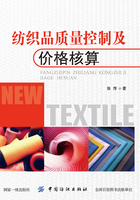
第三节 质量控制的统计方法
质量控制的统计方法,主要是应用数理统计的基本原理来揭示质量运动的规律,为企业的质量管理工作提供可靠的信息。企业质量管理人员根据这些信息采取必要的措施,以达到对产品质量进行控制的目的。
一、产品质量的波动性与质量控制中常用的特征参数
(一)产品质量的波动性
在生产过程中影响产品质量的因素是很多的,有工程方面的原因,也有工作方面的原因;有人的因素,也有物的因素。对这些因素不可以又完全控制在一个水平上,因此生产出来的产品质量不会完全一样,而是形成一定的分布。这就是说,产品质量具有波动性。
1.偶然性因素
偶然性因素又称为随机因素,它是自然发生、自然消失的,但它是对产品质量波动经常起作用的因素。这种因素一般数目较多,但对产品质量的波动影响不大,而且在技术上不易消除,通常也不值得消除。如工人操作上的微小变化、机器的轻微震动等。
由偶然因素引起的产品质量的波动称为正常波动,或称随机误差。
2.系统性因素
系统性因素是对产品质量波动不经常起作用的因素,这种因素一旦发生后就不会自行消失,并且对产品质量的波动影响较大,但这种因素在技术上是可以消除和避免的。如工人违反操作规程、机器过度磨损等。
由系统性因素引起的产品质量的波动称为非正常波动,或称条件误差。
以上两类因素的划分是相对的,随着科学技术的进步,偶然性因素也可能转变为系统性因素。
(二)质量控制中常用的特征数
由于产品质量具有波动性,所以通过随机取样获得的质量数据不会完全一样。为了对产品质量进行分析和判断,就需要用一定的特征数来表示产品质量。
1.集中性特征数
集中性特征数表示产品质量集中的位置或质量水平,如算术平均数、中位数和众数等。在质量控制中常用的集中性特征数是算术平均数。其计算公式如下。
(1)不分组时:

式中:——算术平均数;
X——随机变量;
f——频数;
n,∑f——总频数。
(2)分组时:

式中:X0——基数(一般取频数最大的一组变量值);
c——组距;
u——随机变量距基数的组距数。
由上式可得:

u的平均值为:

2.离散性特征数
离散性特征数表示产品质量离散程度的大小,在质量控制中常用的离散性特征数有极差与均方差。
(1)极差(R):极差表示产品质量的波动范围,其计算公式如下:
R=Xmax-Xmin
式中:Xmax——随机变量的极大值;
Xmin——随机变量的极小值。
(2)均方差(σ):均方差表示一批数据的离散程度,其计算公式如下:不分组时:

或

分组时:

在质量管理中,为了全面反映产品质量的分布情况,必须同时使用算术平均数,而不能只说明离散情况,极差只能说明产品质量的波动范围,而且不能说明其他各个数据的离散情况。
二、质量控制的基本方法
(一)直方图
直方图又称频数分布图,它是进行质量控制的既简便又有效的方法。
1.直方图的用途
(1)直观地分析质量数据集中和离散的情况。
(2)直观地看出各组数据所占的比重。
(3)直观地判断工程质量是否满足质量标准的要求。
例:经测试获得浆轴回潮率的数据见表1-3。
表 1-3浆轴回潮率(%)

根据以上数据绘制出直方图,如图1-5所示。
从浆轴回潮率直方图可以直观地看出:质量集中情况较好,在靠近平均数6.25~6.5范围内的频数比重占82%,但集中的位置偏离标准中心(下偏),并且距标准下限太近,而距标准上限太远。因此,需要采取措施提高平均数,使其处于标准中心的位置。另外,全部数据都在标准上下限范围以内,说明工程质量能够满足质量标准的要求,在正常的情况下不采取措施也不会产生疵品。
2.直方图的使用与分析
直方图做好后,要检定其分布情况及与标准的差异情况。
(1)看分布形态。直方图一般可分为正常型直方图和异常型直方图两种。正常型直方图的特点是图形呈左右对称的山峰形状,如图1-6所示。异常型直方图情况较多,是注意的重点。异常型直方图的特点是图形左右不对称的山峰形状。

图 1-5浆轴回潮率直方图
(2)将实际分布情况与标准进行比较,判断工程质量是否正常。正常情况是分布图形左右对称,并且图形与标准上下限之间有一定余量,如图1-7所示。

图 1-6正常型直方图
B—产品范围(实际质量差异范围)
T—标准界限(设计标准范围)

图 1-7正常情况下的直方图
非正常情况有以下几种。
①图形分布与标准上下限之间余量太大或太小,如图1-8所示。
②图形分布与标准上下限之间没有余量,或超出标准上下限,如图1-9所示。
③图形分布偏离标准中心,如图1-10所示。

图 1-8非正常情况下的直方图(一)

图 1-9非正常情况下的直方图(二)

