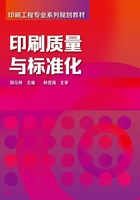
第二节 彩色软打样系统要求
现在印刷行业中越来越多地用彩色显示器显示图像进行颜色评价和颜色的可接受性评估(即软打样),这就需要显示器及其相应的观测环境能够模拟在标准的印刷观察条件下看到最终印刷品的外貌。要完成这样的功能就要创建软打样系统,该系统通常由显示器、色彩管理设备、驱动软件(用于校准、特性化显示器显示数据)和观察箱组成。所有的设计及校正要考虑并控制好环境光的影响。
随着软打样应用的增多,对软打样系统客观中立的评价的需求也稳步提升,软打样通常会遇到三种典型的场景,第一种仅用显示器显示,无观察箱,第二种是观察箱和显示器,第三种是显示器内置在观察箱中。从测试显示的图像能够多大程度地模拟原稿的编码色度数据角度讲,这三种场景并不需要区分。然而,评价软打样和参考印刷品的模拟程度,观察箱或房间的可控光源还是必需的。
软打样系统的客观评价分为三个步骤:第一步,显示器和观察箱要进行测试,以保证它们能够达到进行高质量软打样的要求;第二步,要测试显示器和显示驱动软件配套后的能力;第三步,测试输出条件的模拟,通常是特性印刷条件。
获得一个参考的软打样模拟不是一件简单的事情,为了非常精确,就要精心控制工艺过程的很多方面。
一、软打样的数据要求
软打样系统应接受ISO 15930中定义的PDF/X数据文件交付的数字数据,或应接受ISO 12639中定义的TIFF/IT文件所提供的数字数据。在使用TIFF/IT文件时,应按照ISO 12639中定义的要求,将颜色信息包含在标签34675或34029中。
二、软打样的显示器要求
所有的显示器测试都应当把显示器校正到亮度160cd/m2,色度匹配到2°视场下的D50(x=0.3457,y=0.3585),伽玛2.2。显示器必须显示包含各个红、绿、蓝通道最大值(8位时为255)的“白色”图像。
测试显示器时必须在稳定的条件下进行,为了确定各显示器的稳定时间,每一个测试的显示器必须在温度可控的房间内在校正模式下运行12h。房间温度变化不能超过±0.5℃,范围在18~28℃。
亮度变化不超过2%(和12h的最后9h的测量平均值相比),白点变化不超过校正条件CIE Δx、Δy的±0.005,这样就得到了稳定时间(预热时间)。如果显示器达不到稳定条件,就不能用。
显示器的预热必须用亮度和CIE Δx、Δy的测量值和12h的最后9h的平均值的图形表示出来,以百分比表示。
在参考白的最大驱动下,测量屏幕5×5均匀网格的中心,计算CIELAB值。注意,这种方法会导致CIE L*大于100。在三种驱动水平下,即最大驱动水平(白)(8位显示器R=G=B=255)、半驱动水平(灰)(8位显示器R=G=B=127)、1/4驱动水平(深灰)(8位显示器R=G=B=63),计算周围24个网格和中心网格的CIEDE2000色差。对于白和灰驱动水平,ΔE00要≤4。
测量灰(最大驱动水平的一半,8位显示器R=G=B=127)和白(最大驱动水平,8位显示器R=G=B=255)的亮度(cd/m2),计算25个区域的灰/白比。对于非中心区域的比例Ti(i=1,…,24)由各非中心区域的灰/白比Ri(i=1,…,24)除以中心区域的灰/白比Rc,再减去1,并取绝对值。色调均匀性的偏差应小于10%,即Ti(i=1,…,24)的最大值应小于10%。
Ti=abs(Ri/Rc-1) (3-2)
色调均匀性取决于max(Ti),(i=1,…,24),应小于10%。
显示器关闭状态下的表面反射特性必须在黑屋子里用点光源进行视觉评判。点光源从屏幕的反射应该显示模糊,并且随着偏离镜面反射方向逐渐平滑地下降。
印刷工业软打样显示器在任何驱动水平下在可视观察锥内都应该具有很小的颜色偏差,通过计算每个方位角的所有观察角直到最大θ的ΔE00色差来评价可视观察锥的颜色稳定性,在最大驱动水平的白(8位显示器R=G=B=255)和半驱动水平的灰(8位显示器R=G=B=127)的ΔE00必须小于10,对于1/4驱动水平的深灰(8位显示器R=G=B=63)以及达到1%亮度(1.6cd/m2)的驱动水平也应该小于10。
三、显示要求
视觉环境的设计应尽量减少对观察任务的干扰,重要的是要消除外部条件对显示器上图像和观察箱中印刷品观察评价的影响。软打样设置时有多种可能的潜在变化。
显示器有两种不同的设置方式。第一种是显示器位于专用观察箱旁边(不是内部)。这里,环境应该能够控制,这样杂散光不会对显示的图像或它的周围产生显著的影响。在这种情况下,观察箱内的照度水平可以使用远程光谱辐射计进行调整,使得从纸张上反射的亮度(可能包含对将要使用纸张的模拟)可以与显示对纸张的模拟相匹配。如果需要的照度级别不同于P1或P2,则应在ISO 3664评估测试中使用此级别(除了定义的级别P1或P2之外)。
第二种显示器上方的照明不可避免。这种情况下,例如,显示器放置在印刷机旁边的观察箱里面。在这里,通过使用显示罩,尽可能减少照明对显示屏幕的影响。对于这样的系统,当补偿以达到印刷品和显示之间亮度水平和一致性匹配时,观察箱的照度也可能不在ISO 3664中规定的范围内。
当制造商没有在暗室对专用的观察箱进行测试时,ISO 3664中定义的所有标准都要应用(对于要进行软打样的对象)。
当仅用显示器进行图像评价时,应遵循下列准则:
① 位于显示器的面板(在任何反射罩后面)上的完全反射漫射器的亮度不应大于显示白点亮度的1/4(8位显示器的R=G=B=255)。
② 显示框、显示器的周围、书桌、墙壁和视野中的所有东西都应接近中性,以确保没有饱和的彩色元素影响观察者的色彩适应。对于显示器框架,灰色是最好的颜色,但黑色或白色也可以使用。由于眩光,银或铝显示器架不适合。对于墙壁和书桌,中性灰色最好,但白色也可以使用。
③ 应使用显示器罩尽量减少周围照明在显示器表面反射所造成影响。遮光罩应覆盖从顶部和两侧的显示面。
④ 桌面和键盘应该是中性色,并且反射率低。从显示面到前缘,顶部罩应该相当深,但不可压迫。
用与ISO 12647-7测控条兼容的色块测量的特征化印刷条件和显示之间的颜色偏差值应在表3-2规定的公差内。
表3-2 色度精确性:参考印刷和软打样复制间的ΔE00容差

四、显示驱动和模拟要求
对于要测试的每个特征化印刷条件,除了所要求的专色色块外,只需要印刷中所列的色块。这些色块印刷的最小尺寸应为10cm×10cm。这些印刷品在目标观察平面内进行连续的演示和测量,以检验模拟的准确性。专色要复制时,应用统一的印刷样品加以定义。它们被呈现和测量的方式与以前的印品相同。
印刷样本的公差应比ISO 12647-7中的规定更严格,即模拟特征化印刷条件的色块相对于参考特征数据,其平均色差ΔE00值必须≤2,最大色差ΔE00值必须≤3,并且每个专色色块色差ΔE00值应≤1.5。显示驱动和模拟要求的测试色块如表3-3所示。
表3-3 显示驱动和模拟要求的测试色块

