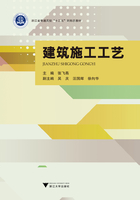
2.3 桩基础工程施工
当天然地基上的浅基础沉降量过大或基础稳定性不能满足建筑物的要求时,常采用桩基础。桩基础简称桩基,是由基桩(沉入土中的单桩)和连接基桩桩顶的承台共同组成。如图2-31所示。桩基础的作用是将上部结构的荷载,传递到深部较坚硬、压缩性较小、承载力较大的土层或岩层上;或使软弱土层受挤压,提高地基土的密实度和承载力,以保证建筑物的稳定性,减少地基沉降。

图2-31 桩基础
2.3.1 桩基础的分类:
1.按承载形状分类(见图2-32)

图2-32 桩型分类
(1)摩擦型桩。在极限承载力状态下,桩顶竖向荷载全部或主要由桩侧阻力承担;根据桩侧阻力承担荷载的份额,或桩端有无较好的持力层,摩擦型桩又分为摩擦桩和端承摩擦桩。
(2)端承型桩。在极限承载力状态下,桩顶竖向荷载全部或主要由桩端阻力承担;根据桩端阻力承担荷载的份额,端承型桩又分为端承桩和摩擦端承桩。
2.按成桩方法与工艺分类
(1)非挤土桩。成桩过程中,将与桩体积相同的土挖出,因而桩周围的土体较少受到扰动,但有应力松弛现象。如干作业法桩、泥浆护壁法桩、套管护壁法桩、人工挖孔桩。
(2)部分挤土桩。成桩过程中,桩周围的土仅受轻微的扰动。如部分挤土灌注桩、预钻孔打入式预制桩、打入式开口钢管桩、H型钢桩、螺旋成孔桩等。
(3)挤土桩:成桩过程中,桩周围的土被压密或挤开,因而使其周围土层受到严重扰动。如挤土灌注桩、挤土预制混凝土桩(打入式桩、振入式桩、压入式桩)。
3.按桩的施工方法分类
(1)预制桩。预制桩是在工厂或施工现场制成的各种材料、各种形式的桩(如木桩、混凝土方桩、预应力混凝土管桩、钢桩等),用沉桩设备将桩打入、压入或振入土中。
(2)灌注桩。灌注桩是在施工现场的桩位上用机械或人工成孔,吊放钢筋笼,然后在孔内灌注混凝土而成。
2.3.2 预制桩施工
钢筋混凝土预制桩能承受较大的荷载、施工速度快,可以制作成各种需要的断面及长度。其桩的制作及沉桩工艺简单,不受地下水位高低变化的影响,是我国广泛应用的桩型之一。预制桩按沉桩方式分为锤击沉桩和静力沉桩。
1.桩的制作、运输和堆放
预制桩主要有钢筋混凝土方桩、混凝土管桩和钢桩等,目前常用的为预应力混凝土管桩。
(1)预制桩制作
①钢筋混凝土方桩。钢筋混凝土实心桩,断面一般呈方形。桩身截面一般沿桩长不变。实心方桩截面尺寸一般为200mm×200mm~600mm×600mm。钢筋混凝土实心桩桩身长度,因限于桩架高度,现场预制桩的长度一般在25~30m。限于运输条件,工厂预制桩桩长一般不超过12m,否则应分节预制,然后在打桩过程中予以接长。接头不宜超过3个。制作一般采用间隔、重叠生产,每层桩与桩间用塑料薄膜、油毡、水泥袋纸等隔开,邻桩与上层桩的浇筑须待邻桩或下层桩的混凝土达到设计强度的30%以后进行,重叠层数不宜超过4层。材料要求:钢筋混凝土实心桩所用混凝土的强度等级不宜低于C30(30N/mm2)。采用静压法沉桩时,可适当降低,但不宜低于C20,预应力混凝土桩的混凝土强度等级不宜低于C40,浇筑时从桩顶向桩尖进行,应一次浇筑完毕,严禁中断。主筋根据桩断面大小及吊装验算确定,一般为4~8根,直径12~25mm;不宜小于ϕ14,箍筋直径为6~8mm,间距不大于200mm,打入桩桩顶2~3d长度范围内箍筋应加密,并设置钢筋网片。预制桩纵向钢筋的混凝土保护层厚度不宜小于30mm。桩尖处可将主筋合拢焊在桩尖辅助钢筋上,在密实砂和碎石类土中,可在桩尖处包以钢板桩靴,加强桩尖。如图2-33和图2-34所示。

图2-33 钢筋混凝土方桩制作

图2-34 钢筋混凝土方桩构造(单位:mm)
②预应力混凝土管桩。其是采用先张法预应力工艺和离心成型法制成的一种空心筒体细长混凝土预制构件。如图2-35所示。它主要由圆筒形桩身、端头板和钢套箍等组成,如图2-36所示。

图2-35 离心成型法

1—桩身;2—钢套箍;3—端头板;D—外径;t—壁厚
图2-36 预应力管桩示意
管桩按混凝土强度等级和壁厚分为预应力混凝土管桩(代号PC桩)、预应力高强度混凝土管桩(代号PHC桩)和预应力薄壁管桩(代号PTC桩)。管桩按外直径分为300~1000mm等规格,实际生产的管径以300、400、500、600mm为主,桩长以8~12m为主。预应力混凝土管桩的标注方法如图2-37所示。

图2-37 预应力混凝土管桩标注示意
预应力管桩具有单桩竖向承载力高(600~4500kN),抗震性能好,耐久性好,耐打、耐压,穿透能力强(穿透5~6m厚的密实砂夹层),造价适宜,施工工期短等优点,适用于各类工程地质条件为黏性土、粉土、砂土、碎石、碎石类土层以及持力层为强风化岩层、密实的砂层(或卵石层)等土层,是目前常用的预制桩桩型,本节主要介绍该桩的施工方法。预应力管桩应有出厂合格证,进场后检查桩径(±5mm)、管壁厚度(±5mm)、桩尖中心线(<2mm)、顶面平整度(10mm)、桩体弯曲(<L/1000)等项目。
(2)预制桩的起吊、运输和堆放
当桩的混凝土达到设计强度标准值的70%后方可起吊,吊点应位于设计规定之处。在吊索与桩间应加衬垫,起吊应平稳提升,并采取措施保护桩身质量,防止撞击和受振动。
桩运输时的强度应达到设计强度标准值的100%。装载时桩支承应按设计吊钩位置或接近设计吊钩位置叠放平稳并垫实,支撑或绑扎牢固,以防运输中晃动或滑动;长桩采用挂车或炮车运输时,桩不宜设活动支座,行车应平稳,并掌握好行驶速度,防止任何碰撞和冲击。严禁在现场以直接拖拉桩体方式代替装车运输。
堆放场地应平整坚实,排水良好。桩应按规格、桩号分层叠置,支承点应设在吊点或其近旁处,保持在同一横断平面上,各层垫木应上下对齐,并支承平稳。当场地条件许可时,宜单层堆放;当叠层堆放时,外径为500~600mm的桩不宜超过4层,外径为300~400mm的桩不宜超过5层。如图2-38所示。运到打桩位置堆放时,应布置在打桩架附设的起重钩工作半径范围内,并考虑到起吊方向,避免转向。

