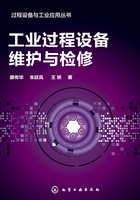
3.2 往复式压缩机的检修
为杜绝压缩机严重事故的发生,以及将故障减少到最低限度,除采取动态监测手段以外,实行科学的计划检修对压缩机安全、稳定、长周期运行也是一种可靠的手段。
3.2.1 往复式压缩机的计划检修制度
压缩机的计划检修制度按检修的要求和工作量的大小分为小修、中修、大修3种。
(1)小修
不定期进行,主要是检查性的检修,例如排除机组运转时发现的不正常现象,如阀片破裂、弹簧折断、紧固件松动等。
(2)中修
每半年一次,主要是检修易损零部件(如进、排气阀,填料、活塞环、支撑环等),并校验压力表、安全阀的精度,以及其他阀门的密封性。
(3)大修
每两年或三年一次,全面解体、检查所有零部件。检查各段进、排气阀门的气密性,更换已损坏的零部件;清洗或更换填料,塑料制品的填料每三个月(高温段每两个月)检查一次磨损量;校验有关仪表(如各段的温度表、压力表)及电气设备、安全联锁装置;检查气缸、缸套、活塞环、支撑环的磨损情况,并作必要的更换或修整;检查各连杆大头瓦和小头套的磨损情况,调整轴瓦间隙或更换大头瓦和小头套;检查主轴瓦和十字头滑履与滑道的磨损情况,调整主轴瓦和滑履滑道间隙或更换主轴瓦和滑履;清洗油过滤器和油箱,必要时更换滤芯,更换润滑油;清除冷却器和气缸水道中的积垢;对照原来记录的数据重新对压缩机找正;检查基础是否有裂纹和不均匀的下沉等不正常现象,当发现异常时,应采取必要的补救措施后才能运行。在大修中,对零部件的磨损、更换和修复等情况保留永久性记录,以利于备件的准备及做出预防性改进措施等。
3.2.2 检修周期和检修项目
3.2.2.1 检修周期
检修周期见表3-1。根据压缩机日常维护以及对压缩机状态的监测,或者已经具备开展预知维护条件的,可不受此约束。
表3-1 检修周期

