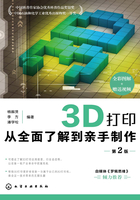
3.6 其他前沿3D打印技术
经过前几年的行业洗牌后,3D打印越来越注重应用场景,也促使技术不断更新升级。传统的3D打印技术在打印速度、材料性能、生产成本上存在很大局限,多数用来原型打样、模具制作、非核心零部件的替换生产,应用场景并没有打开。
随着消费升级趋势日显,更多行业领域产品升级和重塑的需求促使3D打印技术进一步突破。可喜的是,新的3D打印技术不断出现,不仅在打印速度上得到很大提升,还结合新材料技术,实现了打印件的应用性能,带来了顺应新消费的更人性化的使用体验,使体验更接近完美。相信不久的将来,3D打印技术将具备规模化制造的应用条件,颠覆传统制造业的产品设计思维和供应链模式,形成更具创意思维的新制造。
3.6.1 CLIP技术和LEAP技术
3.6.1.1 CLIP技术
成立于2013年的位于美国加州的一家3D打印初创公司Carbon,在2015年Science的一期刊文里介绍了其革命性的3D打印技术——连续液体界面成型(CLIP: Continuous Liquid Interface Production)。CLIP技术利用光固化树脂,氧气作为抑制剂,在液体中成型三维物体,其成型速度比当时市场上任意一种3D打印技术都要快25~100倍。
CLIP技术源自传统的Bottom-up DLP。该技术的关键是氧气抑制,这通常被认为是传统SLA/DLP的缺点,因为氧气淬灭了由紫外光激发光引发剂形成的自由基,导致固化不完全、表面发黏。而CLIP是通过利用氧气来抑制固化从而达到高速打印的目的:在紫外图像投影平面下方具有透氧窗口,产生“死区”(持久性液体界面),在透氧窗口和聚合部分之间抑制聚合反应。这样,固化部分不会黏附到料盒的底部,因此省去了最为耗时的剥离步骤,打印速度高达50cm/h甚至更快(图3-14、图3-15)。这种打印速度,让传统SLA/DLP望尘莫及。

图3-14 采用CLIP技术打印“埃菲尔铁塔”

图3-15 CLIP技术原理
但也因其核心技术原理,CLIP仍存在一些限制其广泛应用的缺点。首先,氧气抑制的作用仅存在于自由基聚合中,这限制了CLIP打印原材料的通用性。其次,为了实现快速打印,必须精密控制透过膜的氧气量,其影响“死区”厚度,决定了打印稳定性。因而,CLIP技术3D打印机的机械设计相对复杂,会较大幅度增加打印机的造价。CLIP技术旨在发挥其快速打印的优势,进行大规模生产。然而,高成本限制了这一技术的广泛量产应用。因而,建造一个有数百台CLIP 3D打印机的工厂(图3-16),并不便宜。

图3-16 CLIP技术3D打印机
作为较早提出快速3D打印概念的Carbon公司,目前在量产应用市场正在尝试运动鞋等消费品领域、汽车零部件等工业领域、齿科牙模等医疗领域,取得了一定的开创性成果。
3.6.1.2 LEAP技术
不同于Carbon的CLIP技术原理,一家起源于我国清华大学边上的30m2宿舍里的3D打印公司清锋时代,在2016年自主发明了同样快速的3D打印技术——LEAP(Light Enabled Additive Production)。LEAP的技术核心在于,无需氧气抑制环节,就可以实现最高120cm/h的打印速度,相较传统3D打印提升100倍以上,这在国内史无前例,相比于Carbon速度甚至更快(图3-17)。

图3-17 LEAP技术3D打印结构体
LEAP技术也是基于Bottom-up DLP,通过使用ARI(Advanced Release Interface)改性界面,解决了光敏树脂在打印过程的液体粘连问题,从而实现连续快速成型(图3-18)。除了超快的速度,LEAP技术的另一个优点是不需要氧气来抑制自由基聚合,这使得打印机可适用更多种不同的材料,并且打印机的造价成本要低得多。通过这种方式,LEAP技术提供了更为宽广的量产应用可能。