图2-38 预应力管桩的堆放
2.混凝土预制桩的接桩

2-8 方桩接桩
当施工设备条件对桩的限制长度小于桩的设计长度时,需要用多节桩组成设计桩长。接头的构造分为焊接(见图2-39)、法兰连接或机械快速连接(螺纹式、啮合类)三类形式。这里主要介绍焊接法接桩操作及其质量要求。

图2-39 焊接法
采用焊接接桩除应符合现行行业标准《建筑钢结构焊接技术规程》的有关规定外,尚应符合下列规定:
(1)下节桩端的桩头宜高出地面0.5m。
(2)下节桩的桩头处宜设导向箍。接桩时上下节桩段应保持顺直,错位偏差不宜大于2mm。接桩就位纠偏时,不得采用大锤横向敲打。
(3)桩对接前,上下端板表面应使用铁刷子将其清刷干净,坡口处应刷至露出金属光泽。
(4)焊接宜在桩四周对称地进行,待上下桩节固定后拆除导向箍再分层施焊;焊接层数不得少于2层,第一层焊完后必须把焊渣清理干净,方可进行第二层(的)施焊,焊缝应连续、饱满。
(5)焊好后的桩接头应自然冷却后方可继续锤击,自然冷却时间不宜少于8min;严禁采用水冷却或焊好即施打。
(6)雨天焊接时,应采取可靠的防雨措施。
(7)焊接接头的质量检查,对于同一工程探伤抽样检验不得少于3个接头。
3.打桩顺序
打桩顺序根据桩的尺寸、密集程度、深度,桩移动方便程序以及施工现场实际情况等因素来确定,一般分为逐排打设、自中部向边缘打设、分段打设等,如图2-40所示。

图2-40 打桩顺序
确定打桩顺序应遵循以下原则:
(1)桩基的设计标高不同时,打桩顺序宜先深后浅。
(2)不同规格的桩,宜先大后小。
(3)当一侧毗邻建筑物时,由毗邻建筑物处向另一方向施打。
(4)在桩距大于或等于4倍桩径时,则不用考虑打桩顺序,只需从提高效率出发确定打桩顺序,选择倒行和拐弯次数最少的顺序。
(5)应避免自外向内,或从周边向中央进行,以免中间土体被挤密,桩难以打入,或虽勉强打入,但使邻桩侧移或上冒。

2-9 桩过密打桩顺序不当而产生较强烈的挤土效应
4.施工前准备
(1)整平场地,场内铺设100mm砾石土压实;清除桩基范围内的高空、地面、地下障碍物;架空高压线距打桩架不得小于10m;修设桩机进出、行走道路,做好排水措施。
(2)按图纸布置进行测量放线,定出桩基轴线。先定出中心,再引出两侧,并将桩的准确位置测设到地面,每一个桩位打一个小木桩;并测出每个桩位的实际标高,场地外设2~3个水准点,以便随时检查。
(3)检查桩的质量,将需用的桩按平面布置图堆放在打桩机附近,不合格的桩不能运至打桩现场。
(4)检查打桩机设备及起重工具;铺设水电管网,进行设备架立组装和试打桩,试打桩不少于两根。在桩架上设置标尺或在桩的侧面画上标尺,以便能观测桩身入土深度。
(5)打桩场地建(构)筑物有防震要求时,应采取必要的防护措施。
(6)学习、熟悉桩基施工图纸,并进行会审;做好技术交底,特别是地质情况、设计要求、操作规程和安全措施的交底。
(7)准备好桩基工程沉桩记录和隐蔽工程验收记录表格,并安排好记录、通知业主、监理人员等。
5.锤击沉桩施工
锤击沉桩是利用桩锤下落时的瞬时冲击机械能,克服土体对桩的阻力,使其静力平衡状态遭到破坏,导致桩体下沉,达到新的静压平衡状态,如此反复地锤击桩头,桩身也就不断地下沉。锤击沉桩是预制桩最常用的沉桩方法。该法施工速度快,机械化程度高,适应范围广,现场文明程度高,但施工时有挤土、噪声和振动等公害,不宜在医院、学校、居民区等城镇人口密集地区施工,在城市中心和夜间施工应对其有所限制。锤击沉桩设备如图2-41所示。

图2-41 锤击沉桩设备及现场施工(单位:mm)
(1)锤击沉桩施工工艺流程(见图2-42):

图2-42 锤击沉桩施工工艺流程
测量定位→桩机就位→桩底就位、对中和调直→锤击沉桩→接桩、对中、垂直度校核→再锤击→送桩→收锤。
①测量定位。通过轴线控制点,逐个定出桩位,打设钢筋标桩,并用白灰在标桩附近地面上画一个圆心与标桩重合、直径与管桩相等的圆圈,以方便插桩对中,保持桩位正确。桩位的放样允许偏差是:群桩20mm;单排桩10mm。

