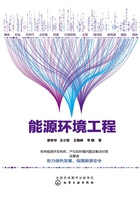
3.3.2 石油炼制
开采出来的石油(原油)可以直接作燃料用,但经济效益较差,若在炼油厂进行深加工,经济效益可以增加许多倍。而且飞机、汽车、拖拉机等也不能直接燃用原油,必须把原油炼制成燃料油才能使用。因此石油炼制是石油利用中非常重要的一环。
石油炼制是以原油为原料,采用物理方法生产各种燃料油和润滑油的加工过程。其主要加工方法有常减压蒸馏、重油裂化、石油精炼与油品精制。
① 常减压蒸馏 是分别在常压和减压条件下,通过蒸馏过程将石油分割为不同沸点范围的馏分,然后进一步加工利用,或除去这些馏分中的非理想组分,或经化学变化得到所需组成结构进而获得一系列合格产品。
② 重油裂化 是以蒸馏过程剩余的重质馏分油为原料,在热和催化剂的作用下发生裂化反应,转变成裂化气、汽油和柴油等轻质馏分油的过程。裂化工艺大体可分为热裂化和催化裂化两种。由于热裂化的产品质量较差,且开工周期短,因此热裂化已被催化裂化所代替。
③ 石油精炼 目的是提高产品的质量,以获得更多质量更高的油品。精炼方法主要有重整、异构化、烷基化和叠合。通过精炼可将普通直馏汽油重整或异构化为高辛烷值的汽油,将裂化气烷基化或聚合成高辛烷值的汽油,同时还可制得石油化工和有机化工的基本原料。
④ 油品精制 石油经过一次加工(蒸馏)、二次加工(裂化)所得到的汽油、喷气燃料油、煤油和柴油等燃料中由于含有各种杂质,产品性能不能全面达到使用要求,往往不能直接作为商品出售或使用,还需经过三次加工(包括石油烃烷基化、烯烃叠合、石油烃异构化等)才能生产高辛烷值的汽油组分和各种化学品,该加工过程称为油品精制。
3.3.2.1 石油炼制厂的类型
石油炼制企业的类型各异,根据主要产品的特性,石油炼制厂可分为四种类型。
(1)燃料型炼油厂
以生产汽油、喷气燃料油、柴油、燃料油等石油燃料为主要产品,同时也附带生产燃料气、芳香烃和石油焦。这类炼油厂的工艺特点是通过一次加工尽量提取原油中的轻质馏分,并利用裂化和焦化等二次加工工艺将重质馏分转化为汽油、柴油等轻质油品。随着石油加工向综合利用方向发展,这类炼油厂所占比例会越来越少。图3-6为燃料型炼油厂的生产工艺流程。
(2)燃料-润滑油型炼油厂
产品除燃料油外还生产各种润滑油原料,然后将这些原料加以精制,一般采用的过程包括溶剂脱蜡、溶剂精制、白土精制及加氢精制等,制得润滑油组分,并以这些组分为基本原料,根据润滑油品种和质量具体要求,再按一定比例加入各种添加剂,最后调配成润滑油成品。若以减压渣油为原料生产重质润滑油馏分,还需增加丙烷脱沥青装置。

图3-6 燃料型炼油厂的生产工艺流程
(3)燃料-化工型炼油厂
除生产各种燃料油品外,还利用催化裂化、延迟焦化、催化重整、芳烃抽提、气体分离等装置生产炼厂气、液化石油气和芳烃等作为石油化工原料。其工艺流程如图3-7所示。

图3-7 燃料-化工型炼油厂工艺流程
随着石油化学工业的发展,为综合利用石油资源,将炼油厂与石油化工厂联合组成石油化工联合企业,利用炼油厂提供的石油化工原料生产各种基本有机化工产品以及合成树脂、合成橡胶、合成纤维和化肥等,已成为石油化工行业实现集约化生产的趋势,并正在逐渐向“大容量、高参数、长周期”方向发展。所谓大容量,指生产规模扩大,单台装置的容量增大;高参数指生产工艺条件提高,以实现高转化率和高收率;长周期指采用各种技术手段和方法,确保装置能长时间安全高效运行。要满足上述这些要求,对石油化工行业提出了新的挑战。
(4)燃料-润滑油-化工型炼油厂
该炼油厂既生产燃料、润滑油类石油产品,又生产石油化工原料。其特点是装置类型多,产品种类广。