3.2.2.2 检修项目
(1)小修项目
①检查、紧固各部位螺栓。
②检查、紧固十字头销。
③检查清洗气阀或更换阀片、阀座、弹簧和升高限制器等零件。
④检查或更换密封函填料函。
⑤检查注油器、循环油止逆阀、油过滤器滤芯、油冷器、油管路等,清除清洗。
⑥清洗气缸冷却水夹套。
⑦清洗水冷却器、油分离器。
⑧消除其他缺陷。
(2)中修项目
①包括小修项目。
②检查或更换活塞、活塞环、支撑环及活塞杆。
③检查或更换连杆大头瓦、小头套,并调整间隙。
④检查或更换主轴瓦、并调整间隙。
⑤检查或更换连杆螺栓;检查十字头滑履、滑道,并调整间隙。
⑥检查调整各段气缸余隙。
⑦安全阀清洗、研磨和调试。
⑧检查、修理或更换压力表、温度表。
⑨检查油泵,清洗油箱,更换润滑油。
检查、清洗机身呼吸器。
(3)大修项目
①包括中修项目。
②解体、清洗各部件。
③曲轴、连杆、连杆螺栓、十字头销、活塞杆无损探伤检查,必要时更换。
④检查修理十字头,必要时更换。
⑤检查、修理或更换气缸套。
⑥修理或更换活塞、活塞环、填料函。
⑦检查机身水平度、垂直度。拉线或采取激光找中的方法对中气缸中线。
⑧检查机身与基础状况,测量机身下沉情况,根据实测结果进行相应的消缺处理。
⑨检查、修理冷却器、油分离器,并做水压试验检查。压力容器按压力容器检验规程的规定进行。
检查更换腐蚀的管线及出入口切断阀;主、辅机防腐喷漆。
3.2.3 往复式压缩机的检修方法
零件清洗后即可进行常规检查。通过检查发现零件缺陷,区别零件技术状况,并分辨出零件该修复或该更换,以便检修中处理。检测方法如下。
①目视。
利用肉眼或借助放大镜检查的方法,称为目视(亦称为视检)。一次宏观检查零部件的破裂、折断、严重变形和磨损等。例如:气缸镜面的划痕、轴瓦的拉伤、裂纹和剥落、气阀的损坏、活塞环及支撑环的磨损等。
②手检。
凭手的感觉检查某些紧固件是否松动,转动副以固定其中一件零件,转动另一件零件,凭手的感觉判断转动副是否正常等。手检以操作者经验为主,只作为初检。
③敲击听诊。
用敲击零件发出的声音来诊断零件。此方法常用来检查零部件的裂纹及轴瓦巴氏合金的脱壳等。
④测检。
利用各种测量仪器检查。常用来检测弯曲、圆度和圆柱度及各配合间隙和各点水平。用压铅法测量轴承间隙、气缸上下止点间隙。
⑤着色法。
某些零部件的裂纹或金属表面的裂纹很细,单凭肉眼很难诊断时,常用着色探伤法来判断。
⑥仪器探伤。
利用磁力、X射线、超声波等探伤仪器对重要零部件进行内外部缺陷检查。
⑦水压试验检查。
用以检验受压容器的缺陷和承压能力。
⑧测量并记录易损件的尺寸。
3.2.4 往复式压缩机的检修质量标准
(1)基础
①外观检查不允许有裂纹、疏松、露筋、渗油和混凝土剥落等缺陷。
②基础无不均匀下沉或倾斜。
(2)机身、中体
①机身纵、横向水平度≤0.05mm/m。
②十字头滑道中心线与主轴瓦背孔中心线垂直度≤0.02mm/m。
③机身主轴承与电机外伸副轴承座孔中心线同轴度≤0.03mm。
④机身滑道圆柱度≤0.5mm。
⑤气缸中心线与滑道同轴度允许偏差见表3-2。
表3-2 气缸中心线与滑道同轴度允许偏差 单位:mm

⑥组装后各列滑道中心线平行度为0.1mm/m。
⑦机身油池进行试漏,试漏时间≥4h机身不得有渗漏现象。
(3)曲轴、轴承
①曲轴经放大镜或探伤检查,不得有裂纹缺陷;主轴颈和曲拐擦伤面积不得大于2%,深度不大于0.01mm;超过时需进行机械加工,其加工减少量不超过原轴颈直径的1%,并调整其配合间隙。
②曲轴安装水平度≤0.10mm/m。
③曲轴开度差≤10-4s,装上电机后≤3×10-4s(s为行程,mm)。
④主轴颈径向圆跳动值≤0.05mm;各主轴颈同轴度≤0.03mm。
⑤轴颈修复后圆度,圆柱度要求见表3-3。
表3-3 轴颈同柱度要求 单位:mm