图3-18 LEAP技术原理示意
同时,LEAP技术3D打印机通过软硬件的一体架构,能够实现产品的模拟打印、数据分析以及最终成型制造的智能化生产体系。利用软件的参数化设置对设备进行个性化调试,以验证得到新材料的最佳性能,从而提高符合应用场景需求的材料研发效率。
3.6.2 Desktop Metal技术
位于美国马萨诸塞州的金属3D打印初创公司Desktop Metal,成立于2015年,已经推出两款3D打印金属产品,分别是Studio System和Production System,涵盖了从原型到批量生产的整个产品生命周期。不仅大幅提升金属3D打印速度,还能降低每个零部件的制造成本,并提供更快的生产速度、更高的安全性能和更好的产品质量(图3-19)。

图3-19 采用Desktop Metal技术的金属打印件
Studio System是一款适用于办公环境的快速成型金属3D打印系统(图3-20),包括打印机、脱模机和烧结炉,可在办公环境或工厂车间生产复杂且高品质的金属3D打印部件。该系统采用一个专有的工艺,名为结合金属沉积(BMD:Bound Metal Deposition),DM公司将其比作金属的FDM(熔融沉积式)。让人印象深刻的是,Studio System比现有的金属激光技术便宜10倍,速度则提升了100倍。此外,可以使用超过200多种合金,并能够同金属粉末一起用于金属注射成型,打印出来的金属零件可以媲美传统意义上的注塑成型工艺。

图3-20 Desktop Metal桌面金属机集群Studio System+
Production System则是一款可实现高分辨率金属零部件批量生产的3D打印系统(图3-21),可以大规模生产金属3D打印零部件。该系统采用一项专有的单通道喷射(SPJ)技术,制造金属零件的速度比现有的基于激光的金属3D打印系统快100倍,显著降低每个零件的制造成本,使其成为替代铸造等更广泛使用的金属制造技术的新制造技术。

图3-21 Desktop Metal量产金属3D打印系统Production System
3.6.3 惠普的MJF技术
2014年2D打印巨头惠普公司发布了一项创新3D打印技术——Multi Jet Fusion(MJF),被称为多射流熔融3D打印技术,2016年惠普正式推出基于该技术的3D打印机(图3-22)。这是基于他们现有的高分辨率2D热喷墨技术开发的一种3D打印技术,这种优化的打印方式不仅令MJF具备了10倍于选择性激光烧结(SLS)技术和熔融沉积成型(FDM)技术的超高速度,而且不会牺牲打印精度。

图3-22 惠普MJF技术3D打印机
惠普所用的多射流熔融(Multi Jet Fusion) 3D打印技术,其成型步骤如图3-23所示。

图3-23 MJF技术成型步骤
a—铺设成型粉末(铺粉厚度70~100μm);b—喷射助熔剂(fusing agent);c—喷射精细剂(detailing agent);d—在成型区域施加能量使粉末熔融(注意:喷射精细剂的区域并没有被熔融);e—重复步骤a~d直到所有的层片成型结束

图3-24 惠普全彩色MJF技术打印的彩色手机壳
惠普MJF技术的推出,在一定程度上将3D打印技术又向前推进了一大步,就目前来看,该技术具有很多优势。
(1)打印效率大幅提升,比常规的3D打印技术快10倍。
(2)材料几乎可以达到100%重复利用,材料利用率高,成本低。
(3)支持各行业新应用的开放式材料与软件创新平台。
(4)打印件性能高,可以用于最终零部件。
除此之外,MJF技术还有很强的拓展性,惠普还推出了基于该技术的全彩色3D打印机(图3-24)和金属3D打印机。
其中彩色打印设备标配了4种颜色剂,包括黑色、青色、品红色、黄色,可以混合出1600万色。以及3种热剂,包括助熔剂、细化剂、明亮助熔剂,未来可以配置多达8种打印剂,从而实现导电、光激荧光、半透明、弹性等效果。而金属打印设备被称为Metal Jet,是一种“voxel-level binder jetting technology”(体素级黏合剂喷射技术),其效率比目前的金属3D打印系统高出50倍。惠普Metal Jet将首先应用于生产不锈钢零部件,可以打印出各项性能均满足或高于ASTM和MPIF标准的成品。
3.6.4 电子束熔化(EBM)
1994年瑞典ARCAM公司申请的一份专利,所开发的技术称为电子束熔化成型技术EBM(Electron Beam Melting),ARCAM公司也是世界上第一家将电子束快速制造商业化的公司,并于2003年推出第一代设备,此后美国麻省理工学院、美国航空航天局、北京航空制造工程研究所和我国清华大学均开发出了各自的基于电子束的快速制造系统(图3-25)。

