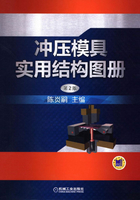
2.3 冲孔模
2.3.1 大型盒盖侧边冲孔模
如图2-35所示为大盒盖侧边冲孔模。
图2-35 大盒盖侧边冲孔模
1—凸模 2—固定卸料板 3—凹模 4—定位板
为便于大型制件的定位与操作,本模具的工作部分设计在压力机工作台之外。冲压时,受力点对压力机滑块中心是偏载荷,但由于冲压力不大,允许采用此种结构。
2.3.2 有橡皮平衡力矩冲孔模
如图2-36所示为有平衡力矩的大型盒盖侧边冲孔模。
图2-36 有橡皮平衡力矩冲孔模
1—定位板 2—凹模 3—弹压卸料板 4—凸模
为便于大型制件的定位与操作,模具工作部分也设计在压力机工作台之外,但有橡皮垫作平衡力矩,故模具工作平稳,避免啃刀口。
2.3.3 圆盖侧边孔双向对冲式冲孔模
如图2-37所示为圆盖件侧边ϕ4mm孔和R7mm、R3mm半圆槽的双向对冲式冲孔模。
图2-37 圆盖侧边孔双向对冲式冲孔模
1—复位弹簧挡板 2—安全保护罩 3—大滑块 4—凸模 5—固定座 6—定位销 7—下模座 8—导向圈 9—凹模 10—小滑块 11—斜楔 12—模柄
在本模具中,利用工件上2×ϕ9mm孔由定位销6定位,斜楔11的两侧面均带斜面,分别对大滑块3和小滑块10作用,一次行程能冲出两个孔。图示为工作位置,固定座5的外形对工件亦起到定位作用,它们间配合松紧合适。斜楔11上升后,大小滑块在各自弹簧的作用下复位。图中箭头所指为冲下废料下落方向。
2.3.4 盒形件侧壁悬臂式双向冲孔模
如图2-38所示为盒形件侧壁悬臂式双向冲孔模。
本模具凹模2为悬臂浮动式结构,它与两个导柱13通过衬套成H7/h6滑动配合,自由状态下,由弹簧16将其顶起,最高位置由定位环14限位。上、下模座各装有冲孔凸模5和压料板6。
工作时,坯件从模具的侧向套到凹模2(兼定位柱)上后,压力机滑块带动上模下行,悬臂凹模上的制件3在上、下凸模的作用下对冲,完成冲孔和切口(图中未表示)工作。上模上行,凹模2上浮恢复原状,制件可从凹模上取走。
本模具操作方便、安全,模具结构简单,生产率高。
图2-38 盒形件侧壁悬臂式双向冲孔模
1—凹模镶块 2—(悬臂式)凹模 3—制件 4—压料板镶块 5—冲孔凸模 6—压料板 7、16—弹簧 8—凸模固定板 9—垫板 10—限位螺钉 11—上模座 12—导套 13—导柱 14—定位环 15—衬套
如采用标准模架,浮动凹模导柱可单独设立。定位环以上导向部分可舍去。另外,冲压过程中要将冲下的废料定期清除,以免堵塞,影响正常生产。
冲槽间隙取≤0.18mm,保证切口不产生较大毛刺。
2.3.5 筒形件悬臂式圆周分度冲孔模
如图2-39所示为凹模装在悬臂式圆周分度冲孔模。
图2-39 悬臂式圆周分度冲孔模
1—下模座 2—弹簧 3—定位销 4—凹模支架 5—凹模 6—支座 7—凸模 8—模柄 9—橡皮 10—定位螺钉 11—制件
根据制件筒壁均匀分布的3×ϕ8mm孔。分别由3次行程冲出,即冲完一个孔后,将毛坯件逆时针方向转动,利用定位销3插入已冲的孔后,依次冲第2、3个孔。这种模具结构简单,但生产效率低,一般适用于小批量生产。
2.3.6 管基套侧壁孔分度冲孔模
如图2-40所示为管基套圆周6×ϕ(8±0.2)mm孔的分度冲孔模。
图2-40 管基套侧壁孔分度冲孔模
模具的冲孔凹模6嵌在悬臂7上。悬臂的一端用来使管基套定位,另一端与支架8固定,为了防止转动,用圆柱销12销住。支架8固定在下模座9上。凸模5靠导板11导向。凸模与模柄3的固定采用螺钉4紧定,使更换凸模非常方便。
定位器上的定位销2固定在手把1上,手把固定在支架8上,它可以绕螺钉10回转,在弹簧13的作用下,定位销压向悬臂7。
冲压开始前,拔开定位器的手把1,将毛坯套在悬臂7上,放松手把,凸模5压下,冲出第一个孔。然后逆时针转动制件,使定位销2落入已冲好的第一个孔内,接着冲第二个孔。用同样的方法冲出其他各孔。
由于该模具在压力机的一次行程内只冲一个孔,对模具来说简化了结构,但定位有积累误差,所以孔的相对位置不很精确,一般可做到±30′。生产率比较低,适用于小批量生产。
2.3.7 拉深件直壁多孔一次冲出模
如图2-41所示为拉深件直壁四周8×ϕ30+0.1mm孔一次冲出模。
图2-41 拉深件直壁多孔一次冲出模
