%~5%浓度的浆液投加,净水药剂在溶药配药时要具有化学稳定性,否则药剂在溶药槽中发生水解反应,使吸附剂性能降低。由于药液中颗粒物较多,采用螺杆泵或蠕动泵可实现稳定加药。
4.吸附剂分离
填充截留材料的粉末床吸附工艺通常在反应器中填充空隙率较大的轻质材料,如浮性塑料微珠或纤维成型体材料,使得吸附剂细颗粒被截留附着在填充材料的巨大表面上,延长了吸附剂在水中的停留时间,理论计算显示,当吸附剂的停留时间为水力停留时间的5倍时,吸附剂的吸附容量利用较为充分,通过空气反冲可排出吸附饱和的吸附剂细颗粒,这种截留吸附法国外称之为吸附澄清法(Adsorption Clarification Process),事实上,该法利用了动态的粉末吸附剂形成吸附剂动态床层,故而称为动床吸附法更合理。
5.粉末吸附剂的动床吸附法除氟工艺原理
根据图3-2的物料平衡可计算得到吸附停留时间T与水力停留时间τ的关系。

图3-2 物料平衡示意图
在T时间内(T=T1+T2),CiT=CeT1+CdT2,得:

在T1时间内,,得:

计算后可绘制运行过程参数曲线,见图3-3。

T为吸附剂达到90%吸附容量的时间,若按粉粒吸附剂的θ设计吸附池,则水中粉粒吸附剂浓度低,与水中氟离子的碰撞几率小;水力停留时间长,池容积大,经济性差。T1(充气间隔时间)和T2(充气时间)的取值依吸附剂特性参数θ和填充床水力特性确定,T1增加,则吸附能力利用率增加,但吸附池运行状况取决于填充床水力阻力;图3-3 运行过程参数曲线的控制由填充材料的比表面积、填充密度、容积均匀性以及填充床充气搅动时间决定;
依吸附池操作方式(T2和T1)的不同可分为多种方式,例如:每周期排出10%~20%的循环间歇充气方式,或饱和吸附后的完全反冲模式。利用截留细微颗粒的吸附能力净化水质的动床吸附工艺在工程上有多种实施方法,但将此法用于水的除氟还是首次。
(二)赤泥除氟复合絮凝剂
对于利用赤泥作为吸附剂去除水中污染物,国内外研究主要集中于去除水体中金属离子,而无机物去除方面多集中于砷、磷等。对于饮用水中常见污染物氟的吸附研究较少。赤泥是铝土矿在拜耳法溶出过程或烧结法熟料在溶出过程中产生的残渣。赤泥中含有活性组分,如铁、铝、钛等,很多研究将赤泥作为吸附材料来治理污水和废气,但通常赤泥都需经过改性处理以提高吸附能力。
1.试验原料及制备方法
试验原料采用铝酸浸液和赤泥。铝酸浸液中铝含量(以Al2O3计)约为13%,pH为1.7左右的酸性黄色液体。赤泥为灰白色固体,烘干研磨过80目筛筛分。其主要成分(以金属离子表示)见表3-4和表3-5。
表3-4 铝酸浸液的主要化学成分

表3-5 赤泥主要化学成分(wt%)

采用两种方法制备三种赤泥絮凝剂:①取浸出液原液200mL放入500mL三口烧瓶中,加入赤泥70g(<80目)室温下搅拌40min,然后将烧瓶移入水浴锅中,于80℃下加热搅拌4h;②以不加热的方法再制备一种絮凝剂;③取浸出液稀释一倍后的稀液200mL放入500mL三口烧瓶中,加入赤泥40g(<80目)室温下搅拌40min,然后将烧瓶移入水浴锅中,于80℃下加热搅拌4h。考察加热后制得的絮凝剂除氟效果。
2.赤泥改性聚铝除氟效果
三种絮凝剂的除氟效果见表3-6。
表3-6 铝酸浸液+赤泥除氟效果

由于原液+赤泥+80℃加热4h后制成的絮凝剂溶出较多,产生胶凝现象,将其稀释20%,呈流态化防止相变。将原液+赤泥+80℃加热4h后制成的絮凝剂稀释25倍;原液+赤泥不加热制成的絮凝剂稀释30倍;稀液+赤泥+80℃加热4h后制成的絮凝剂稀释15倍,分别投加不同量于200mL用氟化钠配成的3.5ppm的水样中,投加4.5mL絮凝剂溶液(原液+赤泥+80℃加热4h),初始pH影响见图3-4。

图3-4 不同初始pH除氟效果
由图3-4可见,原液+赤泥稀释30倍投加4.5mL(折合成未稀释絮凝剂用量为0.75mL/L)即可使上清液氟浓度低于1.0mg/L,折算后需消耗AlT48.6mg/L和Ca33.1mg/L。这几种赤泥溶液处理效果区别不大,沉淀性能很好,絮体破碎后恢复能力强,且pH=6.0~9.0时都能取得较好效果。
3.聚合氯化铝(PAC)溶液除氟效果
试验采用大港油田AlT=3.7125mol/L(其中Ala=36.5%、Alb=34.79%、Alc=28.7%)PAC溶液和膜蒸馏的AlT=0.2mol/L(其中Alb=85%、Alc=10%)高纯PAC溶液。将第一种PAC溶液稀释25倍,第二种PAC溶液原液投加不同量于200mL用氟化钠配成的3.5ppm的自配高氟水中,除氟效果见表3-7。投加2.5mLPAC溶液于不同初始pH的自配高氟水中,pH对除氟效果影响见图3-5。
表3-7 不同PAC溶液除氟效果


图3-5 pH对除氟效果影响
由图3-5可见,两种絮凝剂投加2.5mL即可使上清液氟浓度低于1.0mg/L,折算后需消耗AlT=3.7125mol/L(其中Ala=36.5%、Alb=34.79%、Alc=28.7%)的PAC溶液50.0mg/L(以AlT计)和膜蒸馏后AlT=0.2mol/L(其中Alb=85%、Alc=10%)的PAC溶液67.5mg/L(以AlT计)。膜蒸馏的高纯PAC虽使Alb含量增加但并不能加强除氟效果,说明铝盐除氟电中和作用并不是主导机理,铝盐与氟主要发生协同沉降或吸附反应。絮体沉淀性能较好且破碎后恢复快,但pH范围稍窄,在7.0~8.5之间。
4.石灰+硫酸铝溶液除氟效果
准确称取0.28gCaO溶于100mL水中配成2.0g/L(以Ca计)石灰溶液;准确称取4.9377gAl2(SO4)3·18H2O溶于100mL水中配成2.0g/L(以Al计)硫酸铝溶液。分别投加20mg/L和30mg/L石灰溶液(以Ca计)于200mL氟化钠配成的3.5ppm的水样中,然后分别投加不同量硫酸铝溶液,除氟效果见图3-6。

图3-6 不同絮凝剂(硫酸铝溶液)投加量除氟效果
由图3 6可见,投加20mg/LCaO溶液 (以Ca计)效果较好,投加3.0mL硫酸铝溶液即可使上清液氟浓度低于1.0mg/L,折算后需消耗30.0mg/L硫酸铝 (以AlT 计)。硫酸铝溶液的作用是水解生成的Al3(OH)45+、Al7(OH)174+、Al13O4(OH)247+等高价阳离子与F-发生协同沉降或吸附反应。当水中SO42-、Cl-等阴离子浓度较高时,由于存在竞争作用,会使Al(OH)3矾花对F-的吸附容量显著减少。投加石灰+硫酸铝溶液浊度较大,沉淀性能不好,污泥较疏松,且投加过量CaO溶液改善除氟效果不理想,会增加絮凝剂硫酸铝溶液的使用量,还会使出水pH不达标。因为石灰乳溶解度较小,有许多Ca(OH)2微细颗粒,反应生成的沉淀物CaF2会包裹在Ca(OH)2 颗粒表面,使之不能被充分利用,造成石灰乳用量大。另外除氟效果受氟化钙的溶解度大小限制。
通过对比这三种除氟絮凝剂的效果可知,铝土矿酸浸液+原赤泥溶液处理效果好,沉淀性能很好,絮体破碎后恢复能力强,且pH=6.0~9.0时都能取得较好效果。虽然经折算消耗AlT和Ca量也较多,但其中Ca基本来自赤泥中的溶出成分,AlT也有部分来自赤泥溶出成分,大大降低了药剂成本。
以活性赤泥与PAC絮凝剂酸化复合,制备了新型高效复合聚合铝除氟絮凝剂,通过强化絮凝回流初生态铝絮体,可使5ppm的含氟水稳定降低到1.0mg/L以下,药剂费用仅0.2元以下。
以活性赤泥酸化中和氯化铝,制备了廉价易得的新型赤泥除氟吸附剂,对水中氟吸附容量高达92mg/g,是传统活性氧化铝的吸附容量6~8倍(活性氧化铝在pH=5.0和pH=7.0的最大吸附量分别为16.5mg/g和12.1mg/g)。
(三)改性赤泥吸附剂
本节以赤泥作为原料,利用其中所含的金属氧化物制备除氟吸附剂,并考察其除氟效能,包括时间、投加量、pH等因素对除氟效果的影响。
1.材料与方法
(1)铝改性赤泥制备。实验用赤泥为烧结法赤泥,其主要化学成分分析结果见表3-8。常温下向1mol/L AlCl3·6H2O溶液中加入经烘干12h、研磨、过100目筛后的原状赤泥粉末,中速搅拌(300r/min)条件下,控制体系最终pH=3,慢速(150r/min)搅拌24h。将此赤泥悬浊液缓慢加入到1mol/L的NaOH溶液中,直至该碱液体系pH降到7~8后,静置12h后离心得固体,将其置于马福炉中焙烧2h,焙烧温度为200℃,研磨过100目筛备用。图3-7是原状赤泥与铝改性赤泥的能谱分析,通过对比,很明显看出吸附剂表面的铝含量显著增加。
表3-8 烧结法赤泥(原状赤泥)主要化学成分及质量百分含量

(2)含氟离子模拟水配制。称取1.105g NaF溶于1000mL超纯水中,配成500mg/L的NaF储备液,采用超纯水稀释至所需浓度并实测。以0.01mol/L的NaCl作批次实验的电解质溶液。以1mol/L HCl和1mol/L NaOH调节溶液pH。

图3-7 原状赤泥与铝改性赤泥能谱分析图
(3)静态吸附实验。取所需浓度的含氟水溶液于250mL具塞锥形瓶中,以0.01mol/L NaCl 作批次电解质溶液,投加500mg/L制备好的铝改性赤泥吸附剂,在25℃恒温条件下以150r/min的速度振荡1h,静置沉降,取上清液用离子色谱仪测定溶液中氟离子含量。单位质量吸附剂除氟量Q以式(3-3)进行计算:

式中:Ci为初始溶液中的氟浓度,mg/L;Ce为平衡时溶液中的氟浓度,mg/L;V为反应溶液体积,L;m为吸附剂质量,mg。
2.试验结果
(1)吸附等温线。选取不同初始浓度含氟溶液(5、10、20、40、60、100、150、200、250、350、450,单位为mg/L)在室温下进行吸附等温实验(吸附剂用量为0.5g/L)。分别考察原状赤泥、铝改性赤泥及焙烧不同温度(200℃、300℃、400℃、600℃、800℃)铝改性赤泥的饱和吸附量(见表3-9)。结果表明,铝改性赤泥和焙烧铝改性赤泥可将原状赤泥对氟的饱和吸附容量从13.46mg/g分别提高到68.07mg/g和91.28mg/g。较传统活性氧化铝的吸附容量提高4~5倍,后者在pH=7.0时的最大吸附量是12.1mg/g。
表3-9 氟吸附Langmuir等温模型参数表

由表3-9可知,经过200℃焙烧改性的赤泥吸附剂,其饱和吸附量有了大幅的增加,但随着焙烧温度的提高,改性赤泥的饱和吸附量又逐渐降低。这可能是由于焙烧挥发了原赤泥中所含水分,并产生了微孔,增大了比表面积,激活表面羟基官能团,进而提高了吸附能力。但温度过高导致赤泥中金属氢氧化物和方解石的分解,造成除氟能力下降。
(2)吸附动力学。不同初始氟离子浓度(3mg/L、5mg/L和10mg/L),控制溶液pH为7~8,吸附剂投加量为0.5g/L,室温下以150r/min的速度振荡,考察200℃焙烧铝改性赤泥吸附剂对氟的吸附动力学(图3-8)。在吸附初始阶段,吸附效能迅速提高,在20min后达到最大吸附量,此后趋于稳定,说明达到吸附平衡。动力学实验表明,氟离子静态吸附动力学方程与准二级动力学方程具有较好的拟合性,准二级动力学方程假定吸附速率受化学吸附机理的控制,其方程为:

式中:k2为准二级吸附速率常数,g/(mg·min);qe为平衡吸附量,mg/g;qt为时间t时的吸附量,mg/g。

图3-8 反应时间对于铝改性赤泥除氟效能的影响

图3-9 准二级动力学方程拟合
利用式(3-4)可定量描述铝改性赤泥吸附剂对氟离子的吸附量随时间的变化关系。结果表明(图3-9),准二级动力学方程能较好地反映该吸附除氟过程,并可推测吸附速率受化学吸附机理的控制。在利用一级动力学方程对实验数据进行拟合时,拟合确定系数R2相对较低,推断此吸附过程在3种不同浓度(3mg/L、5mg/L、10mg/L)下不受扩散步骤控制。
(3)pH对除氟效果的影响。氟离子初始浓度10mg/L,其他条件同上,考查体系pH对吸附剂除氟效能的影响 (图310)。由图310可见,与原状赤泥相比,改性赤泥吸附剂在溶液pH为7~8时达到最佳的除氟效果,改性吸附剂对氟的适宜pH高于原状赤泥,这与前者的等电点高于后者的实验结果相符,参照ζ电位对吸附剂表面电荷的表征 (图3 11)。由图3 11可知,当pH>8时,随pH增大3种吸附剂的吸附量急剧下降,这显然与吸附剂表面带电性有关,在pH>8条件下,吸附剂表面带负电,随pH增大,表面负电荷密度增大,导致对F-的抑制作用增强,因而不利于F-的吸附。但在pH>9条件下,仍有吸附发生,说明电性作用并非是引起该吸附发生的唯一因素。实验利用铝在pH为7~8时形成无定形Al (OH)3 (am)凝胶,与溶液中氟离子发生离子交换反应,而当溶液pH>8时,铝的形态主要以铝酸阴离子形式存在,因而除氟效能有所降低。

图3-10 pH对于铝改性赤泥除氟效能的影响

图3-11 pH与ζ电位变化关系
(4)吸附剂投加量对除氟效果的影响。实验考查了200℃焙烧铝改性赤泥吸附剂的投加量对于除氟效果的影响,初始氟浓度分别为3mg/L和5mg/L,吸附时间为20min,其他条件同上,结果见图3-12。结果表明随吸附剂投加量的增大,氟离子的去除率增大,但单位吸附剂的吸附量却逐渐下降。在初始氟浓度3mg/L体系中,当吸附剂投加量为3g/L时,除氟率接近70%,出水氟浓度为0.69mg/L;在初始氟浓度5mg/L体系中,当吸附剂投加量为5g/L时,除氟率接近87%,出水氟浓度为0.87mg/L,均低于国家饮用水标准要求的1mg/L。
(5)吸附剂的脱附实验。采用NaOH溶液对铝改性吸附剂在室温条件下进行脱附实验,实验结果见图3-13。由图3-13可知,NaOH溶液可以较好地对吸附剂吸附的氟进行脱附,随着NaOH浓度的增加脱附率也逐渐提高,在NaOH浓度达到0.4mol/L时,脱附率可达91.2%,此后随碱液浓度增加,脱附率提高不明显,因此可以选择0.4mol/L NaOH作为脱附剂。
(6)吸附机理。目前研究铝对氟离子的吸附多集中于活性氧化铝对于氟离子的吸附,关于采用无定形Al(OH)3(am)对氟离子吸附作用的研究相对较少。当pH>7时,残留在水中的大部分水解态铝转化成Al(OH)3凝胶沉淀微粒,同时吸附在胶体表面的单体或低聚态会发生进一步的水解—沉淀反应,最终结果是在胶粒表面形成氢氧化铝的凝胶沉淀包裹层。

图3-12 吸附剂投加量对氟吸附去除率和吸附量的影响

图3-13 NaOH对氟脱附率的影响

图3-14 吸附量对平衡pH的影响
有研究表明,氟离子在Al (OH)3 (am)的吸附过程是离子交换过程,释放的OH-会增加溶液pH。当pH>7时,Al (OH)3 (am)的溶解度随pH的上升而增加,因此研究其吸附作用时需要考虑pH和Al (OH)3 (am)含量的变化。通过测定反应后溶液pH变化进一步验证以上反应机理,以铝改性赤泥吸附剂做不同吸附量及反应后溶液pH测定实验,初始pH均为7±0.2,吸附剂投加量为0.5g/L,平衡时间24h,结果见图3 14。从图3 14中可以得出在初始pH基本相同的条件下,溶液的平衡pH随吸附量的增加而增加,在投加了0.5g/L铝改性吸附剂的100mg/L高氟水溶液中,经过吸附平衡后,体系pH由初始pH=7上升到pH=7.9,虽吸附过程导致溶液pH略有升高,但仍在中性范围内,该结果进一步验证了上述反应机理。
(四)负载型稀土吸附材料
稀土金属的水合氧化物具有较高的吸附阴离子的能力,吸附处理对象主要为水中F-、、
等离子。有研究表明,锆盐对氟的去除效果较好。二氧化锆是唯一同时具有表面酸性位和碱性位的过渡金属氧化物,同时还有优良的离子交换性能及表面富集的氧缺位。本节研究以壳多糖生物聚合物为载体,制备了负载水合氧化锆的氟离子吸附剂,并通过静态和动态试验研究了该吸附剂的适宜pH、剂量效应、动力学性能和持续利用性能。
1.试验材料与方法
(1)材料和仪器。材料:水合氧化锆吸附剂,NaOH(氢氧化钠)、HCl(盐酸)分析纯;仪器:便携式氟离子比色计,78型磁力搅拌器,FG2型pH计。
(2)试验方法。试验原水为河北省邢台市清河县自来水,其氟化物浓度为3.72mg/L。
1)pH静置试验:原水500mL,吸附剂添加量为1g/100mL,调节pH=2.0~10.0,静置4h、8h后测定溶液中氟化物浓度,并测定平衡pH。
2)pH动态柱试验:两个有机玻璃柱规格均为φ25×500mm,分别装填吸附剂100mL,其中1号柱调节原水pH=3.0,2号柱调节原水pH=6.5,均以SV20/h流速过柱,通水方式采用上进下出,吸附过程连续运行,测定出水氟化物浓度。
3)剂量-效应试验:分别取6个烧杯,各添加原水500mL,调节pH=3.0,吸附剂添加量分别为0.5g/L、1g/L、2.5g/L、5g/L、7.5g/L、10g/L,静置24h后测定溶液中氟化物浓度,中间过程中轻微搅拌3~4次。
4)吸附动力学试验:容量为1.5L的烧杯,添加原水1L,调节pH=3.0,吸附剂添加量分别为1g/L,室温、磁力搅拌器搅拌条件下,在不同的时间间隔取样测定溶液中氟化物浓度。
5)低pH下动态柱吸附-脱附试验:有机玻璃柱规格为φ25×500mm,装填吸附剂100mL,调节原水pH=3.0,SV20/h流速过柱,通水方式采用上进下出。吸附过程连续运行,测定出水氟化物浓度。在上述试验结束后,为清洗吸附剂表层悬浮物,使用去离子水以SV120/h速度反冲洗10min;脱附采用1.6%NaOH溶液以SV5/h的速度淋洗60min;脱附之后使用去离子水以SV5/h的速度水洗60min,继而使用0.2%HCl以SV5/h的速度清洗60min,再使用去离子水以SV5/h的速度水洗30min,重新开始吸附过程。

图3-15 pH静置试验
2.试验结果
(1)不同pH下的吸附效果。pH作为实际运行过程的指标之一,对吸附材料的实际应用起着决定性的作用。研究吸附剂在不同pH条件下运行效果,对于吸附材料的推广应用有重要的实际意义。
1)pH静置试验。不同初始溶液pH情况下,吸附剂的吸附容量变化情况见图3-15。由图3-15可见,当pH=3~10时,吸附剂随着pH值的增加,吸附容量逐渐降低,表明吸附剂较适宜在酸性环境运行;当pH<3时,吸附效果有所下降;在pH<6.0时,静置时间由4h增加至8h,可以显著提高吸附效果;当pH>7.0时,增加静置时间未能提高吸附效果,部分静置8h后吸附容量反而低于静置4h吸附容量,主要原因是吸附剂吸附原水中其他离子而置换出氟离子。
2)pH动态柱试验。调节原水pH=3.0和pH=6.5情况下的试验结果见图3-16。调节原水pH=3.0时,吸附剂的吸附效果较pH=6.5时大大改善,穿透BV由500提高至3200,穿透吸附容量由2.43mg/g提高至11.14mg/g。说明吸附剂对于pH依赖性较强,适宜在偏酸性环境下运行。调节原水pH=3.0时,吸附曲线有波动,出水氟含量较低的点均为午间所取样品,主要原因是温度因素影响吸附剂的吸附能力;午间温度稍高,提高了吸附剂的吸附效果。