图3-25 ARCAM公司EBM技术3D打印机
EBM技术利用电子束熔化铺在工作台面上的金属粉末,与激光选区熔化技术类似,利用电子束实时偏转实现熔化成型。电子束由位于真空腔顶部的电子束枪生成。电子枪是固定的,而电子束则可以受控转向,到达整个加工区域。电子从一个丝极发射出来,当该丝极加热到一定温度时,就会放射电子。电子在一个电场中被加速到光速的一半。然后由两个磁场对电子束进行控制。第一个磁场扮演电磁透镜的角色,负责将电子束聚焦到期望的直径。然后,第二个磁场将已聚焦的电子束转向到工作台上所需的工作点(图3-26)。

图3-26 EBM技术原理图
电子束融化成型技术采用高能电子束作为加工热源,扫描成型可通过操纵磁偏转线圈进行,没有机械惯性,且电子束具有的真空环境还可避免金属粉末在液相烧结或熔化过程中被氧化。与激光选区熔化SLM相比,EBM还具有以下优势。
(1)成型过程效率高,零件变形小,成型过程不需要支撑,微观组织更致密。
(2)真空环境排除了产生杂质(如氧化物和氮化物)的可能。
(3)能打印高熔点的难熔金属,并且可以将不同的金属融合。
(4)由于电子束的转向不需要移动部件,所以既可提高扫描速度,又使所需的维护很少。
当然,EBM技术也有以下劣势。
(1)EBM技术成型室中必须为高真空,才能保证设备正常工作,这使得EBM技术整机复杂度提高。
(2)EBM技术需要将系统预热到800℃以上,使得粉末在成型室内预先烧结固化在一起,高预热温度对系统的整体结构提出非常高的要求。
(3)电子束技术打印出的工件精度较差,因此,对于精密或有细微结构的功能件,电子束选区熔化成型技术是难以直接制造出来的。
EBM技术可成型的材料广泛,如工具钢、钛合金、镍合金,甚至耐火的钼合金等导电金属材料等,电子束还可用于对光能具有较高反射作用的金属沉积成型:如在室温下,Ti-6Al-4V材料对激光反射较为严重,采用激光烧结工艺,能量利用率很低,而此材料对电子束的反射率只有10%左右,具有较高的能量利用率。EBM技术主要应用于航空航天制造、汽车制造、医疗器械制造等领域(图3-27)。

图3-27 采用EBM技术3D打印的人体髋臼杯
3.6.5 SLM+CNC
目前我们在国内最常见的制造设备,一般是独立的CNC机床(减材制造),或者独立的金属3D打印机(增材制造)设备。既然采用SLM(选择性激光熔融)技术3D打印出的金属工件经常需要进行CNC机加工处理,那么为什么不将SLM和CNC直接复合在一台设备中呢?
增材和减材制造技术的组合研究已经有20多年历史,但直到近些年才在民用领域有一些应用经验。第一台商用混合机床是20世纪90年代末期日本的一所大学研究出来的,是将激光粉末熔融与CNC加工相结合的机床。2002年,日本松浦机械制作所研发出金属增减材复合加工设备(图3-28)。随后,德国德玛吉(DMG)、日本沙迪克(Sodick)、中国亚美精密等单位陆续推出增减材复合设备。

图3-28 日本松浦机械制作所的金属增减材复合加工设备
因为在同一台机床上可实现“加减法”的加工,对于传统切削加工无法实现的特殊几何构型或特殊材料的零件,零件成型阶段由增材制造承担,后期的精加工与表面处理,则由传统的减材加工承担。由于在同一台机床上完成所有加工工序,不仅避免了原本在多平台加工时工件的夹持与取放所带来的误差积累,提高制造精度与生产效率,同时也节省了车间空间,降低了制造成本。
其工艺流程简化来讲包括以下三个步骤。
(1)金属粉末均匀平铺。
(2)以激光照射方式使金属粉末熔融凝固。
(3)之后再利用旋转刀具进行高速铣削高精度精加工。
(4)重复以上步骤直至零件加工完成(图3-29)。