冲制前,将毛坯(由料厚0.5mm的黄铜H68拉深成的筒形件)套在凹模3上,压力机滑块下降,带动上模部分,侧板5绕凹模中心作顺时针转动,由于偏心槽的关系,冲孔凸模1在侧板5的转动下,在支座4里向中心滑动,把套在凹模外边的制件孔冲出。压力机滑块回升时,侧板作逆时针转动,凸模离开凹模,然后扳动手柄7,使冲好孔的制件由顶杆6上的螺钉2顶出,最后用手取下制件。
2.3.8 自动分度径向冲孔模
如图2-42所示为自动分度径向冲孔模。
制件套在主轴8右端用压盘19压紧,并可随主轴回转。每冲完一孔后,装于主轴左端的分度机构,带动主轴和制件旋转一个角度;待全部孔冲完后,松开压盘取出制件。
凸模、凹模均采用快换结构,维修更换很方便。
2.3.9 斜楔式冲孔模——双斜面斜楔冲孔模
如图2-43所示为双斜面斜楔冲孔模。
本模具利用两个带双斜面斜楔带动可滑动凸模座5同时将拉深件直壁两侧孔冲出和复位的冲孔模。
冲压时,制件放在凹模座6上定位。上模下行,压料板1首先将制件2压住,接着由于斜楔4推动可滑动凸模座5;带着凸模3将制件两侧孔冲成,凸模3外套橡皮,冲孔前起压料作用。
图2-42 自动分度径向冲孔模
1—挡销 2—转轴 3—手柄 4—凹模座 5—钢球 6、21、23—弹簧 7、20—螺塞 8—主轴 9—分度盘 10—楔形块 11—凹模 12—棘轮 13、18—连杆 14—棘爪 15—凸模 16—弹簧片 17—壳体 19—压盘 22—垫盘 24—限位销
图2-43 双斜面斜楔冲孔模
上模回程,斜楔外侧斜面与凸模座斜楔孔外斜面发生作用,使凸模座5带着凸模离开凹模恢复原状,可以取走制件。
2.3.10 斜楔式冲孔模——斜楔滑杆冲孔模
如图2-44所示为斜楔滑杆冲孔模。
图2-44 斜楔滑杆冲孔模
1—斜楔 2—滑杆 3、4—冲孔凸模 5—压板 6—凹模 7—橡皮
本模具利用上模斜楔1推动滑杆2与凸模3进行横向冲孔,从图示上下模闭合时,凸模4也完成了冲孔工作。此结构适用于两个孔A很近的情况。
2.3.11 斜楔式冲孔模——阶梯斜楔冲孔模
如图2-45所示为对拉深件壁部上下同时冲孔的斜楔式冲孔模。
本模具斜楔2为整体阶梯式,推动一长一短滑杆1,实现上下两个孔同时冲出。冲孔凸模外套有橡皮6,它起压件和脱件双重作用,凹模4是个环状淬硬体,用工具钢制成,然后与用普通钢制成的凹模体固定在一起。
图2-45 阶梯斜楔冲孔模
1—滑杆 2—斜楔 3—压板 4—凹模 5—凸模 6—橡皮
2.3.12 深筒形件冲孔模
如图2-46所示为深筒形件冲孔模。
图2-46 深筒形件冲孔模
本模具在筒形件底部ϕ17.50+0.05mm的圆周上,一次冲出8个孔(7个是ϕ5.60+0.1mm的圆孔,1个是5.60+0.1mm×5.60+0.1mm的特形孔)。
由于压力机行程不够,故采用了活动凹模。凸、凹模的间隙靠导柱10和导套12导向保证。冲制前,将凹模3通过手柄1拉出,毛坯(由冷挤压而成)放入凹模,再将凹模推进,直到定位销2挡住和活动柱13进入垫板14的凹窝里为止,此时,上模即可往下冲孔,冲完后,制件由打杆8及推板11推出。为了提高强度,凸模6和7做得较短,凸模固定板4较厚。凹模采用镶拼式,便于更换。两个导柱10固定在上模,导套12装在下模,便于刃磨。导柱的顶端做成锥形头,当导柱进入导套时,有自动找正的作用。冲孔凸模固定板4、垫板5及固定座9的外径比制件的内径应小0.5mm左右。制件在模具上的定位,主要靠本身的定位键与凹模孔。
2.3.13 聚酰亚胺覆盖膜ϕ0.4mm多小孔冲模
如图2-47所示为覆盖膜ϕ0.4mm多小孔冲模。
图2-47 覆盖膜ϕ0.4mm多小孔冲模
a)制件
图2-47 覆盖膜ϕ0.4mm多小孔冲模(续)
b)模具 1、5—限位柱 2—导柱 3、4—凸模 6、10—套筒 7—键 8—球面模柄 9—上模座 11—垫板 12—凸模固定板 13—卸料板固定板 14—压(卸)料板 15—凹模 16—导套 17—下模座 18—定位销 19—定位销固定座
毛坯为外形经冲裁的落料片,上面有两个供冲孔模定位用工艺孔ϕ10+0.01mm。
料软、料薄、孔小、孔多是本冲孔模的主要特点。冲压时凸模强度差、易折断,料压不紧,凸、凹模间的间隙大小控制不好,就会产生毛刺和孔的质量差等问题,因此本模具在结构上有如下一些特点:
1)小凸模尽量短,以提高刚性。小凸模与固定板成间隙配合,小凸模对凹模的对正导向靠卸料板固定板13、压(卸)料板14保证,而压料板与凹模间有两个直径较大的导柱2导向,使压(卸)料板与凹模相对位置完全处于受控状态下运动,也保证了小凸模与凹模之间的正确位置。