2-10 预制桩锤击沉桩
②桩底就位、对中和调直。底桩就位前,应在桩身上划出单位长度标记,以便观察桩的入土深度及记录每米沉桩击数。吊桩就位一般用单点吊将管桩吊直,使桩尖插在白灰圈内,桩头部插入锤下面的桩帽套内就位,并对中和调直,使桩身、桩帽和桩锤三者的中心线重合,保持桩身垂直,其垂直度偏差不得大于0.5%。桩垂直度观测包括打桩架导杆的垂直度,可用两台经纬仪在离打桩架15m以外成正交方向进行观测,也可在正交方向上设置两根吊砣垂线进行观测校正。
③锤击沉桩。锤击沉桩宜采取低锤轻击或重锤低打,以有效降低锤击应力,同时特别注意保持底桩垂直,在锤击沉桩的全过程中都应使桩锤、桩帽和桩身的中心线重合,防止桩受到偏心锤打,以免桩受弯受扭。在较厚的黏土、粉质黏土层中施打多节管桩时,每根桩宜连续施打,一次完成,以免间歇时间过长,造成再次打入困难,而需增加锤击数,甚至打不下而先将桩头打坏等情况。当遇到贯入度剧变,桩身突然发生倾斜、移位或有严重回弹,桩顶或桩身出现严重裂缝、破碎等情况时,应暂停打桩,并分析原因,采取相应措施。
④接桩、对中、垂直度校核。方桩接头数不宜超过2个,预应力管桩单桩的接头数不宜超过4个,应避免桩尖接近硬持力层或桩尖处于硬持力层时接桩。预应力管桩接一般多采用电焊接头。具体施工要点为:在下节桩离地面0.5~1.0m时,在下节桩的接头处设导向箍以方便上节桩就位,起吊上节桩插入导向箍,进行上下节桩对中和垂直度校核,上下节桩轴线偏差不宜大于2mm;上下端板表面应用铁刷子清刷干净,坡口处应刷至露出金属光泽。焊接时宜先在坡口圆周上对称焊4~6点,待上下桩节固定后拆除导向箍,由两名焊工对称、分层、均匀、连续的施焊,一般焊接层数不少于2层,待焊缝自然冷却8~10min后,方可继续锤击沉桩。
接桩质量检查:焊缝质量、电焊结束后的停歇时间(>1min)、下节平面偏差(10mm)、节点弯矩矢高(<L/1000)。
⑤送桩。当桩顶标高低于自然地面标高时,须用钢制送桩管(长为4~6m)放于桩头,锤击送桩管将桩送入土中。设计送桩器的原则是:打入阻力不能太大,容易拔出,能将冲击力有效地传到桩上,并能重复使用。送桩后遗留的桩孔应及时回填或覆盖。
⑥截桩。露出地面或未能送至设计桩顶标高的桩,必须截桩。截桩要求用截桩器,严禁用大锤横向敲击、冲撞。
(2)锤击沉桩收锤标准
当桩尖(靴)被打入设计持力层一定深度,符合设计确定的停锤条件时,即可收锤停打,终止锤击的控制条件,称为收锤标准。收锤标准通常以达到的桩端持力层、最后贯入度或最后1m沉桩击数为主要控制指标。桩端持力层作为定性控制;最后贯入度或最后1m沉桩锤击数作为定量控制,均通过试桩或设计确定。一般停止锤击的控制原则是:桩端(指桩的全截面)位于一般土层时,以控制桩端设计标高为主,贯入度可作参考;桩端达到坚硬、硬塑的黏性土、中密以上粉土、砂土、碎石类土、风化岩时,以贯入度控制为主,桩端标高可作参考。当贯入度已达到而桩端标高未达到时,应继续锤击3阵,按每阵10击且贯入度不大于设计规定的数值加以确认,必要时施工控制贯入度应通过试验与有关单位会商确定。
6.静力压桩施工
静力压桩是通过静力压桩机的压桩机构,以压桩机自重和桩机的配重作反力而将预制钢筋混凝土桩分节压入地基土层中成桩。其特点是:桩机全部采用液压装置驱动,压力大,自动化程度高,纵横移动方便,运转灵活;桩定位精确,不易产生偏心,可提高桩基施工质量;施工无噪声、无振动、无污染;沉桩采用全液压夹持桩身向下施加压力,可避免锤击应力打碎桩头,桩截面可以减小,混凝土强度等级可降低1~2级,配筋比锤击法可省40%;效率高,施工速度快,压桩速度每分钟可达2m,正常情况下每台班可完成15根,比锤击法可缩短工期1/3;压桩力能自动记录,可预估和验证单桩承载力,施工安全可靠,便于拆装维修、运输等。但存在压桩设备较笨重,要求边桩中心到已有建筑物间距较大,压桩力受一定限制,挤土效应仍然存在等,问题。如图2-43所示。

1—长船行走机构;2—短船行走及回转机构;3—支腿式底盘结构;4—液压起重机;5—夹持与压板装置;6—配重铁块;7—导向架;8—液压系统;9—电控系统;10—操纵室;11—已压入下节桩;12—吊入上节桩
图2-43 全液压式静力压桩机压桩
静力压桩适用于软土、填土及一般黏性土层,特别适合于居民稠密及危房附近环境保护要求严格的地区沉桩;但不宜用于地下有较多孤石、障碍物或有4m以上硬隔离层的情况。如图2-44所示。

图2-44 静力压桩现场施工
(1)静压法沉桩机理
静压预制桩主要应用于软土、一般黏性土地基。在桩压入过程中,系以桩机本身的重力(包括配重)作为反作用力,以克服压桩过程中的桩侧摩阻力和桩端阻力。当预制桩在竖向静压力作用下沉入土中时,桩周土体发生急速而激烈的挤压,土中孔隙水压力急剧上升,土的抗剪强度大大降低,从而使桩身很快下沉。
(2)静力压桩施工工艺流程

2-11 静力压桩施工工艺
静压预制桩的施工,一般都采取分段压入、逐段接长的方法。其施工程序为:测量定位→压桩机就位→吊桩、插桩→桩身对中调直→静压沉桩→接桩→再静压沉桩→送桩→终止压桩→切割桩头。如图2-45所示。

1—第一段桩;2—第二段桩;3—第三段桩;4—送桩;5—桩接头处;6—地面线;7—压桩架操作平台
图2-45 静力压桩施工工艺流程
静力压柱施工要点如下:
①桩机就位。压桩时,桩机就位是利用行走装置完成的,它是由横向行走(短船行走)和回转机构组成。把船体当作铺设的轨道,通过横向和纵向油缸的伸程和回程使桩机实现步履式的横向和纵向行走。当横向两油缸一只伸程,另一只回程,可使桩机实现小角度回转,这样可使桩机到达要求的位置。
②吊桩、插桩和压桩。静压预制桩每节长度一般在12m以内,插桩时先用起重机吊运或用汽车运至桩机附近,再利用桩机上自身设置的工作吊机将预制混凝土桩吊入夹持器中,夹持油缸将桩从侧面夹紧,即可开动压桩油缸,先将桩压入土中1m左右后停止,调正桩在两个方向的垂直度后,压桩油缸继续伸程把桩压入土中,伸长完后,夹持油缸回程松夹,压桩油缸回程,重复上述动作可实现连续压桩操作,直至把桩压入预定深度土层中。在压桩过程中要认真记录桩入土深度和压力表读数的关系,以判断桩的质量及承载力。当压力表读数突然上升或下降时,要停机对照地质资料进行分析,判断是否遇到障碍物或产生断桩现象等。
(3)压桩终止条件
压桩终止条件按设计桩长和终压力进行控制。
①对于摩擦桩,按照设计桩长进行控制,但在施工前应先按设计桩长试压几根桩,待停置24h后,用与桩的设计极限承载力相等的终压力进行复压,如果桩在复压时几乎不动,即可以此进行控制。
②对于端承摩擦桩或摩擦端承桩,按终压力值进行控制:
a.对于桩长大于21m的端承摩擦桩,终压力值一般取桩的设计极限承载力。当桩周土为黏性土且灵敏度较高时,终压力可按设计极限承载力的0.8~0.9取值。
b.当桩长小于等于21m且大于14m时,终压力按设计极限承载力的1.1~1.4倍取值;或桩的设计极限承载力取终压力值的0.7~0.9。
c.当桩长小于等于14m时,终压力按设计极限承载力的1.4~1.6倍取值;或设计极限承载力取终压力值的0.6~0.7,其中对于小于8m的超短桩,按0.6取值。
③超载压桩时,一般不宜采用满载连续复压法,但在必要时可以进行复压,复压的次数不宜超过2次,且每次稳压时间不宜超过10s。
7.质量控制
(1)桩位的放样允许偏差如下:群桩20mm;单排桩10mm。
(2)打(压)入桩的桩位偏差,必须符合表2-7的规定。斜桩倾斜度的偏差不得大于倾斜角正切值的15%(倾斜角系桩的纵向中心线与铅垂线间夹角)。
表2-7 预制桩桩位的允许偏差