⑥滑动轴承。
a.瓦背与轴承座孔接触面积不少于85%,主轴颈与主轴承接触面积不少于90%。
b.主轴颈与主轴承配合一般为。径向间隙为(0.8~1.2)×10-3d(d为主轴颈直径,mm),轴向间隙为0.2~0.5mm。
c.厚壁轴承厚度磨损超过原厚度的10%或剥落、脱壳面积达到3%时,应重新浇铸或更换。
⑦滚动轴承。
a.滚动轴承应转动灵活、无杂音,滚子和内外圈的滚动面应无锈蚀、麻点等缺陷。
b.滚动轴承内圈与轴的配合为,外圈与轴承座内孔的配合为
。
(4)连杆、十字头
①连杆直线度≤0.5mm/m。
②连杆大、小头孔中心线平行度≤0.05mm/m,孔的圆柱度不超过直径尺寸公差。
③十字头和十字头销经放大镜或探伤检查应无裂纹等缺陷。
④十字头瓦和十字头销径向间隙:
a.铜合金轴承为(0.7~1.2)×10-3d (d为十字头销直径,mm)。
b.巴氏合金轴承为(0.4~0.6)×10-3d (d为十字头销直径,mm)。
⑤整体连杆小头轴承与连杆孔的过盈配合量:铜合金轴承为0.02~0.08mm;钢壳巴氏合金轴承为0.05~0.10mm。
⑥连杆大头瓦与曲轴颈接触面积不少于85 %,径向间隙为(0.0006~0.0008)D(D为曲轴颈直径,mm)。
⑦连杆轴向间隙一般为0.30~1mm;非定位轴向间隙为2~5mm。
⑧十字头瓦与滑道应均匀接触,径向间隙为(0.6~0.8)×10-3d (d为十字头外径,mm)。
⑨十字头颈部端面与滑道垂直度为0.2mm/m。
十字头销的圆度、圆柱度要求见表3-4。
表3-4 十字头的圆度与圆柱度要求 单位:mm

连杆螺栓经放大镜或探伤检查不得有裂纹;螺栓拧紧时,伸长量不超过原长度的0.1%。
(5)活塞、活塞环、支撑环
①活塞、活塞环、支撑环经放大镜或探伤检查,不得有裂纹、砂眼、伤痕等缺陷。
②活塞下部耐磨支承表面应均匀接触,支承面磨损不大于原高度的1/2,并不允许有开裂、脱壳现象。
③活塞与气缸安装后径向间隙:
a.立式气缸按公式计算
δ=α(t2-t1)D+δ0 (3-1)
式中 δ——径向间隙,mm;
α——活塞材料的线胀系数,℃-1;
D——气缸直径,mm;
t1——室温,℃;
t2——工作温度,℃(可取气体出口温度);
δ0——按或
配合间隙,mm。
b.卧式气缸,活塞下部有耐磨支承时,上部间隙值为(0.008~0.002)D(D为气缸直径,mm)。
c.无油润滑活塞,塑料整体支承环外圆与气缸内壁间隙值为(0.01~0.02) D(D为气缸直径,mm)。
④活塞磨损后,测量其圆度、圆柱度应符合表3-5的规定。
表3-5 活塞圆度与圆柱度的要求 单位:mm

⑤活塞中心线与活塞杆孔中心线同轴度≤0.05mm。
⑥活塞杆孔中心线与活塞轴肩支承面的垂直度≤0.2mm/m;活塞环槽两端面与活塞杆孔中心线垂直度≤0.2mm/m。
⑦活塞环外圆锐角应倒成小圆角,内圆锐角为45°,尺寸见表3-6。
表3-6 活塞环外圆与内圆尺寸 单位:mm

⑧活塞环的径内磨损量不超过原厚度的20%:轴向两平面的平面度≤0.05mm。
⑨活塞环放入专用量规内其外表面应密合,透光检验时,整个圆周上漏光不得多于两处缝隙,缝隙长度每处不超过45°圆心角所对的弧长;距开口处不少于30°圆心角所对的弧长。
活塞环放入活塞环槽内,在限制自由膨胀的情况下,沉入0.3~0.5mm;活塞环内圆与活塞环槽底外圆的配合为
,其径向间隙值见表3-7。
表3-7 活塞环内圆与槽底外圆的径向间隙 单位:mm

