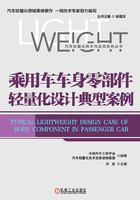
2.4 热冲压零件工装开发
热冲压零件的工装,主要有热冲压模具、落料模具、激光切割夹具、检具、端拾器,部分零件还含有快速模具,以及热冲压零件的冷切模具。本节主要对热冲压零件模具进行介绍,热冲压模具大多采用板式结构,用标准内六角螺栓固定模块,凸凹模采用镶块结构,内置冷却水道,采用可升降定位热坯料托料杆,模板水槽串联各模块的冷却水道。
2.4.1 热冲压模具的工艺设计
1.热冲压模具稳定性工艺设计方式
热冲压模具工艺的设计方式,直接决定了冲压成形过程中零件的成形性、生产稳定性。
模具结构一般分为以下四种:
1)两件式结构,如图2-45所示。
2)带有上活动块的三件式结构,如图2-46所示。
3)带有下活动块的四件式结构,如图2-47所示。
4)带有上、下活动块的四件式结构,如图2-48所示。

图2-45 两件式结构

图2-46 三件式结构

图2-47 带有下活动块四件式结构

图2-48 带有上、下活动块的四件式结构
一般来说,活动部件越少,模具动作越简单,模具结构也越容易加工制造;活动部件越多,对零件成形过程控制越精细,模具结构越复杂。
针对不同的热冲压零件断面形状,热冲压模具也需要采用不同的模具结构形式。热冲压常见的A柱、B柱零件,其热冲压模具结构介绍如下。
典型的A柱零件,其形状和断面如图2-49所示。

图2-49 A柱零件形状及断面
A柱零件一般断面形状比较简单,热冲压工艺一般采用两件式结构,上下模具直接压制成形;对于部分模具结构,为了防止冲压过程中料片窜动,一般会做几个小的局部预压块。
以典型的B柱零件为例,其形状和断面如图2-50所示。

图2-50 B柱零件形状及断面
B柱零件一般断面形状相对比较复杂,底端断面成形深度较深,宽度也较大;向头部成形深度逐渐变浅,跨度也变窄。B柱热冲压工艺一般采用具有顶部衬垫的三件式结构,由上模、下模、压料器构成,压料器先压住大头位置中间部分,再使用上模冲压成形,如图2-51所示。

图2-51 B柱模具
对于法兰边宽度较大、在法兰面平面内有较大翘曲的零件,一般还需要做下托芯,以便控制成形过程中的起皱。在这种情况下,模具变成带有上、下活动块的四件式结构,其热冲压模具如图2-52所示。

图2-52 四件式结构B柱模具
2.热冲压模具的零件排布组合方式
热冲压的生产过程在高温下进行,一般采用自动化的上下料系统,热冲压模具的结构设计,需要与热冲压生产线的设备相匹配。
热冲压零件的冲压过程,与传统冷冲压过程相比,在料片冲压成形后,增加了一个保压的过程,因此,热冲压的冲次周期大于冷冲压的冲次周期。
同时,热冲压一般应用于车身上的加强结构件,其零件尺寸相对偏小。
综合以上特点,目前热冲压一般尽可能地采用一模多件技术,以提高生产效率。
典型的热冲压零件的模具排布方式,一般按如下方式进行:
1)对于地板中通道、前围板等较大的零件,一般采用“1模1出”的方式进行模具排布设计。
2)常规的零件,例如B柱、前纵梁等零件,考虑到加热炉宽度、液压机台面尺寸、冷却系统的冷却能力等,一般来说采用“1模2出”的方式进行模具排布设计,如图2-53所示。

