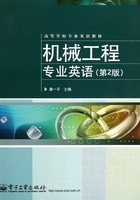
2.2 Ceramics
Ceramics are compounds of metallic and nonmetallic elements. Because of the large number of possible combinations of elements, a great variety of ceramics are now available for a wide range of consumer and industrial applications. Ceramics have been used for many years in automotive spark plugs, as an electrical insulator and for high-temperature strength. They have become increasingly important in tool and die materials, in heat engines, and in automotive components such as exhaust-port liners, coated pistons, and cylinder liners.
Ceramics can be divided into two general categories:
1. Traditional, such as whiteware, tiles, brick, sewer pipe, pottery, and abrasive wheels.
2. Industrial ceramics, also called engineering, fine ceramics, or advanced ceramics, have found wide applications in turbine, automobile, aerospace components, heat exchangers, semiconductors, seals, prosthetics and cutting tools.
Ceramics are available as a single crystal or in polycrystalline form, consisting of many grains. Grain size has a major influence on the strength and properties of ceramics, the finer the grain size, the higher are the strength and toughness.
Oxide Ceramics. There are two major types of oxide ceramics: alumina and zirconia.
Alumina. Also called corundum or emery, alumina (aluminum oxide, Al2O3) is the most widely used oxide ceramic, either in pure form or as a raw material to be mixed with other oxides. It has high hardness and moderate strength. Although alumina exists in nature, it contains unknown amounts of impurities and possesses non-uniform properties. As a result, its behavior is unreliable. Aluminum oxide, silicon carbide, and many other ceramics are now manufactured almost totally synthetically, so that their quality can be controlled.
Zirconia. Zirconia (zirconium oxide, ZrO2, white in color) has good toughness; good resistance to thermal shock, wear, and corrosion; low thermal conductivity; and a low friction coefficient. Partially stabilized zirconia (PSZ) has high strength and toughness and better reliability in performance than does zirconia. It is obtained by doping the zirconia with oxides of calcium, yttrium, or magnesium.[1] Typical applications include dies for hot extrusion of metals and zirconia beads used as grinding and dispersion media for aerospace coatings, for automotive primers and topcoats, and for fine glossy print on flexible food packaging.
Other ceramics may be classified as follows:
Carbides. Typical examples of carbides are those of tungsten (WC) and titanium (TiC), used as cutting tools and die materials, and that of silicon (SiC), used as an abrasive (especially in grinding wheels).
1. Tungsten carbide consists of tungsten-carbide particles with cobalt as a binder. The amount of binder has a major influence on the material’s properties. Toughness increases with cobalt content, whereas hardness, strength, and wear resistance decrease.
2. Titanium carbide has nickel and molybdenum as the binder and is not as tough as tungsten carbides.
3. Silicon carbide has good resistance to wear, thermal shock, and corrosion. It has a low friction coefficient, and it retains strength at elevated temperatures. It is suitable for high-temperature components in heat engines and is also used as an abrasive.
Nitrides. Another important class of ceramics is the nitrides, particularly cubic boron nitride (CBN), titanium nitride (TiN), and silicon nitride (Si3N4).
1. Cubic boron nitride, the second hardest known substance (after diamond), has special applications, such as in cutting tools and for abrasives in grinding wheels. It does not exist in nature; it was first made synthetically in the 1970s, by means of techniques similar to those used in making synthetic diamond.
2. Titanium nitride is used widely as a coating on cutting tools. It improves tool life by virtue of its low frictional characteristics.
3. Silicon nitride has high resistance to creep at elevated temperatures, low thermal expansion, and high thermal conductivity; consequently, it resists thermal shock. It is suitable for high-temperature structural applications, such as in automotive engine and gas-turbine components, in cam-follower rollers, in bearings, in sand-blast nozzles, and in components for the paper industry.
Cermets. Cermets are combinations: a ceramic phase bonded with a metallic phase. Introduced in the 1960s and also called black ceramics or hot-pressed ceramics, they combine the high-temperature oxidation resistance of ceramics with the toughness, thermal-shock resistance, and ductility of metals.[2] An application of cermets is in cutting tools, a typical composition being 70% aluminum oxide and 30% titanium carbide.
Other cermets contain various oxides, carbides, and nitrides. They have been developed for high-temperature applications, such as nozzles for jet engines and brakes for aircraft. Cermets can be regarded as composite materials; they can be used in various combinations of ceramics and metals bonded by powder-metallurgy techniques.
The capability of ceramics to maintain their strength and stiffness at elevated temperatures makes them very attractive for high-temperature applications. Their high resistance to wear makes them suitable for applications such as cylinder liners, bushings, seals, and bearings. The higher operating temperatures made possible by the use of ceramic components mean more efficient burning of fuel and reduction of emissions in automobiles. Currently, internal combustion engines are only about 30% efficient, but with the use of ceramic components the operating performance can be improved by at least 30%.
Much research has been conducted on developing materials and techniques for an all-ceramic heat engine capable of operating at temperatures up to 1000 °C (1830 °F). The development of such an engine has, however, been slower than expected because of such problems as unreliability, lack of sufficient toughness, difficulty with lubricating bearings and hot components, and a lack of the capability for structural ceramics (such as silicon nitride and silicon carbide) to be produced economically in near-net shape, as weighed against the need for the machining and finishing processes required for dimensional accuracy of the engine.[3]
Bioceramics. Because of their strength and inertness, ceramics are used as biomaterials to replace joints in the human body, as prosthetic devices, and in dental work. Furthermore, ceramic implants can be made porous; bone can grow into the porous structure (likewise with porous titanium implants) and develop a strong bond, having high structural integrity between them. Commonly used bioceramics are aluminum oxide, silicon nitride, and various compounds of silica.