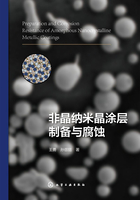
1.2 铁基非晶纳米晶涂层制备
铁基非晶合金制备技术包括:熔体甩带技术;磁控溅射技术;热喷涂技术。
铁基非晶合金应用途径包括:作为软磁材料;提高泊松比改善其塑性;作为涂层应用。
通常非晶合金的获得要求较高的冷却速率(106K/s以上),故常以微米量级粉末或条带样品存在,极大地限制了其应用。随着块体金属玻璃的出现,利用高玻璃形成能力的合金成分制备非晶态合金涂层引起了人们的极大兴趣。铁基非晶态合金具有高强度、高硬度和优异的耐蚀性,而块体材料却表现出非常差的塑韧性,这些因素使得铁基非晶态合金作为一种涂层材料更具应用前景。
1.2.1 铁基非晶涂层
2000年,McCartney等[43]采用超音速火焰(high⁃velocity oxy⁃fuel,HVOF)喷涂法制备了Ni⁃Cr⁃Mo⁃B非晶纳米晶合金涂层,实现了热喷涂制备非晶纳米晶涂层。2001年Branagan等[44]采用HVOF法制备了Fe⁃Cr⁃Mo⁃B⁃C⁃Si⁃Al非晶铁基合金涂层,并申请了专利,实现了铁基非晶纳米晶涂层的制备。
作为高耐蚀、耐磨的涂层材料是走向工业化应用的突破口之一。近年来,国际上诸多研究组纷纷开展非晶态金属涂层的制备工作,在Fe基、Ni基等体系中已成功获得完全非晶态或部分非晶态的高质量涂层。铁基非晶合金高的强度(>3GPa)、高的硬度(>1000HV)、高的热稳定性(晶化温度>500℃)以及优异的耐腐蚀性能(是优质不锈钢的10~1000倍)、低廉的价格及简单的制备工艺等,有望作为新型耐蚀耐磨材料得以应用。缺乏塑性形变是限制块体非晶合金作为结构材料应用的主要技术瓶颈。
2002年,美国国防部和美国能源部启动了“HPCRM”(high performance corrosion resistant materials)工程及“SAM”(structure amorphous metal)重大研究项目,其目的旨在推动非晶钢合金在工业中的应用并致力于非晶态高耐蚀防护涂层的研发。该项目在Lawrence Livermore National Laboratory首席科学家Joseph C.Farmer的领导下,集合威斯康星大学(University of Wisconsin⁃Madison)、加州大学戴维斯分校(UC,Davis)、加州大学伯克利分校(UC,Berkeley)、凯斯西储大学(Case Western Reserve University)四所大学和橡树岭国家实验室(Oak Ridge National Laboratory)及美国海军研究实验室(United States Naval Research Laboratory)等国家实验室科研人员,自2002年以来进行了卓有成效的工作。项目内容涉及合金设计及成分选择、材料合成、热稳定性、腐蚀性能、环境断裂性、力学性能、辐射效应及一些重要的潜在应用[45⁃48]。在与NanoSteel公司合作后,为国防部和能源部开发出以SAM开头命名的一系列性能优异的铁基非晶合金[49⁃51]。SAM制备母合金体系为SAM40(Fe52.3Cr19Mn2Mo2.5W1.7B16C4Si2.5),开发的其他系列SAM均以该合金为基础,如[(SAM40)100-x+Yx],Y是所添加元素种类,如Ni、Cr、Mo、W、Y、Ti、Zr;x是添加元素的原子分数,遵循1、3、5、7原则,衡量指标则为能极大提高玻璃形成能力或腐蚀阻力。SAM项目主要有三个长期目标,开发耐蚀性能优异的铁基非晶纳米晶涂层,使其耐蚀性能优于316L不锈钢、镍基合金C⁃22和钛合金7。