2)凸模固定板12、压(卸)料板14、凹模15三块板的中间方孔一次线切割加工成。其他孔的加工是以加工完的凹模各孔为基准,再用专用样冲通过经凹模孔投定到压(卸)料板14和凸模固定板12上的孔中心位置后,由模具工加工而成,这样三块板的孔位置中心能保持完全一致。
3)为保持上模座9与卸料板固定板13、上模座9与下模座17之间平行运动,在弹压装置上采用了两种规格套筒,分别为件6、件10,每种4件,高度完全一致。
4)为了控制凸模进入凹模的深度≤1mm,也为了使凹模中废料及时推出,防止废料堵塞,容易折断小凸模,在上、下模座中部两侧设有限位柱1、5。
5)凹模采用厚3mm,工作孔48×ϕ0.4mm小孔为刃口高1mm的直刀口,反面为1∶100锥度,保证废料下落通畅。
6)冲裁间隙双面取<0.01mm。
7)定位销18与定位销固定座19固定在一起成偏心体,旋转偏心体,可微调定位销中心距。
8)工作时,下模固定到压力机工作台上,上模与压力机滑块不固定,冲压时上模的下行,靠压力机滑块撞击球面模柄8实现,故本模具的使用对压力机滑块导向精度无要求。
2.3.14 薄料密集小孔冲模(一)
如图2-48所示为薄料密集小孔冲模。
图2-48 薄料密集小孔冲模(一)
a)制件 b)模具 c)凹模孔的分布
制件材料08F,料厚0.1mm,一次冲出549个ϕ2mm孔。
模具采用四导柱滚动导向模架。凸模固定板、卸料板、凹模三板之间外加四个小导柱,导向精度按H6/h5加工。
卸料螺钉装置采用图示2-48b件7~件12结构。在螺钉10上加一套筒12和垫圈11,套筒共16个一起磨成等高。在18个压杆9的作用下保证卸料板15平衡工作。卸料螺钉与压杆的位置均布在排孔周围和13.5mm的两条空白处(见图2-48c)。
凹模采用整体结构,直刃口长2mm,反面扩大至ϕ3mm。冲压时凸模进入凹模深≥2mm,不让废料留在凹模内,有利于延长模具寿命。
凸模长≤38mm,为使不致太长,将固定板固定部分开成通槽,然后用垫板4垫入,这样固定板总厚度未变,而凸模短了。
为使凸模固定板5、卸料板15、凹模17各孔位置一致,三板装夹一起由线切割按最小间隙即卸料板的尺寸割成,再取下卸料板,对其他形孔用原程序再走丝一遍,使固定板、凹模的间隙略有扩大,满足了使用要求。
2.3.15 薄料密集小孔冲模(二)
如图2-49所示为超短凸模薄料密集小孔冲模。
图2-49 薄料密集小孔冲模(二)
a)制件(柔性覆盖膜,材料聚酰亚胺基材,料厚0.1mm) b)A、D排孔冲制排样 c)模具 1—支座 2—下模座 3—导柱 4—凹模框 5—卸料板 6—凸模固定板 7—推板 8—上模座 9—空心垫板 10—卸料螺钉 11—套管 12—橡皮 13—定位销 14—模柄 15—小导柱 16—导套 17—凸模 18—垫板 19、20—两半卸料板块 21—密封圈 22—抽气孔 23、25—两半凹模块 24—封盖 26—导正钉
制件上有128个长方小孔,分四排,每排32个孔。孔距(1.25±0.05)mm,孔的最小边距0.45mm,孔宽(0.8±0.05)mm,孔长1mm。坯料为柔而薄的片料,刚性差、孔小、孔密,孔形状、尺寸公差要求严是本制件的特点。为此采用将一片料的四排孔分为两组,A、D两排孔为一组在一副两工位的连续模上完成;B、C两排孔为一组在另一副两工位的连续模上完成。
见图2-49b,A、D两排孔在一副两工位连续模上通过冲单、双数孔来完成。两侧的定位孔是在数控钻床上已加工完成,孔直径为3.18mm。第一工位以涂黑孔导正冲制单数孔,第二工位以没涂黑孔导正冲制双数孔。B,C两排孔的冲制排样同图2-49b(略)。
本模具用于冲制A、D两排孔。主要结构与设计要点:
1)凸模长22mm,凹模采用镶拼结构(两半凹模块23、25),用线切割三次走丝加工,锥度30′。凸、凹模材料均为Cr12MoV,表面粗糙度Ra≤0.4μm,刃口经研磨锋利。为便于维修,凹模硬度取38~40HRC。
2)卸料板厚度为5mm,工作部分嵌入板块19和20,其外形尺寸、材料与两半凹模块23、25相同,但硬度为58~62HRC,与凸模单面间隙为5μm。为保证卸料板平稳和刚性运动,在卸料螺钉10上安装了4个等高套管11。此外,卸料板与凸模固定板6之间设有小导柱导向,保证卸料板平稳工作,还保护了小凸模。小导柱15与导套16间为H6/h5配合。
3)为使冲下废料及时排出,除凸模进入凹模较深外,在下模座中设有抽气孔22,以形成负压保证废料顺利排出。
2.3.16 金属网板多小孔自动冲模
如图2-50所示为金属铝网板多小孔自动冲模。
