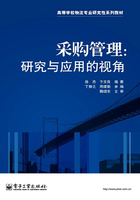
2.3 成本主导型采购方式决策
2.3.1 案例情景与初步分析
某工业制造企业拟采购45号钢(线材),平均每天需求为10吨,但最低需求可能为0吨,最高需求可能达到20吨。供方批量规模化生产,以库存供货,出厂价格不变,订购第二日即可交货。该企业可以准确计算第二天的物料需求量(根据订单和生产计划),但对更长时间的需求则无法准确计算。整车(如60吨)运输费率为0.3元/吨公里,零担运输价格上浮20%,费率为0.36元/吨公里,运输距离为100公里。流动资金贷款利率按8%计,钢材的价格按4000元/吨计,每吨钢材每天的资金占用成本约为0.8元,每吨钢材每天的库存与保管费约为1元。缺货成本为每天每吨5元。计划订购方式下平均单次订货费用为180元,订单订购方式下平均单次订货费用为5元。
为了讨论方便,选择用Microsoft Office Excel中RAND()函数产生随机数,让这些随机数在0~20之间均匀分布,以此作为企业每日的物料需求量。表2-2所示即为12天的物料需求量(数字仅保留小数点后一位)。
表2-2 物料需求量

计划采购方式采购批量为

因此,每次采购60 吨,每6 天采购一次。计划采购方式产生的费用如表2-3所示。
表2-3 计划采购方式产生的费用

订单采购方式前一天发出第二天的准确需求,在用料的当天到货,不存在库存。每天订货都支出5元的订货费,无法采用整车运输,只能是零担运输的方式。订单采购方式产生的费用如表2-4所示。
表2-4 订单采购方式产生的费用

表2-3和表2-4中,运费=到货量×对应运价费率(整车或零担);库存量=上一日结余库存量+当日到货量-当日物资需求量;持货成本=库存量×(每吨物料每日资金占用成本+保管费用)。从表2-3和表2-3不难看出,采用订单订购方式总费用更小,这种方式比计划采购方式节约了155.9元(4240.7-4084.8),节约率约4%。同时,订单采购方式最后库存量为0,而计划采购方式最后仍有库存8.2吨,如果企业继续使用这种材料,除了占用资金和保管费用外,尚不会造成其他后果,但如果企业在一段时间内不再使用这种材料,那么就形成了库存积压,会给企业带来严重的经济损失。
2.3.2 分析过程的计算机模拟
采用2.3.1节所述的手工计算方法可以对两种采购方式进行初步的比较,但也有其明显的不足之处,那就是模拟的期间较短,仅为12天的需求和采购情况。诚然,对一个较长时间的需求和采购情况进行模拟,其结论的可靠性将会更高。然而,用2.3.1节的表格手工计算的方法进行模拟很难对大数据量的情形展开分析,因而这里借助计算机程序化的应用工具,即Matlab进行分析。为了基于Matlab程序来讨论上述案例情景中的采购方式决策问题,首先要将表3-2和表3-3的计算过程抽象出来,明确采购费用的组成结构和计算过程。
计划采购方式下,采购费用包括订货费、运费、持货成本和缺货损失共计四项。每次订货都支出同样金额的费用,订货费用等于订货次数与单次订货费用的乘积。单次运费为订货量与整车运输费率的乘积。持货成本是持货支出费率与库存量的乘积。持货支出费率包括单位数量物料每天的资金占用成本、库存与保管费率两部分。每日库存量为“当日到货量+上日库存量-当日需求量”,如果库存量大于零,就产生了持货成本;如果库存量小于零,不会产生库存持有成本,但会导致缺货损失。每日缺货损失等于缺货量与缺货损失费率的乘积。同类费用每天发生的数量相加求和即为所讨论周期内的该类型总费用,四类费用之总和即为计划采购方式下的费用支出总额,如图2-4所示。

图2-4 计划采购方式采购费用计算流程
为了简化问题,虽然需求是随机的,但仍以平均每日需求量作为需求的基本指标,在不考虑缺货的情形下计算经济订购批量(EOQ),以此作为计划采购的订货批量。为了更贴近实际情况,当经济订购批量(EOQ)不是10吨的整数倍时,采取四舍五入的方式将其转化为10吨的整数倍。当然,也可以设定保险储备,计算允许缺货情形下的经济订购批量,然后再展开分析,本文此处从略,有兴趣的读者可以自行完成分析过程。
订单采购方式下,每天订货一次、到货一次(因此每小时到货一次情形与每天到货一次情形类似,在此简化处理)。这里为了研究方便,假设当天的到货数量(订货数量)完全等于当天的需求量,不产生库存,因而不存在持货成本和缺货损失。所以,订单采购方式下费用只包括订货费和运费两项。每次订货费用固定不变,每天订货一次,因此订货费用即为单次订货费与所讨论周期总天数的乘积。单日运费即为当日到货量与零担运输费率的乘积,各日运费之和即为总运费,如图2-5所示。为了简化问题,运费的计算不考虑在订单采购模式下部分采用整车运输、余下不足整车运输部分采用零担运输的情形,而是简单地选取了一个合适的运输费率(介于整车运输费率和小批量零散运输费率之间)一并进行计算。