注:H为施工现场地面标高与桩顶设计标高的距离。
(3)施工中应对桩体垂直度、沉桩情况、桩顶完整状况、接桩质量等进行检查,对电焊接桩、重要工程应做10%的焊缝探伤检查。
(4)施工结束后,应对承载力及桩体质量做检验。
2.3.3 混凝土灌注桩施工
混凝土灌注桩是直接在施工现场桩位上成孔,然后在孔内安装钢筋笼,浇筑混凝土成桩。与预制桩相比,灌注桩具有不受地层变化限制,不需要接桩和截桩,节约钢材、振动小、噪声小等特点,但施工工艺复杂,施工速度较慢,影响质量的因素多。灌注桩按成孔方法分为:泥浆护壁钻孔灌注桩、沉管灌注桩、人工挖孔灌注桩、爆扩成孔灌注桩等。本节主要介绍前面三种。
1.泥浆护壁钻孔灌注桩
泥浆护壁钻孔灌注桩是通过桩机在泥浆护壁条件下慢速钻进,将钻渣利用泥浆带出,并保护孔壁不致坍塌,成孔后再使用水下混凝土浇筑的方法将泥浆置换出来而成的桩。它是国内最常用的成桩方式。其特点是:可用于各种地质条件,各种大小孔径(300~2000mm)和深度(40~100m),护壁效果好,成孔质量可靠;施工无噪声、无振动、无挤压;机具设备简单,操作方便,费用较低;但成孔速度慢,效率低,用水量大,泥浆排放量大,污染环境,扩孔率较难控制。该成桩方法适用于地下水位较高的软、硬土层,如淤泥、黏性土、砂土、软质岩等土层。如图2-46所示。

图2-46 泥浆护壁钻孔灌注桩现场施工
(1)泥浆的功能、制备和试验
①泥浆的功能:
a.防止孔壁坍塌。泥浆在桩孔内吸附在孔壁上,将土壁上的孔隙填补密实,避免孔内壁漏水,保证护筒内水压的稳定;泥浆比重大,可加大孔内水压力,可以稳固土壁、防止塌孔。
b.排出土渣。泥浆有一定的黏度,通过循环泥浆可使切削碎的泥石渣屑悬浮起来后被排走,起到携砂、排土的作用。
c.冷却、润滑施工机械。
②泥浆的制备:除能自行造浆的黏性土层外,其他土层均应制备泥浆。泥浆制备应选用高塑性黏土或膨胀土。泥浆应根据施工机械、工艺及穿越土层情况进行配合比设计。施工期间护筒内的泥浆面应高出地下水位1.0m以上,在受水位涨落影响时,泥浆面应高出最高水位1.5m以上;在清孔过程中,应不断置换泥浆,直至灌注水下混凝土。
③泥浆试验:在灌注桩工程中所使用的泥浆,必须经常保持地层和施工条件等所要求的性质。为此施工中,不仅在制备泥浆时,在施工的各个阶段都必须测定泥浆的性质并进行质量管理。灌注混凝土前,应对泥浆相对密度、含砂率、黏度等进行测定。孔底500mm以内的泥浆比重应小于1.25,含砂率不得大于8%,黏度不得大于28s。

2-12 正循环泥浆护壁桩
(2)正反循环回转钻机

2-13 反循环泥浆护壁桩
正循环回转钻机成孔的工艺原理是由空心钻杆内部通入泥浆或高压水,从钻杆底部喷出,携带钻下的土渣沿孔壁向上流动,将土渣从孔口带出流入泥浆池。正循环具有设备简单、操作方便、费用较低等优点,适用于小直径孔(不宜大于1000mm),钻孔深度一般以40m为限,但其排渣能力较弱。反循环回转钻机成孔的工艺为泥浆或清水由钻杆与孔壁间的环状间隙流入钻孔,然后由吸泥泵等在钻杆内形成真空,使之携带钻下的土渣由钻杆内腔返回地面而流向泥浆池。反循环工艺的泥浆上流的速度较高,能携带较大的土渣。反循环成孔是目前大直径桩成孔中的一种有效施工方法,适用于打直径孔和孔深大于30m的端承桩。如图2-47所示。

1—钻杆;2—送水管;3—主机;4—钻头;5—沉淀池;6—潜水泥浆泵;7—泥浆池;8—砂石泵;9—抽渣管;10—排渣胶管
图2-47 正反循环排渣方法
(3)试桩

2-14钻孔灌注桩施工工艺
在设计桩位进行试桩(根据设计而定),通过试桩验证钻孔工艺是否适应水文及工程地质条件。试桩时详细记录地层地质,水位标高、塌孔位置、钻孔进尺速度及成孔时间、泥浆用量及泥浆性能指标等,作为正式施工参数,必要时调整施工方案。
(4)施工工艺流程
泥浆护壁钻孔灌注桩施工工艺流程:放线定位→埋设护筒→钻机就位→钻孔→第一次清孔→吊放钢筋笼→下导管→第二次清孔→灌注混凝土。如图2-48所示。

图2-48 泥浆护壁钻孔灌注桩施工工艺流程
①放线定位。要由专业的测量人员根据给定的控制点用“双控法”测量桩位,并用标桩标定准确。
②埋设护筒。其主要作用是保证钻机沿着垂直方向顺利工作,同时还起着存储泥浆,使其高出地下水位和保护桩顶部分土层不致因钻杆反复上下升降、机身振动而导致塌孔。如图2-49所示。

