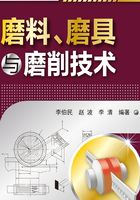
1.3 碳化物系磨料
碳化物有SiC、TiC、WC等多种化合物,在磨料中常见的有绿碳化硅(SiC)和黑碳化硅(C)。
①黑碳化硅(C) 以石英、石油、焦炭为原料,加入少量木屑,在1700℃以上的高温电阻炉中冶炼而成。其化学成分含98.5%以上的SiC、游离碳小于0.2%,Fe2O3小于0.6%,呈黑色光泽结晶。它的韧性较绿碳化硅高。
②绿碳化硅(GC) 以石英沙、焦炭为原料,加入木屑和食盐,在电阻炉中冶炼而成。其化学成分为含99%以上的SiC,游离碳小于0.2%,Fe2O3小于0.2%,呈绿色光泽结晶。其硬度比黑碳化硅高,切削能力强。
③立方碳化硅(SC) 又名β-碳化硅。立方碳化硅是碳化硅的低温相,呈微粒状立方晶体,生成于1450℃,在1600℃以上高温开始转变为六方碳化硅。通常以碳和硅、碳和石英为原料,在小型的管状炉内获得。其化学成分为含SiC92%~94%,矿物成分为β-SiC。具有与金刚石相似的立方形晶体结构。一般呈淡黄绿色,其硬度高于黑碳化硅而略次于绿碳化硅,切削能力较强。
④碳化硼(BC) 用硼酸与石墨粉(或炭粉)为原料熔炼而成。硼酸在250℃以下进行脱水后,粉碎成粉末,与石墨按一定比例混合后,放入电弧炉(或电阻炉)内,在1700~2500℃的高温下,以碳直接还原硼酸生成。它是一种灰暗至金属光泽的粉末,其硬度仅次于金刚石、立方氮化硼,耐磨性好,切削能力强。其分子式为B4C。
1.3.1 碳化硅的晶体结构及相图
(1)SiC晶体结构
用X射线对SiC晶体结构进行衍射分析证明,SiC的晶型有α-SiC、β-SiC。α-SiC为高温稳定型,β-SiC为低温稳定型。β-SiC向α-SiC转变的温度始于2160℃,但转变速率很小,在0.1GPa的压力下,分解温度为2380℃。α-SiC为六方晶体结构,晶体参数为a=b=d≠c(或a=b≠c),α=β=90°,γ=120°为简单六方点阵,阵点坐标为[0,0,0]。按拉斯德尔法命名将α-SiC分为4H-SiC、6H-SiC、15R-SiC。β-SiC用3C-SiC命名。H表示六方晶系结构,R表示菱面体结构,C表示立方晶体结构,4、6、15表示晶体沿c轴周期的层数。4H-SiC、6H-SiC为六方晶体结构,15R-SiC为菱方三方体结构。β-SiC(或3C-SiC)为面心立方体结构(FCC)。SiC离子键性比例为12%,共价键性比例为88%。SiC可视为共价键化合物。其晶体结构中单位晶胞由相同的四面体结构构成,硅原子处于中心,如图1-8所示。

图1-8 SiC四面体结构
(2)SiC系统相图
图1-9(a)所示为常温下SiC系统相图,该图确定了硅基固溶体和熔体的存在范围,SiC的分解温度为2760℃,并确定了气相+C、气相+SiC、液相+气相、液相+碳固溶体两相区,碳及硅所形成的均相区,在1410℃出现液相+碳固溶体+SiC变量的三相平衡,在2760℃呈现气相+SiC+C无变量三相平衡,图中SiC是唯一的固相二元化合物。

图1-9 SiC系统相图
图1-9(b)所示为10MPa气压下SiC系统相图,可以看出高压下的三相平衡和升华曲线向高温方向移动,形成液相+SiC及液相+C的两级分完全互溶的熔体区,SiC在熔融前后固、液相的化学成分不同,高压时它转熔分解为石墨(C)和富硅熔体,常压下分解为石墨和气相,在超高压下可从碳化物熔融体直接制取SiC。
1.3.2 碳化硅磨料的生产工艺
(1)SiC的原材料
其主要原料为硅砂与碳素,辅助材料有木屑、食盐与回炉料。
①硅砂(SiO2) 又称石英砂。冶炼SiC常用河砂、海砂及脉石英。河砂及海砂用来冶炼黑色SiC,脉石英用来冶炼绿色SiC。硅砂的粒度大小影响SiC的产量,也是电能消耗的重要因素,因此要选用质量合适的较细粒度的硅砂。
②碳素 提供生成SiC反应的碳,常用石油焦炭、沥青焦炭及低灰分的无烟煤。
③木粉(硬木屑) 为了增加透气性,扩大反应区。
④食盐 含量在97%~99%,粒度小于2mm。在冶炼绿色SiC时加入可加速排除杂质,起净化剂和催化作用。冶炼黑色SiC时不使用。
(2)SiC的生产工艺流程
电阻炉是冶炼SiC的主要设备。冶炼工艺方法有新料法与熔烧料法。新料法是将配好的原材料直接装入电阻炉的反应区冶炼SiC。熔烧料法是将配好的原材料装入下一炉的反应区进行冶炼。SiC生产的工艺流程分为配料→装炉→冶炼→冷却与扒炉→混料除盐→出炉与分级→造粒。
1.3.3 碳化硅制粒加工
一般将F4~F220粒度的磨料称为磨粒,将F230~F1200粒度的磨料称为微粉。磨粒加工采用筛分分级,微粉采用水力分级。
制粒工艺过程:结晶块破碎→筛分→水洗→酸洗→碱洗→磁选→整形→煅烧(烘干)→精筛→检查包装。
微粉主要工艺过程:结晶块破碎→球磨→筛分→水洗→脱水→干燥→水力分级→磁选→精筛→检查→包装。