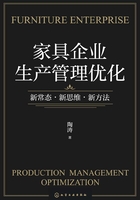
2.1.2 家具生产普遍采用推进式系统
对于加工装配式生产,产品由许多零件构成,每个零件要经过多道工序加工。要组织这样的生产,从理论上可以采用两种不同的方式。
2.1.2.1 推进式生产系统
所谓推进式(Push)生产系统,简称“推式生产”,是指根据某时期的需求预测和现有库存水平,按零部件展开,计算出每种零部件的需要量和各生产阶段的生产提前期,确定每个零部件的投入产出计划,按计划发出生产和订货的指令,然后向最前面的工序发出生产指令,由前一道工序把生产出来的零部件依次“推”到下一道工序,不管后一道工序和下游生产车间当时是否需要,直至成品形成。它通过把生产计划与控制的源头放在链条的起始端,制定详细的生产计划来保证任务的完成,是一种集中式的生产管理模式。显然,在这种方式下,物流和信息流是分离的。推进式生产系统结构示意图如图2.1所示。

图2.1 推进式生产系统结构示意图
作为以MRP Ⅱ、ERP生产控制方法为代表的推进式生产系统,于20世纪60年代中期在美国大批量生产背景下产生发展起来,其优势在于中长期计划能力,注重前期规划,用尽可能周密的计划集中安排各环节的人、财、物等资源以及生产加工,以应对生产的波动。但在实际上,任何计划都不可能把未来的情况考虑得十分周全,因此计划难以做到十分精确,而且不可避免的会有一些随机因素干扰计划的执行。比如说运用ERP系统的家具企业在生产方面会存在一些问题:
① 家具产品结构复杂、种类繁多,产品更新换代的周期短,给数据资料收集工作带来了较大难度;
② 家具产品所用的材料特性差异较大,规则材料、不规则材料都被大量使用,特别是实木材料,本身是家具生产所必需的材料,但是受树木种类和生长差异性的制约,无法统一材料规格,给材料编号、单位换算、用量分析、材料采购及库存管制都带来许多困扰;
③ 家具订单中经常遇到产品编号与实物匹配的问题,同一款产品可能会随时更换材料、配件和产品组合方式,如某一款式的沙发订单,一部分要求用红色皮,一部分用灰色皮,但是根据厂家和客户的习惯,对于形状、规格相同的产品通常使用相同的产品编号,这样一来,如何建立BOM资料、如何控制采购数量、如何确定领料的材料和数量等问题就成为令人头疼的事;
④ 家具生产各阶段之间的控制重点不相同,如备料阶段为了提高材料的利用率,需要尽量加大生产批量,生产过程中为了缩短生产周期,降低在制品库存而减少运输批量,涂装阶段要考虑产品涂装效果和颜色统一,需要把相同系列的产品安排集中生产……这些控制特点是通用ERP软件无法顾及的,经常出现生产去迁就软件的情况,这也就是为何ERP软件对家具行业的生产控制模块无法很好实现的主要原因;
⑤ 轮班作业家具企业一般都采取两班作业制,这一特点给家具企业的日常生产管理带来了一系列的问题,轮班管理夜班生产和交接班等生产数据多,并且数据的收集维护和检索工作量大。
总结起来,推进式生产系统的不足主要有以下几点:
① 由于编排生产计划时,需要提前设定安全库存量、生产提前期等,因此在制品库存和成品库存量都比较大;
② 当需求发生波动时,主生产计划就要进行修改,后序的各个计划也都要跟着进行修改,计划工作量很大;
③ 在进行生产控制时,没有考虑前馈控制,而是通过事后反馈进行生产控制,相对生产实际,存在着不可避免的滞后;
④ 由于对生产采取完全集中的控制,每道工序都要按照制定的生产计划来进行生产,工序间又无协调机制,无法保证每道工序间产量的动态平衡,极易导致工序间在制品库存过多以及生产与实际需求不一致等问题。
2.1.2.2 牵引式生产系统
所谓牵引式(Pull)生产系统,简称“拉式生产”,根据市场需求信息确定生产指令,生产指令由最后一道工序根据订单发出,每道工序、每个车间和每个生产阶段都按照当时的需要向前一道工序、上游车间和生产阶段提出要求、发出工作指令,前道工序由后道工序触发,由后道工序在必要时刻向前道工序领取必要的零部件或物料,然后前道工序只需要生产由后道工序领取走的那部分物料即可。牵引式生产系统的物流和信息流是结合在一起的。日本丰田汽车公司的生产系统就是牵引式生产系统。牵引式生产系统结构示意图如图2.2所示。

图2.2 牵引式生产系统结构示意图