图2-49 护筒
a.护筒埋设应准确、稳定,护筒中心与桩位中心的偏差不得大于50mm。
b.护筒一般用4~8mm钢板制作,其内径应大于钻头直径100mm。其上部宜开设1~2个溢浆孔。
c.护筒的埋设深度:在黏性土中不宜小于1.0m,砂土中不宜小于1.5m,其高度尚应满足孔内泥浆面高度的要求,一般高出地面或水面400~600mm。
d.受水位涨落影响或水下施工的钻孔灌注桩,护筒应加高加深,必要时应打入不透水层。
③钻机就位。就位前,先平整场地,铺好枕木并用水平尺校正,保证钻机平稳、牢固;使钻头中心对准桩位中心,最大偏差不大于10mm,用水平仪检查钻机底座平整度,用多功能垂直度校正器或线垂检查钻塔及钻杆垂直度,机架、钻杆垂直度偏差均不大于0.5%。
④钻孔。
a.钻孔作业应分班连续进行,认真填写钻孔施工记录,交接班时应交代钻进情况及下一班注意事项。应经常对钻孔泥浆进行检测和试验,应经常注意土层变化,在土层变化处均应捞取渣样,判明后记入记录表中与地址剖面图核对。
b.开钻时,在护筒下的一定范围内应慢速钻进,待导向部位或钻头全部进入土层后,方可加速钻进,钻进速度应根据土质情况、孔径、孔深和供水、供浆量的大小确定,一般控制在5m/min左右,在淤泥和淤泥质黏土中不宜大于1m/min,在较硬的土层中以钻机无跳动、电机不超荷为准。在钻孔、排渣或因故障停钻时,应始终保持孔内具有规定的水位和满足相对密度和黏度满足要求的泥浆。
c.钻头到达持力层时,钻速会突然减慢,这时应对浮渣进行取样,并通过与地质报告作比较予以判定,原则上应由地勘单位派出有经验的技术人员进行鉴定,判定钻头是否达到设计持力层深度;用测绳测定孔深做进一步判断。经判定满足设计规范要求后,可同意施工收钻提升钻头。
⑤清孔。清孔分两次进行。
a.第一次清孔。钻孔深度达到设计要求,对孔深、孔径、空的垂直度等进行检查,符合要求后进行第一次清孔。第一次清孔的目的是使孔底沉碴(虚土)厚度、循环液中的钻碴含量和孔壁泥皮厚度符合质量要求,也为下一工序在泥浆中灌注混凝土创造良好条件。当钻孔达到设计深度后应停止钻进,此时稍提钻杆,使钻斗距孔底10~20cm处空转,并保持泥浆正循环,将相对密度为1.05~1.10g/cm3的不含杂质的新浆压入钻杆,把钻孔内悬浮较多钻碴的泥浆臵换出孔外。第一次清孔应达到以下要求:
(a)距孔底500mm以内的泥浆相对密度应小于1.25;
(b)含砂率≤8%,黏度≤28s;
(c)孔底沉碴厚度≤100mm。
b.第二次清孔。在第一次清孔达到要求后,由于要安放钢筋笼及导管准备浇注水下混凝土,这段时间间隔较长,孔底难免会产生新的沉碴,所以待安放钢筋笼及插入导管后,再利用导管进行第二次清孔。清孔方法是在导管顶部安设一个弯头和皮笼,用泵将泥浆压入导管内,再从孔底沿着导管外置换沉渣。第二次清孔后的沉渣厚度和泥浆性能指标应满足设计要求,一般应满足下列要求:
(a)摩擦桩沉渣厚度不大于150mm,端承桩沉渣厚度不大于50mm。沉渣厚度的测定可直接用沉砂测定仪,但在施工现场中多用测绳。将测绳徐徐下入孔中,一旦感觉锤质变轻时,在这一深度范围内,上下试触几次,确定沉渣面的位置,继续放测绳,一旦感觉锤质量减轻了很多或测绳完全松弛时,说明其深度已到孔底,这样重复测试3次以上,孔深取其中的较小值,孔深与沉渣面之差即为沉渣厚度。
(b)在浇筑混凝土前,孔底500mm以内的泥浆密度应控制在1.15~1.20g/cm3。
c.不论采用何种清孔方法,在清孔排渣时,必须注意保持孔内水头,防止塌孔。不应采取加深钻孔深度的方法代替清孔。
⑥灌注混凝土。清孔合格后应及时浇筑混凝土,浇筑方法采用导管进行水下浇筑,对泥浆进行置换。如图2-50所示。

图2-50 水下浇筑法工艺流程
a.导管埋设。导管直径宜为200~250mm,壁厚不小于3mm,分节长度视工艺要求而定。导管埋入混凝土中的深度越大,则混凝土扩散越均匀,密实性越好,其表面也较平坦;反之,混凝土扩散不均匀,表面坡度也大,易于分散离析,影响质量。埋入深度与混凝土浇注速度有关。为防止导管拔出混凝土面造成断桩事故,导管埋设宜为2~6m,同时也要防止埋深造成埋管事故。
b.灌注首批混凝土。为使隔水栓能顺利排出,导管底部至孔底的距离宜为300~500mm。漏斗与储料斗应有足够的混凝土储备量,使导管一次埋入混凝土以下0.8m以上。
c.连续灌注混凝土。首批混凝土灌注正常后,必须连续施工,不得中断,否则先灌注的混凝土达到初凝,将阻止后灌混凝土从导管中流出,造成断桩。
d.控制灌注时间。每根桩的灌注时间按初盘混凝土的初凝时间控制,必要时可适量掺入缓凝剂。本抗拔桩长12~15m,混凝土灌注量10~13m3,灌注时间宜为1~2h。
e.控制桩顶标高。当灌注混凝土接近桩顶部位时,应控制最后一次灌注量,使桩顶的灌注标高比设计标高高出0.5~0.8m,以使凿除桩顶部的泛浆层后达到设计标高的要求,且必须保证暴露的桩顶混凝土达到强度设计值。
(5)钻孔灌注桩施工记录
钻孔灌注桩施工记录一般包括:测量定位(桩位、钢筋笼、护筒安置)记录、钻孔记录、成孔测量记录、泥浆相对密度测定记录、坍落度测定记录、沉渣厚度测定记录、钢筋笼制定安装检查表、混凝土浇捣记录、导管长度记录等。
2.沉管灌注桩
沉管灌注桩是土木建筑工程中众多类型桩基础中的一种,它是采用与桩的设计尺寸相适应的钢管(即套管),在端部套上桩尖后沉入土中后,在套管内吊放钢筋骨架,然后边浇注混凝土边振动或锤击拔管,利用拔管时的振动捣实混凝土而形成所需要的灌注桩。这种施工方法适用于在有地下水、流砂、淤泥的情况。
根据沉管方法和拔管时振动不同,套管成孔灌注桩可分为锤击沉管灌注桩和振动沉管灌注桩。前者多用于一般黏性土、淤泥质土、砂土和人工填土地基,后者除以上范围外,还可用于稍密及中密的碎石土地基。本节主要介绍锤击沉管灌注桩的施工工艺。
(1)锤击沉管灌注桩的施工工艺

