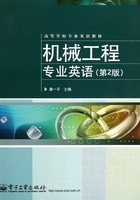
2.3 Polymers
Polymeric materials have extremely large molecules (macromolecules). Consumer and industrial products made of polymers include food and beverage containers, packaging, signs, textiles, medical devices, foams, paints, safety shields, toys, appliances, lenses, gears, electronic and electrical products, and automobile bodies and components. They have many unique and diverse properties:
1. corrosion resistance and resistance to chemicals;
2. low electrical and thermal conductivity;
3. low density;
4. high strength-to-weight ratio, particularly when reinforced;
5. noise reduction;
6. wide choice of colors and transparencies.
The development of modern plastics technology began in the 1920s, when the raw materials necessary for making polymers were extracted from coal and petroleum products. Ethylene was the first example of such a raw material; it became the building block for polyethylene. Ethylene is the product of the reaction between acetylene and hydrogen, and acetylene is the product of the reaction between coke and methane. The commercial polymers, including polypropylene, polyvinyl chloride, polycarbonate, and others, are all made in a similar manner; these materials are known as synthetic organic polymers.
Thermoplastics. When we heat the polymer and then cool the polymer, it returns to its original hardness and strength; in other words, the process is reversible, the polymer is known as thermoplastics, typical examples of which are acrylics, cellulosics, nylons, polyethylenes, and polyvinyl chloride.
Thermosets. However, if the long-chain molecules in a polymer are cross-linked in a three-dimensional arrangement, the structure in effect becomes one giant molecule with strong covalent bonds, these polymers are called thermosetting polymers, or thermosets, because, during polymerization, the network is completed and the shape of the part is permanently set.[4] This curing (cross-linking) reaction, unlike that of thermoplastics, is irreversible. If the temperature is increased sufficiently, the thermosetting polymer begins to burn up, degrade, and char. Thermosetting plastics generally possess better mechanical, thermal, and chemical properties, electrical resistance, and dimensional stability than do thermoplastics. A typical thermoset is phenolic, which is a product of the reaction between phenol and formaldehyde. Common products made from this polymer are the handles and knobs on cooking pots and pans and components of light switches and outlets.
Biodegradable Plastics. Plastic wastes contribute about 10% of municipal solid waste. One-third of plastic production goes into disposable products, such as bottles, packaging, and garbage bags. With the growing use of plastics, and with increasing concern over environmental issues regarding the disposal of plastic products and the shortage of landfills, major efforts are underway to develop completely biodegradable plastics. Most plastic products have traditionally been made from synthetic polymers that are derived from nonrenewable natural resources, are not biodegradable, and are difficult to recycle. Biodegradability means that microbial species in the environment (e.g. microorganisms in soil and water) will degrade a portion of (or even the entire) polymeric material, under the right environmental conditions, and without producing toxic by-products.[5] The end products of the degradation of the biodegradable portion of the material are carbon dioxide and water. Because of the variety of constituents in biodegradable plastics, these plastics can be regarded as composite materials; consequently, only a portion of these plastics may be truly biodegradable.