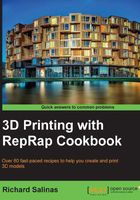
Introduction
In this chapter, we'll look at how we can increase a model's resolution using a laser 3D scanning process.
We'll do this with a 3D scanning system called DAVID Laserscanner. DAVID is a program that utilizes an ordinary line laser and a web camera to scan an object and then takes this information and interpolates a 3D surface. It's a different process compared to what we used with 123D Catch. Instead of photographing an object from all sides, we'll rotate the object by 360 degrees and capture all the sides with a webcam video, as we move a laser line across its surface. Behind the object, a calibration screen that contains a grid of points is placed. The size of the calibration panel will depend on the size of object to be scanned—the larger the object, the larger the calibration panel. We'll find that this limitation can be overlooked when comparing the DAVID scanning results of smaller objects with 123D Catch. 123D Catch works well when scanning large to monumental sized objects, but it doesn't work well for scanning very small objects (as we found when scanning the coin in Chapter 1, Getting Started with 3D Printing). This is the advantage of using laser scanning. We'll explore this system by setting up an inexpensive scanning system and using the free version of DAVID Laserscanner.
We'll also learn how to make a printable model using our scans. We'll do this using an open source program called MeshLab. This program will be an invaluable tool for cleaning up and stitching our scans together.
We'll end the chapter by printing in low and high resolutions and compare the results and the differences in quality of the slicing made by Skeinforge and Slic3r.