2-15 锤击沉管灌注桩
锤击沉管灌注桩施工应根据土质情况和荷载要求,分别选用单打法、复打法或反插法。
①单打法(又称一次拔管法)。一次将沉管沉入设计标高,然后插钢筋笼,灌注砼,拔管时,每提升0.5~1.0m,振动5~10s,然后再拔管0.5~1.0m,如此反复至全部拔出。

2-16 单打锤击桩
②复打法。一次将管沉入设计标高,插钢筋笼,灌注砼,上拔沉管到地面后,二次将沉管下沉到设计标高,或局部进行二次下沉,然后补灌砼,后提升,振动,反复至全部拔出;施工时,应保证前后两次沉管轴线重合。

2-17 复打桩
③反插法。一次将沉管沉入设计标高,插钢筋笼,灌注砼,钢管每提升0.5m,再下插0.3m,这样反复进行,直至拔出。

2-18 反插法桩
工艺流程:放线定位→桩机就位→锤击沉管→灌注混凝土→边拔管、边锤击、边灌注混凝土→下放钢筋笼→继续浇筑混凝土→成桩。如图2-51所示。

图2-51 锤击沉管灌注桩施工工艺
①桩机就位。
桩机就位时,应垂直平稳架设在沉桩部位,桩锤应对准工程桩位,同时在桩架或套管上标出控制深度标记,以便在施工中进行套管深度观测。成桩施工顺序一般从中间开始,向两边或四周进行,对于群桩基础或桩的中心距小于或等于3.5d(d为桩的直径)时,应间隔施打,中间空出的桩,须待邻桩混凝土达到设计强度的50%后,方可施打。群桩基础的基桩施工,应根据土质、布桩情况,采取消减负面挤土效应的技术措施,确保成桩质量。
当桩尖对准桩基中心,并核查调整套管垂直度后,利用捶击及套管自重将桩尖压入土中。用预制混凝土桩尖时,应先在桩基中心预埋好桩尖,在套管下端与桩尖接触处垫好缓冲材料。桩机就位后,吊起套管,对准桩尖,使套管、桩尖、桩锤在一条垂直线上,利用锤重及套管自重将桩尖压入土中。
②锤击沉管。
开始沉管时应轻击慢振。锤击沉管时,可用收紧钢绳加压或加配重的方法提高沉管速度。当水或泥浆有可能进入桩管时,应事先在管内灌入1.5m左右的封顶混凝土。
应按设计要求和试桩情况,严格控制沉管最后灌入度。锤击沉管应测量最后二阵十击灌入度;振动沉管应测量最后两个2min灌入度。在沉管过程中,如出现套管快速下降或沉管不下去的情况,应及时分析原因,进行处理。如快速下沉是因桩尖穿过硬土层进入软土层引起的,则应继续沉管作业。如沉不下去是因桩尖顶住孤石或遇到硬土层引起的,则应放慢速度(轻锤低击或慢振),待越过障碍后再正常沉管。如仍沉不下去或沉管过深,最后贯入度不能满足设计要求,则应核对地质资料,会同建设单位研究处理。
③吊放钢筋笼。
钢筋笼的吊放,对通长的钢筋笼在成孔完成后埋设,短钢筋笼可在混凝土灌至设计标高时再埋设,埋设钢筋笼时要对准管孔,垂直缓慢下降。在混凝土桩顶采取构造连接插筋时,必须沿周围对称均匀垂直插入。
④浇筑混凝土。
每次向套管内灌注混凝土时,如用长套管成孔短桩,则一次灌足,如成孔桩,则第一次应尽量灌满。混凝土坍落度宜为6~8cm,配筋混凝土坍落度宜为8~10cm。
灌注时充盈系数(实际灌注混凝土量理论计算之比)应不小于1。一般土质为1.1;软土为1.2~1.3。在施工中可根据不同土质的充盈系数,计算出单桩混凝土需用量,折合成料斗浇灌次数,以核对混凝土实际灌注量。当充盈系数小于1时,应采用全桩复打;对于断桩及缩颈桩可局部复打,即复打超过断桩或缩颈桩1m以上。
桩顶混凝土一般宜高出设计标高200mm左右,待以后施工承台时再凿除。如设计有规定,应按设计要求施工。
⑤拔管。
每次拔管高度应以能容纳吊斗一次所灌注混凝土为限,并边拔边灌。在任何情况下,套管内应保持不少于2m高的混凝土并按沉管方法不同分别采取不同的方法拔管。在拔管过程中,应有专人用测锤或浮标检查管内混凝土下降情况,一次不应拔得过高。
锤击沉管拔管方法:套管内灌注混凝土后,拔管速度应均匀,对一般土层不宜大于1m/min;对软弱土层及软硬土层交界处不宜大于0.8m/min。采用倒打拔管的打击次数,单动汽锤不得少于70次/min;自由落锤轻击(小落距锤击)不得少于50次/min。在管底未拔到桩顶设计标高之前,倒打或轻击不得四断。
(2)沉管灌注桩常见质量问题及处理方法
①断桩。

2-19 沉管灌注桩施工工艺
a.产生原因:在饱和的流塑状淤泥土中施工时,当拔管速度过快,混凝土还未流出管外,周围土即落入桩身,形成断桩;常发生于地面以下1~3m深处的软硬土层交界处,当桩身混凝土终凝不久后受到邻桩的振动和外力等,自身强度低,受剪力而被剪断;桩距过小,邻桩施工时产生很大的挤推力。
b.处理方法:在布桩时,应避免桩的密度过大,振动灌注桩的间距不应大于4倍桩径,当桩距小于3.5倍桩径时,采用控制时间间隔方法,相邻桩施工时,其间隔时间不得超过混凝土初凝时间,否则,采用跳打法,使邻桩混凝土达到设计强度等级的50%后,再施打中间桩,以减少对邻桩的影响。控制拔管速度,在一般土层中,拔管速度宜控制在1.2~1.5m/min,在软弱土层中,宜控制在0.6~0.8m/min。要制定好打桩顺序及桩架行走路线时,应尽量避免设备碾压桩身及对新桩的振动和外力干扰。
②缩颈。
a.产生原因:在软弱土层中,当含水量大且透水性差时,由于土体受到强烈的扰动和挤压,产生很大的孔隙水压力,拔管后挤向新灌混凝土,产生缩颈现象;拔管速度过快,混凝土来不及下落,被周围土体填充,导致缩颈现象;管内混凝土存量少、和易性差、出管扩散性差。
b.处理方法:要保证灌注时管内混凝土的高度,每次应尽量多灌,第一次拔管高度应控制在能容纳第二次所需贯入的混凝土量为限。如拔得过高,就容易导致混凝土量过少而产生缩颈。要严格控制混凝土的灌入量,对于缩颈桩可采用局部复打,复打深度必须超过缩颈区1m以上。要控制拔管速度,对一般土层宜控制在1m/min,对软弱土层及软硬土层交界处宜控制在0.3~0.8m/min,并且在拔管过程中对桩管进行连续的低锤密击,使钢管不断振动,从而振实混凝土。
③吊脚桩。