图3-16 不同pH情况下运行效果
(2)剂量-效应试验。吸附剂添加量对于除氟效果的影响见图3-17和图3-18。由图3-17可见,随着吸附剂量的增加,溶液平衡氟浓度逐渐降低,吸附剂添加量在0.5g/100mL时,溶液平衡氟浓度可降至1.0以下,添加量在0.75~1g/100mL时,吸附逐渐达到平衡;由图3-18可见,随着吸附剂量的增加,氟去除率升高;由于吸附剂量的增多,可接触的吸附表面积增大,致使更多的氟离子被吸附。

图3-17 吸附剂剂量与平衡氟浓度的关系

图3-18 吸附剂剂量与氟去除率的关系
(3)吸附动力学试验。吸附剂的动力学性能是表征吸附能力的重要参数之一。吸附剂的吸附动力学曲线见图3-19。
由图3-19(a)可见,在起始阶段,氟吸附速率较快,并在300min左右达到吸附平衡。用伪二级动力学方程对吸附动力学试验数据进行回归分析:


图3-19 吸附剂吸附动力学曲线
式中:Qe为吸附剂平衡吸附量,mg/g;Qt为吸附剂t时刻的瞬时吸附量,mg/g;k2为吸附速率常数,g/mg/min,当t→0时,为一常数。
分析结果见图3-19(b),因变量y代表,自变量x代表时间t,相关系数R2大于0.99,表明吸附剂的吸附动力学符合伪二级动力学模型,具有良好的动力学吸附性能。
(4)低pH下动态柱吸附—脱附试验。在原水氟浓度为3.72mg/L的条件下,调节pH至3.0,控制SV20/h,连续3次吸附—脱附—再吸附运行,结果见图3-20。

图3-20 吸附剂氟吸附穿透曲线
由图3-20可见,连续3次运行吸附效果无衰减趋势,其出水氟浓度达到1mg/L时的BV值分别为3200、4180、4860,其穿透吸附容量和相应的脱附率见表3-10。由表3-10可见,吸附剂3次吸附—脱附—再吸附的穿透吸附容量分别为11.14mg/g、16.10mg/g、18.98mg/g;除第1次脱附率为84.6%外,其他脱附率都大于90%。
表3-10 吸附与脱附容量

试验结果表明吸附剂最佳适宜pH=2.0~4.0,吸附速率较快,平衡时间短。原水氟化物含量为3.72mg/L时,吸附剂添加量为0.5g/100mL,即可将溶液中氟化物浓度降至1.0mg/L以下,并且具有良好的吸附动力学性能;在pH=3时,试验的三个周期中,吸附能力未见衰减现象,脱附率都在84%以上,最高可达100%,并具有良好的洗脱性能,可多次重复利用。试验表明,水合氧化锆吸附剂是一种快速、高效、稳定的除氟剂。但是,在目前情况下,由于对于原水pH要求较高,尚难以用于高pH的饮用水除氟。
(五)微波辐射法制备吸附剂
活性氧化镁除氟剂具有原料易得的特点,采用高温煅烧工艺制造的活性氧化镁,特点是生产能耗高、煅烧耗时长。与高温煅烧工艺相比,微波煅烧制备工业活性氧化镁具有煅烧时间短、煅烧过程易于控制和节省能耗等技术优势,但微波煅烧法制备的活性氧化镁是否具有除氟活性尚未见报道。本节研究微波煅烧碱式碳酸镁制备活性氧化镁除氟剂的方法,掺加活性炭以强化微波加热效率,通过XRD和SEM进行理化分析考察微波煅烧工艺特点,研究产物的除氟性质和除氟容量,进而制备活性氧化镁与活性炭混合的粉末状除氟剂。
1.研究方法
(1)制备原理。制备原料为碱式碳酸镁,其热分解反应为:

上述反应为吸热反应,需要提高温度以保证分解,热解温度可通过监测加热过程中反应物的重量随温度的变化情况确定。微波加热是指材料在外加电磁场中由介质损耗而引起的体加热,优点是升温速率快、加热均匀,尤其适合加热极性材料。对于碱式碳酸镁等弱极性材料,直接在微波场中处理难以使物料温度升高,需要加入强极性材料作为敏化剂,以便在短时间内使混合物料加热升温。

图3-21 微波加热装置示意图
1—微波功率显示仪;2—温度显示仪;3—热电偶;4—物料;5—刚玉坩埚;6—保温材料;7—刚玉坩埚;8—微波腔体
(2)材料与方法。碱式碳酸镁和粉末活性炭均为分析纯,分析纯NaF加去离子水配制含氟水。微波加热装置由可调功率工业微波炉(0.2~3kW连续可调,频率2450MHz)、刚玉坩埚、保温材料、温度测量显示等部分组成,见图3-21。煅烧原料由2g碱式碳酸镁与活性炭按不同比例配制,用坩埚定量称取原料置于微波炉中,根据原料的热重分析结果设定微波加热温度,考察不同功率条件下的微波加热时间,用XRD和SEM技术分析煅烧产物的微观结构及微观形态,采用烧杯试验法研究含活性炭的活性氧化镁粉末除氟剂的除氟容量。
2.制备条件试验
(1)煅烧温度确定。使用热重分析仪对碱式碳酸镁进行热重分析,考察碱式碳酸镁在温度升高过程中的质量变化和微商热重,结果见图3-22,微商热重表示质量变化速率。由图3-22可知,碱式碳酸镁在170℃左右出现小的失重峰,在263℃质量降至初重的88.48%;在370℃出现大的失重,在453℃时质量仅为初始值的46.50%,表明370~453℃为碱式碳酸镁集中分解温度;在600℃以上失重基本趋于平缓,说明600℃能够保证碱式碳酸镁分解完全。因此,确定碱式碳酸镁的微波煅烧温度应高于450℃。

图3-22 碱式碳酸镁热重分析
(2)敏化剂掺加比例确定。在碱式碳酸镁中掺加活性炭敏化剂的目的是利用活性炭的微波吸收特性以提高煅烧温度,掺加活性炭与碱式碳酸镁的质量比用Ω表示。在微波功率1.5kW时,不同Ω条件下混合物料的升温曲线见图3-23,其中,活性炭的升温曲线在0.8kW微波功率下测得。由图3-23可知,活性炭的微波吸收能力强,在微波功率0.8kW条件下,可在3.5min时升温至1022℃;碱式碳酸镁吸波能力差,最高温度为247℃;对于活性炭和碱式碳酸镁的混合物,微波功率相同时,活性炭比例越大,混合物升温越快且升温值越高。当微波功率1.5kW时,活性炭与碱式碳酸镁质量比为(5~7):8,能够保证混合物料的温度在4~50min的范围内保持在450℃以上。
(3)微波功率选择。Ω=3:4时,不同微波功率条件下,混合物料的升温曲线见图3-24。由图3-24可知,在微波加热过程中,混合物料的吸波升温过程与向外散热过程同时发生,故而物料的温度先急剧上升后缓慢下降,实验表明,微波功率在0.5~2kW均可使物料的温度达到碱式碳酸镁分解温度。
(4)微波煅烧时间的确定。Ω=3:4,且微波功率为0.5kW和1.5kW时,混合物料的除氟容量与失重率随微波煅烧时间的变化见图3-25。在微波加热初期,随着微波处理时间增加,物料的失重率显著增加,对应的产物除氟容量亦增加;在功率1.5kW条件下,微波作用20min时,产物的除氟容量已达11.75mg/g,约为最大值的94%,微波作用20min后,尽管失重率持续增加,但除氟容量变化不大;在0.5kW功率条件下,产物的除氟容量在10min已达到11.74mg/g,并在40min时达到最大值12.89mg/g。

图3-23 微波功率1.5kW下不同Ω条件下混合物料升温曲线

图3-24 Ω=3:4,不同微波功率下混合物料升温曲线
综合上述实验结果,对应于0.5~2kW的微波功率范围,加热煅烧时间应大于20min。
3.除氟剂的理化分析及除氟活性
理化分析和除氟活性测定所用的除氟剂采用下列制备参数制得,Ω=5:8、微波功率1.0kW和煅烧时间20min。

图3-25 Ω=3:4时混合物料的除氟容量和失重率随时间变化

图3-26 不同煅烧时间物料的X射线衍射图
(1)X射线衍射(XRD)分析。物料在不同煅烧时间的X射线衍射图见图3-26。煅烧前,碱式碳酸镁是混合物料中的主要组分;随着煅烧时间增加,活性氧化镁出现并逐渐增加;煅烧20min后,活性氧化镁成为混合物料中的主要组分。随着煅烧时间延长,活性氧化镁的峰强增强,峰高增加,表明活性氧化镁结晶度随煅烧时间增加。对XRD图谱中活性氧化镁进行晶粒大小分析可知,5min、10min与20min煅烧时间下的氧化镁晶粒大小分别为89Å,101Å和148Å。
(2)扫描电镜(SEM)分析。混合原料和煅烧产物的SEM照片见图3-27。由图3-27可知,混合原料和煅烧产物中,颗粒状活性炭和片状镁混合物混合均匀;碱式碳酸镁为松散片状结构,煅烧后除氟剂中的活性氧化镁亦为松散片状结构,二者均具有巨大的比表面积;碱式碳酸镁的形状规整,活性氧化镁边界相对粗糙。
(3)除氟剂除氟容量与原水pH的关系。原水氟浓度5mg/L时,除氟剂除氟容量与原水pH的关系见图3-28。实验结果表明,pH=5~9时,除氟剂除氟容量受原水pH变化影响较小。pH=4.91~9时,除氟剂的除氟容量为13.11~13.29mg/g;pH=7时,除氟剂的除氟容量值最高,为13.29mg/g;pH=9时,除氟剂的除氟容量值最低,为13.11mg/g,二者相差1.41%。若按碱式碳酸镁的失重率为45%计算,则活性氧化镁的计算除氟容量为28.01~28.39mg/g。

图3-27 混合原料煅烧产物除氟剂的SEM照片
二、除氟工艺和设备
(一)吸附法与混凝法组合的高氟水处理成套技术及设备
1.HX115-10型劣质地下水净化成套设备
(1)Trident动床吸附法原型机简介。“三叉戟”(Trident HS)水净化成套设备包含四个工艺步骤,分述如下:

图3-28 原水不同pH条件下除氟剂的除氟容量
1)混合。原水进入处理单元前,加入混凝剂和助凝剂,同时将该单元产生的污泥回流至混凝剂投加口,以促进絮体形成,同时保持系统稳定的固体浓度,降低进水固体浓度的变化。对于一体的强化混凝单元,在吸附澄清池之前设置斜管沉淀池,降低进水固体浓度,将大部分絮体留在斜管沉淀池内。斜管沉淀池延长了停留时间,对低温水处理较为有利。总之,斜管沉淀池可减少剩余污泥产量,同时提高有机物的去除效率。
2)强化混凝。利用轻质材料吸附床进一步处理,轻质材料可选择塑料微珠,吸附澄清池中轻质吸附材料可进一步去除颗粒物,被俘获的颗粒物利用气水联合冲洗定期排出澄清池。
3)过滤。混合介质过滤可进一步去除剩余的颗粒物,介质一般使用无烟煤、石英砂和高密度石榴石。对于改进的过滤系统,滤料的比表面积从下到上逐渐减小,同时采用气水反冲洗,反冲洗出水处设有挡板,以防止滤料流失并保证滤料清洁。
4)紫外线消毒。每个单元均安装有紫外线(UV)消毒系统,可灭活水生致病生物,包括隐孢子虫和贾第虫。与化学消毒剂不同的是,UV消毒不会产生有害的消毒副产物。通过紧凑设计,可以制作占地面积小、采用中压紫外灯并配有控制和监测系统的成套紫外消毒系统。
(2)研制方法。以Trident HS为原型,研制用于劣质地下水处理的成套设备,主要功能包括:去除劣质地下水中的悬浮物、有机物、氟化物、砷、胶质、色度、铁锰、重金属等多种杂质,使劣质地下水转化为生活饮用水,额定净化能力10m3/h。产品采用多项成熟水处理单元技术进行二次集成,预装内置件的罐体组合设备,以方便安装,与水质相适应的预调式自由水面无压运行,以实现操作简便。为降低制水成本,采用一次投药与吸附剂内循环结合的方式,内衬一定厚度的无毒防腐层,延长罐体寿命,便于拆卸和易地安装,可靠性高。
(3)工艺设计与计算。
1)总体设计。水质处理成套设备的主体为4个钢塑复合材料制水罐(槽),配置加药器、空压机、输水泵及电控柜等外部设备。投药方式根据实际运转情况采用水溶液投加;清洗方式采用上一级出水作为下一级清洗进水,辅以气流搅动和反冲洗;全流程以水力控制为主,操作和控制简便。设操作架台以方便投药和日常操作,罐内功能件和结构件随罐体预装后运输,现场安装工作以外设和管道为主;罐体与底座螺栓连接,可整体运输;现场安装可采用整体吊装方式,也可采用分解后就位的二次组装方式。清水罐设水位指示防止溢流,并设在线浊度显示及报警器,确保合格净化水流入清水池。
2)水处理工艺。水处理工艺流程见图3-29。

图3-29 水处理工艺流程
3)工艺参数计算。单元技术参数计算见表3-11。
表3-11 技术参数

4)处理单元设计。由四个单元构成,四个处理单元分别制造,置于同一底座上安装。a.投药混合混凝单元(1号罐)。粉末药剂快速混合后在1号罐中完成混凝,使药剂中的吸附剂与水中有害离子充分接触,充分利用絮凝体的吸附能力。罐体外部侧壁预埋带孔钢板,用于安装管夹,以固定外接水管。罐体外部焊接10号槽钢加固,以支撑罐顶部安装的加药器,罐排空由外接水管路阀门实现。粉末药剂或水溶液投入后与原水在承料方管中混合,自流入混合筒,在搅拌桨作用下快速混合(混凝),含细小絮凝体的出水从罐上部出水口排出。从3号罐回流的部分絮凝体经由下部管口回流至1号罐。1号罐功能图解见图3-30。

图3-30 1号罐功能图解
b.吸附剂动床吸附单元(2号罐)。利用比表面积大的彗星式纤维滤料将混凝后产生的絮凝体和吸附剂细颗粒截留,增加絮凝体与水中杂质的碰撞几率和提高絮凝体对水中离子的吸附量。进水(底部)布水方式采用条缝滤网筒“丰”形布置,并支撑于罐底。出水(上部)配水方式采用拼装式条缝滤网板分隔填料,开槽管集水。罐体外部端壁预埋带孔钢件,用于安装管夹,以固定外接水管。按50kg/m2填装“H形软质863填料”,承托层为模塑条缝滤板,条缝滤板开孔面积与总面积之比大于40%,属小阻力配水系统。滤速4.2m/h。滤板和滤料见图3-31。
通过脉冲供气搅动填料床使部分“老龄絮体”脱落并排出至后续分离罐;脉冲供气的间隔时间和供气时间根据原水性质和絮体性质现场调试确定。空气脉冲搅动填料床使“老龄絮体”脱落,来自空压机的压缩空气流量0.12m3/min,ABS材质尖式滤头布气,气冲强度q=10L/(m2·s)。
c.一次过滤单元(3号)与二次过滤单元(4号)。通过两级过滤,分离水中絮凝体和吸附剂细颗粒。一次过滤采用彗星式纤维滤料,滤速7.2m/h;二次过滤采用活性炭,滤速5.6m/h。活性炭填装方式为活性炭包铺层方式,即将颗粒活性炭预先装入φ80×800mm的网眼布口袋中,清洗后铺装。先后运转试验了多种功能性颗粒滤料:用于去除重金属离子的“转型阳离子交换树脂填充吸附包”;用于去除水中硬度离子的“沸石填充吸附包”;用于去除硫酸盐的“转型阴离子交换树脂填充吸附包”。试验结果显示,颗粒状功能性过滤材料饱和后的再生过于频繁,并且操作难度超出了普通操作工的能力,因此,功能性滤料过滤技术不宜用于小型水处理成套设备。

图3-31 滤板和滤料
d.投药混合系统。粉末药剂投入后与原水在承料管中混合,自流入搅拌混合筒,在搅拌桨作用下实现快速混合。投药装置分干式和湿式两种。干式投药装置由可调式干粉喂料器、承料混合筒、搅拌机和托架四部分组成。干粉喂料器技术参数:储药容积10~12L,一次盛药量7~8kg,投药速率300~500g/h,电机功率(0.18+0.18)kW,380V;混合竖筒直径300mm,长1500mm,容积106L,混合时间30~36s;搅拌机转速160r/min,桨叶φ130mm,电机0.55kW,380V,额定搅拌处理量200~300L;上述3个设备安装在专用托架上,托架与1号罐用螺栓固定。粉末干式投药装置见图3-32。

图3-32 粉末干式投药器
湿式投药选用螺杆泵,投加药剂为HX115型净水剂,由混凝剂和吸附剂复配制成。
e.消毒剂投加装置。采用“定量比例泵”投加,与管道泵串联,定量比例泵型号Dosatron-11GPM,过水额定流量1m3/h,药剂注入率0.2%~2%。消毒剂选二氯异氰尿酸钠,配药液桶选用水处理专用储药桶。
f.外部设备。外部设备包括水泵和空气压缩机。输水泵流量12~15m3/h,型号SJ-50-32-125,功率3kW,外型632×310;空气压缩机排气量0.25m3/min,排气压力0.7MPa,型号Z-0.25/7,功率2.2kW。
g.计量与控制。进水管和加药管设玻璃转子流量计。清水罐水位计为普通型玻璃管水位计,安装在清水罐侧壁。电控柜内安装电度表计量设备用电量。
h.电气控制技术条件见表3-12。
表3-12 电气控制技术条件

(4)模型制作与实体制造。正式设计与制造之前,按照设计构思制作了物理模型,模型材质为6mm层压板,各部分尺寸按1:10制作,经积木式搭装布设后,确定了成套设备的结构与布置方式、运输方法与条件、管道走向及连接方式、操作架台布置、操作要求等。根据模型确定的制造思路,进一步细化设计要求,绘制设备零部件加工图,进行实体制造。罐体为Q235,厚6mm,内衬低压聚乙烯镶嵌层(LDPE),厚12~16mm,在后期设备改造中,3号和4号两个过滤罐改用聚脲弹性体涂层,该涂层采用100%双固体组分,专用喷涂器施工,层厚500~1500μm,卫生安全,防腐效果好。罐体外相应部位预埋钢件,用于安装管架。管道连接采用法兰连接和胶接两种方式。气管路按通用气管连接要求执行,气管路与罐口法兰的连接方法为法兰盲板车螺纹,黄铜接头作为转换接口。管道泵和水力泵的固定采用螺栓固定在罐体预埋件上的方法。敞口罐体上部加装格栅板。二层操作架和扶梯采用预制货架/搁架,现场组装。立式电控柜固定于操作架台上。设备制作、安装和调试见图3-33。

图3-33 设备制作、安装和调试照片
(5)工程实例。山西省襄垣县某村,地下水水质特点是多种超标物质共存。其中地下150m的水质特点是悬浮物含量高、有机物含量高、含氟量高和硫酸盐含量高,并且水中悬浮固体颗粒的比重较轻,地下700m深井水的水质特点是悬浮物含量高和硫酸盐含量高。
工程采用HX-115型复合混凝剂和“高速混凝—动床吸附两段法”除氟工艺。设计处理水量10m3/h,日处理水量200t。工程远期处理水量40m3/h,日供水量1000t,供水系统见图3-34。
1)运转试验系统配置见表3-13。
2)水质净化方法。
a.净化工艺。采用投加粉末吸附剂的强化混凝法。净水剂投入水中后产生微小絮凝体,絮凝体被比表面积很大的填料截留,水中杂质与絮凝体微粒接触碰撞并附着其上,通过后续分离单元将杂质和絮凝体一并除去,可去除水中悬浮物、有机物、氟化物、砷、煤粉、胶质、色度、铁、锰、砷、油类、挥发酚、重金属等杂质,将超标地下水净化为生活饮用水。

图3-34 供水系统示意图
表3-13 运转试验系统配置

b.工艺特点。集成了五项新型水处理材料与技术:净水药剂、水位信号远距离显示箱、新型大孔隙率滤料、高通孔率滤板、配制成浆料的药剂。螺杆泵加药系统具有以下特点:节能式设计,系统压降小;预装内置件的罐体组合式设计,按工艺要求分模块制造;积木式成套设备,比常规净化设施减少占地40%~60%;针对原水水质进行工艺参数预调节,简化日常操作程序。
3)水处理效果及制水成本。
a.水处理效果:工程实施后,采出水中的氟化物含量均小于1.0mg/L。其中,地下150m井下采出水中的氟化物由4.12mg/L降至0.3mg/L,效果非常明显;地下700m采出水中的氟化物则由0.76mg/L降为0.58mg/L,亦有改善。工程净化前后水质改善情况见表3-14。
表3-14 工程净化前后水质改善情况

b.制水成本包括药剂费、电费、人工费和维护费等,合计0.26~0.94元/t。
工程运行情况表明,HX115-10高氟水成套技术及设备可用于“低碱度、高悬浮物、硫酸盐型”高氟水处理及多指标超标水质共存的农村供水工程。
2.HX115-5A型含氟地下水净化成套设备
(1)工艺设计与计算。
1)总体设计。HX115-5A型含氟地下水净化成套设备包含四个水处理单元:投药混合混凝单元、絮体动床接触吸附单元、过滤单元和精滤单元,净化能力5m3/h。1号罐为投药混合混凝单元,2号罐为絮体动床接触吸附单元,3号和4号罐分别为过滤单元和精滤单元。设备结构见图3-35。