图2-53 “1模2出”模具排布设计
3)门防撞梁、顶盖横梁、地板纵梁加强板等细长形梁夹件,一般采用“1模4出”的方式进行模具排布设计,如图2-54所示。

图2-54 “1模4出”模具排布设计
4)对于其他小件,通过合理的工艺连料,可以做到“1模6出”或“1模8出”,从而大幅提高生产效率。
2.4.2 热冲压模具结构设计
1.热冲压模具的主要构成
热冲压模具主要由基体、镶块、导向部件、定位系统、退料部件、冷却循环系统等构成,如图2-55所示。
模具的基体、导向部件,采用的材质或零部件与传统冷冲压一致。基体(模架)一般采用HT300材质铸造,导向采用导柱、导套或者导腿形式,其设计方法与传统冷冲压基本一致;而冷却系统、退料部件、定位系统的设计需要根据热冲压的特点进行专门的设计。
2.热冲压模具的镶块材质
由于钢板热量的传递,在冲压前以及冲压过程中短暂的时间内,热冲压模具的镶块表面温度急速上升,随后在保压过程中逐步冷却。镶块表面的温度长期在70~300℃之间交替变化。
对于热冲压生产来说,热冲压模具镶块材料具有以下特性:导热性能、抗高温回火性能、延展性/韧性、热屈服强度、热膨胀系数、耐磨性能、可焊接性。

图2-55 热冲压模具
为了满足以上要求,热冲压模具镶块材料,需要严格控制钢材的化学成分,遵守严谨的热处理工艺条件。
对于生产出来的镶块材料,需要对实物进行金相组织检查,检测镶块材质的非金属夹杂物(纯净度),测试不同温度下的冲击韧性(V形口),检测镶块材质在高温(400~600℃)下的热传导性能、强度,以及硬度随保温时间的变化等。
3.热冲压模具的水路设计
(1)热冲压模具的水路结构
为了对加热后的板材实施有效的冷却淬火,热冲压模具的一个典型特征是镶块模面下方约10~15mm范围内布满了冷却水道。有效的水道设计,需要在满足强度要求的情况下,实现快速冷却(冷却速度不小于27℃/s)。模具需满足一定的传热效率并确保模具型腔表面温度均匀。
热冲压模具的水路,一般采用深钻孔或者铣刀加工方式。冷却水路系统设计目前主要有以下几种方式:①分段式倒U形水路;②直通式水路;③壳式水路;④插片式水路。其中,前两种采用深钻孔方式加工,后两种采用铣切削加工。
1)分段式倒U形水路。根据分段的位置,一般有以下两种,如图2-56和图2-57所示。
2)直通式水路。整个镶块组从头开始,一条水路直通到底。相邻的镶块之前没有水路折弯减速效应,有利于保障水流速度,水流可快速通过。由于此特点,直通式水路(图2-58)是目前热冲压模具水路设计的主流方案。

图2-56 单个镶块内循环的倒U形水路设计

图2-57 单个镶块组合内循环的倒U形水路设计

图2-58 直通式水路
由于一组镶块全部串行为一体,直通水路一个不便利之处是拆卸、安装其中某个镶块的时候,需要将全组的镶块拆开,这会造成维护保养不便。另外,直通式水路镶块与镶块之间的密封全部采用橡胶密封圈,冲压到一定冲次后,橡胶老化失效的可能性增大,会增加维修的频次。
分段式倒U形水路、直通式水路加工采用的设备都是枪钻。由于机加工的钻机,仅可在直线方向加工,对于多个方向翘曲的复杂型面,采用深钻孔加工水道的方式比较困难。后面的两种水路设计方式,是通过机械铣切削加工的方式来实现水路的效果。
3)壳式水路。由于加工工艺限制,深钻孔方式加工的水道与模面之间的距离很难做到均匀一致,从而导致零件出模后精度受到影响,壳式水路则解决了这个问题,如图2-59所示。

图2-59 壳式水路
当然,壳式水路也有缺点,首先,壳式水路两端壁厚区域冷却效果不及中央部分;其次,壳式水路对高度方向的装配精度提出了更高的要求;最后,模面所在整体薄层强度欠佳,冲压过程中受力容易发生永久性损伤。
4)插片式水路。插片式水路(图2-60)能针对性地解决壳式水路的缺点,但由于较大的加工量,目前未被普遍采用。