2-20 吊脚桩
a.产生原因:混凝土预制桩尖质量差,边沿被破坏,桩尖挤入桩管内,拔管时冲击振动不够,桩尖未被挤出,直到桩管拔至一定高度下落,卡在硬土层中,未落到底,导致桩底的混凝土脱空,形成吊脚桩;混凝土桩尖强度不够,在沉管过程中被打碎,和泥沙一起进入桩管内,与桩管内的混凝土的混合而形成松软土,从而形成吊脚桩;桩间距较小不符合规范要求,桩尖挤土效应显著,形成吊脚桩,严重影响桩的承载力。
b.处理方法:严格控制预制混凝土桩尖的强度,强度等级应不低于C30;应根据层间土的性质、持力层土的性质等情况合理布桩,避免过小的桩距和过大的布桩平面系数,确定正确的打桩顺序和打桩速率;沉管时,应随时用吊砣检查桩尖是否缩入管内,若有缩入管内现象,则应及时拔出桩管纠正处理;或拔出桩管,填砂重打;若桩尖被打碎,导致桩管涌入泥浆,可采用密振慢拔的方法,开始拔管时,可先反插几次,再正常拔管。
④隔层。
a.产生原因:钢管套的管径较小,混凝土粗骨料粒径过大、和易性差,且拔管速度过快。
b.处理方法:施工时应严格控制混凝土的配合比,保证混凝土的坍落度不小于50~70mm;骨料粒径不大于30mm;拔管速度在淤泥中不大于0.8m/min,拔管时边拔边振,每拔0.5~1.0m,停拔振动5~10s。
⑤拒桩。
a.产生原因:在沉管过程中,地基中积累的孔隙水压力增大,使桩尖不能到达设计深度;地下有坚硬物,使桩尖无法穿透;激振器的电机转速过低,或锤击冲击力过小;地层摩擦阻力过大,沉管困难。
b.处理方法:控制打桩速度,采用跳打方式;当桩尖无法穿透地下坚硬物时,可拔出桩管,采用人工挖孔方法;可以将电机转速调高,或更换重锤,加大冲程。
3.人工挖孔灌注桩
人工挖孔灌注桩,是指用人力挖土、现场浇筑的钢筋混凝土桩。人工挖孔桩一般直径较粗,最细的也在800mm以上,能够承载楼层较少且压力较大的结构主体,目前应用比较普遍。桩的上面设置承台,再用承台梁拉结、联系起来,使各个桩的受力均匀分布,用以支承整个建筑物。如图2-52和图2-53所示。

图2-52 人工挖孔桩施工

图2-53 人工挖孔桩现场施工
人工挖孔桩施工方便、速度较快、不需要大型机械设备,挖孔桩要比木桩、混凝土打入桩抗震能力强,造价比冲锥冲孔、冲击锥冲孔、冲击钻机冲孔、回旋钻机钻孔、沉井基础节低,因而在公路、民用建筑中得到广泛应用。但挖孔桩井下作业条件差、环境恶劣、劳动强度大,安全和质量显得尤为重要。场地内打降水井抽水,当确因施工需要采取小范围抽水时,应注意对周围地层及建筑物进行观察,发现异常情况应及时通知有关单位进行处理。
人工挖孔桩宜用于地下水位以上的黏性土、粉土、填土、中等密实以上的沙土、分化岩层,也可在黄土、膨胀土和冻土中使用,适应性较强。在地下水位较高,有承压水的砂土层、滞水层,厚度较大的流塑状淤泥、淤泥质土层中不得选用人工挖孔灌注桩。人工挖孔桩的孔径不得小于800mm,且不得大于2500mm;孔深不得大于30m。当桩净距小于2.5m时,应采用间隔开挖。相邻排桩跳挖的最小施工净距不得小于4.5m。

2-21 人工挖孔桩施工工艺
(1)人工挖孔桩施工工艺流程
人工挖孔桩的施工程序:场地平整→放线、定桩位→挖第一节桩孔土方→做第一节护壁→在护壁上二次投测标高及桩位十字轴线→第二节桩身挖土→校核桩孔垂直度和直径→做第二节护壁→重复第二节挖土、支模、浇筑混凝土护壁工序,循环作业直至设计深度→检查持力层后进行扩底→清理虚土,排除积水检查尺寸和持力层→吊放钢筋笼就位→浇筑桩身混凝土。
①挖第一节桩孔土方,做第一节护壁。为防止塌孔和保证操作安全,一般按1m左右分节开挖分节支护,循环进行。施工人员在保护圈内用常规挖土工具(短柄铁锹、镐、锤、钎)进行挖土。将土运出孔的提升机具主要有人工绞架、卷扬机或电动葫芦。每节土方应挖成圆台形状,下部至少比上部宽一个护壁厚度,以利护壁施工和受力,如图2-54所示。护壁一般采用C20或C25混凝土,用木模板或钢模板支设,土质较差时加配适量钢筋,土质较好时也可采用红砖护壁,厚度为1/4、1/2和1砖厚。第一节护壁一般要高出自然地面200~300mm,且高出部分的厚度不小于300mm,以防止地面杂草掉入孔中。同时把十字轴线引测到护壁表面,把标高引测到护壁内壁。