2.3.17 棘爪齿条式半自动多小孔冲模
如图2-51所示为棘爪齿条式半自动多小孔冲模。
当压力机滑块向下时,固定在上模的推块1推动滑块2,装在滑块2上的棘爪4带动齿条导轨6一起左移。齿条导轨的齿距相当于送进步距。齿条另一侧的V形齿是供定位用的,以保证冲出孔距的精度。当冲程回升时,滑块2受弹簧3的作用退回。楔块7用以调整齿条导轨6的间隙。被冲材料用压板8固定在齿条导轨6上,由定位板5定位。
2.3.18 菱形件冲孔模
如图2-52所示是在一个菱形和厚薄不相同的毛坯上冲四个孔的冲孔模。
上模部分有四个凸模,其中两个冲ϕ3.4+00.05 mm孔,料厚为3 -00.1mm,另两个冲ϕ4.2 -00.1mm孔,料厚为2mm。由于毛坯的料比较厚,所以凸模均做成带台的。压杆6是用来压下卸料板3的。当模具开启时,压杆6与卸料板3之间的空程h应小于卸料板台孔深h1,即h<h1。这样可以保证冲压时卸料板压下的力量完全靠压杆6传递,而与凸模无关。
冲孔前,将毛坯放入定位板中。定位板的定位孔按制件外形调配,使之能自由放取,但不能太松,一般按实际间隙0.03~0.05mm动配合加工。制件的内孔与外形的相对位置尺寸,取决于定位板的装配质量。所以,一般待试模合格后再加工定位销孔。定位板的前面有一缺口,便于放料。冲孔后的废料从凹模里落下。
2.3.19 中厚钢板多孔冲模
如图2-53所示为客车底盘一横梁中厚钢板多孔冲孔模。
图2-5O 金属铝网板多小孔自动冲模
1—模柄 2—模板 3—固定板 4—低熔点合金 5—凸模 6—凸模固定板 7—中间导柱 8—压料板 9—凹模 1O—凹模固定板 11—底座 12—导套 13—导柱 14—活动导板 15—导尺 16、2O—调节螺杆 17—承料板 18—卸料板 19—导板 21—斜楔 22—支架 23—滑轮 24—止退夹持器 25—接触板 26—送料夹持器 27—旋钮 28—螺杆 29—滑板 3O—固定架 31—镶块 32—托板 33—滑板座 34—永磁垫块 35—支板 36—调节器
图2-51 棘爪齿条式半自动多小孔冲模
1—推块 2—滑块 3—弹簧 4—棘爪 5—定位板 6—齿条导轨 7—楔块 8—压板
制件材料Q345钢板,厚4mm,上面有最大孔ϕ60mm、最小孔ϕ6.5mm,还有ϕ8.5~ϕ17mm的孔,大小不等总计30个孔,分布在840mm×315mm的平面上。
本模具采用四导柱滑动导向模架,弹压卸料。冲孔凸模为阶梯形带台结构,ϕ6.5mm凸模设有护套保护。孔中心距560mm的两个ϕ60mm孔的大凸模兼作导柱对卸料板导向,其相应配合精度为ϕ60H6/h5,精度比护套与凸模固定板的H7/h6高。
凹模全部采用镶套结构,便于制造和更换。
废料的漏出采取在每个孔位的下模漏料板上开槽,然后嵌入斜滑板10(见图示B—B),斜滑板10与漏料板8成过盈配合,无需螺钉固定,较好地解决了废料的排出问题。
2.3.20 厚料冲小孔模
如图2-54所示为厚料上冲小孔的模具。
材料为厚2mmQ235钢,冲孔直径为2mm。
图2-52 菱形件冲孔模
1—凹模 2—定位板 3—卸料板 4、5—凸模 6—压杆
凸模4为台阶形,台阶部分与固定板2采用过盈配合,工作部分采用了活动护套5和固定块3保护。冲压时,凸模除进入材料内的一段外,其余部分均可得到不间断的导向,从而增加了凸模的刚度,消除了凸模在工作时的弯曲和折断的可能。活动护套5的一端压入卸料板7中,另一端与固定板17成H7/h6动配合。
固定块3呈三角形,以60°斜面嵌入固定板17和活动护套5内,并以三等分分布在凸模4的外围(见图A—A剖视)。其结构尺寸如图2-54b所示。材料用T10A,淬火硬度55~60HRC。内孔ϕ2.05mm与凸模也为H7/h6动配合。装配时,应保证每一块都能与凸模很均匀地接触。
弹压卸料板7由导柱1、导套6、8导向,这样在工作时,卸料板不会歪斜或移动,使凸模的导向更为可靠。卸料板上还装有强力弹簧16,当模具工作时,首先使卸料板压紧坯料,然后冲孔,可使冲孔后的孔壁具有很好的表面粗糙度。
凹模10为圆柱形台阶式,待全部加工完后压入固定板15中,然后与下模座9装配在一起。
图2-53 中厚钢板多孔冲模
a)制件 b)模具 c)凸模、护套配合关系 1—上模座 2—上垫板 3—大凸模 4—卸料板 5—凸模固定座 6—小凸模 7—简易护套 8—漏料板 9—下模座 10—斜滑板 11—凹模固定座 12—凹模
图2-54 厚料冲小孔模