3.3.2.2 典型炼制工艺流程
石油炼制行业主要加工方法有常减压蒸馏、裂化、精炼与精制。
(1)常减压蒸馏
原油通过常减压蒸馏分离成若干个沸点范围适合作不同燃料的馏分。通常这种蒸馏是在两个塔(常压蒸馏塔和减压蒸馏塔)中进行的。常压蒸馏在大气压下进行,仅能分离出沸点较低的馏分。通过常压蒸馏,将原油分割为拔顶气馏分(C4及C4以下的轻质烃)、直馏汽油、航空汽油、煤油、轻柴油(沸点250~300℃)和重柴油(沸点300~350℃)等,而剩余部分从塔底排出进入减压蒸馏塔,在真空情况(8kPa)下进行,使重油的沸点降低,避免了裂解和焦化。常压重油可以进一步提取润滑油馏分。
常减压蒸馏的工艺流程如图3-8所示。原油经预热后进入脱盐罐,脱除盐水后经过一系列的换热器,使温度升高到200~250℃,然后进入初馏塔进行预分离,将原油中部分较轻的组分蒸出,经冷凝冷却后在塔顶回流罐作气液分离,液体的一部分返回塔顶作回流,另一部分作轻汽油(或称石脑油)送出装置。从初馏塔塔底出来的头拔原油,经常压加热炉加热至360~370℃,进入常压蒸馏塔,在此轻质油料气化蒸出。塔顶油气经冷凝冷却后在塔顶回流罐进行气液分离,液体的一部分返回塔顶作回流,另一部分作为汽油送出装置。常压塔一般有4~5根侧线,在此抽出液体,可依次得到航空煤油、灯用煤油、轻柴油和重柴油等。这些馏分在汽提塔中用水蒸气汽提,脱除轻组分后,与原油换热,冷却至规定温度送出装置。从初馏塔塔顶和常压塔塔顶的回流罐中分离出的石油气体为C1~C4轻质烷烃和少量轻油,可引至加热炉作燃料或经压缩后进行气体分馏,以回收液化石油气(液态烃)。

图3-8 常减压蒸馏工艺流程
常压塔塔底未气化的重油(常压渣油)经水蒸气汽提吹出轻组分后进加热炉,加热至400~410℃进入减压塔,在减压条件下使重质油气化蒸出。塔顶为不凝气和水蒸气,经冷凝后采用真空喷射器抽出不凝气,使塔内压力维持在2~8kPa。减压塔一般有3~5根侧线,用作引出润滑油原料或裂化原料。液体侧线经水蒸气汽提、换热、冷却至规定的温度后送出装置。
减压塔塔底渣油经水蒸气汽提,以提高拔出率,然后经换热、冷却至规定温度后送出装置。减压渣油经调合后可作为重质燃料油供炼钢厂或发电厂使用,或作为丙烷脱沥青、延迟焦化、氧化沥青装置的原料。
(2)催化裂化
中国的原油一般轻馏分较少,通常减压蒸馏后可得到10%~40%的汽油、煤油及柴油等轻质油品,其余的是重质馏分和残渣油。为了满足国民经济对轻质燃料油,尤其是汽油的需要,通常可采用催化裂化、催化重整、烷基化、异构化等方法,所以现代炼油厂中的催化裂化工艺十分重要,其装置性能的好坏对全厂的经济效益有显著的影响。
催化裂化是在热和催化剂作用下使重质油发生裂化反应,转变为裂化气、汽油和柴油等轻质馏分油的过程。原料采用原油蒸馏所得的重质馏分油或在重质馏分油中混入少量渣油,渣油是经溶剂脱沥青后的脱沥青渣油或常压渣油及减压渣油。催化裂化除得到高辛烷值(80以上)汽油外,还可得到裂化气,其中含有丙烯、异丁烯、正丁烯,可作基本有机化工的原料。催化裂化的工艺流程如图3-9所示,包括原料的催化裂化、催化剂的再生及产物的分离。

图3-9 催化裂化工艺流程
新鲜原料油经换热后与回炼油混合,经加热炉加热至300~400℃后至提升管反应器下部的喷嘴,原料油用蒸汽雾化并喷入提升管内,与来自再生器的高温催化剂(600~750℃)接触,随即气化并进行反应。由于反应使大分子变成小分子,油气体积增大,在管内的线速度不断增加,催化剂也被加速,一直到提升管口。油气在提升管内的停留时间很短,一般只有几秒钟,反应温度为480~530℃,压力为0.14MPa(表压)。反应产物经旋风分离器分离出夹带的催化剂后离开反应器去分馏塔。