图2-60 插片式水路
(2)热冲压模具的水路连接方式和密封设计
水路从压力机接口处通过快插接头连接进入模具,然后通过模具分水块,给各部分镶块进行供水,如图2-61所示。

图2-61 水路连接方式
镶块之间通过直接孔连接的水路,镶块之间一般采用O形密封圈进行密封,两个镶块在长度方向需要设计锁紧螺钉,通过螺钉锁紧,确保不发生漏水,如图2-62所示。
4.热冲压模具的板料设计原则
热冲压生产的关键在于提高生产效率,降低生产成本,原材料成本占热冲压零件成本的40%~60%,优良的板料设计是热冲压生产的关键技术之一。
由于热冲压工艺特点类似于冷冲压的非拉延成形,热冲压工艺过程具有缩小废料区的板料尺寸的能力,因此,热冲压的板料一般都尽可能得小,产品边界周圈除了预留3~10mm激光切割余量外,基本接近净尺寸。
(1)第一个原则是满足成形性

图2-62 镶块的密封与连接
案例 B柱零件的板料设计,热冲压后周圈留有5mm左右激光切割余量,产品分析发现底部大头段成形过程中减薄过大,首轮调试出现开裂。然后通过仿真分析,并现场验证,局部适当将料片增大,最终解决了此问题,如图2-63所示。

图2-63 增加板料满足成形性
(2)第二个原则是满足生产工艺性稳定性
板料设计需要考虑生产过程中的稳定性问题,主要体现在以下几个方面:
1)辊底式加热炉,出炉撞阻挡器的位置设计。
2)加热炉对中位置板料局部边线设计。
3)端拾器抓取板料位置局部形状考虑。
4)热压模具上定位用孔设计、定位杆位置局部边线形状考虑。
5)冲压完成,脱模零件料片顶出辅助特征设计。
6)后续定位用板料辅助特征设计。
案例 下B柱的板料设计就需要考虑稳定性问题。料片在加热炉内运行中并非一条完整的直线,料片在加热炉撞料端错开10mm的距离,出炉撞挡板后容易发生偏离,不利于料片进行对中,如图2-64所示。
(3)第三个原则是在满足前2个原则同时兼顾经济性,尽可能缩小板料
以上所述原则,需要结合现场调试、落料工艺设计综合考虑,最终确定板料的形状。图2-65为某B柱最终的落料工艺排样图。

图2-64 料片在加热炉撞料端错开
5.热冲压模具的定位系统设计
热冲压模具对料片的定位系统设计,一般采用边缘定位杆初定位、定位销精确定位的方式进行,如图2-66所示。其周圈采用四个定位杆对料片进行粗定位,板料中央采用一个圆孔加一个长圆圈孔的方式,来实现精确定位。

图2-65 B柱落料工艺排样图
(1)定位杆设计注意事项
1)周圈定位杆的高度,应该高于定位销的高度,起到初始导向的作用,但是也不能过高,否则冲压后取件需要的取件空间加大。

图2-66 B柱定位布置图
2)定位杆一般采用带托料爪的设计,避免料片放入模具的瞬间大面积接触凸模,温降过快。
3)定位杆在模具结构上需要留出足够的调整空间,需要考虑料片的热胀冷缩效应。
4)定位杆需要有足够的强度,冲压过程中定位杆温度会升高,对于分段焊接式定位杆的强度不利,需要做加强筋增强,避免生产过程中断裂。
(2)定位孔、定位销设计注意事项
1)板料上定位孔必须为一个圆孔,一个长圆孔。圆孔的孔心与长圆孔直边段在一条直线上,保证板料冲压过程中的热胀冷缩不会造成卡死定位销或拉断定位销。
2)翻边孔位置设计,尽量靠近圆孔区域。翻边销一定要设计退料装置,因为成形后,由于冷收缩效应,容易将定位销卡死,无法退料。
3)为了防止定位销断裂,圆孔定位销尽量设计在成形过程中材料不发生流动或流动较小的区域。如果非得设计在材料流动大的区域,定位销所在区域需要设置压料装置,在整理料片成形前先行压住该区域,防止成形过程中,出现料片拉断定位销的情况。
2.4.3 热冲压模具的加工制造
1.热冲压模具的加工制造流程
模具结构设计完成后,会分为以下两部分开始实施制造:①模具本体实型、模具本体铸造、模具本体加工;②镶块采购、镶块水道加工、镶块3D粗仿形、镶块淬火,镶块装配。
两部分并行进行,同时工作完成后,将镶块安装到模座上,进行整体仿形,然后安装模具标准件与非标件等装配工作,最后开始调试并出件。
一个标准的热冲压模具项目运作流程如图2-67所示。