a)模具 b)固定块详图 1—导柱 2—固定板 3—固定块 4—凸模 5—活动护套 6、8—导套 7—弹压卸料板 9—下模座 10—凹模 11—定位板 12—支撑板 13—滚花螺母 14—螺钉 15—固定板 16—弹簧 17—固定板
下模座上固定的支撑板12,用来安装可移动的定位板11,在支持板上开有T形槽,定位板11根据制件的长短调整好后,用方头螺钉14和滚花螺母13紧固。
上、下模座和卸料板均由两个直径相同的导柱导向。为避免将上、下模装反,采取一个导柱压入上模座,另一个压入下模座的方法,这样也有利于模具的刃磨。
2.3.21 小凸模护套结构形式
如图2-55所示为直通式小凸模和带台固定滑块。小凸模固定端采用铆接,带台固定滑块外形为扇形。
凸模直径为1.5~2mm的凸模活动护套结构与参考尺寸见图2-56所示。
各种尺寸的凸模护套及有关导向零件的标准规格,如图2-57所示。
当图2-57的规格不适用,需另行计算决定其长度时,必须注意两点:
1)当冲模处于开启位置时,护套上端应位于扇形块内,其导向深度不小于3~5mm。
图2-55 直通式小凸模与护套
a)开始冲压时 b)冲压结束时 1—卸料板 2—凸模活动护套 3—固定板 4—凸模 5—凸模固定板 6—扇形固定块 7—材料 8—凹模
图2-56 直径为1.5~2mm的凸模护套
图2-57 凸模护套及导向零件的标准规格
a)d=1.5~2mm b)d=2.1~3mm c)d=3.1~4mm d)d=4.1~5mm
2)在工作行程终了时,护套不应碰到凸模的固定板上。
还有一些特殊的护套可供使用:
1)简化结构的凸模护套如图2-58和图2-59所示。图2-58所示的这种凸模护套没有铣槽。凸模上端有部分长度(大于冲件料厚t)未被导向。图2-59是另一种简化结构。凸模用三个在圆周上均布并紧贴凸模表面的圆销保护,防止其受压失稳。
图2-58 简化凸模护套结构
图2-59 圆销式简化凸模护套结构
2)在冲直径ϕ0.3~ϕ0.8mm的小孔时,宜采用如图2-60所示的缩短式全长导向凸模护套结构。
3)当孔距较小时,需采用近距多孔结构,如图2-61所示。图中L为冲孔件孔距;D为保护套外径。
图2-60 缩短式全长导向凸模护套结构
1—固定块 2—套筒 3—凸模护套
图2-61 孔距很近的凸模护套
4)如图2-62所示是弹性凸模护套结构。
弹性部分由钢垫圈1与橡皮垫圈2交替重叠组成。采用这种结构,可以在冷轧钢带、铝、黄铜及纯铜板上冲ϕ1mm小孔,料厚可达2.5mm。设计中取钢垫厚度=(1~1.5)mm×凸模直径;取钢垫圈外径与外套内径的配合为H7/h6;取钢垫圈内径与凸模外径的配合为H9/h8。橡皮垫圈外径小于外套内径,橡皮垫圈内孔大于凸模外径。设计中取橡皮垫圈厚度=(1~1.5)mm×凸模直径;取橡胶垫圈压缩量约为厚度的1/3;取橡皮垫圈总压缩量=冲件厚度+1mm,增加1mm是考虑超程及刃磨。
5)如图2-63所示为冲长方孔凸模护套结构。
图2-62 弹性凸模护套结构
1—钢垫圈 2—橡皮垫圈 3—凸模 4—外套
图2-63 长方孔凸模护套
a)工作部分 b)凸模护套
2.3.22 短凸模精密冲孔模(一)
如图2-64所示为带有浮动模柄及多导向精密冲孔模。
本模具适用于精密小孔冲裁工作。结构特点是:①多导向,即模架的导柱导套,接头8与上模座;凸模固定板4与导板3之间的小导柱10与小导套9;凸模5与导板3之间均按IT6~IT7级精度间隙配合。②导板与固定板之间空隙较小(一般取制件料厚再加2~3mm),凸模的有效工作行程非常小。③模架采用瑞士精密钟表模架标准,上下模座厚,导柱导套导向部分长。因此,冲裁工作稳定,能提高制件精度和延长模具使用寿命。
2.3.23 短凸模精密冲孔模(二)
如图2-65所示为短凸模多孔冲孔模又一实例。
本模具结构特点为:制件孔多且尺寸小(<ϕ2mm),为了提高模具寿命,采用了厚垫板短凸模的结构设计,同时卸料板1与凸模固定板2,卸料板1与凸模4均按IT6~IT7级精度间隙配合,装配后的实际配合间隙前者比后者要小些。
图2-64 短凸模精密冲孔模(一)
1—凹模 2—精密钟表模架 3—导板 4—凸模固定板 5—凸模 6—连接头 7—弹顶器(橡皮) 8—接头 9—小导套 1O—小导柱
图2-65 短凸模精密冲孔模(二)
1—卸料板 2—凸模固定板 3—垫板 4—凸模 5—下垫板 6—凹模
2.3.24 短凸模中厚料冲孔模
如图2-66所示为短凸模中厚板料冲孔模。
图2-66 短凸模中厚板料冲孔模
