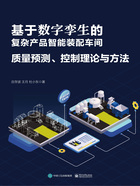
1.6 基于数字孪生的复杂产品智能装配车间质量管控体系
参考六西格玛质量管理方法的思想,在考虑复杂产品离散智能装配车间质量管控的全面性、准确性、及时性、可追溯性和预见性等需求的基础上,以数据在数字空间的自动流动为核心,提出了一种基于数字孪生的复杂产品智能装配车间质量管控方法(见图1.14),并将其实施过程定义为“CFMPOD六步循环”,具体包括采集(Collect, C)、融合(Fuse, F)、映射(Mapping, M)或作镜像(Mirror, M)、预测(Predict, P)、决策(Optimize, O)或分析(Analysis, A)、执行(Do, D)。其中,用于映射的可视化模型、用于计算的预测,以及在线优化与控制模型共同组成了复杂产品智能装配车间质量管控的数字孪生模型。

图1.14 基于数字孪生的复杂产品智能装配车间质量管控的实施流程
(1)采集:通过硬件采集终端、条码、传感器、射频识别、人机交互等各种数据获取方式采集车间运行过程中产生的各类动态数据,包括制造资源感知数据、传感数据、设备运行数据、环境数据、工序完工数据、实际工时数据、质量数据、实做物料数据、车间多媒体数据等。
(2)融合:通过数据清洗、数据统一建模、数据时空对准等方法对车间运行过程中采集的多源异构数据(尤其是多源传感数据)进行预处理和统一管理,从而为车间运行的同步映射、精准预测、快速决策与反馈控制提供可信的数据和信息。
(3)镜像:通过三维模型重构、二维看板展示、数据可视化、运行过程模拟等方式实现数字孪生可视化模型与物理车间的同步运行,实现对复杂离散制造车间的三维全局可视化监控。
(4)预测:基于历史数据和实时数据,通过大数据模型、数理模型或两者的融合模型来预测未来的车间运行状态及可能发生的异常。
(5)决策:基于数字空间的映射和预测结果进行决策,一方面对车间运行过程中的潜在异常进行预警,并提醒相关人员通过调整和优化工艺参数、制定新的生产计划等方式来避免异常的发生;另一方面对运行过程中已经出现的异常进行报警,并辅助相关人员快速响应和处理该异常。
(6)执行:物理空间的人、机、料等制造资源将在新的解决方案指导下运行,并确保过程一旦完成能继续保持下去而不会返回到先前的状态。
通过基于数字孪生的复杂产品智能装配车间质量管控方法及其实施流程,能够实现对装配车间运行状态和运行过程的同步映射(可视)、在线预测(可测)和精准决策(可控)。在可视层面,包括全面监控复杂产品智能装配车间全要素、全业务的运行状态和运行过程、实时洞察装配过程中的产品工艺的状态变化等。在可测层面,包括产品质量预测、瓶颈资源预测、工时预测、完工时间预测等。在可控层面,包括工艺参数的优化与控制、制造资源的优化配置、质量和技术问题的快速处理等。