积有焦炭的催化剂(称待生催化剂)由沉降器落入下面的汽提段。汽提段内装有多层人字形挡板并在底部通入过热水蒸气,待生催化剂上吸附的油气和颗粒之间空间的油气被水蒸气置换而返回上部。经汽提后的待生催化剂通过待生斜管进入再生器。
再生器的主要作用是烧去催化剂因反应而生成的积炭,使催化剂的活性得以恢复。再生温度一般为600~700℃,再生用的空气由主风机供给,空气通过再生器下面的辅助燃烧室及分布板进入密相床层。再生后的催化剂(称再生催化剂)落入溢流管,再经再生斜管送回反应器循环使用。再生烟气经旋风分离器分离出夹带的催化剂后,经双动滑阀排入大气。
(3)延迟焦化
延迟焦化是一种重质油热炼化工艺,在加热炉的高热强度炉管中,油品达到结焦温度,同时通过提高油品的流速使其无法结焦,而延迟到在焦炭塔中裂化、结焦。延迟焦化的原料多为重油、渣油、沥青及各种污油,产品主要为焦炭、汽油、柴油、蜡油、液态烃及副气等。
延迟焦化装置通常为间歇操作,最常用的为“一炉两塔”工艺,始终有一个塔处于生产状态,另一个处于准备冷焦、除焦或油气预热状态。来自加热炉的物料进入焦炭塔,待充装一定容积后,先用四通阀将物料切换至另一个焦炭塔。在焦炭塔内的油气经充分裂解、缩合后,轻组分分别进入分馏塔,焦炭留在塔内。再通过四通阀通入蒸汽,将遗留的油气进一步提升至放空冷却塔,同时冷却塔内温度。然后用水将塔内焦层冷却至80~90℃后,水从塔内排出,该过程所用的水称为冷焦水。延迟焦化装置通常采用水力除焦,即水力切焦器利用高压水产生的高速水流将焦炭切割成块,焦炭及水从焦炭塔内流出,进入储焦池,该过程所用的水称为切焦水。
(4)催化加氢
催化加氢是指石油馏分在氢气存在下催化加氢过程的通称,对提高原油的加工深度,合理利用石油资源,改善产品质量,提高轻油的收率以及减少大气污染都具有重要意义。
目前炼油厂采用的加氢过程主要有加氢精制和加氢裂化两大类。加氢精制主要用于油品精制,其目的是除掉油品中的硫、氮、氧等杂原子及金属杂质,有时还对部分芳烃进行加氢,改善油品的使用性能。所用原料有重整油、汽油、煤油、各种中间馏分油、重油和渣油。加氢裂化是在较高压力下烃分子与氢气在催化剂表面进行裂解和加氢反应生成较小分子的过程。根据原料的不同,加氢裂化分为馏分油加氢裂化和渣油加氢裂化。馏分油加氢裂化的原料主要有减压蜡油、焦化蜡油、裂化循环油及脱沥青油等,目的是生产高品质的轻质油品,如柴油、航空煤油、汽油等。渣油加氢裂化主要是热解反应,同时对产品进行加氢精制。
根据原料性质、产品要求和处理量大小,加氢裂化装置主要有一段加氢裂化和两段加氢裂化,我国引进的加氢装置两者均有。
1)一段加氢裂化
一段加氢裂化流程用于由粗汽油生产液化气,由减压蜡油、脱沥青油生产航空煤油和柴油。图3-10为直馏重柴油馏分(330~490℃)一段加氢裂化工艺流程。原料油经泵升压至16.0MPa,与氢气混合、换热后进入加热炉,反应器的进料温度为370~450℃。原料在反应温度380~440℃,空速1.0h-1,氢油比约为2500(体积比)的条件下进行反应。为控制反应温度,向反应器分层注入冷氢。反应产物经与原料换热后温度降至200℃,再经空冷器冷却,温度降至30~40℃之后进入高压分离器。反应产物进入空冷器之前注入软化水以溶解其中的NH3、H2S等,防止水合物析出而堵塞管道。自高压分离器顶部分出循环气,经循环氢压缩机升压后,返回反应系统循环使用。自高压分离器底部分出生成油,经减压系统减压至0.5MPa,进入低压分离器,在低压分离器中将水脱出,并释放出部分溶解气体,作为富氢气送出装置,可以作燃料用。生成油经加热后送入稳定塔,在1.0~1.2MPa下蒸出液化气,塔底液体经加热炉加热至320℃后送入分馏塔,最后得到轻汽油、航空煤油、冷凝柴油和塔底油(尾油),尾油可一部分或全部作循环油,与原料混合再去反应。