制件材料为低碳钢板,料厚4mm,冲孔直径最小为ϕ2.030+0.09mm,最大为ϕ3.30+0.05mm,最小孔距公差为(6.2±0.05)mm,要求较严。
本模具采用滚动导向模架,凹模、小压板之间又有小导柱导向来提高上下模的对中要求。小凸模未设护套,采用超短凸模来提高它的强度。
模具工作时,采用冲击块冲击凸模进行冲孔。当上模下行时,卸料板4和小压板3先后压紧坯件,凸模10、11、12上端露出小压板3上平面,上模继续下行,冲击块14冲击凸模10、11、12对坯件进行冲孔,卸料由卸料板4完成。定位板5、9厚度小于料厚。
2.3.25 叶轮辐板多孔冲模
图2-67 叶轮辐板多孔冲模
a)制件(材料5A02铝合金,料厚1.5mm)
如图2-67所示为叶轮辐板多孔冲模。
制件叶轮辐板有弧形槽孔共36个,均匀分布,每个槽的尺寸控制在10°±15′之内,槽底尺寸为ϕ(95±0.2)mm,对中心圆孔ϕ450+0.05mm的同轴度≤0.1mm。
本冲模毛坯为带内孔ϕ450+0.05mm的圆片,外圆为115mm,由模具中定位柱16定位后进行冲裁。槽孔宽为1.2mm,小于料厚1.5mm,类似于小孔冲裁,故采用较短凸模长度(L=18mm)来提高凸模强度。整个模具采用四导柱模架外,上模对下模的相对位置靠导向柱10与导向套11精密滑动配合保证,其工作行程控制在4mm之内。压料板兼卸料板4与凹模17又是一起加工而成的,因此冲压稳定性和冲裁精度很高。
图2-67 叶轮辐板多孔冲模(续)
b)模具 1、7、13、15—螺钉 2—衬板 3、6、14、18—圆柱销 4—压料板兼卸料板 5—衬板 8—橡皮 9—模柄 20、10—导向柱 11—导向套 12—垫板 16—定位柱 17—凹模 19—固定板 21、22—凸模
2.3.26 印制板冲孔模
如图2-68所示为印制板冲孔模。
图2-68 印制板冲孔模
a)模具 b)两孔及孔与边缘的最小搭边 (—基板厚度(mm)—两孔间最小搭边值—孔与边缘的最小搭边值) 1—凹模固定板 2—凹模 3—定位销 4—卸料板组件 5—弹簧 6—凸模 7—固定板组件 8—小导柱 9—小导套 1O—卸料板(兼压料板)
印制板为电器产品中广泛使用的一种零件,材料为表面覆铜箔酚醛纸质层压板或环氧板等,厚度为1.5mm左右。印制板根据不同要求,在它的上面布满了许多小孔,如彩电主印制板为2000个左右,录像机用主印制板在3000个左右,其中80%的孔为ϕ0.7~ϕ1.3mm,还有一些腰圆孔、矩形孔,其中孔的尺寸为2.5mm×1mm占了不少。大生产都用冲裁方法制成。
为了得到较大的压料力,防止印制板冲孔时孔壁分层或裂纹,上模采用六个方钢丝强力弹簧,卸料板组件4材料采用CrWMn,并淬硬至50~54HRC,小凸模可采用琴钢丝制造。凸模与固定板、卸料板均为间隙配合。但卸料板也起到导板作用,卸料板与凸模之间的配合间隙比固定板与凸模之间配合间隙更小,凸模的正确位置完全靠卸料板保证。卸料板与固定板另设有小导柱导向。下模为防止废料胀死,漏料孔扩大至ϕ5mm,制件的孔与孔较近时,漏料孔可以相互开通。
下模凹模上双点画线为冲孔凹模区域。为了提高加工质量,凹模、卸料板可夹在一起加工。为了确保印制板的加工质量,有的印制板需加热后冲裁,加热冲裁时要考虑热胀冷缩的影响;同时印制板上孔与边缘以及孔壁之间的最小搭边值应保证在合理范围内,如图2-68b所示。
2.3.27 管子冲孔模(一)
如图2-69所示为管子冲孔模。
图2-69 管子冲孔模(一)
a)被冲管子已放入模具里 b)上下模压紧管子 c)模具闭合状态
管子是在上下模的弹压压料板包住并压紧下直接由凸模在无凹模的情况下将孔冲出。两个凸模从外向内冲孔,这种结构容易导致孔的边缘有轻微凹陷,可以用合适的凸模工作端面来解决。
2.3.28 管子冲孔模(二)
如图2-70所示为管子冲孔模。
与图2-69结构上的不同是本模具上、下模之间设有导正销,使上、下模闭合时有正确的位置;另外凸模在一定尺寸范围内可以快速更换,使本模具有通用性,还有弹性元件用聚氨酯橡胶弹压力大。为使凸模工作部分与制件的接触面越小越好,使用中,对材质较软或管壁小于2mm的管子冲孔,建议用图2-70c中Ⅰ、Ⅱ类凸模;对于材质较硬或管壁大于2mm管子冲孔,用Ⅲ、Ⅳ类较好。
开始工作时,聚氨酯橡胶10被压缩,使上、下活动座3、2抱紧管子11,同时,凸模从上、下活动座中升出,冲入管子中将孔冲出。当工作结束时,由于聚氨酯橡胶能量释放,活动座2、3将制件卸下,完成一个工作行程。