以JIT理念为代表的牵引式生产系统实质上是一种文化理念的传承,是一种以根植于日本民族土壤的精神力量作为支撑的,因此在特定产品生产类型的日本企业获得了巨大成功。牵引式生产系统在计划执行与降低成本,特别是在降低在制品数量、减少浪费和现场改善等方面具有明显的优势,目前在医药、化工原料、计算机等大批量重复性生产企业应用比较成功。但是牵引式生产系统所要求的生产环境,如生产能力平衡、需求供应稳定等,对中国现阶段家具生产企业来讲是一道无法逾越的门槛。因此,在众多家具企业生产系统中推行的所谓“精益生产”、“JIT”等理念,稍加留意便会发现,这些理念推行的主要定位在诸如“5S”、零浪费、全面质量管理(TQM)、全面产能维护(TPM)等生产现场改善的肤浅层面,主要负责作业计划的执行、生产的控制和现场的反馈工作,至于一个流生产、多面手工人、制造单元等核心层面方案由于过于理想化,对于现阶段家具生产来说难以贯彻,真正获得成功的家具企业生产案例还没有。究其原因,主要在于从汽车生产等行业发展出来的精益生产技术在多品种小批量的家具生产环境中具有一定的局限性。
① 计划性弱,面向短期计划,生产系统稳定性低。牵引式生产系统整体计划性弱,由于缺少安全库存,对生产波动敏感,对需求变化的响应能力要远低于推进式生产系统,一旦某生产环节停工,那么此前的所有工序都将处于待工状态,在生产中不确定因素时有发生,过少的库存会导致生产的波动,使整个环节加工情况时好时坏。
② 应对需求变化能力不足。牵引式生产系统比较适用于少品种、大批量、重复性生产类型,需要非常稳定的生产周期,难以适应较大的需求变化。过大的需求变化将导致生产能力严重过剩或严重不足,造成生产资源闲置浪费或失去订单。
③ 应用和实施受很多实际条件的限制。如要求系统中的人员具有多种能力,工人必须熟悉生产流程中多个工站的操作,可以应对产品类型发生变化时的生产要求。要求一体化的供应系统,强调人、机、企业间的相互协作来保证生产的稳定和能力的平衡,且需要非常稳定的生产周期,产品品种有限且具有一定的相似性,这就使得JIT的大规模应用显得非常困难。
2.1.2.3 我国家具生产目前普遍采用推进式生产系统的原因
我国当前家具生产普遍采用推进式生产系统是基于以下几方面原因。
① 不论是实木还是板式家具生产,从古至今都必须依照一定的程式即工序,一步一步方能制造出来,缺一道工序或是交换一下工序的位置都会出问题,因而从源头开始的这种生产控制形式符合常理。例如,对于在不同方向上既有榫头又有榫眼的实木零件,一般先加工榫头然后再加工榫眼,以榫肩作为定位基准确保装配精度,就是这个道理。
② 随着信息技术的发展,美国率先将推进式生产系统发展成为MRP、MRP Ⅱ、ERP等企业信息化平台,以制定周全计划引领生产的形式迎合了中国家具企业生产的需要,也对近十年来中国家具大批量跨越式生产的发展起到了有力的推动作用。
③ 我国家具企业多数为家族企业,从小手工业、作坊式的简陋工场发展而来,属于劳动密集型行业,员工学识水平与业务素养普遍不高,难以达到诸如执行力、学习力、凝聚力、多面手等牵引式生产系统的高素质员工要求。
④ 牵引式生产系统主要面向的生产控制对象是医药、汽车、计算机等大批量、少品种、重复性生产企业的生产系统,由于追求零库存可能导致对需求变化的响应能力远低于推进式生产系统,因此其核心理念不适合我国家具生产方式的要求。
在这里有必要强调的是,2008年金融危机之后,中国家具市场已由卖方市场转变为买方市场。家具生产大多以多品种小批量的方式进行,需求波动较大,致使整体粗放型的推进式生产系统存在的问题日益显露出来,主要表现在生产灵活程度较低、在制品库存较高、订单准交率偏低。这些缺陷也许在高速发展、品种单一且生产批量较大的时期看不见,但在经济结构转型升级的买方主导的市场环境里却马上浮出水面:生产灵活程度低将造成浪费;在制品库存高将造成生产成本居高不下和资金链的断裂;订单准交率偏低将造成客户流失和企业的倒闭。
然而回过头来看,集约型的牵引式生产系统追求的消灭一切浪费等理想,在我国目前的家具生产环境中是难以实现的,主要原因是:多数企业面临的市场需求都具有较大的波动与不确定性,难以直接面对客户组织生产;供应商对于原材料供应难以做到真正准时、有效;整个系统实施看板管理非常困难。那么在今天市场趋于饱和、买方主导市场的大背景下,家具产业能否保持快速、健康和持续的发展态势,实现更高层次的发展目标完全取决于我们能否站在结构调整与产业转型升级的高度,创造性地提出解决问题的新思路和主张,这已经成为当前我国家具行业亟待解决的关键性问题。