SAM涂层研发的初衷主要用于核废料(spent nuclear fuel)和高放废物(high⁃level nuclear waste,高水平放射性废物)的储存罐,如图1⁃3所示。2003年,采用HVOF制备了高耐蚀性能(high⁃performance corrosion⁃resistant)的铁基非晶金属涂层,用于储存美国内华达Yucca山的高放废物,降低储存材料成本近40亿美元,降低核废料储存周期成本近580亿美元[52]。SAM项目的最终目的是研制、评估这种高耐蚀涂层并发展为低成本的核废料储存材料,并与美国国防部高级研究计划局(Defense Advanced Research Projects Agency,DARPA)合作,力争用于海洋环境中各种构件的耐蚀防护。
1.2.2 超音速火焰(HVOF)喷涂原理
热喷涂是一种被广泛应用的制备保护涂层的工业技术,它将喷涂材料加热至熔化或半熔 化状态,之后高速喷射金属熔滴到基体表面形成堆砌结构的涂层。工业应用中开发多种热喷涂方法:火焰喷涂(flame spray),焊丝电弧喷涂(wire arc spray),等离子喷涂(plasma spray),水稳等离子喷涂(water⁃stabilized plasma spray),超音速火焰(HVOF)喷涂,爆炸喷涂(detonation spray)等。

图1⁃3 核废料罐外围高耐蚀铁基非晶纳米晶涂层[52]
热喷涂技术冷却速率(106K/s)可以满足非晶相形成的临界冷速。不同的合金体系,其玻璃形成能力是不同的。材料的玻璃形成能力在一定程度上决定着涂层中非晶相的含量,当合金的临界冷速低于喷涂过程的冷却速率时即可形成非晶结构。20世纪80年代末,人们用磁控溅射(sputtering)[53]及等离子喷涂(plasma spraying)方法[54]制备出了铁基非晶态合金涂层。由于所采用的非晶态合金的玻璃形成能力有限及制备工艺的局限,制备的涂层质量较差。近年来,随着具有高玻璃形成能力的块体非晶合金的出现,利用这些合金成分制备非晶态合金涂层引起了人们的极大兴趣。
目前工业上常用的热喷涂工艺主要为等离子热喷涂和超音速热喷涂制备非晶纳米合金涂层。由于在等离子热喷涂过程中液滴的速度较慢,形成的涂层孔隙率较高(大于5%),不适宜制备耐蚀性涂层。而HVOF喷涂是一种制备致密结构涂层的有效方法,由于在该工艺中颗粒的速度较高,甚至超过700m/s,制备的涂层的孔隙率较低(通常小于1%),适宜于耐蚀性涂层的制备。在热喷涂过程中,晶化和氧化难以避免,当涂层超过一定厚度时,就很难得到完全非晶态的合金涂层。但研究发现,非晶态合金涂层的晶化有利于其硬度的提高,这就使非晶涂层的应用范围更为广阔,尤其适用于腐蚀磨损等条件苛刻的环境。
铁基非晶态合金具有较为低廉的价格和较强的玻璃形成能力,性价比高。最近,Otsubo等[55]报道了利用HVOF喷涂可制得完全非晶态的Fe⁃Cr⁃Mo⁃C⁃B⁃P合金涂层,这表明目前制备的铁基非晶涂层可以通过制备工艺优化来进一步提高其非晶相含量。通过热喷涂制备铁基非晶涂层,并不会使腐蚀性能有太大的降低[56]。一般非晶形成的条件是最大临界冷却速度达到106K/s以上,而HVOF热喷涂可以获得临界冷却速度107K/s左右[57],使得多数合金成分都可在临界速度以上喷涂而形成玻璃态组织,但能用HVOF热喷涂制备非晶涂层的合金成分也是有限的。个别铁基非晶合金体系甚至在102K/s时即可形成玻璃态,这就使得HVOF热喷涂方法制备铁基非晶涂层成为可能。