图2-70 管子冲孔模(二)
a)制件 b)模具 c)凸模工作部分形状 d)模具闭合时凸模冲孔情况 1—下凸模座 2—下活动座 3—上活动座 4—导正销 5—上凸模座 6—上模座 7—固定螺钉 8—位置螺钉 9—凸模 10—聚氨酯橡胶 11—管子 12—紧定螺钉 13—下模座
2.3.29 沙滩椅管子对向冲孔模
如图2-71所示为沙滩椅管子冲孔模。
制件为沙滩椅管子,在管子的上面冲ϕ4.2mm通孔,孔的中心离管子一端为100mm,要求这个距离在模具上定位是可调的,从而可以适应不同尺寸的加工。
装有相同的两组模块内,在卸料板2将管件1抱紧后,由凸模4分别在管件1的上下两个方向同时冲孔,这样管件1在冲孔时不产生变形。凸模4固定在定位套13上后装在凸模固定套9中,用紧定螺钉10紧固。考虑到凸模4较细长,又安装了小导柱14进行导向,模具工作时,小导柱14始终处于导向状态,凸模4冲向管件1后,由凸模固定套9触及凸模导套3限位,完成冲孔。
凸模设计成针形,如图2-71c所示。相比台阶形结构容易加工,成本较低,安装时将顶部加热后铆合磨平即可,铆合余量h=1~2mm,凸模端部设计成斜面,使孔的周围变形小。一般取斜角α=30°~45°。凸模刃口要保持锋利。
当凸模需刃磨时,卸下紧固螺钉6,拧下紧定螺钉10即可实现凸模的快换。并且可将定位套13作成许多长短不同的尺寸组,实现凸模4长度的调节。
本模具控制孔中心至管子端100mm的限位装置图中未画出。根据管件需要,上下模可安装多个相同模块进行多孔冲制。
图2-71 沙滩椅管子对向冲孔模
a)沙滩椅管子(ϕ19×0.8mmQ235钢管) b)模具 c)凸模结构 1—管件(圆钢管) 2—卸料板 3—凸模导套 4—凸模 5—橡皮 6—螺钉 7—卸料螺钉 8—上模座 9—凸模固定套 10—紧定螺钉 11—模柄 12—垫块 13—定位套 14—小导柱 15—小导套
2.3.30 方管双面冲孔模
如图2-72所示为跑步机方管双面冲孔模。
利用本模具将方管放入固定条11与活动压条12之间的凹模板2上,一头靠住定位角钢3,然后由手柄13顺时针方向扳动,将方管夹紧定好位后,上模即可下行冲孔。本模具特点是空心方管中无芯子,在一次冲压行程中凸模同时冲两个双面腰圆孔,尺寸精度高,一致性好。
2.3.31 管子冲长圆孔模
如图2-73所示为管子冲长圆孔模。
管子长孔距管端的距离由后挡块12控制,定位精度在0.13mm之内。
冲压时,管子放在左右夹紧镶块10之间,管端与后挡块12相接触定位。上模下行,管子在左右斜楔作用下,驱使滑块7向模具中心运动,将管子夹紧状况下凸模进入管子冲出第一个长圆孔,然后把管子旋转180°,使定位销进入长圆孔定位,开始冲第2个长圆孔,上模上行,转动定位键,使定位销下降,取出管子。
图2-72 方管双面冲孔模
a)跑步机方管(材料Q215方管20mm×20mm×1.5mm) b)模具 1—下模座 2—凹模板 3—定位角钢 4—固定板 5—上模座 6—模柄 7—垫板 8—凸模 9—卸料板 10—凹模镶块 11—固定条 12—活动压条 13—手柄 14—锁紧偏心轮 15—轴 16—支撑块
图2-73 管子冲长圆孔模
1—定位键 2—管子 3—螺钉 4—定位器 5—垫板 6—止动块 7—滑块 8—斜楔 9—带滑动导向模架 10—夹紧镶块 11—凸模 12—后挡块
2.3.32 圆管长方孔冲模
如图2-74所示为圆管长方孔冲模。
本模具为对冲冲孔模结构。工作时,圆管坯件放在下压紧块9上,制件一端靠压紧块阶梯端面(见图2-74cR10mm的圆弧面)定位。冲压开始,上模下行,上压紧块8先接触导销7,通过两个导销先导向。上模继续下行,上、下压紧块将制件压紧,上模再继续下行冲裁开始,废料落入钢管腔内,上模上行,上、下压紧块从凸模上将制件卸下,钢管落在下压紧块上,取出制件,冲孔过程完毕。
凸模结构如图2-74d所示,采用斜刃,尖角处有R1.5mm圆弧,以减小冲裁力和提高模具使用寿命。凸模材料选用Cr12钢制造,刃口部分硬度58~60HRC,固定部分硬度为35~40HRC。
2.3.33 长圆管多孔冲模
如图2-75所示为长圆管多孔冲模。
本模具采用活动悬壁上下对冲方法将长圆管上6×ϕ14+0.2-0.1mm孔一次冲成。
凹模主体10为一长圆悬臂(见图2-75c)长520mm,选用Q235钢制成。侧面两边开槽10mm×2mm,为的是避开有缝钢管件的焊缝,中心ϕ25mm通孔是废料排出口。凹模刃口部分采用凹模镶套14(见图2-75d),它与凹模10为过盈配合。