图3-35 设备结构图
1—投药混凝罐;2—静态混合器;3—搅拌桨;4—动床接触吸附罐;5—过滤罐;6—出水槽;7—精滤罐;8—气管;9—反洗水管;10—放空管
投药混合混凝单元的功能是实现吸附剂、絮凝剂与水的混合反应,药剂投加到安装在进水管路上的静态混合器中,经快速混合后在1号罐进行进一步混合反应,形成包含吸附剂细颗粒的絮凝体。
絮体动床接触吸附单元的功能是使1号罐来水中的颗粒物附着在2号罐中填充的大比表面积的滤料上,延长吸附剂在水中的停留时间,增加水中氟化物与吸附剂的碰撞几率,提高吸附剂吸附容量的利用率,待吸附剂饱和后或滤床水力阻力达到预定值后,通入空气搅动滤料床层,使饱和的“老龄絮凝体”排出2号罐。
过滤单元和精滤单元的功能是去除水中絮凝体及各类颗粒物,其中,粗滤采用彗星式纤维过滤材料,精滤采用活性炭滤料。
成套设备采用共壁一体式设计与加工方法,材质为钢板涂卫生级涂层,阀门与管道开孔于设备同侧,使得全部操作在设备同侧完成,既减少了占地面积,又便于操作。加药泵为工业级蠕动泵,具有计量准确、可输送含颗粒物药剂的特点。在2号和3号罐上安装透明水位指示管,可随时显示设备各单元的运行状况。反冲洗用水为前级单元出水,即2号罐反冲洗水来自1号罐出水,3号罐反冲洗水来自2号罐出水,成套设备不设反冲洗储水箱和反冲洗水泵,这是本装置的突出技术特点和优点,适合农村水站的管理条件。在设备出水管段设水质观察管段,由有机玻璃加工制成,可实时显示运行的出水情况,亦可用于观察各单元的反冲洗终点。
2)水处理工艺。HX115-5A型含氟地下水净化成套设备的处理工艺见图3-36。

图3-36 HX115-5A型含氟地下水净化成套设备的处理工艺流程图
3)工艺参数计算。药液浓度2%,加药量20~150mg/L,加药泵流量5~40L/h。单元设计参数、管道水力计算、供气量计算分别见表3-15~表3-17。
表3-15 单元设计参数

表3-16 管道水力计算(满流流速)

表3-17 供气量计算

(2)成套装置设计与制造。
1)罐体设计与制造。采用整体式共壁设计,罐体由四个水处理单元构成,共用一个底板(厚8mm),罐体上沿焊接角钢,各单元之间由下部开槽或上部水堰槽连接,罐体上设置总溢流管法兰,罐体外部焊接槽钢补强。罐体材质为钢板(Q235),厚6mm,内壁涂卫生级UNIFLEX 1500涂料(双组分、100%固含量聚脲弹性涂料),外壁涂抗紫外UNIFLEX 1500涂料。罐体一侧设爬梯,以方便安装与维护操作。罐体之上安装气体释放槽,以释放井水减压后的气泡。罐体构造见图3-37。
2)器材与配套设备见表3-18。
表3-18 器材与配套设备

3)电控柜设计资料见表3-19。

图3-37 成套设备的罐体构造
表3-19 用电器一览表

电控柜技术要求:电控柜在地面安装,电控柜外面板安装正常运行所需开关和指示灯,柜内面板设置电器独立控制开关和指示灯等电器。
功能设置:照明开关,独立控制照明灯,接电插座(3孔),用于给各类临时设备供电,电表记电。
控制方式:电源开关和指示灯,接通和断电;输水开关和指示灯,预留接输水泵;溶药搅拌机通电状态下,加药泵开关起作用。搅拌机和空压机均独立控制。
(3)运行方式与调试。HX115-5A型含氟地下水净化成套设备的运行操作特点是可视性好、操作简便。当设备制水时,打开电源开关、给水开关、加药开关(溶药搅拌机自动打开)和搅拌机开关。关闭阀1、阀2、阀3、阀4、阀5、阀7,打开阀6,观察透明管段中出水情况,若出水清澈,符合要求,则关闭阀6、打开阀7,开始制水。
1号罐的清洗。因地下水中的溶解性气体释放,因此1号罐水面上有浮渣,需定期人工清理。
2号罐反冲洗。每运行12h,2号罐反冲洗1次。反冲洗时,打开阀1约10s,关闭阀1,打开控制盘上的空压机开关,同时打开阀3,并观察透明管段中出水情况,若出水清澈,则关闭空气压缩机和阀3,反冲洗结束,重新开始制水。
3号罐反冲洗。每运行12h,3号罐反冲洗1次。反冲洗时,打开控制盘上的空压机开关,同时打开阀2和阀5,观察透明管段中出水情况,若出水清澈,则关闭阀2和阀5以及空压机,打开阀4约10s,待滤床形成后,关闭阀4,重新开始制水。
4号罐炭包整理和更换。4号罐炭包的整理和更换需人工操作。当炭包堵塞或出水水质变差时,停止进水,放出设备内剩余水,更换炭包。放入新炭包后,进行洗炭操作,打开6号阀,关闭7号阀,观察透明管段中出水情况,若出水清澈,则关闭6号阀,打开7号阀,清洗结束,重新开始制水。
(4)工程实例。HX115-5A型含氟地下水净化成套设备的试点工程应用于河北省乐亭县某除氟工程。试点工程简要情况如下:
1)给水水源:自备300m深井。
2)水质情况:浑浊度6~40度,色度(黄)大于160度,氟化物1.89~2.6mg/L,重碳酸盐碱度大于450mg/L,COD为1.56mg/L,pH=8.50。
3)输配水系统:已建有完善的输水管路,并增配2个容积5m3塑料储水桶。
4)水量控制方式:提水端为深井泵通断方式;输水端为恒压变频方式。
5)配置5t/h水净化设备,PU涂层防护,日产水量大于100t,增设了两个5m3的储水桶以满足15t/h的高峰用水。
6)净化方法:动床吸附法净化工艺见图3-38。
7)净化设备:由HX115-5A型改造而成,改造内容包括支撑条缝滤板方式、加药管上附加除渣器、搅拌桨加装消沫器等。净化能力5m3/h,本机功率不大于4.0kW,电压380V。
8)运行费用(按用水高峰季节的日最大用水量估算):药剂费100~150元/d;电费约增5~10元/d,换算成制水成本为1.0~1.5元/t。
运行前后水质情况见表3-20。

图3-38 动床吸附法净化工艺
表3-20 运行前后水质情况

(二)改性赤泥除氟设备
1.强化吸附絮凝除氟设备研制
(1)试剂材料。1号搅拌器转速280~300r/min;2号、3号搅拌器转速50~70r/min;水力停留时间1h。动态试验原水为3.5mg/L的含氟水样。絮凝剂采用赤泥改性PAC溶液,制备方法:取聚合铝酸浸原液200mL放入500mL三口烧瓶中,向其加入赤泥70g,室温下搅拌40min,转速控制在400r/min,制得的赤泥改性PAC絮凝剂作为除氟储备液,将储备液稀释15倍即得使用液。
(2)运行试验结果。
1)赤泥絮凝剂投加量影响。在高密度澄清池中用计量泵分别投加不同量的经稀释的絮凝剂,考察其除氟效果。运行条件:进水流量100L/h(停留时间1h);絮凝剂投加量4.5~12.0mL/L;混凝剂投加1号搅拌器搅速280~300r/min;污泥回流量40%(40L/h);污泥回流2号搅拌器搅速50~70r/min;污泥回流区域为4号回流管。试验结果(图3-39)表明,当稀释15倍的絮凝剂投加量为10.5mL/L时,反应器出水经过滤即可达标。考虑到后续瓷砂滤柱有一定的过滤吸附能力,可适当减少絮凝剂投加量。

图3-39 不同絮凝剂投加量除氟效果
2)滤柱滤速影响。在高密度澄清池中用计量泵分别投加7.5mL/L经稀释的絮凝剂,改变滤柱滤速考察其除氟效果。运行条件:进水流量为100L/h(停留时间1h);絮凝剂投加量7.5mL/L(12.5mL/min);混凝剂投加1号搅拌器转速280~300r/min;污泥回流量40%(40L/h);污泥回流2号搅拌器搅速50~70r/min;污泥回流区域为4号回流管;滤柱滤速0.5~5.0L/h。试验结果见图3-40。由图3-40可知,当滤速为5.0L/h时,滤柱迅速穿透。这是由于滤柱吸附能力有限,并且CaF2颗粒细小而滤柱中滤料颗粒相对偏大,因此降低滤速,以1.0L/h为宜。

图3-40 不同滤速下滤柱除氟效果
3)运行稳定性试验。在高密度澄清池中用计量泵分别投加7.5mL/L经稀释的絮凝剂,连续运行8h考察其除氟效果。运行条件:进水流量为100L/h(停留时间1h);絮凝剂投加量7.5mL/L;混凝剂投加1号搅拌器搅速280~300r/min;污泥回流量40%(40L/h);污泥回流2号搅拌器搅速50~70r/min;污泥回流区域为4号回流管;滤柱滤速为1.0L/h。试验结果见图3-41。试验结果表明,当稀释的铝土矿酸浸液+原赤泥溶液絮凝剂投加量为7.5mL/L(折算成储备液为0.5mL/L)时,系统连续运行8h稳定,且出水氟含量和浊度均能达标。

图3-41 连续运行除氟效果
(3)高密度旋流絮凝反应器。高密度旋流絮凝澄清反应器结构见图3-42。设备结构主要由污泥浓缩区、旋流絮凝区、重力分离区、过滤分离区、清水区以及絮体回流构成。源水与混凝药剂经充分混合后切向进入反应器旋流絮凝区,水流在自身能量的驱动下沿反应器的器壁自下而上作螺旋旋流运动,水体中凝聚脱稳微絮体颗粒物在微旋流过程中不断发生碰撞絮凝作用,絮体颗粒逐渐增大;当上升水流经旋流絮凝区进入重力分离区时,水力旋流消失,水流基本呈层流稳定状态,此时水中已形成的大的絮体颗粒由于重力作用而沉降分离;没有沉降的微小絮体颗粒随水体进入过滤分离区,被上浮聚酯过滤粒子截留作用,水体中的絮体颗粒基本被完全去除,再进入清水区,经稳流后自反应器出口排放;表面呈正电荷的絮体颗粒物在重力作用下沉降至污泥浓缩区上部,一部分絮体颗粒通过回流管再返回旋流絮凝区,与加药脱稳微絮体颗粒发生碰撞絮凝作用;一部分絮体颗粒则下沉降至污泥浓缩区低部适时排出。

