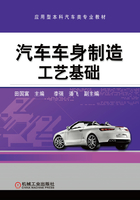
第四节 车身制造技术的发展
一、车身新材料与新工艺的应用
1.车身材料发展
为兼顾轻量化与碰撞安全性,普通钢板和管材用量逐渐减少,而高强度钢用量增加。同时,铝合金和塑料及其复合材料的用量也增加较快,但价格较高制约其进一步扩大应用。目前,车身中已采用的轻量化材料主要有高强度钢、铝合金、复合材料、塑料、镁合金等。下面将对各种材料的优缺点、力学性能、加工工艺与结构设计方法、经济性和轻量化效果进行分析。表1-3列出了车身常用各种轻量化材料性能比较。由于数据来源不一,表中数据仅供参考。
表1-3 车身常用各种轻量化材料性能比较

车身外板材料的选择主要考虑喷漆烘烤后具有高的屈服强度,能抵抗冲击,同时具有耐腐蚀、抗老化特性,并在成形后有好的形状冻结性。车身内板由于形状复杂,需要具有较好的拉延成形性以及与其他零件之间较好的连接特性。
(1)高强度钢 高强度钢是指屈服强度为210~550MPa的钢,屈服强度超过550MPa的为超高强度钢。国际钢铁协会(IISI)《先进高强度钢应用指南(第三版)》中将高强度钢分为传统高强度钢(CHSS)和先进高强度钢(AHSS),传统高强度钢主要包括碳锰(C-Mn)钢、烘烤硬化(BH)钢、高强度无间隙原子(HSS-IF)钢和高强度低合金(HSLA)钢。AHSS主要包括双相(DP)钢、相变诱导塑性(TRIP)钢、马氏体(M)钢、复相(CP)钢、热成形(HF)钢和孪晶诱导塑性(TWIP)钢。AHSS的强度较高,主要应用于汽车结构件、安全件和加强件,如A/B/C柱、车门槛、前后保险杠、车门防撞梁、横梁、纵梁、座椅滑轨等零件。先进高强度钢具有较低的屈强比、较高的应变分布能力和较好的应变硬化特性,且力学性能更加均匀、回弹量波动小。同时,其碰撞吸能性较好,疲劳寿命也较高。
目前,钢铁材料在汽车车身上的使用仍保持相对稳定的主导地位,但是其内部结构已发生很大变化。主要变化趋势是:高强度钢的用量将有较大增长,而中、低强度钢的比例将会逐步下降。例如,北美开发的PNGV-Class级轿车,其车身全部采用高强度钢,质量只有218kg,与全铝车身相当。
汽车使用的高强度钢主要为板材与管材,车身上以板材为主。此外,采用液压成形技术生产的高强度钢构件也越来越多,如发动机托架、散热器支架、仪表板横梁、座椅骨架以及轻型车后桥壳和车架等。事实上,高强度钢已成为颇具竞争力的汽车轻量化材料,它在抗碰撞性能、耐蚀性能和成本方面较其他材料具有较大的优势。
(2)铝合金
1)铝合金的优点:
①具有高的比强度。
②由于具有良好的塑性,可以采用冲压的方法进行加工,基本上不改变结构就可以使用原来的钢板冲压件的模具,对现在生产中的车型可快速实现轻量化。
③可焊接,具有良好的耐蚀性,回收利用性好。
④弹性模量小,因而可以较好地吸收撞击能量(吸收冲击的能力是钢的两倍),有利于在发生事故时保证乘员的安全。
⑤密度小(约为钢铁的1/3),可使整车质心降低,对提高汽车行驶稳定性有利。同时,还可以带来累进效应,发动机和底盘都可以相应减轻。
2)铝合金的缺点:
①成形性还需继续改善。铝合金板材的局部拉延性不好,容易产生裂纹。如发动机舱盖内板因为形状比较复杂,为了提高其拉延变形性能采用高级铝合金,伸长率已超过30%,但仍比钢差,所以在结构设计时要尽可能地保证形状不突变,使材料容易流动以避免拉裂。
②尺寸精度不容易掌握,回弹难以控制,在形状设计时要尽可能采用回弹少的形状。
③因为铝的硬度比钢小,在生产和运输中的碰撞和各种粉尘附着等易使零件表面产生碰伤、划伤等缺陷,所以要对模具的清洁、设备的清洁、环境的粉尘、空气污染等方面采取措施,确保零件的完好。
④不能像钢板那样采用磁力搬运和传递,要设计新的方案。
(3)镁合金
1)镁合金的优点:
①密度小(约为钢的1/4,铝的2/3),比强度(强度与密度的比值)高。
②具有良好的压铸经济性、尺寸稳定性和机械加工性能,其板材的抗凹性也较强。
③镁是地球表面含量丰富的金属元素。
④吸振性好,受冲击载荷时吸能性也较好。
2)镁合金的缺点:
①抗盐水腐蚀性差,与钢接触易产生电化学腐蚀。
②疲劳强度比铝合金和钢差,铸造的综合成本比铝合金高。
③焊接性差,硬度低。
近年来镁在汽车中的应用一直以较快的速度增长,尽管目前全球每辆汽车镁合金的平均用量仍不高,但是汽车用镁正以年均约20%的速度迅速增长,汽车上使用的镁压铸件对减小质量和提高性能十分有利,镁合金已成为汽车材料技术发展的一个重要领域。图1-25所示为用镁合金制造的汽车零件。
(4)塑料及复合材料件设计 塑料由于质量小、抗疲劳、易成型,在汽车内饰中有广泛应用。其优点是可将复杂零件做成一体,质感好。但缺点是易老化、难回收。