2)两段加氢裂化
图3-11所示为两段加氢裂化的工艺流程,原料油经泵升压并与循环氢混合后首先与生成油换热,再在加热炉中加热至反应温度,进入第一段加氢精制反应器,在加氢活性高的催化剂上进行脱硫、脱氮反应,原料中的微量金属也被脱掉,反应生成物经换热、冷却后进入高压分离器,分出循环氢。生成油进入脱氨(硫)塔,脱去NH3和H2S,作为第二段加氢裂化反应器的原料。在脱氨塔中用氢气吹掉溶解气、氨和硫化氢。第二段进料与循环氢混合后,进入第二段加热炉,加热至反应温度,在装有高酸性催化剂的第二段加氢裂化反应器内进行裂化反应。反应生成物经换热、冷却、分离,分出溶解气和循环氢后送至稳定和分馏系统。

图3-10 一段加氢裂化工艺流程

图3-11 两段加氢裂化的工艺流程
两段加氢裂化流程具有原料适用性广、操作灵活性大等特点,采用两段加氢裂化流程处理重质原料油生产重整原料油以扩大芳烃的来源,已成为许多国家重视的一种工艺方案。我国南京的金陵石化厂就是用胜利减压蜡油来生产重整原料油制取苯、甲苯和二甲苯的,取得了良好的经济效益。
(5)催化重整
催化重整是在加热、氢压和催化剂存在的条件下,使轻汽油馏分(或石脑油)的分子重新排列,转变为芳烃和异构烷烃,同时副产氢气及液化气的一种单元过程。原料通过预处理,得到馏分范围、杂质含量都合乎要求的重整原料,与循环氢混合,再经换热、加热后,进入重整反应器。反应器的入口温度一般为480~520℃,第一个反应器的入口温度比较低,后面的反应器入口温度稍高些。铂铼重整的操作条件一般为:压力1.8MPa,空速1.5h-1,氢油比约1200(体积比);铂重整的操作条件为:压力2.5~3MPa,空速2~5h-1,氢油比1200~1500(体积比)。反应器出来的反应产物经高压分离器分出富氢气体(含氢体积分数为85%~95%),重整油进入稳定塔,塔底得到重整汽油。
以生产芳烃为目的时,催化重整装置由原料预处理、重整、芳烃抽提和芳烃精馏四个部分组成。重整后需加氢,使烯烃变成烷烃,再经过稳定塔,脱去气态烃和戊烷,然后进行芳烃抽提。
连续重整是催化重整的重要组成部分,目前常用的连续重整工艺有UOP与IFP两种。
1)UOP连续重整工艺
其工艺流程如图3-12所示。重整通常设3~4个反应器,反应器从上而下叠置在一起,催化剂在反应器内靠重力向下移动。运转过程中积炭的催化剂即待生催化剂从反应器底部流出,被输送到具有特殊结构的再生器中进行再生。再生后的催化剂经氢气还原,再返回第一反应器,依次流经第二、第三、第四反应器,构成了催化剂连续再生回路。这一工艺的优点是产品收率高,氢产率和氢纯度高,产品质量稳定,运转周期长等。

图3-12 UOP连续重整工艺流程
1—再生器;2—反应器;3—加热炉;4—低压分离炉;5—高压分离器
2)IFP连续重整工艺
其工艺流程如图3-13所示。此工艺与UOP连续重整工艺的不同之处在于多个反应器采用并列式放置,新鲜催化剂从一个反应器顶部加入,逐步移至底部,连续地用氢气提升到后一个反应器的顶部,流经三个反应器后,用氮气将第三反应器底部流出的积炭催化剂提升到一个固定床再生器进行再生,再生后的催化剂循环使用。
3.3.2.3 石油炼制的产品
石油炼制的原理是利用石油中各种不同成分具有不同沸点的特点,将原油加热,从而在不同温度范围内(称为馏程)获得不同的石油产品。在接近大气压力条件下,于40~180℃馏出者为汽油,于150~300℃馏出者为煤油,于200~350℃馏出者为直馏柴油,余下者为高沸点的重质油,称为常压重油。

