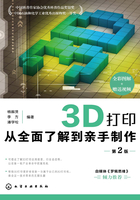
3.5 激光熔融式(SLM)
选择性激光熔融技术(Selective Laser Melting,SLM),又被称作激光选区融化技术。其技术原理与选择性激光烧结(SLS)技术非常相似,但又区别于SLS。SLS工艺中粉体未发生完全熔化,成型件中含有未熔化颗粒,可能会导致内部疏松、致密度低、力学性能差等工艺缺陷。为获取全致密的激光成型件,同时也受益于2000年之后激光快速成型设备的长足进步,SLM技术迅速发展起来。
SLM技术所使用的原材料主要为金属粉末状材料,包括钛合金、不锈钢、模具钢、高温合金、铜合金等。通过高功率的激光,可以将金属粉末加热到上千摄氏度,从而融化金属粉末并成型。
3.5.1 技术原理
1995年,德国Fraunhofer激光器研究所(Fraunhofer Institute for Laser Technology,ILT)最早提出了选择性激光熔融技术(Selective Laser Melting,SLM),用它能直接成型出接近完全致密度的金属零件。SLM技术不依靠黏结剂而是直接用激光束完全熔化粉体,成型性能及稳定性得以显著提高,可直接满足实际工程应用。SLM技术的主要发明人之一,是迪特·施瓦泽(Dieter Schwarze)博士。
SLM技术的原理如图3-12所示,其主要加工过程与SLS工艺基本一致,开始打印以后的工艺流程也是先采用铺粉辊平铺一层金属粉末材料,接着激光束按照该层的截面轮廓在粉层上照射,使被照射区粉末熔融并与下面已制作成型的部分实现黏结;当一个层截面被打印完成后,打印平台下降一个层厚的高度,铺粉系统为凹陷的工作台铺上新的粉材;然后控制激光束再次熔融新层,如此循环往复,层层叠加,直到完成整个三维零件的打印成型工作;最后,将未使用的粉末回收到粉末缸中,取出已成型工件。

图3-12 SLM技术原理
同时,两者也有一些不同之处。
(1)使用的激光器不同,SLS技术一般使用的是波长较长(9.2~10.8μm)、功率比较小的CO2激光器。SLM技术为了更好地熔化金属,需要使用金属有较高吸收率的激光束,所以一般使用的是Nd-YAG激光器(1.064μm)和光纤激光器(1.09μm)等波长较短的高功率激光束。
(2)使用的材料不同,SLS技术所使用的材料一般为熔点较低的PA(尼龙)、TPU(热塑性聚氨酯弹性体橡胶)、PS、蜡粉、树脂砂等。而SLM技术所使用的材料一般是熔点较高(上千摄氏度)的金属粉末,比如钛合金、不锈钢、模具钢、高温合金等。
(3)支撑不同,SLS工艺一般不需要添加支撑结构,而SLM工艺则需要,其主要作用是承接下一层未成型粉末层,防止激光扫描到过厚的金属粉末层,发生塌陷;另外,由于成型过程中粉末受热熔化冷却后,内部存在收缩应力,导致零件发生翘曲等,支撑结构连接已成型部分与未成型部分,可有效抑制这种收缩,能使成型件保持应力平衡。
(4)后处理方式不同,由于SLS工艺没有支撑结构,因此后处理时当整个原型被取出后,可以用刷子小心刷去表面粉末,清理干净后即可得到最终零件。而SLM工艺由于添加了支撑结构,因此打印完成后需要使用线切割将打印工件从平台上切割下来,再使用钳子等工具拆除支撑,随后还需要进行热处理和表面机加工等,从而满足对工件的机械性能和表面精度要求。
除了这些区别之外,两种技术工艺在保护气体、打印室预热、应用领域等方面也有着诸多区别,在此不再一一赘述。
3.5.2 工艺过程