上、下压料板与钢管接触处设计成弧形,增大压板与钢管的接触面,能防止冲压时钢管变形。
螺钉7调节凹模10和下压料板6的距离,保证钢管方便地插入凹模。
图2-74 圆管长方孔冲模
a)圆管(材料不锈钢管,壁厚1.2mm) b)模具 c)压紧块工作状态 d)凸模 1—上模座 2、11—垫板 3、14—卸料螺钉 4、13—聚氨酯橡胶 5、12—凸模 6、10—凸模固定板 7—导销 8—上压紧块 9—下压紧块 15—下模座
图2-75 长圆管多孔冲模
a)制件(焊接有缝钢管) b)模具 c)凹模 d)凹模镶套 1、13—上、下模座 2—卸料橡胶 3—垫板 4—固定板 5、15—凸模 6、16—压料板 7—螺钉 8—聚氨酯橡胶 9—活动块 10—凹模 11—圆柱销 12—压块 14—凹模镶套 17—模柄 18—圆柱销 19—导柱 20—卸料板 21—支撑杆
工作过程为钢管插入凹模10后,上模下行,压料板6、16压紧钢管,接着上凸模15冲穿钢管上面一排6个孔,上模继续下行,上压料板16接触钢管同时,压块12接触活动块9,推动带有钢管的活动凹模10一起向下移动,下凸模5冲穿下面一排6个孔,完成多孔对冲工作。压力机滑块回程时,利用卸料橡胶2使钢管从凸模中退出,凹模复位,废料从凹模中用压缩空气吹走。
本模具结构可以改变凸、凹模形状,对异形管和异形孔进行多孔冲裁。
2.3.34 长L形件多孔冲模
如图2-76所示为长L形件多孔冲模。
图2-76 长L形件多孔冲模
a)模具 b)制件 c)孔放大图 1—钢球 2—螺塞 3—弹簧 4—定位块 5—凹模固定板 6—卸料板镶块 7—卸料板 8—橡皮 9—凸模 10—上固定板 11—上垫板 12—螺钉 13—固定凸模镶块 14—压板 15—凹模镶块压板 16—组合凹模镶块 17—下垫板 18—压紧螺钉 19—垫块 20—定位镶块
制件的毛坯压弯成L形后,在冲孔模上经8次冲制将制件上的360个长槽孔全部冲出。一次冲45个槽孔,然后经定位镶块20定位,隔孔再冲,分四段8次完成360个槽孔的冲制。单孔形状尺寸见图2-76c。
本模具模架采用四导柱结构;上下模、卸料板均在导柱的导向下工作,凹模、凸模固定板和卸料板为了便于加工、维修、保证加工精度,均采用镶拼结构;模架的导柱与上模座固定、导套固定在下模座上,便于下模凹模的整体刃磨。冲压前,制件的侧边在四处靠四个钢球1压紧、上下由卸料板7压紧,然后上模下行进行冲孔,凸模较短,并在卸料板镶块6的精密导向和保护下工作,凸模强度好。
2.3.35 可换排孔通用冲孔模
如图2-77所示为可换排孔通用冲孔模。
本冲孔模可在条料或角钢上冲出成一直线的不同孔距的各类孔。适用于多品种小批量生产。
图2-77 可换排孔通用冲孔模
1—挡料块 2—模架 3—凸模固定座 4—卸料板 5—凸模固定螺母 6—可换凸模 7—可换凹模 8—制件 9—凹模固定座
利用本模具在一次冲程中冲出的一排孔中,孔的大小、数量、孔距通过更换可换凸模6、可换凹模7和在各自的凸、凹模固定座上可移动,调整孔距位置,实现不同加工要求。根据制件的形状和特点不同,挡料块1的形状和位置可以变动。
2.3.36 锥形管冲孔模
如图2-78所示为锥形管冲孔模。
锥形管经缩口、扩口、冷挤压成形而成。中间位置两个ϕ3mm轴对称孔由冲孔模加工而成。
本模具采取锥形管垂直放置,侧向冲孔的模具结构。制件定位容易,冲件质量好,操作方便,但模具结构较复杂。
图2-78 锥形管冲孔模
工作时,上模座1带动压杆8向下运动,动滑块10在压杆的作用下沿动滑块10侧向导轨11向下运动,由于有楔角的存在会推动楔形侧滑块7向中间运动,此时楔形侧滑块7上的冲孔凸模22沿着凸模导轨向中间运动,完成冲孔成形。成形后上模开启,楔形侧滑块7在弹簧18的作用下沿导轨26向外侧运动,冲孔凸模22从凹模腔中退出,直至分离。冲孔成形结束,冲裁过程中产生的废料从凹模内部开设的废料通孔中排出。
此模具的关键在于斜楔机构的设计。斜楔机构主要由楔形侧滑块7、楔形侧滑块导轨26、动滑块10、动滑块侧向导轨11、凸模导轨24和弹簧18组成。楔形侧滑块和动滑块配合部分的楔角为45°,因此斜楔机构上、下方向和左、右方向的行程相同。因锥形管壁厚仅0.4mm,所以斜楔机构的行程可以很小,本模具采用的动滑块在压杆作用下的行程为2mm。另外,在模具闭合时,冲裁凹模21的顶端距压杆固定板下表面的距离要求不小于锥形管的高度,如此才能确保成形后锥形管顺利取出。