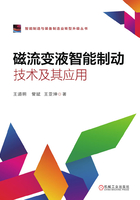
3.2.2 瞬态温度场仿真模型
以多盘式磁流变液制动器为研究对象,对其进行适当简化,忽略轴承、键槽、螺栓以及密封件等对温度场的影响,得到简化后的磁流变液制动器瞬态温度场仿真模型如图3.7所示。
在仿真前,需要在软件中导入磁流变液制动器各部分材料的热物性参数。表3.1所示为磁流变液制动器各部分所用材料不锈钢0Cr18Ni9、20钢、纯铜Cu、空气以及磁流变液MRF2035的热物性参数。
表3.1 磁流变液制动器各部分所用材料的热物性参数


图3.7 磁流变液制动器的瞬态温度场仿真模型
在瞬态温度场仿真模型的基础上,采用四面体网格单元对其进行网格划分,得到磁流变液制动器有限元网格划分结果如图3.8所示,整个仿真模型共有4490183个网格单元。
设定磁流变液制动器的初始温度等于环境温度25℃,制动过程中,作用于磁流变液制动器上的热载荷有:线圈区域生热率、各个工作间隙区域生热率以及制动器和周围环境间的辐射和对流换热。在Workbench仿真平台中,热载荷和边界条件可以以常量或者函数表达式的形式导入[9]。本仿真中,线圈区域生热率以常量导入,而各个工作间隙区域生热率以函数表达式导入。

图3.8 磁流变液制动器有限元网格划分
假定车辆制动时减少的行驶动能全部转化为制动盘和磁流变液之间的剪切摩擦热量,则工作间隙区域生热率ϕm可表示为

式中,Vm为制动器中磁流变液的体积。
假定线圈的发热功率全部转化为线圈区域的温升,则线圈区域生热率ϕc可表示为

式中,Vc为线圈体积。
根据所设计线圈的结构特点,其体积可表示为

式中,bc为线圈宽度;为线圈内半径;
为线圈外半径。
磁流变液制动器与周围环境接触部分包括静止部分和运动部分,因此同时存在自然换热与强制换热。其中,自然换热系数δs可表示为

式中,δc为自然对流换热系数;δr为辐射换热系数。
根据文献[10],取δs=9.7W·m-2·℃-1。
强制换热系数δk可表示为[11]

式中,ds为旋转表面的平均直径;为旋转轴的平均转速。
为了尽可能符合汽车实际制动情况,选择如图3.9所示的三种不同制动模式下进行瞬态温度场仿真。其中,模式一的制动减速度为2.5m/s2;模式二的制动减速度为5.5m/s2;模式三的制动减速度为:1~3s时为3.5m/s2、5~8s时为2m/s2、10~13s时为2m/s2、15~16.6s时为2m/s2。

图3.9 三种不同制动模式下车速随时间变化情况
结合式(3.5)和式(3.10)以及磁流变液制动器的结构参数,可以计算得到三种不同制动模式下工作间隙区域生热率随时间变化如图3.10所示。结合式(3.5)~式(3.14),可以计算得到边界条件中各参数的具体数值见表3.2。

图3.10 不同制动模式下工作间隙区域生热率随时间变化
表3.2 边界条件各参数及数值
