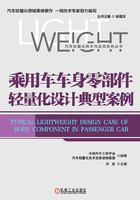
2.6 总结
一般的高强钢钢板的抗拉强度为400~450MPa,而热冲压成形钢材加热前抗拉强度就已达到500~800MPa,加热冲压后则可提高至1300~1600MPa,为普通钢材的3~4倍,其硬度仅次于陶瓷,但又具有钢材的韧性。因此,由热冲压成形钢板制成的车身极大地提高了车身的抗碰撞能力和整体安全性,在碰撞中会对车内人员起到很好的保护作用。
由于热冲压零件极高的材料强度,因此在设计时可用一个热冲压零件代替多个普通钢板零件。在保证强度的情况下,减少零件数量,可降低成本并实现减重。
热冲压钢板具有很好的材料成形准确度,消除材料回弹的影响,可以实现复杂的形状。由于热冲压钢板的特殊性质,并且是加热后成形,因此可以在一道工序完成普通冷冲压成形需多道工序才能完成的复杂形状。一次成形的工艺好处在于可以确保钢板在加工过程中,钢板内部纤维流向不必受到二次受力的冲击,保证钢板保持最好的强度和韧度,而且在零件成形后进行快速冷却,零件成形后的回弹量很小,极大地提高了材料成形准确度,保证了零件尺寸精度,为下一步的车身焊接打下良好的基础。
关键技术点主要有以下几个方面:
1)热冲压的仿真分析过程中应考虑材料成形温度、降温速率及相变行为的本构关系描述。材料的本构关系是表征材料力学性质的数学关系式,准确的流变行为描述是影响计算机仿真精度的首要条件,对于丰富板料成形理论有重要的意义。在材料本构关系研究中,热冲压过程耦合了传热和力学性能。在一定板料升温速度和降温速度下进行高温拉伸试验,根据应力-应变曲线可进行本构描述,但考虑到成形过程中,不同板料降温速度会使构成各相的体积比不同,应力—应变曲线也不同,因此可通过改变试验条件,获得考虑降温速率及相变行为等的材料本构关系。
2)热冲压的仿真分析过程中应考虑成形温度、降温速率和相变行为的热冲压成形极限。在以弯曲为主的成形情况下,热冲压不会发生冷加工成形时的问题,即弹性变形。但在对复杂部件进行成形时,需要进行凸肚、深冲和凸缘等成形加工,必须弄清它们在高温下的成形极限。变形阻抗不仅与温度有关,而且冲头接触部分温度的下降和氧化铁皮的润滑效果会产生复合影响。因此通过改进常温成形极限试验装置,考虑成形温度、降温速度及材料相变行为等,建立热冲压成形极限很有必要。
3)加强对热冲压零件的质量控制。热冲压零件最终质量既受宏观工艺条件影响,又由材料微观组织变化决定。一方面冲压过程中零件的温度不均匀性直接导致最终零件性能的不均匀性;另一方面控制冲压作业线的节拍与零件的最终性能呈对立关系。如果在冲压零件没有充分冷却时就从金属模取出,制品的硬度和形状精度会下降。因此,针对不同零件,在进行模具结构及其冷却系统设计,改进冷却水道的布置,提高模具冷却速度的同时,保障零件均匀降温,是热冲压零件质量控制的重要手段。
4)热冲压模具技术一直是热冲压成形技术的核心,是模具设计、计算机仿真分析、优化设计及先进加工技术的集成。具体来说,工艺面设计根据热冲压成形的特点进行成形分析,根据分析结果,找出解决成形困难的措施,如优化零件形状、修改模面、增设拉延筋等方法。冷却水道优化设计是热冲压模具的关键,水道直径大小、到模面距离都是关键的参数,冷却水道的布置在考虑可加工性的条件下,必须是尽量贴近模面,这样才能保证冷却效果。除此之外,冷却水管的接口应具备可快速拆卸,便于运输和安装,冷却水管的布置与模体的布局相匹配,可结合流体仿真技术验证冷却水道设计的合理性。目前采用的压边装置为氮气弹簧,可以根据水道的布置和模体设计灵活地布置氮气弹簧的位置。最后需要对设计的模具进行强度校核,确保模具使用的寿命。
新型热冲压成形技术,如不等强度、不等厚度热冲压、补丁板、激光拼焊门环已经在部分量产车型应用。比如,分段强化技术使B柱下部分的抗拉强度降低,从而更有效地提高侧面碰撞安全性;不等厚板热冲压B柱,抗碰撞性能得到更细致的控制;基于激光拼焊板整体式热冲压门环,更有效地提高车身刚度及安全性;预先点焊补丁板后一起热冲压,加强局部结构的同时可降低开发成本。