HVOF喷涂是20世纪80年代兴起的一种热喷涂技术,它的出现给热喷涂技术注入了新的活力。该设备的开发旨在提高熔滴射流速度和降低颗粒的过热程度,相对于其他热喷涂技术,HVOF喷涂制备的涂层具有高硬度、孔隙率低、抗磨损性好、涂层与基体结合强度高等优点,在热喷涂领域已经占有了相当重要的地位。起初主要应用于航空航天领域的飞机发动机零部件上,现已广泛应用于石油、化工、冶金、汽车和造船等领域。
HVOF喷涂方法的主要特点如下:
① 火焰焰流速度高达2200m/s,火焰温度低于3000℃。
② 卷入燃烧焰流的空气少,加之粒子速度快,颗粒在高温中停留的时间极短,喷涂材料的相变、氧化和分解得到抑制。
③ 粉末颗粒飞行速度高达700m/s,颗粒高的飞行速度使得其对基材撞击作用增大,颗粒变形充分,涂层与基体的结合强度远优于普通火焰和等离子喷涂,且涂层呈现出压应力状态,可制备较厚的涂层。
④ 涂层致密性好,可以达到99.5%以上。
基于HVOF喷涂涂层具有极其致密的结构等诸多优点,越来越多的研究人员开始利用HVOF喷涂制备耐蚀合金涂层,其耐蚀性要优于其他热喷涂方法。
HVOF喷涂的原理是利用丙烷、丙烯等烃类燃气或者煤油等可燃液体与高压氧气在特制的燃烧室内燃烧,产生高温高速的燃烧焰流,进而实现粉末粒子的加热和加速,并沉积在工件表面而形成涂层。由于火焰焰流速度极高,喷涂粒子被加热至熔化或半熔化状态的同时,在极短的时间里高速飞行撞击到工件表面,产生明显的喷丸效应并将动能转化为热能,使涂层产生残余压应力,可有效地提高涂层的表观结合强度、抗裂性及耐磨性;同时对工件表面的热影响区小(一般基体表面温度不超过150℃),不影响基体材料的原始热处理组织。
在HVOF技术中,喷枪是产生稳定的高速焰流及获得高质量涂层的关键。Metco公司生产的Diamond Jet系列HVOF喷枪[58]采用了喉管燃烧方式,与线材火焰喷枪的设计较为相似,具有环形分布的火焰射流、中心轴向送粉和压缩空气帽约束等特点。燃气(丙烷、丙烯或氢气)和氧气分别以一定的压力输入,同时从喷枪喷管轴向的圆心处由送粉气(通常为氮气)送入喷涂粉末。气体燃烧产生很高的压力,通过Laval喷嘴形成高速焰流,由焰流流场的膨胀波和压缩波反射与相交形成菱形激波,其数目的多少是火焰速度的一个重要判据。数目越多说明火焰的速度越高。通常情况下会产生4~7个菱形激波。因此,焰流的速度与气体的成分、压力、流量、温度、密度以及喷枪喷嘴的通径等有关。
喷涂过程中,焰流和粉末粒子之间存在着动量和热量的传输,动量传输可用下式表示:
π
=
CDπ
(u-v)2(1⁃1)
式中,u为燃流速度;v为粒子速度;dp为粒子直径;、
分别为粒子和焰流的密度;CD为牵引系数(drag coefficient)。
热量的传输比较复杂,包括传导(conduction)传热、对流(convection)传热和辐射(radiation)传热。对导热性较好的粉末粒子(good heat⁃conducting particles),热量传输可用下式表示:
πh(Tg-Tp)=
π
cp
(1⁃2)
式中,dp表示粒子直径;h表示热传输系数;Tg、Tp分别表示燃流和粒子的温度;cp表示粒子的比热容。
由于涂层是由熔滴溅射一层一层堆积而形成的,喷涂过程中的动量和热量传输对涂层的质量和性能起着重要的作用,如氧化、孔隙率、结合强度和热应力等。
1.2.3 高速三电极等离子喷涂
(1)等离子喷涂
