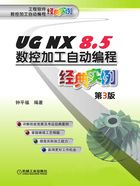
1.2.2 加工工艺分析和规划
数控加工程序编制简称数控编程。数控编程由编程员或工艺员完成。加工零件之前,必须将零件的全部工艺过程、工艺参数和位移数据等进行拟定,其过程与常规工艺路线拟定过程相似,数控加工工艺路线的设计,需先找出零件所有的加工表面并逐一确定各表面的加工方法,其每一步相当于一个工步,然后将所有工步内容按一定原则排列成先后顺序。接着确定哪些相邻工步可以划为一个工序,即进行工序的划分。最后再将所需的其他工序如常规工序、辅助工序、热处理工序等插入,衔接于数控加工工序序列之中,就得到了要求的工艺路线。数控加工的工艺路线设计与普通机床加工的常规工艺路线拟定的区别,主要在于它仅是几道数控加工工艺过程的概括,而不是指从毛坯到成品的整个工艺过程。由于数控加工工序一般均穿插于零件加工的整个工艺过程之中,因此在工艺路线设计中,一定要兼顾常规工序的安排,使之与整个工艺过程协调吻合。
1.工序的划分
在数控机床上加工的零件,一般按工序集中原则划分工序。划分方法如下:
(1)按安装次数划分工序 以一次安装完成的那一部分工艺过程为一道工序。该方法一般适合于加工内容不多的工件,加工完毕就能达到待检状态。
(2)按所用刀具划分工序 以同一把刀具完成的那一部分工艺过程为一道工序。这种方法适用于工件的待加工表面较多,机床连续工作时间过长,加工程序的编制和检查难度较大等情况。在专用数控机床和加工中心上常用这种方法。
(3)按粗、精加工划分工序 考虑工件的加工精度要求、刚度和变形等因素来划分工序时,可按粗、精加工分开的原则来划分工序,即以粗加工中完成的那部分工艺过程为一道工序,精加工中完成的那部分工艺过程为另一道工序。一般来说,在一次安装中不允许将工件的某一表面粗、精不分地加工至精度要求后再加工工件的其他表面。
(4)按加工部位划分工序 以完成相同型面的那一部分工艺过程为一道工序。有些零件加工表面多而复杂,构成零件轮廓的表面结构差异较大,可按其结构特点(如内型、外形、曲面或平面等)划分成多道工序。
综上所述,在划分工序时,一定要视零件的结构与工艺性、机床的功能、零件数控加工内容的多少、安装次数以及生产组织等实际情况灵活掌握。
2.加工顺序的安排
加工顺序安排得合理与否,将直接影响到零件的加工质量、生产率和加工成本。应根据零件的结构和毛坯状况,结合定位及夹紧的需要综合考虑,重点应保证工件的刚度不被破坏,尽量减少变形,同时还应遵循下列原则:
1)尽量使工件的装夹次数、工作台转动次数、刀具更换次数及所有空行程时间减至最少,提高加工精度和生产率。
2)先内后外原则,即先进行内型内腔加工,后进行外形加工。
3)为了及时发现毛坯的内在缺陷,精度要求较高的主要表面的粗加工一般应安排在次要表面粗加工之前;大表面加工时,因内应力和热变形对工件影响较大,一般也需先加工。
4)在同一次安装中进行的多个工步,应先安排对工件刚性破坏较小的工步。
5)为了提高机床的使用效率,在保证加工质量的前提下,可将粗加工和半精加工合为一道工序。
6)加工中容易损伤的表面(如螺纹等),应放在加工路线的后面。
3.数控加工工序与普通工序的衔接
这里所说的普通工序是指常规的加工工序、热处理工序和检验等辅助工序。数控工序前后一般都穿插其他普通工序,若衔接不好就容易产生矛盾。较好的解决办法是建立工序间的相互状态联系,在工艺文件中做到互审会签。例如是否预留加工余量,留多少、定位基准的要求、零件的热处理等,这些问题都需要前后衔接,统筹兼顾。
4.工件的定位与夹紧方案
