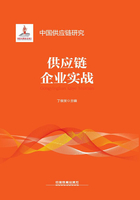
四、供应链管理绩效分析
嘉诚物流创新的“嵌入式全程供应链一体化管理”,将世界先进制造企业的供应链管理理念以及现代化的信息技术应用到全程供应链管理的业务上,对全程供应链上的各个环节(各个企业)都将产生巨大的经济效益,具体分析如下:
1.有效优化物流流程
在嵌入式全程供应链一体化管理模式下,公司与制造企业深度合作的物流流程如图1-7-10所示。公司主要将原材料物流、生产物流、配销物流、逆向物流、流通加工和全球售后服务等六大服务模块融入制造业企业中,以先进物流管理理念作为指导,以物流技术体系作为支撑,以物流金融作为增值手段,并将一体化供应链管理及保税物流作为公司的重点建设对象,切实融合制造供应链体系的生产和流通环节。其中,物流信息技术是支撑基础,因为只有良好的物流信息沟通和交流,才能使物流与制造之间的联动更深入,更加快速和准确地了解市场的需求变化,对市场的需求做出快速的反应,从而帮助制造企业及时调整物流作业,满足制造生产的变化。

图1-7-10 公司发展“嵌入式全程供应链一体化管理”联动的架构图
图1-7-11表示,公司供应链管理推动制造业物流改革实施,不仅将Milk Run,VMI以及JIT/看板等先进管理手段运用到供应链管理中,并且通过与制造企业的密切合作,将物流与原材料采购、制造生产、销售以及售后安装等环节实现无缝衔接。如公司负责对配送半成品的组合加工以及捆包;公司成为制造企业品牌的成品代理;公司实施逆物流,通过客户订单需求的反馈,为制造企业进行生产改革提供建议。这些都为公司在实现制造业供应链管理的全程优化方面提供了良好的运作模式。

图1-7-11 公司实施的制造业供应链管理流程
由此不难发现:优化后的流程实现了公司与制造企业的密切合作。公司为制造企业实现原材料的集中采购、共同配送、零库存管理、逆向物流、保税物流等一体化服务;真正优化了制造企业的生产结构;减少了制造企业产品的多个流通环节;提高了制造企业原有的物流服务质量;为制造企业实现了标准化和专业化的物流运作。因此,“嵌入式的全程供应链一体化管理”能够使得制造企业省心、省力和省钱。
2.有效缩短物流时间
制造企业和公司的联动发展,能有效降低制造企业的物流时间成本,这一优势体现在以下几个方面:
(1)专业化的物流管理,缩短提前期
公司具备先进的VMI、Milk Run、JIT等管理技术,在原材料物流上,可根据客户需求的变化以及制造企业的生产变化,提前告知供应商及时安排相应的原材料供应,或采用VMI的方式即时向供应商提供完整的采购计划为供应商管理库存,从而将生产提前期由4天缩短为1天。另外,还通过全球、全国的Milk Run取货及直拨配送,大大缩短了物流时间。因此,制造企业与公司的合作能够为制造企业大力缩短订购提前期和库存量。
(2)实现信息共享,减少缺货等待的时间
公司根据制造企业客户的需求,自主开发了相应的ERP系统、WMS系统、TMS系统等,整合到公司的信息一体化平台上,有效支撑企业的业务运作,同时,该信息化平台使供应商和生产商实现VMI的信息共享,共有VMI仓库的入库、出库、预测缺料信息。制造企业与公司合作后,缺货等待时间减少了20%,保证了生产的顺利进行。
(3)共同物流作业,缩短物流时间
公司致力于原材料、半成品与产成品的共同物流作业。在原材料物流上执行全球、全国的Milk Run取货及直拨配送;在半成品上执行包括生产线上的加工和产品捆包下线;在产成品上则囊括国内产品和出口产品的下线转运,仓储管理、国内干线及区域配送通过整合代理商的二次物流、三次物流等实现共同仓储、共同配送、共同理货的理念,达到缩短物流时间的目的。
3.有效节约物流成本
(1)订单处理作业成本
联动前,零售商直接下订单给制造企业,制造企业接到订单后,交给相应的订单处理人员进行处理,开始检查库存和准备运输车辆等,但是订单处理人员之间几乎没有沟通,因此信息沟通力度不够。
联动后,制造企业接到零售商的订单后,把订单的内容传送给公司,公司把一段时间的订单进行汇总、整合、分类,把在同一条路线上的订单归类,并安排车辆进行共同配送。
联动前后的订单处理成本如表1-7-2所示。
表1-7-2 联动前后的订单处理成本对比

(2)生产作业成本
联动前,制造企业独立承担着生产和配料工作,其产品生产周期长,配料的出错率高,导致次品率居高不下,而且由于配料出错,造成大量的原料浪费,或者过剩的原料没有及时回收,从而造成了资源浪费。
联动后,公司承担了制造企业的配料工作,采用RFID射频技术,对入库及出库的原材料进行实时跟踪。生产线上,公司员工可以根据信息中心的指示,确定需要及时地补料的环节,能够做到数量上的精确,从而避免了原料的浪费。
联动前后相比,原料节约了39%以上,生产周期缩短了28%,补料人员减少了3个。
(3)出入库及仓储作业成本
联动前,制造企业根据历史数据预测市场需求,并进行生产计划和设置库存水平,但是由于市场需求变化的不规则性,预测经常发生较大的偏差,出现过量的库存,导致巨大的库存持有成本,或者缺货不足,导致较大的缺货成本。同时,制造企业仓库内的设备运作效率低下,有些机械设备处于空闲状态,利用率不高,而有些却不间断地工作,设备的使用寿命严重下降。
联动后,公司负责制造企业的库存管理。公司能够根据需求订单,做出比较准确的市场预测,并为制造企业的库存进行全面管理。
联动前后相比,制造企业设备利用率提高24%,库存周转率缩短43%。联动前后的仓储成本如表1-7-3所示。
表1-7-3 联动前后的仓储成本对比

(4)配送作业成本
联动前,制造企业的货物配送是以订单为单位进行,且经常出现返程空驶现象,车辆的实载率低;运输路径的选择大都凭司机经验,迂回运输现象频繁,运输距离增大。因此油费、路费、车辆维修费等相关成本上升,导致配送作业成本居高不下。
联动后,公司承担制造企业的配送工作,由于公司拥有专业的配送车队和长期合作的协议车队,可以通过整合制造企业的订单,选用合理的包装容器和装载方式,使车辆利用率达到最大化;通过合理地安排运输计划,减少车辆返程空驶现象;通过优化配送路径,减少运输迂回现象;通过合理的选择包装以及包装容器的循环利用,减少包装费用。
联动前后相比,车辆实载率由75%上升到95%以上,车辆返程的实载率也提高了62%,车辆运行总里程节约了35%以上,耗油量减少了28%以上,相关的管理费用节约36%以上。短途运输的时间由原来的4天以上,缩短为现在的2天以内,缩短率达50%以上。同时,包装材料费用降低了16%以上。
(5)资金成本
资金成本方面,不仅仅是减少了制造企业的资金成本,而且对零部件和原材料供应商也减少了资金成本压力。如图1-7-12所示,通过零库存管理,制造企业实现了资产的转移,减少了在库数量和资金成本;同时,通过VMI信息共有Web,公司会将采购计划、库存水平与供应商进行分享,减少了供应商库存成本和原材料资金占用时间。

图1-7-12 “两业”联动的信息共享图