图 1-10非正常情况下的直方图(三)
(二)控制图
控制图是企业进行质量控制的重要手段,企业质量管理人员根据控制图所提供的信息来判断工程质量的状态,并及时采取相应的措施,达到事先控制的目的。
1.控制图的基本原理
控制图的基本原理是正态分布理论。正态分布曲线(图1-11)具有以下特点。

图 1-11正态分布曲线
(1)以平均值μ为轴左右对称,当X=μ时为曲线的最高点。
(2)正态分布曲线的位置由平均值μ来决定,其形状由均方差σ来决定。
(3)正态分布曲线与横坐标所围成的面积为100%。曲线与μ±σ所围成的面积为68.25%;曲线与μ±2σ所围成的面积为95.45%;曲线与μ±3σ所围成的面积为99.73%;曲线与μ±4σ所围成的面积为99.99%。
这就是说,越靠近平均值,数据出现的概率越大,越远离平均值,数据出现的概率越小。在距μ±3σ以外,数据出现的概率只有0.27%。根据正态分布的这个特点,在总体中抽取有限个试验数据时,有数据落在μ±3σ以外的可能性极小,就可以认为此事件是不可能发生的。这样进行判断的准确性是99.73%,判断的错误性只有0.27%(近似0.3%),这种判断方法叫作千分之三法则。
2.控制图的种类和基本格式
(1)控制图的种类。控制图的种类有多种,但基本上可分为计量控制图和计数控制图两大类,每一类又可分为许多种。
①计量控制图。如单值(单个值)控制图(X图),平均值与极差控制图(—R图),中位数与极差控制图(~X—R图)等。
②计数控制图。如不合格品数控制图(P—n图),不合格品率控制图(P图),缺陷数控制图(C图),单位长度(或面积)缺陷数控制图(U图)等。
以上各种控制图都具有其自己的用途。控制的指标不同,采用的控制图也不同,应视需要而定。
(2)控制图的基本格式。控制图的基本格式如图1-12所示,横坐标表示试验顺序(号码)或取样时间,纵坐标表示产品质量特性。在图中画有一条中心线,再分别画出上下质量控制界限和上下质量标准界限。

图 1-12控制图的基本格式
3.控制图的作图步骤
(1)收集数据。收集数据要在生产正常的情况下进行,在收集数据时要详细记录数据的历史,以便于后续对数据进行分析。
(2)整理数据。一般按加工时间或取样时间先后顺序将数据进行排列。
(3)计算特征数。根据控制图的需要计算有关特征数。
(4)确定中心线和上下质量控制界限。
(5)画图。
(6)验证。将试验数据标在图上,如果全部数据都在上下质量控制界限范围内,这个控制图就可以应用。如果有数据点超出上下质量控制界限,就把该数据去掉,重新取样,去掉几个数据补充几个数据。再重复步骤(3)~(6),直至全部数据都在质量控制界限范围内为止。
4.几种常用的控制图
(1)单值控制图(X图)。单值控制图所取的数据是所有被测量的样品的单个值。采用单值控制图时,不用对数据进行分组,不必计算组中值,所以比较简便,可以及时发现产生质量缺陷的原因。其缺点是由于某种偶然因素出现了异常的单值,可能使数据点超出质量控制界限,如果根据这种偶然情况就断定生产过程已经失调,发出警报,采取某项措施,反而会出现相反的情况。为了避免这种偶然情况的出现,可将X图同X—R图一起使用。单值控制图的作图步骤如下。
①收集数据。例如,清花间每只棉卷重量(kg)数据,见表1-4。
表 1-4棉卷重量数据
单位:kg

②计算中心线。

③计算均方差。

④计算质量控制界限。根据纺织生产的实际情况,取作为控制界限。
质量控制上限==15.0+2×0.114=15.23
质量控制下限==15﹣2×0.114=14.77
⑤画图。
⑥验证。因全部数据都在上下质量控制界限范围内,所以该控制图(图1-13)可以在生产中使用。

图 1-13单值控制图
(2)平均值与极差控制图(—R图)。
—R图是一种经常使用且理论根据十分充分的控制图。适用于产品批量较大、较稳定的生产过程。
—R图的特点是把
图和R图画在同一张图上,一方面可以控制平均数
值;另一方面可以控制极差R值。根据
—R图所提供的信息进行工艺技术的分析和工程能力的研究。
—R图的做法如下。
①收集数据。例如,五台并条机生产同一品种条子数据(g/5m),见表1-5。
表 1-5条子重量数据
单位:g/5m

②计算各组平均值及
的平均值

③计算各组极差R及R的平均值

④确定中心线。图中心线
=20.01,R图中心线
=0.21。
⑤计算质量控制界限。—R图质量控制界限的计算方法,可以采用3σ的计算方法,也可以用系数法计算,用系数法计算比较简便,不必计算均方差,在n(组内数据)确定的情况下,可查
—R图系数表(表1-6)得各系数值。
表 1-6—R图系数表

已知:n=5,查表得A2=0.58,D3=0,D4=2.11。




⑥画图(图1-14)。
(3)不合格品数控制图(P—n图)。P—n图属于计算型控制图,当子样容量固定不变时,可使用该图。
不合格品数为:
Pn=n·P
平均不合格品数为:

式中:n——子样容量;
P——不合格品率。


(4)不合格品率控制图(P图)。当子样容量不固定时可使用P图。P图的中心线为平均不合格品率,则:


图 1-14条子重量—R控制图
由于子样容量是不固定的,所以P图的质量控制界限随着n的大小而变化。一般地说,如果子样平均值与实际子样相差在±范围内,就可以用子样平均值表示实际子样。这样,控制界限也就是一个固定值。
(5)缺陷数控制图(C图)。C图也是属于计数型控制图,如棉结杂质、织疵等可使用C图。

以上介绍的是几种主要控制图的做法。控制图的主要用途是判断工程质量是否稳定,而不是判断产品质量是否合格。判断产品质量是否合格用质量标准或规格,这两者是不同的。另外,控制图只能反映异常情况,不能反映造成异常情况的原因。
5.控制图的分析
一般说来,控制图上的点子能反映出工程质量的稳定程度,但是,有的控制图的点子分布反映得比较明显,而有些则不明显。为了判断工程质量是否处于稳定状态,需要制订一定的判断规则。一般控制图的判断规则如下。
(1)点子不越出质量控制界限。
(2)点子排列正常。如30个数据有下列缺陷,也判断有异常变化。
①点子在中心线一侧连续出现七次以上。
②连续七个点子上升或下降。
③点子在中心线一侧多次出现。
④点子发生周期性变动。
6.控制图的注意事项
(1)在收集数据时要在生产正常的情况下进行,并注意详细记录数据的历史。做好控制图以后要进行验证。
(2)当原料、设备等生产条件有变化时要重新绘制控制图。
(3)验证所控制的质量指标是否遵循正态分布。可采用正态概率纸法、偏度峰度法等进行验证。
(4)在确定质量控制界限时要考虑由于统计判断的两类错误所造成的损失,并把它们减少到最低限度。
(5)控制图一般适用于生产过程相对稳定的大量生产或成批生产,对于多品种的小批量生产适用性较差。
(三)相关与回归分析
在生产过程中,许多现象是互相联系、互相制约的,如果现象A是现象B的原因,则现象B就是现象A的结果。A和B的这种关系叫因果关系。如果不考虑原因和结果的区别,只从现象A与现象B之间有关系而言,这种关系就叫相关关系。
在质量管理中研究两个质量特性之间的关系时,当测定值xi增大时,yi值的平均值也增大,xi减小时,yi值的平均值也减小,那么,x和y之间存在相关关系。如果x和y之间存在函数关系,而这种函数关系又是不确定的,那么,x和y之间存在回归关系,这个函数叫回归函数或回归。
1.相关分析
相关分析是对变量之间的相关关系进行分析,其目的是找出变量之间的相关程度和相关类型。相关分析的主要方法如下。
(1)相关图法。通过相关图(图1-15)可以直观地判断变量之间是否存在相关关系以及相关程度是否密切。同时,还可看出变量之间的相关关系属何种类型的相关。
当一个变量随着另一个变量增加而减少时,为负相关[图1-15(c)];反之,为正相关[图1-15(b)]。当一个变量随着另一个变量的增加而增加,在到一定程度时又随着另一变量的增加而减小时,称为正负相关[图1-15(d)]。
(2)相关系数法。为了定量地分析变量之间的相关程度,通常采用相关系数法。其计算公式如下:

图 1-15相关图

式中:r——相关系数。
可以证明,相关系数r的范围是﹣1≤r≤1。
当>0.5时,则变量之间的相关程度比较密切,
越接近1,则相关程度越密切;当r值为正数时,则变量之间的相关关系为正相关,当r值为负数时为负相关。当r值为零时则变量之间是不相关或正负相关。
2.回归分析
回归分析是对变量之间不确定的函数关系进行分析,以便用一个变量来说明另一个变量。如果两个变量之间存在线性函数关系,可用下列直线方程式来表示:
y=a+bx
该直线方程式为y对x的回归方程式。为了使回归直线能够比较准确地反映实际情况,就需要合理地确定a和b,其计算公式如下:

因为回归直线能够比较准确地反映实际情况,可以应用回归直线方程式对产品质量和工程质量进行预测和控制。
例如,经测试获得梳棉机道夫速度与生条棉结杂质的数据如下。
道夫速度(x)18 21 24 27 30 33
棉结杂质(y)30.4 34.7 35.5 36.5 37.5 39.4
求棉结杂质对道夫速度的回归方程式:
首先计算和
:

然后计算a和b:

把a和b代入回归方程式,得到棉结杂质对道夫速度的回归方程式为:
y=a+bx=22.49+0.51x
根据这个方程式,在给定道夫速度的情况下,可求出相应的棉结杂质粒数,这为预测和控制棉结杂质提供了理论根据。
回归方程式的应用范围一般应在试验数据范围内(本例中适用于道夫速度在18~33r/min)。如需扩大应用范围,要有理论根据。另外,回归方程式的应用只能由给定x值求相应的y值,而不能由y值求x值。