工件的定位,粗基准方案的确定应遵循以下原则:相互位置要求原则;加工余量合理分配原则;重要表面原则;不重复使用原则;便于装夹原则。
精基准的选择原则:基准重合原则;基准统一原则;自为基准原则;互为基准反复加工原则;便于装夹原则。
辅助基准:辅助基准是为了便于装夹或易于实现基准统一而人为制成的一种定位基准。
工件的夹紧:夹紧装置由力源部分和夹紧机构两个基本部分组成。
夹紧力方向的确定:夹紧力的作用方向应垂直指向主要定位基准,应使所需夹紧力尽可能小,应使工件变形尽可能小。夹紧力作用点的选择:应施加于工件刚性较好的部位上,应尽量靠近工件加工面,应落在定位元件的支承范围内。夹紧力的大小:一般按静力平衡原理,计算所需的理论夹紧力,乘上安全系数即为实际所需夹紧力。
5.铣削刀具的选择
铣刀主要参数的选择:选择铣刀时要根据不同的加工材料和加工精度要求,选择不同参数的铣刀进行加工。数控铣床上使用最多的是可转位面铣刀和立铣刀,下面重点介绍面铣刀和立铣刀参数的选择。
(1)面铣刀主要参数的选择 标准可转位面铣刀直径为16~630mm,应根据侧吃刀量选择适当的铣刀直径(一般比切宽大20%~50%),尽量包容工件整个加工宽度,以提高加工精度和效率,减小相邻两次进给之间的接刀痕迹和保证铣刀的寿命。粗铣时,铣刀直径要大些,因为粗铣切削力大,选小直径铣刀会减小切削扭矩。精铣时,铣刀直径也要大些,尽量包容工件整个加工宽度,以提高加工精度和效率,并减小相邻两次进给之间的接刀痕迹。
(2)立铣刀主要参数的选择 立铣刀的有关参数,推荐按下述经验数据选取。
刀具半径R应小于零件内轮廓面的最小曲率半径ρ,一般取R=(0.8~0.9)ρ。
零件的加工高度H≤(1/6~1/4)R,以保证刀具有足够的刚度。
对不通孔(深槽),选取L=H+5~10mm(L为刀具切削部分长度,H为零件高度)。
加工外形及通槽时,选取L=H+r+5~10mm(r为刀尖半径)。
粗加工内轮廓面时,铣刀最大直径D粗可按下式计算:
D粗=2(δsinθ/2-δ1)/(1-sinθ/2)+D
式中,D—轮廓的最小凹圆角直径;
δ—圆角邻边夹角等分线上的槽加工余量;
δ1—精加工余量;
θ—圆角两邻边的夹角。
加工肋时,刀具直径D=(5~10)b,其中b为肋的厚度。
技巧提示:刀具的选择要注意考虑:切削性能好,精度高,可靠性高,寿命长,断屑及排屑性能好。
6.切削用量的选择
切削用量包括切削速度、进给速度、背吃刀量和侧吃刀量。从刀具寿命出发,切削用量的选择方法是:先选取背吃刀量或侧吃刀量,其次确定进给速度,最后确定切削速度。
(1)背吃刀量(端铣)或侧吃刀量(圆周铣)背吃刀量和侧吃刀量的选取主要由加工余量和对表面质量的要求决定。
在工件表面粗糙度值要求为Ra12.5~25µm时,如果圆周铣削的加工余量小于5mm,端铣的加工余量小于6mm,粗铣一次进给就可以达到要求。但在余量较大、工艺系统刚性较差或机床动力不足时,可分两次进给完成。
在工件表面粗糙度值要求为Ra3.2~12.5µm时,可分粗铣和半精铣两步进行,粗铣时背吃刀量或侧吃刀量选取不同,粗铣后留0.5~1.0mm余量,在半精铣时切除。
在工件表面粗糙度值要求为Ra0.8~3.2µm时,可分粗铣、半精铣、精铣三步进行。半精铣时背吃刀量或侧吃刀量取1.5~2.0mm,精铣时圆周铣侧吃刀量取0.3~0.5mm,面铣背吃刀量取0.5~1mm。
(2)进给速度 进给速度vf是单位时间内工件与铣刀沿进给方向的相对位移,单位为mm/min。它与铣刀转速n、铣刀齿数z及每齿进给量fz(单位为mm/z)的关系式为:
vf=fzzn
(3)切削速度 铣削的切削速度计算公式为vc=πDn/1000,其中n为主轴转速,D为刀具直径。