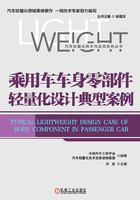
上QQ阅读APP看书,第一时间看更新
1.3 总结
专家点拨
门槛加强件采用辊压成形制造,在进行工艺设计时需考虑如下要点:
1)设计原则:材料按照预想的方式平滑顺畅流动,足够的成形道次数,考虑了产品所有尺寸要求,可避免水平间隔和导入轮缘太小。
2)针对材料HC950/1180MS的超高强度和低伸长率,需要采取措施防止材料的弯角处开裂,采用的圆角设计变化规律是由大到小,避免应力集中。
3)变形抗力大,轧辊圆角处载荷大,采用的圆角设计变化规律是由大到小,减少了变形圆角区域的平均载荷,有利于提高轧辊模具的寿命。
4)相对于其他成形方法,圆角设计做出释放角,减少了成形载荷,排除了过约束和由于轧辊制造、安装、板厚度波动造成的局部挤死的可能性,采用了成形功率最小的方法。
5)成形基准:机组要保证轧辊正确的空间位置,轧辊制造准确,并且轧机轴不弯曲,不松动,轴肩定位精确。
6)材料要与成形过程匹配,使用恰当的成形方式。
7)经过良好培训的操作者要能正确地安装调试轧辊,并确保生产线的良好运行。
8)调试基准按照设计基准和轧辊的安装基准一致的原则确定。其中,最重要的第一基准均以轧机的驱动侧为同一基准确定轴向基准(X向);第二基准为材料高度方向的成形基准,由轧机的下轴线高度确定(Y向);第三基准为材料的成形方向(Z向)。
随着汽车工业的发展,节能、环保、安全、舒适和智能化是当今汽车技术发展的总体趋势。高燃油经济性、低碳排放和更高的安全性对车身轻量化提出了新的要求和挑战,推进了先进高强钢在车身设计制造上的应用稳步增长。汽车用先进高强钢以其轻质、高强度的特点在汽车工业中的应用越来越广泛,并已成为满足车身轻量化和高安全性能的重要途径,具有不可替代的优势,用辊压成形工艺加工超高强钢也得到越来越广泛的应用。