图3-13 IFP连续重整工艺流程
1~3—反应器;4—再生器;5—干燥器
通过常压蒸馏所获得的各种馏分仍是一个多组分的混合物,可进一步加工,例如把高沸点的常压重油加热至400℃以上可以继续分馏出各种重质油来。但炼油厂为了简便,一般采用降低压力的方法来提取,即根据气压降低、沸点下降的原理,在压力为0.01MPa下,在400℃左右可以从常压重油分馏出在常压下沸点为700℃以下的石油产品。降压分馏的产品有重柴油及沸点较高的蜡油(可作为生产润滑油的原料),余下者称减压重油,其初沸点大于340~370℃。通常将常压重油与减压重油统称为直馏重油。
为了增产轻质油、增加品种和提高质量,炼油厂还采用裂化的方法从某些重质油中生产出汽油、柴油以及一些高级车用汽油和航空汽油等。所谓裂化就是使分子较大的烃类裂解为分子较小的烃类,以取得轻质油产品。裂化方法又可分为热裂化和催化裂化。经过上述加工方法可获得可燃气、汽油和润滑油等产品,残留的高沸点重质油称裂化重油,其初沸点大于500~550℃。与直馏重油相比,其密度、黏度及所含杂质均较高,燃料稳定性差,易沉淀堵塞油管,燃烧性能亦较差。近年来还采用加氢等工艺来增产轻质油产品。通过以上介绍可以看出,通过提高石油加工深度,可以获得更多的轻质石油产品。
按石油产品的用途和特性,可将其分成14大类,即溶剂油、燃料油、润滑油、电器用油、液压油、真空油脂、防锈油脂、工艺用油、润滑脂、蜡及其制品、沥青、油焦、石油添加剂和石油化学品。主要石油产品的用途如下:
① 溶剂油:按用途可分为石油醚、橡胶溶剂油、香花溶剂油等,可用作橡胶、油漆、油脂、香料、药物等的工业溶剂、稀释剂、提取剂,在毛纺工业中作洗涤剂。
② 燃料油:按燃料油的馏分组成可分为石油气、汽油、煤油、柴油、重质燃料油,柴油之前的各种油品统称为轻质燃料油。按使用对象或使用条件,各种燃料油又可分成不同级别,如汽油可分车用汽油和航空汽油,前者供各种形式的汽车使用,后者供螺旋桨式飞机使用;煤油可分航空煤油和灯用煤油,前者作喷气式飞机的燃料,后者供点灯用(分为灯用、信号灯用)、拖拉机用,也可作洗涤剂和农用杀虫药溶剂;柴油可分为轻柴油(用于高速柴油机)、重柴油(用于低速柴油机)、船用柴油和直馏柴油。
石油气可用于制造合成氨、甲醇、乙烯、丙烯等。
③ 润滑油:润滑油品种很多,几种典型的润滑油如:汽油机油和柴油机油,前者用于各种汽油发动机,后者用于柴油机,主要是供润滑和冷却;机械油,用于纺织缝纫机及各种切削机床;压缩机油、汽轮机油、冷冻机油和气缸油;齿轮油,又分为工业齿轮油和拖拉机、汽车齿轮油,前者用于工业机械的齿轮传动,后者用于拖拉机、汽车的变速箱;液压油,用作各类液压机械的传动介质;电器用油,又分为变压器油、电缆油,主要起绝缘作用。因其原料属润滑油馏分范围,通常也将其包括在润滑油中。
④ 润滑脂:是在润滑油中加入稠化剂制成的。根据稠化剂的不同,又可分为皂基脂、烃基脂、无机脂和有机脂4大类。用于不便于使用润滑油润滑的设备,如低速、重负荷和高温下工作的机械,工作环境潮湿、水和灰尘多且难以密封的机械。
⑤ 石蜡和地蜡:石蜡和地蜡是不同结构的高分子固态烃。石蜡分为精白蜡、白石蜡、黄石蜡、食品蜡等,可分别用于火柴、蜡烛、蜡纸、电绝缘材料、橡胶、食品包装、制药工业等。
⑥ 沥青:沥青可分为道路沥青、建筑沥青、油漆沥青、橡胶沥青、专用沥青等多种类型。主要用于建筑工程防水、铺路以及涂料、塑料、橡胶等工业中。
⑦ 石油焦:石油焦是优良的碳质材料,用于制造电极,也可作冶金过程的还原剂和燃料。