等离子喷涂是最常用的一种热喷涂技术。它是将粉末材料送入等离子射流(直流压缩电弧)中,使粉末颗粒在其中加速、熔化或部分熔化后,通过高速气流的冲击作用,在基底上铺展并凝固形成涂层。它具有生产效率高、制备的涂层质量优良、喷涂材料范围广、成本低等优点。因此,近几十年来,其技术进步和生产应用发展很快,已成为热喷涂技术的最重要组成部分。
等离子喷涂的工作气体常用N2或Ar,再加入5%~10%的H2。这些工作气体进入电极腔的弧状区后,被压缩电弧加热离解形成等离子体,其中心温度可达15000℃以上,同时经孔道高压压缩后呈高速等离子射流喷出。载有喷涂粉末的气体进入等离子焰流,使粉末很快呈熔化或半熔化状态,高速喷打在零件表面并发生塑性变形,黏附在零件表面。各粉末之间也依靠塑性变形而相互钩接,从而获得结合良好的层状致密涂层。但是等离子喷涂由于温度过高会使涂层氧化严重,且涂层结合强度在一定的工况下还不够理想。
随着计算机、机器人、传感器、激光等先进技术的发展,等离子喷涂设备的功能也得到了不断的强化。目前,国内外先进的等离子喷涂设备正向轴向送粉技术、多功能集成技术、实时控制技术、喷涂功率两极分化(小功率或大功率)的方向发展。
Axial Ⅲ等离子喷涂是由加拿大西北Mettech公司自主研发设计的一种高速三电极等离子喷涂系统。它采用了独特的三电极轴向送粉设计,具有喷束集中、粒子速度高、落斑小等特点,可实现极高的喂给速度和沉积效率,并可保证均匀一致的高质量涂层。由于采用闭环自动控制和轴向送粉,提高了高质量涂层的可重复生产性。
Axial Ⅲ喷枪还采用了独特的双惰性气体保护罩设计,降低了喷涂材料的氧化程度,可喷涂活性金属材料等。Axial Ⅲ等离子喷涂系统已经成为服务于航空、航天、印刷、汽车和替换硬铬等工业应用的高效、可靠的涂层生产工具。
Axial Ⅲ喷涂系统的主要优势是:高沉积效率;高喂给速度;均匀的高质量涂层。
(2)等离子喷涂原理
Axial Ⅲ等离子喷枪由三个阳极、三个阴极组成。采用多电极结构不仅提高了电弧的有效功率,而且还可以使电弧电流在多个电极间平均分配,从而单个电极上的热负荷相对大大降低,避免了大功率条件下电极的烧损。喷枪所产生的三条等离子射流将通过集束器被汇流形成一条束流,粉末通过送粉管直接从轴向位置被送入汇流点中,通过喷嘴加热加速并到达基材。粉末速度明显高于常规的等离子喷涂设备,并可达到超音速火焰喷涂的粒子速度。
传统等离子喷涂的致命弱点是采用了径向送粉的方式。由于喷涂用粉末一般都有一定的粒度分布,这样在喷涂时,大尺寸的粒子将会有一种穿过等离子焰的趋势,而小一些或轻一些的粒子则不能全部进入等离子焰流或者直接被蒸发掉。因此,径向送粉的结果是沉积效率低,带来巨大的损失。Mettech公司开发的轴向送粉系统解决了这一难题。通过这种轴向送粉系统,粉末将全部进入等离子焰流中,而且大部分粉末(最高可达95%)都能充分熔化并沉积到基材上。这不仅能制备出更均匀、更致密、更纯净的涂层,而且工艺的经济性也得到显著的提高。
正因为Axial Ⅲ设备采用了轴向送粉方式,其喷束及喷涂落斑相对于径向外送粉而言更小,也更集中,因此具有高的沉积效率。并且在飞行过程中,小粒子的飞行速度要高于大粒子的,这又使得高速飞行的小粒子在等离子射流中的停留时间更短,进而减少了小粒子过热情况的发生。
与其他等离子喷涂相比,其粒子速度相对于常规外送而言更高(最高可达400m/s)。通过喷嘴尺寸和气体流量的调节,粒子速度可以达到和超音速火焰喷涂相当的水平,随着喷嘴直径的变小,粉末颗粒会以更快的速度到达基体并发生严重的变形。另外,三电极等离子喷涂的惰性气体保护罩将产生两层环绕着主等离子焰的惰性气体罩。内层气体罩通常使用氩气,从保护罩与喷枪喷嘴之间的通路送出。外层气体罩将产生一个同心的高速气流,通常使用氮气,以进一步降低外界氧气的侵入。通过这一气体保护罩附加装置可以喷涂低氧化物金属涂层,特别适用于喷涂活性金属或非晶纳米合金涂层。