图2-54 护壁(单位:mm)
②校核桩孔垂直度和直径。每完成一节施工,均须通过第一节混凝土内壁上设十字控制点并拉十字线,吊线坠用水平尺杆找圆周,保证桩孔垂直度和直径,桩径允许偏差为±50mm,垂直度允许偏差小于0.5%。
③扩底。采取先挖桩身圆柱体,再按扩底尺寸从上到下削土,修成扩底形状。在浇筑混凝土之前,应先清理孔底虚土、排除积水,经甲方及监理人员检查好后迅速进行封底。
④吊放钢筋笼就位。钢筋笼宜分节制作,连接方式一般采用单面搭接焊;钢筋笼主筋混凝土保护层厚度不宜小于70mm,一般在钢筋笼四侧主筋上每隔5m设置耳环或直接制作混凝土保护层垫块来控制其厚度;吊放钢筋笼入孔时,不得碰撞孔壁,防止钢筋笼变形,注意控制上部第一个箍筋的设计标高并保证主筋锚固长度。
⑤浇筑桩身混凝土。因桩深度一般超过混凝土自由下落高度2m,所以混凝土下料采用串筒、溜管等措施;如地下水大(孔中水位上升速度大于6mm/min),应采用混凝土导管水中浇筑混凝土工艺,混凝土要垂直灌入桩孔内,并应连续分层浇筑,每层厚不超过1.5m。小直径桩孔,6m以下利用混凝土的大坍落度和下冲力使其密实;6m以内分层捣实。大直径桩应分层捣实,或用卷扬机吊导管上下插捣。对直径小、深度大的桩,人工下井振捣有困难时,可在混凝土中掺水泥用量0.25%的木钙减水剂,使混凝土坍落度增至130~180mm,利用混凝土的大坍落度和下沉力使之密实,但桩上部钢筋部位仍应用振捣器振捣密实。
⑥地下水及流砂处理。桩挖孔时,如地下水丰富、渗水或涌水量较大时,可根据情况分别采取以下措施:a.少量渗水,可在桩孔内挖小集水坑,随挖土随用吊桶,将泥水一起吊出;b.大量渗水,可在桩孔内先挖较深集水井,设小型潜水泵将地下水排出桩孔外,随挖土随加深集水井;c.涌水量很大时,如桩较密集,可将一桩超前开挖,使附近地下水汇集于此桩孔内,用1~2台潜水泵将地下水抽出,起到深井降水的作用,将附近桩孔地下水位降低;d.渗水量较大,井底地下水难以排干时,底部泥渣可用压缩空气清孔方法清孔;e.当挖孔时遇流砂层,一般可在井孔内设高1~2m、厚4mm钢套护筒,直径略小于混凝土护壁内径,利用混凝土支护作支点,用小型油压千斤顶将钢护筒逐渐压入土中,阻挡流砂,钢套筒可一个接一个下沉,压入一段,开挖一段桩孔,直至穿过流砂层0.5~1.0m,再转入正常挖土和设混凝土支护。浇筑混凝土时,至该段,随浇混凝土随将钢护筒(上设吊环)吊出,也可不吊出。
(2)人工挖孔灌注桩的特殊安全措施
①孔内必须设置应急软爬梯,供人员上下井使用的“电葫芦”、吊笼等应安全可靠并配有自动卡紧保险装置,不得使用麻绳和尼龙绳子吊挂或脚踏井壁凸缘上下。“电葫芦”宜用按钮式开关,使用前必须检查其安全起吊能力。
②每日开工前必须检测井下的有毒有害气体,并应有足够的安全防护措施。
③孔口四周必须设置防护栏杆,并加设0.8m高的围栏围护。
④挖出的土石方应及时运离孔口。不得堆放在孔口四周1m范围内,机动车辆的通行不得对井壁的安全造成影响。
⑤施工现场的一切电源、电路的安装和拆除必须由持证电工操作。电器必须严格接地、接零和使用漏电保护器。各孔用电必分闸,严禁一闸多用,孔上电缆必须架空2m以上,严禁拖地和埋压土中,孔内电缆、电线必须有防磨损、防潮、防断等保护措施。照明应采用安全矿灯或12V以下的安全灯。
⑥井通信联络要畅通,施工时保证井口有人,井下工作人员必须经常检查井下是否存在塌方、涌水、涌泥和流砂迹象,若发现异常情况应停止作业并通知有关单位及时处理。
4.质量控制
(1)成孔深度控制
成孔控制深度应符合下列要求:
①摩擦型桩:摩擦桩以设计桩长控制成孔深度;端承摩擦桩必须保证设计桩长及桩端进入持力层。
②端承型桩:当采用钻(冲),挖掘成孔时,必须保证桩端进入持力层的设计深度;当采用沉管深度控制,以贯入度为主,设计持力层标高对照为辅。
(2)灌注桩质量控制
①灌注桩的桩位偏差必须符合表2-8规定,桩顶标高至少要比设计标高高出0.5m;每灌注50m3混凝土必须有1组试块。对于小于50m3的单柱单桩或每个承台下的桩,至少有1组试块。
表2-8 灌注桩的平面位置和垂直度的允许偏差

注:1.桩径允许偏差的负数值是指个别断面;
2.采用复打、反插法施工的桩径允许偏差不受本表限制;
3.H为施工现场地面标高与桩顶设计标高的距离,D为设计桩径。
②灌注桩的沉渣厚度:对摩擦型桩,不应大于100mm;对端承型桩,不应大于50mm。
③桩的静载荷载试验根数应不少于总桩数的1%,且不少于3根,当总桩数少于50根时,不应少于2根。
④桩身完整性检测的抽检数量:柱下三桩或三桩以下承台抽检桩数不得少于1根;设计等级为甲级,或地质条件复杂,成桩可靠性较差的灌注桩,抽检数量不应少于总桩数的30%,且不少于20根,其他桩基工程的抽检数量不应少于总桩数的20%,且不少于10根。
⑤施工中应对成孔、清渣、放置钢筋笼、灌注混凝土等全过程检查;人工挖孔桩尚应复检孔底持力层土(岩)性。
⑥施工结束后,应检查混凝土强度,并应做桩体质量及承载力检验。
2.3.4 承台施工
承台是桩与柱或墩联系的部分。承台把几根,甚至十几根桩联系在一起形成桩基础。承台分为高桩承台和低桩承台。低桩承台一般埋在土中或部分埋进土中;高桩承台一般露出地面或水面。高桩承台由于具有一段自由长度,其周围无支撑体共同承受水平外力,基桩的受力情况极为不利。桩身内力和位移都比同样水平外力作用下低桩承台要大,其稳定性因而比低桩承台差。高桩承台一般用于港口、码头、海洋工程及桥梁工程。低桩承台一般用于工业与民用房屋建筑物。桩头一般伸入承台0.1m,并有钢筋锚入承台。承台上再建柱或墩,形成完整的传力体系。
1.作业条件
(1)桩基施工已全部完成,并按设计要求挖完土,而且办完桩基施工验收记录。
(2)修整桩顶混凝土:桩顶疏松混凝土全部剔完,如桩顶低于设计标高时,须用同级混凝土接高,在达到桩强度的50%以上,再将埋入承台梁内的桩顶部分剔毛、冲净。如桩顶高于设计标高时,应预先剔凿,使桩顶伸入承台梁深度完全符合设计要求。
(3)桩顶伸入承台梁中的钢筋应符合设计要求,一般不小于30d,钢筋长度不够时,应予以接长。
(4)对于冻胀土地区,必须按设计要求完成承台梁下防冻胀的处理措施。
(5)应将槽底虚土、杂物等垃圾清除干净。
2.钢筋混凝土施工要点
(1)绑扎钢筋前应将灌注桩桩头浮浆部分和预制桩桩顶锤击面破碎部分去除,桩体及其主筋埋入承台的长度应符合设计要求,钢管桩尚应焊好桩顶连接件,并应按设计施作桩头和垫层防水。
(2)承台混凝土应一次浇筑完成,混凝土入槽宜采用平铺法。对大体积混凝土施工,应采取有效措施防止因温度应力引起裂缝。