图3-42 高密度絮凝反应器结构示意图
(4)高密度絮凝澄清池。对于每日千吨以上的处理量,采用上述钢制絮凝反应器设备,投资过高,所以应采用高密度絮凝澄清池。高密度絮凝澄清池由强制混合絮凝段强制快速混合;回流絮凝段通过适宜的水力紊流或进行絮凝搅拌,使一定比例的正电荷的回流絮体污泥与脱稳颗粒进行循环接触碰撞结合,再通过加入的助凝剂进行絮凝架桥,使絮体颗粒逐渐形成大而密实的絮体颗粒,进入沉淀澄清段。沉淀澄清段则是由上部斜板或斜管分离区和污泥浓缩区组成,通过斜板澄清分离,清水排出。大而密实的絮体颗粒则沉淀进入污泥浓缩区。
进入到污泥浓缩区的新生成的正电荷絮体污泥则通过回流污泥管连续不断地返回回流絮凝段,使絮凝反应段的接触污泥达到并保持一定地悬浊污泥比例(依据水质情况而定污泥回流比)。剩余浓缩污泥通过污泥管排放。优点:形成絮体大而密实,沉淀澄清迅速;系统水力停留时间短,处理量大;出水水质优良;药剂用量省,占地面积小,污泥量少,易于集中控制。用于除浊处理,总水力停留时间仅为20min,是一种全新概念的絮凝反应设备(图3-43)。

图3-43 高密度絮凝澄清池结构
2.组合集成工艺技术系统及设备
根据上述试验结果,提出了经济安全的农村劣质水安全净化工艺技术系统,即强化吸附絮凝—安全吸附过滤净化处理工艺技术流程,见图3-44。

图3-44 强化吸附絮凝—安全吸附过滤净化处理工艺技术流程
在上述净化处理工艺技术系统中,关键技术和设备是高密度回流吸附絮凝澄清池和后续强化瓷砂吸附过滤器。高效铝铁絮凝剂投加水中后进一步发生水解,进而迅速转化成为带弱正电荷的羟基氧化铁、铝微粒,这些初生成的正电荷的羟基氧化铁、铝微粒(既初生态氢氧化铝或氢氧化铁絮凝体)对水中氟化物具有较强的吸附絮凝作用。通过将沉淀澄清不同断面的部分新沉积的初生态氢氧化铝或氢氧化铁絮凝颗粒污泥按比例回流至絮凝反应过程,使絮凝反应段保持一定数量的混合污泥;这部分新沉积的、带正电荷的初生态氢氧化铝或氢氧化铁絮凝体与源水混合,降低了水中胶体颗粒负阴电势位,增强了正电荷初生态絮凝体对微污染物的电中和/吸附凝聚效能;循环回流的带正电荷的初生态氢氧化铝或氢氧化铁絮凝体颗粒污泥可进一步吸附水中微污染物,极大地弥补了由于絮凝过程的吸附时间短暂,导致吸附量低的缺点。最后,投加新型次氯酸钙安全消毒剂进行消毒处理,确保处理水质安全可靠。
(三)组合电絮凝(CEC)除氟工艺
在电絮凝过程中,电解产生的OH-和Al3+存在3∶1的浓度关系。对于含一定浓度的F-且pH较高的原水,通常需要加入酸性溶液来控制体系的γOH+F。采用铝盐混凝剂代替普通的酸,也可达到控制γOH+F的目的。对于初始OH-和F-浓度一定的原水,可以通过改变铝盐混凝剂中存在的和电解产生的Al3+之间的比例,来达到一定的总铝投加量([Al3+]T)和γOH+F。这种方法称为组合电絮凝(Combined Electro coagulation,CEC)。
本节内容主要利用CEC技术进行除氟试验,确定CEC工艺中γOH+F与除氟率之间的关系,以及此关系随初始碱度的变化规律。提出CEC工艺去除以为初始碱度的含氟地下水的优化操作方案,并以此方案验证CEC除氟工艺处理含氟地下水的效果并对其电能消耗做出评价。
1.材料和方法
(1)原水。
1)去离子水中加入2.0mmol/L NaCl和适量的NaF,用适量NaOH或NaHCO3调节实验所需的碱度。
2)取自北京大学地下水,并投加适量NaF以满足实验所需的初始F-含量。含氟地下水pH=7.80~7.95,离子组成见表3 21。
表3-21 含氟地下水的水质指标

(2)CEC工艺操作参数确定。CEC工艺中的γOH、γF和γOH+F通过式(3-7)~式(3-9)计算:

式中:γOH为水中OH-摩尔浓度与Al3+摩尔浓度的比值;γF 为水中初始F-摩尔浓度与Al3+摩尔浓度的比值;γOH+F为水中OH-和F-摩尔浓度之和与 Al3+摩尔浓度的比值;[OH-]0为水中初始OH-浓度;[OH-]EC为电解过程中产生的OH-浓度;[H+]0 为水中初始H+浓度;[F-]0为初始F-浓度;[Al3+]T 为投加的Al3+总量。
首先对含氟水进行水质分析,测定初始的F-、碱度和酸度等含量。然后根据预定的[Al3+]T 和γOH+F,可根据式 (3 9)计算出 [OH-]EC。根据电絮凝电解特点 (忽略铝的化学溶解),电絮凝过程中产生的OH-与Al3+的摩尔比值为3∶1。因此,电化学Al3+投加量 ([Al3+]EC)和化学 Al3+投加量 ([Al3+]CC)可根据式 (3 10)和式 (3 11)得出:


[Al3+]EC与电解过程中的操作参数有关。在其他参数恒定的情况下,电化学Al3+投加可通过控制电流强度来实现。

式中:I为电流强度,A;z为Al3+的荷电数,z=3;F为法拉第常数(96486C/mol);V为反应体积,L;T为电解时间,s;εc为电流效率(本实验选择εc值为1.11)。
(3)CEC除氟实验。采用铝板(纯度为99.999%)为阳极,铜板作为阴极(以防止由于阴极化学溶解造成的Al3+投加量偏差)。电极的面积为90mm×60mm,极板间距为10mm。采用序批式实验,每次实验用水300mL,电解时间为10min。根据确定的Al3+投加总量和γOH+F计算出应加入的AlCl3和电解过程中应保持的电流强度。向实验用水中加入AlCl3后,采用电磁搅拌器进行快速搅拌,使电絮凝反应器中溶液保持均匀。同时开启稳压电源,在恒定的电流强度下进行电解。电解过程结束后立即取出电极板,溶液慢搅10min后采样。样品用针式过滤器(0.22μm,PSE)过滤后进行水质分析。实验数据均为平行实验或重复实验数据。
(4)分析方法。水中的阴离子F-、Cl-、、
和阳离子Na+、K+、Ca2+、Mg2+含量均采用离子色谱(戴安,ICS2500)分析,分析前水样均经0.22μm过滤。阴离子测定条件:阴离子柱AS11-HC(4×250mm),阴离子抑制器ASRS-ULTRA II(4mm),电导检测器,淋洗液为NaOH(30mmol/L),洗脱速度1.2mL/min。阳离子测定条件:阳离子柱IonPac CS12A(4×250mm),阳离子抑制器 Cation Atlas CAES,电导检测器,淋洗液为甲磺酸(20mmol/L),洗脱速度1.2mL/min。水中碱度采用电位滴定法测定(HZ-HJ-SZ-1030)。
2.试验结果
(1)γOH+F的影响。在保持某个[Al3+]T不变的条件下,通过调整CEC过程中电解产生的Al3+和化学混凝剂投加AlCl3的比例来改变γOH。CEC处理不存在初始碱度的含氟水时,除氟率εF随γOH和Al3+投加量的变化见图3-45(a)所示。从图中可以看出,对于每个Al3+投加量,均存在一个γOH值使得CEC的除氟效率最高,且该值随着Al3+投加量的增加而增加。将此γOH值定义为最佳的γOH值。由于γF随着Al3+投加量的增加而减少。因此,最佳γOH值和γF进行加和,得到的γOH+F可能为一个常数。图3-45(b)则表示了εF在不同[Al3+]T投加量条件下随γOH+F的变化。从图中可以看出,对于每个Al3+投加量,当γOH+F接近3.0时CEC都能取得最高的除氟效率。这说明CEC过程中γOH+F=3.0可作为除氟工艺参数优化的控制标准。
(2)初始碱度的影响。当原水中存在碱度时,通常按照碳酸氢根与氢氧根的摩尔比1:1的关系,以
代替式 (3 9)中 [OH-]0,γOH+F相应地以γAlkalinity+F表示:

图3-46表示了初始浓度相同(2mmol)的两种碱度类型(OH-和)在不同γAlkalinity+F条件下εF 的变化。从图中可以发现,初始碱度为 OH-时,除氟效果的最佳γAlkalinity+F (γAlkalinity+F(opt))在3.0附近。与图3 45(b)的结果比较可知,当初始碱度为OH-时,可采用γAlkalinity+F=3.0作为除氟工艺参数优化的控制标准。

图345 εF在不同[Al3+]T投加量下随γOH和γOH+F的变化([F-]0=10mg/L;[OH-]0=0mg/L)
但是,当初始碱度为时,其最优γOH+F值不在3.0附近,而是在3.6附近(图3 46)。这可能由于水中的碳酸氢根只有部分水解为OH-,其表现出的碱性弱于OH-的碱性。因此,对于以
为初始碱度的含氟水,不能直接采用γAlkalinity+F=3.0作为除氟工艺参数优化的控制标准。通过改变初始
的浓度,研究初始
浓度变化对除氟效率的影响,实验结果见图3-47。从图中可以发现,随着
浓度的增加,除氟率的γAlkalinity+F(opt)随之增加。这说明γAlkalinity+F(opt)与
的浓度有关。如果γAlkalinity+F(opt)能保持在3.0,将在应用中带来方便,为此需对
引起的碱度进行矫正。

图3-46 初始碱度为OH-和的含氟水的εF随γAlkalinity+F的变化 ([F-]0=10mg/L,[Al3+]T=1.2mmol/L)

图347 εF在不同HCO3-浓度下随γAlkalinity+F的变化 ([F-]0=10mg/L,[Al3+]T=1.2mmol/L)
(3)碱度的矫正。为了得到
碱度的矫正系数,做下列假设:
1)即使浓度发生变化,CEC的γAlkalinity+F(opt)仍保持在3.0。
2)和OH-两种碱度的差别可以用矫正公式 (3 14)表示,其中α为矫正系数且为常数:

3)初始碱度为时γAlkalinity+F的矫正计算按式(3-15)进行:

γ Alkalinity+F(cor)为矫正后的γAlkalinity+F。根据假设1),在除氟效率最高时γAlkalinity+F(cor)应为3.0。对于不同的浓度,其γAlkalinity+F(opt)应同时满足式(3-14)和式(3-15)。将两式相减,得式(3-16):

