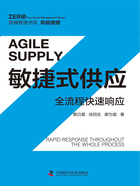
二
传统精益生产理论与一体化供应链观念
传统精益生产理论的基本假设是:消费者偏好价格和制造质量。同时,为了最大可能地为企业创造利润以及实现企业价值增长,精益生产理论也致力于缩短产品交付周期,加快现金流动。精益生产最重要的关键词是“消除浪费”,“消除浪费”几乎就是“精益”的同义词。丰田生产方式(TPS)创始人大野耐一说:“我们所做的就是研究客户给我们下订单的那一刻到我们收到货款的整个时间段,通过消除无价值的浪费来缩短这一时间段。”
但是,传统的精益生产理论主要研究企业内部改善,对于外部供应链的研究较少。20世纪90年代初期,继日本丰田的准时制生产(Just In Time,缩写为JIT)模式之后,在美国兴起了一种全新的管理模式——供应链管理。供应链是一条从供应商到制造商再到最终顾客的贯穿所有企业的“链”,它包括满足顾客需求所直接或间接涉及的所有环节。不过,传统供应链管理虽然也强调对资源的充分利用和挖掘,但更多的还是把供需双方看成是博弈关系,而客户仅是服务对象。
不可否认的是,传统精益生产理论与一体化供应链观念至今仍是企业管理的重要工具。如果脱离了精益和供应链理念去谈模式创新,那就是哗众取宠、不切实际。下面我们来简单介绍一下精益生产和供应链管理的基本理念。
1 精益生产的基本思想
前面已经提过,精益生产的基本思想是“杜绝浪费”。从客户价值的角度看,客户愿意付款的活动才是有价值的,只有在正确的地点、正确的时间提供的方案才是正确的解决方案。因此,不增值的活动就是浪费。
现有能力=工作+浪费(无效劳动)
作业=有效劳动+无效劳动(浪费)
精益生产理论认为,提高效率只有与降低成本结合起来才有意义,企业必须朝着以最少的人员仅仅生产客户所需要的数量和所需要的产品这一方向努力。局部的效率提升不但无助于降低成本,反而可能造成生产过剩,产生不必要的库存。所以,推行精益生产时,要以生产线为中心,从整个工厂着眼提高整体效率。
《精益思想》一书,针对精益思想的实施总结出五个基本原则,这些原则是:
(1)正确地确定价值 正确地确定价值就是企业以顾客的观点来确定从设计到生产再到配送的全部过程,实现顾客需求的最大满足。并且企业还要将供应链全过程的多余消耗减至最少,不将额外的成本转嫁给顾客。
(2)识别价值流 价值流是指从原材料转变为成品,并给它赋予价值的全部活动。这些活动包括从概念,到设计,到生产的技术过程;从订单处理,到计划,到配送的信息过程;从原材料,到半成品,到产成品的物质转换过程;产品全生命周期的支持和服务过程。精益思想识别价值流的含义是在价值流中找出哪些是真正增值的活动,哪些是可以立即去掉的不增值活动。精益思想将供应链中消耗了资源而不增值的活动称为浪费。简言之,识别价值流就是发现浪费和消灭浪费。
(3)价值流动 精益思想要求创造价值的各个活动(步骤)流动起来,强调的是不间断地“流动”。“价值流”本身的含义就是“动”的,但是由于根深蒂固的传统观念和做法,如部门的分工、大批量生产等,阻断了本应流动起来的价值流。精益思想则将所有的停滞作为供应链的浪费,是用持续改进、及时制等方法在任何批量条件下创造价值的连续流动。
(4)需求拉动 “需求拉动”就是按顾客的需求投入和产出,使顾客在他们要求的时间内得到需要的东西。实行需求拉动以后,顾客或者供应链下游企业就会像在超市的货架上选取他们所需要的东西一样,而不是企业把顾客并不想要的产品强行推给顾客。在需求拉动原则中,供应和需求直接对应,这样可消除过早、过量的投入,减少大量的库存和现场在制品,极大地压缩前置周期。其深远的意义在于企业具备了当顾客一旦需要某种产品,就能立即进行设计、计划、制造和配送给顾客真正需要的产品的能力,最后是抛开预测,直接按照顾客的实际需求进行生产和物流管理。
(5)尽善尽美 上述四个原则相互作用的结果必然是价值流动速度显著加快,这样就必须不断地用价值流分析方法找出更隐藏的浪费,做进一步的改进,这样的良性循环成为趋于尽善尽美的过程。虽然在现实中“尽善尽美”是永远达不到的,但通过持续地对尽善尽美的追求,将会造就一个永远充满活力、不断进步的企业。
2 精益生产的目标
制造企业的利润是通过降低成本获得的。现代企业追求效率,就是为了达到企业运营的根本目的——降低成本。所以,如前所述,提高效率只有与降低成本结合起来才有意义。那么,怎样才能降低成本呢?答案只有六个字:“增加流程效率”。
我们通过准时制交货、缩短交货周期、提高应变弹性等手段,不断提高流程效率,消除所有无价值的浪费,从而达到降低成本的目的,如图2所示。
那么,企业中存在哪些浪费呢?伴随企业运营中各业务环节不被察觉或不被重视的浪费,日本企业管理界将之形象地比喻为“地下工厂”。工厂常见的八大浪费包括等待浪费、搬运浪费、不良浪费、动作浪费、加工浪费、库存浪费、制造过多(过早)浪费和缺货损失,如图3所示。