图2-67 热冲压模具项目开发流程图
2.热冲压模具的开发周期
(1)热冲压量产模具的开发周期
从接到产品开始到交出合格的工装样件,热冲压模具的开发周期根据零件的复杂程度不同,一般需要5~6.5个月,如图2-68所示。
专家点拨
关于开发周期,由于TRB、TWB板材获取渠道特殊,如市场上找不到现货的情况下,重新制作周期为7~8个月,超过模具本身的开发周期,需提前准备。
关于产品变更的模具开发周期,传统冷冲压项目可通过先将模具底座铸造出来,等产品变更完成后再加工镶块的方式来缩短产品设计变更的模具开发周期。对于热冲压模具,由于镶块的加工周期是整个模具加工中周期最长的部分,且镶块模面下方全是水道,因此,需要从新的产品加工指令下发后开始计算模具开发周期,无法再采用冷冲压的方式来缩短产品变更的模具开发周期。

图2-68 热冲压模具开发周期
(2)热冲压快速模具的开发周期
基于验证产品设计可行性、项目周期紧张等情况考虑,可以采用快速模具来提供小批量的样件。快速模具,行业内一般称为软模,不考虑批量生产的要求,仅保证能提供样件为目的。
通过使用标准模座、简化模具脱模动作、取消镶块水道等一系列操作,大幅缩短模具的开发周期,一般开发周期为2~2.5个月。
由于快速模具仅仅为提供前期试装样件,快速模具的样件与产品的复合率一般在80%~90%;同时因为无冷却水道,每次生产一件后,需等模具冷却下来后再进行下一件的生产,约15min能生产一冲次,生产效率较低。另外,由于采用的镶块材质、热处理工艺等因素,一般快速模具仅能提供300~500冲次的样件生产能力。
2.4.4 热冲压模具的检查与验收
热冲压模具的验收,主要从以下几个方面来进行检查:外观、安全部件、导向、镶块、型面、定位件、活动部件、水路、电路、气路油路、生产线匹配等,验收过程一般重点关注以下三方面:
1.静态检查
包括模具外观检查、起吊以及安全部件检查、导向间隙检查、密封性检查、镶块硬度检查、镶块安装间隙检查、水路畅通性以及密封效果检查,与生产线安装匹配相关的检查等。
2.动态检查
包括研合率检查、料片投入模具动作稳定性检查、卸料可靠性检查、气路(或油路)动作检查、热点区域检查、装配拆卸便利性检查、批量生产能力检查、生产裕度检查等。
3.热冲压零件性能检查
热冲压后的零件,主要检查几何尺寸、零件成形风险区局部、零件表面质量。力学性能方面主要检查零件硬度、抗拉强度、屈服强度、硬断后伸长率、金相组织。对于涂层板材料的热冲压零件,需要检查零件涂层厚度,对于裸板材料的热冲压零件,需要检查脱碳层厚度。
热冲压模具验收一般按照各个公司设定的验收表格进行,验收合格的模具,经过双方确认后,则可以发运到母线进行调试并批量生产。
热冲压模具的典型动态验收表示例如表2-7所示。

表2-7 热冲压模具的动态验收表示例(部分)