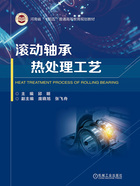
1.1.2 国内轴承钢发展概况
与国外相比,我国工业基础相对薄弱,轴承钢的发展起步较晚。1953年制定了高碳铬轴承钢的相关标准。20世纪60年代,我国开始进行高温轴承钢、不锈轴承钢以及渗碳轴承钢等特殊用途轴承钢的生产。20世纪90年代初,轴承钢的连铸技术在我国得到应用,此时轴承钢的年产量和日本轴承钢的年产量相当。进入21世纪,由于冶炼和轧制技术及装备水平的提升,特别是真空脱气技术和装备的应用,我国轴承钢在纯净度和夹杂物方面上了一个大的台阶,关键技术指标已达国际先进水平。氧的质量分数由原来的电炉钢(30~40)×10-6降低到真空脱气模铸钢的(5~12)×10-6和连铸钢的(4~12)×10-6,Ti控制在25×10-6以下,通过严格控制添加的铬铁合金含量,Ti达到15×10-6以下;DS类夹杂物基本上能达到1.0级以下。经过70年的发展,我国有较大轴承钢生产能力的特钢企业达到20多家,轴承钢的年产量超过400万吨,其中高碳铬轴承钢占95%以上,稳居世界第一位。兴澄特钢已发展成为轴承钢销量世界第一的特钢厂。其生产的高档轴承钢已向斯凯孚、舍弗勒、NTN等世界各国轴承公司供货。氧含量、疲劳寿命、单颗粒球状夹杂物等技术指标达到国际先进水平。有的指标已达国际领先水平。但是,轴承钢技术质量水平依然是制约我国轴承产业高质量发展的短板之一,尤其在质量的一致性、性能的稳定性和特种轴承钢个性化需求上与国际先进水平还存在一定差距。
目前,以连铸轴承钢为代表的日本山阳(Sanyo)和以模铸轴承钢为代表的瑞典奥沃科(Ovako)达到了轴承钢生产工艺以及质量的最高水平。传统国产轴承钢与国际先进水平的差距主要体现在以下三个方面:氧含量和钛含量偏高,且波动性较大;非金属夹杂物的尺寸较大、分布均匀性和稳定性较差;碳化物较大,且分布均匀性较差。目前我国轴承钢制造逐渐形成了较为完善的工业体系,产品质量和品种也取得了显著的进步,部分大型钢企如兴澄特钢、宝武钢铁等生产的轴承钢产品均已得到国际著名轴承生产企业的认可。国内一直针对上述问题持续开展研究,力求进一步提升质量。
1)提高纯净度。部分国内生产的轴承钢中氧的质量分数已经可以极限控制在5×10-6以下,与国际先进水平相近,但仍存在高纯净度条件下大颗粒夹杂物尺寸大、夹杂物的分布不均匀、残留钛含量偏高等问题。
2)减少低倍组织缺陷。进一步降低轴承钢中的中心疏松、中心缩孔与中心成分偏析。
3)微观组织的超细化、稳定化。细化原奥氏体晶粒和碳化物尺寸,提高均匀性,并调控残留奥氏体,提高其稳定性。
4)提高综合服役性能。提高轴承钢的强韧性,使其具备耐蚀、抗冲击、耐超高温及轻质化等服役性能。