图3-29 沙迪克SLM+CNC复合机原理图
a—铺粉;b—SLM激光熔融;c—CNC机加工
随着增材制造的发展以及其局限性的突出,国际上越来越多的学者和研究机构把目光转向基于增减材的复合加工制造。相比于国内,国际上对基于增减材制造的复合加工技术的研究开展得比较早,研究的内容也比较多。但总的来说,该项技术仍然处于研究与探索阶段。
3.6.6 轮廓工艺
其工作流程与我们常见的FDM(熔融沉积)技术非常相近,“轮廓工艺”的3D打印机看起来就像一台巨型的FDM 3D打印机。不同之处在于所使用的材料不是PLA等塑料线材,而是混凝土,混凝土不需要加热,直接通过巨大的喷头将混凝土按照电脑上的数据模型喷在相应的位置,混凝土在空气中逐渐凝固定型,层层堆叠直至打印出一幢房子。
“轮廓工艺”的发明人南加州大学教授比赫洛克·霍什内维斯(Behrokh Khoshnevis)这样形容该技术:“轮廓工艺”其实就是一个超级打印机器人,其外形像一台悬停于建筑物之上的桥式起重机,两边是轨道,而中间的横梁则是“打印头”,横梁可以上下前后移动,进行X轴和Y轴的打印工作,然后一层层地将房子打印出来(图3-30)。

图3-30 “轮廓工艺”概念图
与传统的建筑工艺相比,“轮廓工艺”有很多优点。
(1)工作速度非常快,24h之内能打印出一栋两层楼高、2500平方英尺(约合232m2)的房子。
(2)“轮廓工艺”可以做到全程由电脑程序操控,将节省45%~55%的人工,减少能源消耗,降低排放。
(3)可以打印出弧形或波浪形等独特外观,而且节省材料。
(4)利用该技术未来或许可以就地取材,在月球上建造栖息地。
3.6.7 生物3D打印技术
器官移植可以拯救器官被损坏的患者生命,然而事实上绝大部分患者找不到匹配的器官捐献者,即便成功获得了移植,也会存在排异反应等难以避免的弊端。不过,随着生物3D打印技术的问世,这些问题的解决有了新希望。
生物3D打印技术是一项前沿的新技术,其融合了3D打印和生物组织工程等技术。3D生物打印这一技术概念最早是由美国Clemson University、University of Missouri、Drexel University等大学的教授在2000年左右提出的,2003年Mironv V和Boland T在Trends in Biotechnology杂志系统提出“器官3D打印”这一概念。2002年左右,清华大学颜永年教授团队率先在国内开展3D生物打印技术研究。
生物3D打印技术的成型工艺也是采用我们本章前面介绍的熔融挤压打印、光固化立体打印等技术。只不过生物3D打印所使用的原料是生物墨水,而非传统的塑料材料。研究者会从人体骨髓或脂肪中提取干细胞,再以生物化学手段将其“改造”(分化)为不同类型的其他细胞后,封存为“墨粉”。通过3D打印生物材料或细胞单元,可以用来制造医疗器械、组织工程支架和组织器官等制品(图3-31)。

图3-31 Organovo生物3D打印机
清华大学生物制造中心将生物3D打印技术分为以下5个应用层次。
(1)无需考虑生物相容性的非体内植入物,用于3D打印成型个性化医疗器械和生理/病理模型,主要应用于术前规划、假肢定制等领域。
(2)具有良好生物相容性材料的永久植入物的制造,包括人造骨骼、非降解骨钉、人工外耳、牙齿等(图3-32)。

图3-32 生物3D打印技术制造的耳朵
(3)具有良好生物相容性和可降解性生物材料的组织工程支架的制造。组织工程支架不仅需要具有良好的生物相容性,能够支持甚至促进种子细胞的增殖分化和功能表达,同时支架材料需要适当的降解速率,在新组织结构的生成后,支架降解为可被体内完全吸收或排除的物质,应用领域包括可降解的血管支架等。
(4)细胞3D打印技术,用于构建体外生物结构体。将细胞、蛋白及其他具有生物活性的材料作为3D打印的基本单元,以离散堆积的方式,直接进行细胞打印来构建体外生物结构体、组织或器官模型。
(5)体外生命系统工程。通过对干细胞、微组织、微器官的研究,建立体外生命系统、微生理组织等。体外生命系统工程的研究不仅使生物制造学科拓展到复杂体外生命系统和生命机械的构建及制造,也是细胞3D打印、微纳及微流控芯片技术、干细胞技术和材料工程技术等诸大学科的进一步大交叉。