将图3-47的实验结果代入式(3-16),并对不同浓度下的[γAlkalinity+F(opt)-3.0]×[Al3+]T值进行直线拟合,可得y=0.4039x,R2=0.9731。斜率(1-α)为0.4039,由此得出
浓度的实验矫正系数α为0.5961。
根据图3-47的实验数据,将实验所得矫正系数α代入方程(3-16)进行γAlkalinity+F(cor)的计算,除氟效率εF在不同初始浓度下随γAlkalinity+F(cor)的变化,见图3-48。由图中可以看出,初始
浓度在1.0~3.0mmol/L范围内,通过对
浓度进行矫正后,CEC在γAlkalinity+F(cor)值3.0附近能够取得最优的除氟效果。
对于天然含氟地下水,通过电位滴定法,测得其碱度类型为重碳酸盐型,其初始浓度为2.362mmol/L。总Al3+投加量为1.2mmol/L条件下,CEC的除氟效率随校正后γAlkalinity+F(cor)的增加而增加,在3.0附近达到最大值后逐渐降低(图3-48)。这说明上述实验中得出的
浓度的矫正系数同样适用于含氟地下水中的重碳酸盐碱度。

图3-48 εF在不同浓度下随校正后γAlkalinity+F(cor)的变化 ([F-]0=10mg/L,[Al3+]T=1.2mM)
(4)CEC处理含氟地下水的效果和能耗分析。利用获得的矫正系数对含氟地下水的
碱度进行矫正,采用CEC和电絮凝+酸调节两种工艺在γAlkalinity+F(cor)=3.0条件下对含氟地下水进行处理,结果见图3 49(a)。可以看出,随着Al3+投加量的上升,两种工艺的除氟率均随之上升。在Al3+投加量超过1.5mM时,二者的除氟率均能超过90%,出水F-浓度小于1mg/L。CEC中Al3+部分来自电解过程,电场作用较弱;电絮凝+酸调节工艺中Al3+全部来自电解过程,电场作用较强。在低Al3+投加量 (Al3+<1.2mM)下电场所起的电浓缩作用对除氟贡献较大,氟的去除主要发生在电极附近,因此,电絮凝+酸调节工艺的除氟效果略高于CEC。随着Al3+投加量增加,电浓缩作用已不显著。此时氟的去除不仅发生在电极附近,而更多地依赖于分散于本体溶液中的Al(OH)3的吸附作用。因此,在较高Al3+投加量(Al3+>1.2mM)条件下,两种工艺的除氟效率相差不大。

图349 CEC和CE+酸两种方法处理含氟地下水的比较(初始F-=10mg/L)
在Al3+投加量为1.5mM时CEC处理后其他水质指标分析结果见表3 22。虽然由于投加部分 AlCl3 造成末端出水中 Cl-浓度增加,但是与传统化学混凝相比 (投加1.5mMAlCl3会额外增加出水160mg/LCl-),其可能造成的阴离子污染则相对小了很多。
表3-22 CEC处理后的含氟地下水水质

图3-49(b)列出了电能消耗(去除1gF所需消耗的电能)的分析结果。把CEC中加入的AlCl3絮凝剂按当前价格转换成等额的电能消耗。可以看出,计算絮凝剂的CEC电能消耗和不计算絮凝剂的CEC电能消耗差别很小,并且CEC的电能消耗明显小于电絮凝+酸调节工艺,这种能耗的差别随着Al3+投加量的增加而增大。由于CEC过程中的Al3+一部分来自于化学方法投加,且投加量很小,因此电絮凝部分所需电耗小于完全由电解投加Al3+的电絮凝工艺。两种工艺在除氟效率相近的条件下,CEC的电能消耗不及电絮凝工艺的1/3[图3-49(b)]。不仅如此,CEC中Al3+投加量只有部分来自电解过程,因此CEC在电极板消耗方面的成本也有所降低。
试验表明,对于OH-为唯一碱度的配水,控制γAlkalinity+F=3.0可使CEC达到最高的除氟效率。当原水中存在碱度时,需要对
的浓度进行矫正才能使CEC的最佳除氟条件为γAlkalinity+F=3.0。试验得出
碱度的矫正系数为0.5961。CEC与电絮凝+酸调节工艺的除氟率相差不大,在Al3+投加量超过1.5mM时,二者的除氟率均能超过90%。但CEC电能消耗较少,不到电絮凝工艺的1/3。组合电絮凝(CEC)工艺在保证高效除氟的同时,不仅降低了电能和铝板消耗,而且保留了电絮凝电场作用方面的优点,具有良好的应用前景。
(四)吸附—超滤除氟工艺
适用于分散式供水除氟的吸附—超滤工艺,采用活性氧化铝粉末为除氟剂,以超滤膜为分离设施。用粉末活性氧化铝为吸附剂时,在提高吸附容量的同时,可能会造成超滤膜的污染。因此,要通过试验确定适宜的吸附剂投加量、吸附剂粒径、曝气量、回流量、反冲周期、反冲流量和反冲时间等因素。
1.装置与方法
(1)材料与流程。试验用原水为去离子水配水(pH=5.5),即在去离子水中加入一定量的氟化钠,使原水氟浓度约为2mg/L。试验所用的超滤膜为中空纤维超滤膜,膜材料为PVC合金,截留分子量为100000U,膜面积约为0.2m2。试验流程见图3-50。

图3-50 试验流程图
(2)试验方法。超滤膜以浸没的方式安装在反应器膜区内,吸附剂通过恒流泵的作用与原水在反应区入口处混合,一同进入反应区。回流泵将沉积在沉淀区底部的吸附剂回流到反应区,使反应区内吸附剂与原水充分混合,同时保持反应区内吸附剂的较高浓度。为了有效地控制膜污染,定期对超滤膜进行反冲洗,反冲洗水由超滤膜出水提供。系统在恒流条件下运行,即膜通量保持恒定,膜污染情况通过跨膜压差表示。跨膜压差由压力传感器采集,通过数显仪显示并最终在计算机上记录。系统运行采用自动控制。主要操作参数:膜通量为150mL/min,反应区停留时间为15min,沉淀区停留时间为15min,反冲周期为6h,反冲时间为2min,反冲流量为150mL/min,原水氟浓度为2mg/L,活性氧化铝投加量为0.1g/L。
2.试验结果
(1)吸附剂粒径对膜污染和除氟效果的影响。研究表明,吸附剂粒径越小吸附容量越高,吸附速度越快。对不同粒径的活性氧化铝进行吸附容量的静态试验发现,随着粒径的减小,吸附容量增大。然而,吸附剂的粒径越小对膜污染的影响可能越大,尤其是与膜孔径尺寸相近的微粒,更加容易导致膜污染。因此,在连续试验中,选用粒径为0.050~0.074mm和小于0.038mm的活性氧化铝,考查不同粒径活性氧化铝对膜污染和除氟效果的影响,以期获得较高吸附容量,同时最大限度地减少膜污染。为了更好地考查粒径对于膜污染和除氟效果的影响,该部分试验中保持反应器内吸附剂质量浓度恒定,为5g/L,见图3-51。可见,粒径对于膜污染有显著影响,粒径越小膜污染越快,污染程度也越严重,但对于除氟效果,粒径为0.050~0.074mm和小于0.038mm的活性氧化铝差别不大(P>0.05),因此,后续试验选用粒径为0.050~0.074mm的活性氧化铝。

图3-51 粒径对膜污染和除氟效果的影响
(2)膜区曝气量对膜污染和除氟效果的影响。曝气对于该系统的影响体现在两个方面:①曝气可将沉积在膜区底部的吸附剂鼓起,增大吸附剂含量,提高除氟效果,同时也可能增加膜污染;②曝气对于膜丝的冲刷引起的水流剪切作用又可能缓解膜污染的发生,曝气量的大小起了决定作用。因此,为考察曝气量对于除氟效果和膜污染的影响,选择气水比为0(无曝气),10:1和20:1进行试验,对应的曝气量分别为0,90L/h和180L/h。曝气量对膜污染的影响见图3-52(a)。
由图3-52(a)可见,曝气量越大,膜污染越严重。当气水比为20:1时,可以看到膜污染迅速增加,运行45h后膜阻力增加了5.6kPa,而无曝气时,膜阻力增加了0.8kPa,气水比为10:1时膜阻力增加了1.9kPa。研究表明,曝气强度大,导致系统中水流紊流剧烈,提高膜表面的剪切力,减少了污染物在膜表面的沉积。在曝气量可以满足冲刷膜表面的要求时,膜通量的下降缓慢。原因为:①曝气量越大,吸附剂在膜区底部的沉积越少,膜区内吸附剂含量越大,因此膜污染越严重;②试验所用的超滤膜为束状膜,曝气量大时,吸附剂一经膜区底部进入膜区即被吹到膜丝上,并大量黏附于膜丝之间,快速在膜表面形成滤饼层;③曝气量大时,将粒径与膜孔径相当的吸附剂大量吹到膜丝表面,从而堵塞膜孔,造成膜的不可逆污染;而且使膜表面沉积的颗粒物粒径减小,形成的滤饼结构更加致密,导致膜污染迅速增加。
膜区不同的曝气量对除氟效果的影响见图3-52(b)。在除氟效果方面,理论上,曝气量越大,吸附剂含量越高,水中的氟离子与活性氧化铝的有效接触就越多,除氟效果越好。但由图3-52(b)可见,气水比为10:1时比无曝气时除氟效果要好,符合一般规律,但是差别不大(P>0.05)。而当气水比为20:1时,除氟效果反而比较差。这可能是因为曝气量过大(180L/h)时,吸附剂一经膜区底部进入膜区即被吹到了膜丝上,大量黏附于膜丝之间,快速在膜表面形成滤饼层,实际上减少了与水中氟离子的有效接触,因而除氟效果变差。

图3-52 曝气量对膜污染和除氟效果的影响
综合考虑膜污染情况、除氟效果以及动力损耗,后续试验中将不再在膜区进行曝气,尽量减小膜区吸附剂的含量,以减缓膜污染的发生。
(3)回流量对于膜污染和除氟效果的影响。沉淀区与膜区之间的回流可有效增加反应区的吸附剂含量,提高系统的除氟效果。通过试验测定可知,无回流时,反应区的吸附剂质量浓度仅为0.1g/L,与吸附剂投加量相当,大部分吸附剂在沉淀区底部沉积,而有回流时,系统运行5d左右,反应区内的吸附剂质量浓度可达4g/L。但是回流量太大,又会导致进入膜区的吸附剂增加,加剧膜污染。因此,为了得到适宜该系统稳定运行的回流参数。选取回流比分别为0(无回流),0.5和1.5,对应的回流量分别为0,4.5L/h和13.5L/h,连续运行3d,定期取样测定氟并记录膜压力变化情况。
回流量对膜污染的影响见图3-53(a),回流量的增大并没有增加膜污染。在3个回流量下,随着系统的运行,膜污染都有所增加,反冲洗能对膜污染产生有效的控制。总体来说,后一个周期过膜压力的增加值大于前一周期。试验开始的前4个反冲周期,每个周期内过膜压力增加了约0.5kPa,反冲后都能恢复到初始压力。试验后期,一个反冲周期内过膜压力增加了约1.5kPa。这可能是由于不断有未能在沉淀区沉淀的小粒径吸附剂进入膜区,使膜区的吸附剂质量浓度逐渐增加,不断堵塞膜孔和在膜表面生成滤饼层,导致膜污染不断加剧,并产生了膜的不可逆污染。试验中对膜区的吸附剂质量浓度进行了监测,当回流量为0,4.5L/h和13.5L/h时,测得膜区吸附剂质量浓度分别为0.0228g/L,0.0644g/L和0.1035g/L。
回流量对除氟效果的影响见图3-53(b),有回流时除氟效果较无回流时有所改善,且回流量越大,除氟效果越好,回流量对于除氟效果影响显著。根据观察,回流量为4.5L/h时,沉淀区的吸附剂已能很好地回流到反应区进行充分混合,运行稳定,且出水氟浓度为1.2mg/L左右,基本满足我国小型分散式供水含氟标准。
由试验结果可知,选取适宜的参数,在吸附剂粒径为0.050~0.074mm,无曝气,回流比为0.5(回流量为4.5L/h)的条件下,可获得较好的除氟效果,并有效控制膜污染,使该系统在一定时间内稳定运行。