图2-5 订单采购方式采购费用计算流程
根据上述计算流程,编写Matlab程序,对上述案例情景进行周期为100天的模拟。Matlab程序(M文件)见附录A。为了减少需求不确定性对分析结果的影响,模拟进行了100次。也就是说,每次模拟100天的采购情形,共进行100次这样的模拟过程,得到结果如图2-6所示。需要说明的是,本模拟过程受每次产生随机数(每日的物料需求量)不同的影响,结果略有不同,但总体特征不变。

图2-6 计划采购与订单采购成本支出比较(100天)
由图2-6不难发现,本案例情景下,订单采购成本支出在总体上明显小于计划采购成本支出。从100次的模拟情况来看,总费用平均节约了11.7%(订单采购节约金额/计划采购实际支出金额)。当然,订单采购支出大于计划采购的情形同样存在,这主要是因为不确定性需求的实际情况。这种情形在100次的模拟过程中出现了4次,总体上较少,因此,从统计意义上可以认为在上述案例给定的情景下订单采购方式更有价值。不仅从总费用支出角度有这样的结论,从采购费用变化的程度来看,计划采购支出的采购费用波动幅度很大,而订单采购支出的采购费用相对比较稳定。如果将分析周期由100天变为1000天,这一趋势就更加显著,如图2-7所示。

图2-7 计划采购与订单采购成本支出比较(1000天)
2.3.3 案例中的运价因素敏感性分析
2.3.2节所述的例中,从费用结构对比分析可以看出,订单采购方式具有较低的成本支出,主要归因于没有了持货成本和缺货损失,同时,订单采购单次采购流程简单,订购费用也产生了显著的减少。而计划采购方式采用了整车运输的批量运输方式,运输费用支出较小。基于这一分析,如果燃油价格上涨,运力紧张,从而导致运输价格整体上涨(零担运输价格在整车运输价格基础上上浮20%,这一特点保持不变),那么经计算可以发现,订单采购方式受到的影响较大。从定量的角度来看,当运输价格上涨到什么程度将会导致订单采购方式不经济?也就是,运输价格上涨到什么程度就需要将采购方式调整为计划采购?这一问题属于本案例中的采购成本对运价因素的敏感性分析。这里利用上述Matlab程序对此展开定量研究,只要对上述程序进行一些较小的修改即可,关于程序的修改本文不再赘述。
为了研究方便,将整车运输价格设定为从0.1~1.1 元/吨公里,每次加价幅度为0.01元/吨公里,找出不同运价与订单采购方式总费用节约率(订单采购节约金额/计划采购支出金额)对应关系,并将其以图形的方式展示出来,如图2-8 所示。从图2-8不难发现,随着运价的升高,虽然零担运输价格在整车运输价格基础上上浮20%的比例不变,订单采购方式的总费用节约率在持续下降。也就是说,随着运价的升高,将导致订单采购方式的优势被弱化,直至完全不占有优势。当整车运输价格达到0.45~0.55元/吨公里时,订单采购方式与计划采购方式费用支出基本相当。当整车运输价格高于0.55元/吨公里时,采用计划采购方式效果更好。

图2-8 运价对采购方式选择的影响
从这一分析过程可以看出,企业采购方式的选择并不是一成不变的,一定时期效果很好的采购方式,可能随着外部环境的变化而变差。发现和界定这些变化的临界点对企业经营决策具有重要意义。通过上述分析,企业决策者可以遵循以下原则进行采购方式选择决策,即在其他条件不变的情况下,整车运输价格高于0.55元/吨公里时,宜采用计划采购方式进行采购;整车运输价格低于0.45元/吨公里时,宜采用订单采购方式进行采购;整车运输价格位于0.45~0.55元/吨公里之间时,可保持原有采购方式不变,因为两种采购方式对成本的影响不大。
其实,除了运价因素外,其他因素也可能会影响采购方式的选择决策。读者可以自行分析。