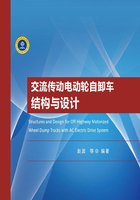
1.7 机械传动和电传动
1.7.1 机电之争
20世纪60、70年代,大型矿用自卸车极大提高了露天矿山开采效率,但露天矿山多为折回坡道,柴油卡车运行成本较高。由于当时大功率液力变矩器等传动系统的研制没有过关,机械传动型矿车一直难以大型化。矿用电动轮自卸车的出现,解决了制约自卸车向更大吨位发展的关键技术难题——传动系统问题,极大地提高了矿山运输的经济性,于是电动轮矿用车乘势崛起,几乎全部占领了100t级以上的矿用车市场,载重量超过百吨的矿车都采用电传动这种趋势一直延续到了20世纪80年代初期。
20世纪80年代初,由于工业技术的进步和合金钢冶炼与热处理工艺取得突破性进展,才解决了制造大型机械传动矿车所必需的关键部件(如高强度、小尺寸的变矩器—变速箱等)的材料、工艺及可靠性问题;与此同时,轴承设计和制动系统的工艺改进以及电子技术的应用,也大大促进了大型矿用机械传动自卸车的迅速发展[16]。直至1983年,机械制造业的技术发展和美国艾里逊(Allison)公司的大功率液力变矩器研制成功,以美国卡特彼勒的785型和日本小松的HD-1200M型问世为标志,机械传动车型才逐步进入100t级矿用车市场,但市场占有率相当低。1988年,美国卡特彼勒公司试制成功载重量154~177t的CAT789型机械传动自卸车后,机械传动重新受到人们的重视,出现机械传动和电力传动孰优孰劣的争论[16]~[18]。目前百吨级以上机械传动的生产商只有美国卡特彼勒一家,其797F机械传动型矿车载重量已经达到最高的400短吨(363t),见图1.30。

图1.30 797F机械传动型矿车
近50年来,机械传动和电传动的竞争一直很激烈,大型机械传动自卸车的出现,又从另一方面促进了电动轮自卸车的持续改进。因此机、电两类传动矿车一直是互相促进、共同发展。目前百吨以上的机、电两类传动矿车的产销量几乎是平分秋色,但由于电传动起步较早,电动轮自卸车在各矿山中的保有量仍占绝对优势。
目前,对于载重100t以下的中小吨位车型,年需求量稍大,多采用液力机械变矩器和传统后驱动桥(少数还采用液压传动或液力传动),小吨位车型性能要求不高,以及结构上的限制,电传动并无明显优势。100t以上的车型,则为小批量生产,一般均采用电传动,100~200t的大型自卸车多采用直流驱动方式,而200t以上的巨型矿车普遍采用交流驱动。这是因为:交流驱动系统所具有的特点最适合于高速度和露天矿深部运输。这些特征包括:在较大的速度范围内的高驱动系统的效率、低维修量(无需更换轴承)、可靠的性能(大修间隔期约为25000h)。由于交流电系统价格昂贵,所以豪帕克公司认为将其用于小型矿车是不合适的,直流驱动仍是136~218t电动轮矿车的优先选择。