图3-53 回流量对膜污染和除氟效果的影响
(五)单元组合式除氟工艺与装置
单元组合式除氟工艺与装置是针对家庭使用开发的除氟技术,特点是使用方便、经济合理。
1.吸附剂选择
单元组合式除氟成套设备的关键技术是轴向过滤式除氟单元,轴向过滤滤芯中使用的吸附剂选用原则是,在具有较好的吸附性能的基础上,吸附剂应价格低廉、供应充足、易于获得,长期使用过程中具有较高的性价比。在对多种备选吸附剂比较的基础上,选择了具有较好试验研究基础的活性氧化铝。
2.活性氧化铝处理工艺
(1)吸附剂预处理。为了提高活性氧化铝的吸附性能,用硫酸铝对活性氧化铝进行预处理,分别在实验室内利用配置高氟水、在现场利用高氟地下水试验了不同浓度硫酸铝处理对活性氧化铝吸附性能的影响。
1)静态吸附试验。分别取不同处理的活性氧化铝5g,加入100mL氟浓度为5mg/L的配制高氟水中,在25℃下以80r/min避光振荡,24h后取出并将溶液过滤,测定氟离子浓度,采用不同处理后的活性氧化铝进行静态吸附试验。由表3-23可见,在等温吸附后,经过4%和10%硫酸铝浸泡后的活性氧化铝吸附性能较好,但经过4%和10%硫酸铝浸泡后的活性氧化铝在吸附过程结束后,其溶液中残留大量的硫酸根,远远超过国家饮用水卫生标准所要求的250mg/L;去离子水、0.5%、1%、2%硫酸铝溶液浸泡后活性氧化铝的吸附效果相比较,2%硫酸铝预处理后的活性氧化铝吸附效果较好。
表3-23 不同预处理活性氧化铝等温吸附效果

2)动态吸附试验。使用规格分别为φ15×300mm和φ25×500mm的有机玻璃柱,装填不同预处理吸附剂运行;规格为φ15×300mm有机玻璃柱装填40mL(质量30g±1.5g)粒径范围为0.5~2.5mm活性氧化铝,φ25×500mm规格柱装填100mL(质量80g±2.5g)粒径范围为0.5~2.5mm活性氧化铝,过柱氟溶液浓度为5mg/L,使用蠕动泵控制进水流速,通水方式上进下出,吸附过程连续运行,间隔一定时间取样分析出水氟浓度。
图3-54(a)是柱规格为φ25×500mm情况下运行结果,可见,预处理措施影响初始出水氟浓度,未进行预处理以及1%硫酸铝浸泡后活性氧化铝在运行初始阶段其出水氟浓度大于1mg/L,但随着硫酸铝浓度的升高,其初始出水氟浓度降低,处理深度增加;不同预处理措施的活性氧化铝的穿透吸附容量及穿透BV见表3-24。未进行预处理吸附剂其穿透吸附容量和穿透BV最小;1%硫酸铝浸泡后活性氧化铝穿透吸附容量和穿透BV最大,但其初始运行出水氟浓度未能降至1.0mg/L以下。
柱规格为φ15×300mm时,2%和10%硫酸铝预处理情况下的运行结果见图3-54(b)。经过10%硫酸铝浸泡后活性氧化铝起始运行阶段出水氟浓度较低,但吸附效果持续性较差,穿透BV为165;经过2%硫酸铝浸泡后活性氧化铝起始运行阶段出水氟浓度低于1.0mg/L,吸附效果持续性较好,穿透吸附容量可达1.532mg/g,穿透BV可达342。不同预处理活性氧化铝穿透吸附容量及穿透BV值见表3-24。

图3-54 不同预处理活性氧化铝柱试验
表3-24 不同预处理活性氧化铝穿透吸附容量及穿透BV值

① 穿透指出水氟浓度达到1.0mg/L。
3)现场静置吸附试验。室内试验表明,使用2%硫酸铝溶液预处理后的活性氧化铝吸附效果有明显改善。为验证实验室结果,进行了现场静置试验。由图3-55可见,活性氧化铝在使用2%硫酸铝预处理后,吸附效果明显改善,这和实验室获得结果是一致的。
(2)原水pH对活性氧化铝吸附性能的影响。试验在河北省清河县进行,未预处理的活性氧化铝用于高氟水处理时,穿透BV很小(图3-56前半段)。原因是原水pH较高(8.5左右)。因此,在出水量达到27BV时,调节原水pH至6.0,继续上述试验过程。由图3-56可见,调节pH至6.0可显著提高活性氧化铝的吸附性能,并且持续性较好。

图3-55 预处理效果现场试验

图3-56 原水pH对未预处理活性氧化铝的影响

图3-57 不同原水pH情况下运行结果
(3)调节原水pH与硫酸铝预处理的综合效果试验。用2%硫酸铝溶液预处理和调节原水pH均可明显改善活性氧化铝的吸附性能,但应用于河北省清河县条件下,出水均难以达到理想效果。为此,同时采取了预处理和调节原水pH两项措施进行试验,结果见图3-57所示。可见,接触吸附时间控制在5min时,用2%硫酸铝预处理后的活性氧化铝,调节pH至6.0后,除个别时刻测得的出水氟化物浓度稍大于1.0mg/L外,出水氟化物浓度大都保持在1.0mg/L以下,穿透BV可达240。出水pH在6.6~7.0之间,不需要调节,符合国家饮用水卫生标准。增加接触时间,还可进一步改善吸附效果。
3.活性氧化铝再生工艺
(1)再生方案比选。分别采用不同浓度的氢氧化钠、硫酸铝、硫酸及其不同组合对经过一个完整吸附过程的活性氧化铝进行再生,并比较再生后下一个吸附周期的吸附效果,结果见图3-58。在不同的组合中,以3%硫酸铝和0.4%氢氧化钠的组合效果最好。
(2)不调节pH条件下连续三个周期的吸附—再生—再吸附运行结果。将采用2%硫酸铝预处理的活性氧化铝装填在除氟单元装置中,连接在自来水管道上连续运行,接触时间控制在20min。当出水氟浓度达到1.5~2.0时,采用3%硫酸铝溶液再生。再生后重复运行及连续三个周期的吸附—再生—再吸附的运行结果,见图3-59和表3-25。由试验结果可知,随着运行周期的增加,活性氧化铝吸附性能不断下降。三个周期的处理水量可达409BV。每个单元活性氧化铝的装填量为6L,三个周期处理水量为2454L。

图3-58 不同浓度的氢氧化钠、硫酸铝、硫酸及其不同组合的再生效果

图3-59 连续三个周期吸附—再生—再吸附的运行结果
表3-25 穿透BV与穿透吸附容量

4.轴向过滤式除氟单元关键参数
(1)径高比。径高比即吸附柱直径与吸附剂装填高度的比值,选用3种不同尺寸的有机玻璃柱即φ30×300mm、φ25×500mm、φ20×300mm,均装填经预处理后的活性氧化铝60mL,相应的径高比为1:3、1:5、1:10,使用蠕动泵控制进水流速SV3/h,即接触时间为20min,连续运行,观察径高比对活性氧化铝吸附效果的影响,运行结果见图3-60所示。可见,随着活性氧化铝装填径高比值的减小,穿透BV、穿透吸附容量逐渐增大,可见径高比是影响吸附材料吸附效果的重要因素。在实际应用过程中,可据此设计家用设备的外形,增大吸附剂装填高度,提高吸附剂的吸附性能。

图3-60 不同径高比的运行结果
(2)粒径。许多研究表明粒径是影响吸附材料的关键因素,为检验在清河现场水质条件下,粒径对活性氧化铝吸附效果的影响,分别筛取粒径为2~2.5mm、2.5~3mm的活性氧化铝各3L,预处理后装填除氟单元,起始运行控制接触时间10min,自75BV起,模拟组合式除氟设备实际运行工况,白天每隔4h放水18L,夜间静置8h。运行结果见图3-61。图3-61表明,在同等条件下,粒径2~2.5mm的活性氧化铝除氟效果优于粒径为2.5~3mm的活性氧化铝,粒径对于活性氧化铝的吸附效果是非常重要的影响因素;自75BV起,改变运行工况后,夜间静置8h后再运行的出水氟浓度降低较多,但吸附剂处理后溶液的氟浓度总体趋势在上升,但较连续运行缓慢得多,对于活性氧化铝而言,接触时间亦是重要的控制因素。

图3-61 粒径对活性氧化铝除氟效果影响

图3-62 接触时间对除氟效果的影响
(3)接触时间。由上述试验结果可知,接触时间对于活性氧化铝的吸附效果影响较大。取采用2%硫酸铝预处理后的活性氧化铝12L,分别等量装填至4台家用除氟设备中,分别控制接触时间为10min、20min、30min、50min,连续运行,运行结果见图3-62。由图3-62可见,接触时间由10min增长至30min时,穿透BV及穿透吸附容量有较大的增加,接触时间为30min时,穿透BV可达214,穿透吸附容量达1mg/g;但接触时间由30min增加至50min时,穿透BV和穿透吸附容量增加幅度较小,在动态运行过程中,控制接触30min即可达到良好的运行效果。
5.单元组合式除氟成套装置
组合式除氟成套装置单元见图3-63。分别按处理规模为2m3/h和5m3/h计算组合式除氟成套装置的参数,具体见表3-26。单元组合式除氟成套设备是以轴向过滤式滤芯为除氟单元关键技术组合而成的成套技术,该除氟成套设备最突出的特点是:①可以根据用水量大小灵活组合;②统一运行和管理,可按规范严格操作,水质有保证;③制水成本低,特备适用于高碱度高氟水地区分质供水,据估算,本成套设备的制水成本可较市售的反渗透低氟水降低一倍;④维护简便,除氟单元并联组合,实现不间断制水,每次再生20%的单元。
表3-26 组合式除氟成套装置参数表


图3-63 组合式除氟成套装置单元