图2 提高流程效率的四大目的

图3 工厂八大浪费
精益生产就是要不断消除八大浪费,同时追求七个“零”目标,即零切换浪费、零库存、零浪费、零不良、零故障、零停滞和零事故。
3 精益生产的基本法则
精益生产的基本法则包括均衡化、准时化和自动化。
均衡化生产也叫作均匀化生产,它是精益生产的基础,其要求是生产要平稳、有序。供应链的生产系统其实是一套非常精细而复杂的系统,最怕的就是干扰,一旦由于内部原因或外部原因干扰,生产系统就容易造成紊乱。生产系统一旦紊乱,企业必然要付出失败成本,而且调整回来不容易,必须付出很大的代价。可是,外部市场千变万化,精益生产是如何做到均衡化生产的呢?奥妙就在于混流生产。通过混流生产,可以屏蔽掉外部的巨大变化对内部的干扰,使其对生产系统的影响降低到可以接受的程度。
实现准时化生产有三大工具:一是单件流动,二是节拍时间,三是拉式生产。所谓单件流动,就是通过流线化生产实现工件一件接着一件快速流动,杜绝一批产品在某工序生产以后才流动到下一个工序,消除中间库存和等待时间,缩短生产周期。什么是节拍时间呢?实施工序标准化作业,平均每一个标准作业所需要的时间称为节拍时间。拉式生产是用市场需求拉动企业生产,用完成品生产拉动部件和零件生产,进而拉动供应商生产。
自动化有两层意思:一是传统意义上的自动化,二是自动防错。传统意义上的自动化是指利用工装、夹具、装备、设施、软件、程序等来取代人工作业,或者是辅助人工作业。海尔从德国引进的自动化生产线,富士康用机器人减少一线用工等,这些都是自动化的例子。自动化的第二层意思就是自动防错。自动防错是精益生产的重要思想之一,自动防错技术是实现精益生产的重要技术手段。自动防错的思想最早出现在丰田佐吉发明的织布机中,为了防止断纱造成的次品损失,丰田佐吉发明了一旦断纱立即停机报警的防错装置,这一发明使防错思想和防错技术得到运用。
4 从纵向一体化到横向一体化
随着企业发展规模壮大,有些企业为了更好地控制供应链的稳定性、成本和协作效率,采取了纵向一体化的策略,即兼并原来的供应商或自营、经销商。但是,这种小而全、大而全的管理模式,只考虑本企业内部资源的最优利用,并未跨越企业边界,在产业竞争环境中考虑是否具有最大优势。
后来,很多企业意识到这个问题,在激烈的市场竞争中,一体化企业中多个子公司并无足够的市场竞争力,全依赖核心公司养活,反而拖累了企业整体的健康发展。于是,这些企业开始重组减负,剥离非核心产业,转而整合企业外部资源快速响应市场,本企业专注于核心能力——产品方向和市场。这种横向一体化的模式同样会重视上下游供应商的管理,但不再采取兼并的方式来运营,只通过商业联盟、战略合作、外包等非股权手段来控制。
不过,纵向一体化和横向一体化是可以相互转化的,纵向一体化的企业会向横向一体化转变,横向一体化发展到一定程度的企业也可能会实施纵向一体化。这主要取决于供应链的特点以及现状。一般来说,如果上下游的企业越来越成为制约企业发展的瓶颈,或者有重大风险,企业会考虑实施纵向一体化。例如,汽车公司一般会自建发动机厂,葡萄酒商大多拥有自己的庄园。另外,如果上下游利润率较高,而企业又具备一体化的实力,同样会选择实施纵向一体化。所以,横向一体化与纵向一体化本身没有绝对的好坏之分,只是单纯追求大而全的纵向一体化的时代已经过去,更加灵活、高效的横向一体化越来越成为趋势。
5 建设一体化供应链
供应链是为满足顾客需求而组成的,是指从供应商的供应商、供应商,到制造企业、销售公司,再到经销商、顾客、顾客的顾客等整条产业链,如图4所示。供应链对顾客要求做出反应,按顾客提出的数量和时间要求提供适当的商品和服务。它由贯穿整条链的物流、信息流、资金流组成。

图4 供应链模型
供应链管理关注的是整体效率最大化,即及时正确的数字化信息流、连续的物流以及各方满意的资金流。它追求全供应链的产品实现成本最低化,而不仅仅是单个企业成本最优。事实上,只有全链成本最优,单个企业的效益才能最大化,因为任意一个环节的成本浪费,都会以交易价格、质量损失、缺货损失等方式转嫁给其他企业。对于库存的管理,同样也要实现全供应链式的考虑,既能满足客户需求又能降低供应链成本,所以要求全链库存可视化,这样才能避免重复设置。
但是,想要实现库存可视化,前提条件是实现供应链信息共享,这就要求供应链上各企业既要有信息共享的意愿,又要有实现信息共享的技术手段。所以,供应链管理的一大课题是研究如何塑造新型的合作关系,将供应链作为一个整体来经营,使供应链企业成为战略合作关系。