目前SLM技术制造出的工件性能已经可以和锻造相媲美,优于铸造。但由于其成本高昂,因此,该工艺率先在航空航天、医疗等领域得到应用。如今,随着技术的日渐成熟,材料成本降低等因素的影响,SLM技术在齿科、汽车、随形流道模具等领域也开始应用。
SLM技术的工艺过程与SLS极其相似,其具体工艺过程可概括如下。
(1)整个打印仓在打印期间,仓内温度一般为室温,或预热到不超过200℃(消除工件应力)。另外,打印仓内需要在惰性气体氮气/氩气的保护下。
(2)铺粉辊将材料粉末铺撒在已成型零件的上表面并刮平。
(3)使用高强度的光纤激光器在刚铺的新层上照射出零件的层截面,材料粉末在高强度的激光照射下被烧融在一起,并与下面已成型的部分相黏结。
(4)当一层截面被烧融完成后,通过铺粉系统新铺一层粉末材料,然后进行下一层截面的打印。
选择性激光熔融技术有着明显的优势,但是也同样存在缺陷。首先是粉末烧融带来的表面粗糙、支撑结构、内应力等,需要进行后期处理才能作为最终工件;其次是需使用大功率激光器,使得需要较高的设备成本和维护成本,以及配套的保护部件、控制部件,设备整体技术复杂度高、制造难度大。所以目前SLM设备的应用范围主要集中在高端制造领域。
3.5.3 技术特点
与其他3D打印机技术相比,SLM工艺最突出的优点在于可以打印高熔点的金属材料,打印出的金属工件可以用于工业零部件。其典型的代表案例就是GE为LEAP喷气发动机设计的燃油喷嘴,完全使用SLM金属3D打印技术制造,将20个金属零部件直接合成为1个部件。截至2018年10月份,GE已经完成30000个3D打印燃油喷嘴的制造,将3D打印技术用于航空航天零部件的批量制造。
具体来讲,SLM的优点主要有以下几点。
(1)与其他3D打印工艺相比,能直接成型出接近完全致密度的金属零件,零件强度高、材料属性优异,可以直接作为终端产品使用。
(2)可供使用的原材料种类众多,包括钛合金、不锈钢、铝合金、钴铬合金、镍基合金、模具钢、铜合金等。
(3)与传统制造技术相比,可以进行轻量化的设计和制造,替代传统的零部件,如果轻量化再与特定功能(如冷却、减震、梯度功能等)相结合,那么这是其他技术无法比拟的。
相对其他3D打印技术,其缺点主要包括以下几个方面。
(1)激光器、振镜等关键零部件成本高,材料成本高,使得SLM打印成本相对高昂。
(2)支撑结构、内应力、表面粗糙等问题的存在,使得需要进行相对复杂的后处理才能得到最终工件。
(3)打印过程中需要使用惰性气体进行保护。
(4)打印效率有待提升。
3.5.4 典型设备
虽然SLM技术商业化比较晚,但是由于其工业应用潜力巨大,因此目前全球范围内从事SLM设备研发的公司不在少数,其中比较有代表性的包括德国EOS、德国SLM Solutions、美国GE Additive、中国华曙高科、中国汉邦科技等公司。国内从事SLM技术研究的高校包括西北工业大学、华南理工大学等。
图3-13是一款比较典型的SLM设备,德国SLM Solutions公司的SLM®280 2.0型号设备,可以打印尺寸在280mm×280mm×365mm范围内的金属工件。

图3-13 SLM Solutions公司的SLM®280 2.0选择性激光熔融3D打印机
从未来发展来看,SLM技术是非常具有潜力的一种技术,随着可打印金属粉末种类的丰富、打印效率的提高、打印成本的下降、打印性能的提升,SLM技术应用前景广阔。目前在航空航天、医疗、齿科、模具、汽车等领域已经被作为先进制造技术所采用,未来在这些行业会进一步普及,并且会在新的领域爆发出应用场景,将从根本上替代部分传统的制造手段。