因此,利用三电极等离子喷涂制备的涂层,结合强度高,孔隙率低,氧含量低。它的诸多优势,使得三电极等离子喷涂在工业界得到广泛认可。
(3)等离子喷涂参数
等离子喷涂可以看作是由等离子电弧、等离子射流、喷涂粒子和涂层四个环节构成的串联系统,中间的每一个环节都对其后的环节有显著的影响,并且最终影响着涂层的组织结构和性能。对于一定的粉末材料和基体材料,改变可控输入参数是影响和控制涂层组织结构与性能的主要途径,而诸多可控输入因素中,电弧功率、工作气体成分与流量以及喷涂距离是最便于调节和控制的工艺参数,并且对涂层的组织结构和性能有显著影响,因此成为等离子喷涂最重要的工艺参数。
由于喷涂粒子在基体上碰撞、铺展、凝固以及传热的能量都来自碰撞基体前粒子所具有的动能和热能,因此粒子的温度和速度是影响粒子沉积行为的最重要参量,也是影响涂层组织结构与性能的决定性因素。研究表明,提高粒子温度可以改善粒子的熔化效果,降低熔滴的黏性,从而增加熔滴粒子铺展时的流动性能,增加扁平粒子和基体的有效接触面积,进而提高涂层的结合性能等。
1.2.4 活性燃烧高速燃气(AC⁃HVAF)喷涂原理
活性燃烧高速燃气(activated combustion⁃high velocity air fuel,AC⁃HVAF)喷涂工艺是近几年发展起来的热喷涂新技术,该工艺采用空气替代传统的氧气,通过压缩空气与燃料燃烧产生高速气流加热和熔化粉末,粉末颗粒以超过700m/s的速度撞击基体,高于传统的HVOF喷涂,见图1⁃4,形成极低氧化物含量和极高致密度的涂层。

图1⁃4 HVOF和HVAF喷涂颗粒温度和喷涂速率对比
AC⁃HVAF喷涂工艺过程对喷涂材料热退化影响非常低,制备的涂层表现出比HVOF更为优异的耐腐蚀及耐磨损特性。可见,AC⁃HVAF喷涂具有制备高质量耐蚀耐磨非晶涂层的潜质,但这需要对合金成分、AC⁃HVAF喷涂过程、工艺参数与涂层结构性能之间的关系有深入的了解。在AC⁃HVAF喷涂过程中,控制参数复杂,影响因素多,如何制备出孔隙率低、非晶相含量高、大面积、具有优异性能的低成本高质量铁基非晶涂层依然是一大难题。另外AC⁃HVAF喷涂过程生产效率高,极大地降低了涂层的加工成本,更有利于超音速喷涂技术的推广应用。
在热喷涂技术中,喷枪是产生稳定的高速焰流及获得高质量涂层的关键。AcuKote⁃HVAF喷枪能够通过压缩空气和燃气燃烧产生的高速喷束,加热并加速金属或者金属陶瓷粉末从而获得涂层。AcuKote⁃HVAF喷枪产生大的焰流,直径约为3/4in(1in=0.0254m),“马赫节”长达10~12in,这远远大于其他工艺(5~7in)的距离。由于喷涂粉末在到达基体的过程中被很好包覆在燃烧室的焰流内部,有效防止了在飞行过程中的氧化,减少或消除了氧化和热损伤。传统HVOF喷涂WC陶瓷时,过高的火焰温度易造成WC粒子分解,操作工艺不易控制,涂层质量难以保证。AC⁃HVAF喷涂则可以避免此类现象,难熔喷涂材料(如碳化物)喷涂时不发生分解。由于固态粒子被加速至极大速度,喷束中的固态粒子会将被沉积粒子中质量差的部分以类似喷砂的方式去除,消除产生缺陷的隐患。另外,固态粒子撞击将产生压应力,在喷涂过程中将减少由于冷却收缩所造成的残余拉应力。在更广的喷涂参数范围内形成同等质量的涂层。