活塞环装入气缸后的开口间隙及轴向间隙:
a.铸铁活塞环的开口间隙及轴向间隙见表3-8。
表3-8 铸铁活塞环的开口间隙与轴向间隙 单位:mm

b.非铸铁活塞环开口间隙及轴向间隙:
轴向间隙按公式(3-2)计算
B=hα(t2-t1) (3-2)
式中 B——轴向间隙,mm;
h——活塞环轴向高度,mm;
α——活塞环材料的线胀系数,℃-1;
t1——室温,℃;
t2——工作温度,℃(可取气体出口温度)。
开口间隙按公式(3-3)计算
A=πDα(t2-t1)+0.005D (3-3)
式中 A——活塞环开口间隙,mm;
D——活塞环外径,mm;
α——活塞环材料的线胀系数,℃-1;
t1——室温,℃;
t2——工作温度,℃(可取气体出口温度)。
塑料活塞环在槽内的轴向间隙按公式(3-4)计算
B=bα+0.01b (3-4)
式中 B——轴向间隙,mm;
b——活塞环的轴向高度,mm;
α——活塞环材料的线胀系数,℃-1;
t1——室温,℃;
t2——工作温度,℃(可取气体出口温度)。
活塞环装入气缸后,在符合本节第⑨条要求的情况下贴合允许间隙见表3-9。
表3-9 活塞环装入气缸后贴合允许间隙 单位:mm

(6)活塞杆
①活塞杆经放大镜或探伤检查不得有裂纹缺陷。
②活塞杆直线度≤0.05mm/m。
③装机后活塞杆跳动量不超过0.10mm/m。
④活塞杆圆度、圆柱度要求见表3-10。
表3-10 活塞杆圆度和圆柱度要求 单位:mm

(7)气缸、气缸套
①气缸内壁应光滑,无裂纹、砂眼、锈斑和拉毛等缺陷;如拉毛沟槽超过1/4周或沟深超过0.5mm时,应镗缸、镶缸套或更换缸套,镗缸直径增大量不大于原气缸内径的2%,壁厚减少量不大于原壁厚的1/12。缸径增大后,活塞推力增加量不大于设计值的10%。
②气缸的圆度、圆柱度、均匀磨损值见表3-11。
表3-11 气缸的圆度、圆柱度和均匀磨损值 单位:mm

③气缸与气缸套配合过盈量:(0.000.5~0.0002)d(d为气缸套外径,mm)。
④气缸安装水平度≤0.05mm/m。
⑤气缸水压试验:
a.设计压力<10MPa时,试验压力为设计压力的1.5倍,但不得小于0.5MPa。
b.设计压力≥10MPa时,试验压力为设计压力的1.25倍。
⑥调整气缸与活塞的余隙,应符合表3-12的规定。
表3-12 气缸与活塞的余隙 单位:mm

⑦气缸连接螺栓拧入后和连接端面的垂直度为1mm/m,螺栓拧紧后,螺母与连接支承面应均匀接触。
(8)阀片、阀座
①阀片、阀座、升高限制器表面应平整、光滑,不允许有裂纹、伤痕、麻点、锈斑等缺陷。阀片与阀座结合严密。
②气阀弹簧应无损伤、锈蚀,不允许倾斜,弹性良好;同一阀片的弹簧在自由状态下长度差不超过1mm。
③气阀组装后,弹簧弹力应均匀,阀片和弹簧应无卡涩观象。
④气阀组装后,其调节装置和阀片开启度应符合图样规定。
⑤气阀组装后,应以煤油进行严密性试验,在5min内允许有不连续的滴状渗漏,其渗漏程度可参考表3-13。
表3-13 气阀渗漏程度

⑥气阀组装后,气阀中心螺栓和螺母应拧紧,并锁紧放松垫片。
(9)填料函、刮油器
①金属或塑料密封元件不允许有划痕、损伤等缺陷。
②密封元件安装前需研磨刮配,平面和径向密封面应接触均匀,每平方厘米内不少于5~6个色印点,接触面积不少于85%。
③金属密封元件的轴向间隙为0.05~0.20mm;塑料密封元件的轴向间隙,按其膨胀系数的大小来确定,一般为金属密封元件间隙的2~3倍。
④锥形金属填料密封环、平面金属填料密封环、塑料平面密封环的径向开口间隙见表3-14。
表3-14 径向开口间隙 单位:mm

