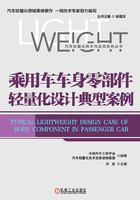
1.1 超高强钢辊压成形工艺应用简介
1.1.1 辊压成形工艺简介
辊压成形,又称为辊弯成形或冷弯成形,英文名称为Rollforming或者Roll-forming,是指以金属卷料或板料为原料,通过多架装配了特定形状成形辊的成形机组,对材料逐步进行弯曲变形,从而得到特定截面产品的加工方法,如图1-1所示。辊压成形技术在建筑、汽车、电气设备、家具等行业得到了广泛的应用。

图1-1 辊压成形工艺示意图
辊压成形工艺可以分为四种,即单张(或单件)成形工艺、成卷成形工艺、连续成形工艺和联合加工工艺。考虑到机组效率问题,现在大多数企业采用的是成卷连续成形。即以卷材为原料,前一卷带材的尾部与后一卷带材的头部对焊,使坯料带材连续不断地进入成形机组进行成形。
整个工艺流程大致为:开卷——矫平——预冲孔——进料——成形——(焊接)整形——切断——出件。
辊压成形工艺的优点如下:
1)辊压成形适用的材料广泛,适合各种力学性能及不同组织结构的钢,特别是高强钢、超高强钢。
2)辊压成形采用多道次渐进弯曲成形,与冲压成形相比,可以获得更小的弯曲半径,且能成形制造各种开放或封闭复杂截面形式的零件,成形后零件刚度较好。
3)辊压成形通过多个道次的变形来进行回弹补偿,回弹调整空间大,成形精度高,且零件表面质量好。
4)辊压成形可集成其他加工工艺,如冲孔、焊接、压花、弯圆等,生产中成形速度可超过10m/min,生产过程自动化程度和生产效率高。
5)辊压成形零件板坯为一定宽度的板带,辊压成形过程中除冲孔外,几乎无其他工艺废料,材料利用率高,材料成本优势明显。
6)辊压成形模具加工简单,使用寿命长,模具制造成本低。
1.1.2 高强钢辊压成形在车身中的典型应用
图1-2给出了典型乘用车高强钢辊压成形零件强度分布及其发展趋势,主要有前后碰撞横梁、车门防撞杆、门槛加强件以及座椅滑轨,其中:
1)前碰撞横梁辊压成形零件的抗拉强度多为800~1000MPa,预测后续将进一步提升到1200~1400MPa。
2)后碰撞横梁辊压成形零件的抗拉强度主要集中在600MPa左右,预测后续将提升到1000MPa及以上。
3)车门防撞杆辊压成形零件的抗拉强度多为800MPa左右,预测后续将提升至1200MPa及以上。
4)门槛加强件辊压成形零件的抗拉强度集中在1000~1200MPa,预测后续将持续提升至1500MPa。

图1-2 典型乘用车高强钢辊压成形零件强度分布及其发展趋势
5)座椅滑轨的辊压成形零件抗拉强度在800MPa左右,预测后续将提升至1200MPa。
1.1.3 高强钢辊压成形的关键技术
1.辊花工艺设计与优化
基于辊压成形的车身各类零件,应设计零件截面并优化辊花,零件截面可以分为对称截面、非对称截面,以及开口型和闭合型等。图1-3为对称截面的辊花图。

图1-3 对称截面的辊花图
2.高强钢辊压模具设计技术
辊压模具的设计主要依据辊花设计图,如图1-4所示。

图1-4 典型辊压模具设计
3.高强钢辊压成形预冲孔、后冲切技术
预冲孔是在板料进行辊压工序之前,利用冲压模具预先在板料上制孔。后冲切是在成形末端,利用冲切模具在生产线上对产品进行在线冲孔。
4.高强钢辊压成形工艺仿真技术
图1-5所示为对辊压成形工艺进行仿真分析的示意图。

图1-5 典型辊压成形仿真分析
5.高强钢辊压成形缺陷控制技术
高强钢辊压成形的常见缺陷包括纵向弯曲、侧弯、扭曲、边浪、边部开裂等。对于纵向弯曲,可在出口利用矫直机矫正,或者采用轧辊压下装置,使轧辊间隙比板厚小,这是使腹板部分产生轻度压延的方法。对于侧弯和扭曲,一方面可以调整轧辊间隙,另一方面也可以用扭转成形机架和轧辊垫片进行调整和矫正。对于边浪,可对成形中的板施加产品纵向的张力,抑制板带的纵向压缩或者可通过整形辊消除。对于边部开裂,可增加道次,减少每一道次的变形量,降低边部的应力应变或者提高板料的边界质量。