⑤填料密封环组装时,开口间隙应互相错开120°。
⑥塑料平面填料盒内闭锁环与密封环等密封元件的组装需按顺序进行,闭锁环靠近气缸方向,密封环在外,接着是阻流环;闭锁环与密封环互相贴合的两个端面内圆不得倒角或倒圆。
⑦填料函安装时,必须保证润滑油及冷却水流道对正和畅通。
⑧刮油环内圆柱面应与活塞杆贴合,要求和填料密封环基本相同,安装时注意不得将刮刃口方向装反,设有两个以上刮油环时,刮油环刃口方向应相反,以达到往复刮油的目的。
(10)安全阀
①闭式安全阀阀体应做水压强度试验,试验压力应为系统工作压力的1.5倍。
②安全阀应进行气密性试验,试验压力为系统工作压力。
③安全阀启跳压力按系统额定工作压力的1.05~1.1倍。
(11)联轴器、皮带轮
①联轴器两轴对中偏差见表3-15。
表3-15 联轴器两轴对中偏差 单位:mm

②两皮带轮宽度中心线应在同一平面内,允许偏差≤1mm;轴向倾斜度≤0.5mm/m。
(12)齿轮油泵、注油器
①齿轮油泵的检修方法和质量标准按《齿轮泵维护检修规程》(SHS 01017—2004)执行。
②注油器试验压力为工作压力,保持30min不漏为合格;注油器注油止逆阀强度试验压力为公称压力的1.5倍。
(13)冷却器、缓冲器、油分离器
冷却器、缓冲器、油分离器的检修方法和质量标准按《压力容器维护检修规程》(SHS 01004—2004)执行。
(14)管道、阀门
管道、阀门的检修方法和质量标准按《工业管道维护检修规程》(SHS 01005—2003)执行。
3.2.5 维护检修安全注意事项
(1)维护安全注意事项
①严禁违章开停车和违章操作。
②严禁使用不合格或变质润滑油。
③临时处理故障,必须办理安全检修任务书,采取可靠安全措施,并按规定进行审批。
④严禁带压松动或紧固螺栓。
⑤转动外露部分必须有安全防护装置。
⑥设备运行时,不得在转动部位擦抹设备或检修。
⑦起吊重物不得在运行设备上方停留。
⑧现场不得存放与设备运行无关的物品,保持现场畅通。
(2)检修安全注意事项
①设备检修前必须办理安全检修任务书,采取可靠的安全措施,并按大、中、小修规定逐级审批。
②按规定停车,卸完余压、处理合格。
③切断电源、并挂上“有人检修,禁止合闸”标志。
④按规定办理设备交出检修手续。
⑤对检修用起吊机具、工具进行严格检查,确保安全可靠。
⑥对应该加盲板的部位加上盲板,并有盲板示意图。
⑦拆卸零部件必须按顺序进行整齐摆放,高压螺栓、活塞杆等外露螺纹,必须加以保护,以免损伤,检修现场用专用围栏围上,检修完毕将围栏和其他临时设施拆去。
⑧拆开的设备孔、管孔,要及时堵好防止掉进杂物。
⑨使用吊车和其他起吊机具时,必须有专人指挥,绳索要拴牢固。
交叉作业时,下面工作人员要戴安全帽。高空作业时,工作人员要系安全带。
需要动火作业时,必须办动火证,并按规定审批。
检修用临时灯电压不得超过36V,罐内作业临时灯电压不得超过12V。
压力容器水压试验,必须按规程规定进行。
检修完毕后,对需要封闭的部位应先经过仔细检查,防止工具、杂物等留在设备内。
检修完毕应按盲板分布图拆除检修前所加的盲板。
(3)试车安全注意事项
①设备检修后试车,要有试车方案(小修除外),经审批后按方案组织试车。
②试车必须有专人指挥,专人负责安全,专人进行操作。
③试车前需按相应要求做好一切准备工作。
④试车过程中,禁止无关人员进入现场。
⑤试车中如发生异常现象,要立即停止试车,查出原因并处理后,再继续试车。