车身塑料主要采用注塑成型。其过程为:颗粒状的高分子材料(塑料)经过注塑机螺杆的挤压和加热,成为熔融状态的、可以流动的熔体。在螺杆的推动下,塑料熔体通过注塑机喷嘴,模具的主流道、分流道和浇口进入模具型腔,成型出具有一定形状和尺寸的制品。

图1-25 用镁合金制造的汽车零件
目前注塑成型法已在整个仪表板、油箱、保险杠、轮罩内衬、车顶、车门、转向盘、行李舱盖等零件制造中得到应用。
为进一步提高塑料的力学性能,以塑料为基体的复合材料逐渐得到更多的应用。
复合材料是指由两种或两种以上不同性质的组分材料,通过复合工艺,在宏观上组成具有新性能的多相材料。其中有一相是连续的,称为基体相,另一相为分散的,被基体包容,称为增强相,它们之间的交界面称为界面相。由于复合过程的物理或化学变化,各组分材料通过彼此在性能上取长补短,使复合材料的综合性能优于原组成材料而满足各种不同的要求。
复合材料的特点:
1)轻质高强。普通碳钢的密度为7.8g/cm3,玻璃纤维增强树脂基复合材料的密度为1.5~2.0g/cm3,只有普通碳钢的1/5~1/4,比铝合金的密度还要小,而机械强度却超过普通碳钢。若按比强度计算,玻璃纤维增强的树脂基复合材料不仅大大超过碳钢,而且可超过某些特殊的合金钢。碳纤维复合材料、有机纤维复合材料具有比玻璃纤维复合材料更低的密度和更高的强度,因此具有更高的比强度。
2)耐撞击,断裂韧度高。玻璃纤维增强复合材料的抗撞击断裂能力是钢的5倍以上。复合材料的抗撞击断裂能力要比一般的金属材料强得多。
3)减振、隔声性能好。复合材料高的自振频率避免了结构工作状态下因共振而引起的早期破坏。同时,复合材料中的纤维与黏弹性聚合物基体界面具有吸振能力,因此其振动阻尼很高。对相同形状和尺寸的梁进行的试验可知,铝合金梁需9s才能停止振动,而碳纤维复合材料梁只需2.5s就能停止振动。此外,复合材料的抗声振特性也是很好的。用复合材料制成的汽车车身,具有良好的减振、隔声效果,从而改善了乘坐舒适性。
4)设计性好。复合材料可以根据不同的用途要求,灵活地进行产品设计,具有很好的设计性。对于结构件来说,可以根据受力情况合理布置增强材料,以达到节约材料、减小质量的目的。对于有耐腐蚀性能要求的产品,设计时可以选用耐腐蚀性能好的基体树脂和增强材料,对于其他一些性能要求,如介电性能、耐热性能等,都可以方便地通过选择合适的原材料来满足。复合材料良好的设计性还可以最大限度地克服其弹性模量、层间剪切强度低等缺点。
5)电性能好。复合材料具有优良的电性能,通过选择不同的树脂基体、增强材料和辅助材料,可以将其制成绝缘材料或导电材料。
6)耐腐蚀性能好。聚合物基复合材料具有优异的耐酸性能、耐海水性能,也能耐碱、盐和有机溶剂,因此,它是一种优良的耐腐蚀材料,用其制造的化工管道、储罐、塔器等具有较长的使用寿命和极低的维修费用。玻璃纤维增强的聚酯基复合材料的耐腐蚀性能比金属材料好很多,这就从根本上解决了作为汽车车身覆盖件材料的耐腐蚀问题。
7)热性能好。玻璃纤维增强的聚合物基复合材料具有较低的导热系数,只有金属的1/1000~1/100,是一种优良的绝热材料。选择适当的基体材料和增强材料可以制成耐烧蚀材料和热防护材料。汽车车身外板覆盖件采用玻璃纤维增强的SMC材料,使用温度可以达到200℃,并可在较宽的温度范围内保持尺寸的稳定和原有的外形。
8)工艺性能优良。纤维增强的聚合物基复合材料具有优良的工艺性能,可以通过缠绕成形、接触成形等复合材料特有的工艺方法生产制品。它能满足各种类型制品的制造需要,特别适合于大型、形状复杂、数量少制品的制造。能用模具制造的复合材料构件,可一次成形,从而减少了零部件、紧固件和接头的数目,并可节省原材料和工时。
9)老化现象。在自然条件下,由于紫外线、湿热、机械应力、化学腐蚀的作用,会导致复合材料的性能变差,即发生所谓的老化现象。复合材料在使用过程中发生老化现象的程度与其组成、结构和所处的环境有关。
目前塑料及其复合材料主要应用于车身、仪表板、前后保险杠、顶篷、座椅、车轮罩以及油箱、散热器冷却液室等部件。热固性复合材料在车顶、行李舱盖、翼子板、车身外覆盖件上有一些应用;热塑性复合材料在吸能保险杠、前端框架、仪表板骨架、备胎室、车门骨架、车身底部护板有应用。此外,GMT材料也有很多应用。
碳纤维增强复合材料是制造汽车覆盖件的非金属材料,在减小车身质量的同时,也能保持防撞性能。目前,宝马(BMW)公司已在其开发的Z-9、Z-22车中大量采用碳纤维增强复合材料车身结构件,2003年M3系列车型上的顶盖和车身结构部件采用碳纤维增强复合材料。大众汽车公司在“2L车”CC1研究项目中,应用了较多的碳纤维复合材料,其中用于车身的比例高达45%。由于目前碳纤维的价格偏高,碳纤维增强复合材料车身仅仅是在高档车型或小批量车型上得到实际应用,今后随着大丝束碳纤维价格的进一步下降,预计将应用于更多的车型。可以说,未来潜在市场前景巨大。
2.车身成形与连接工艺发展
(1)液压成形和内高压成形 液压成形是一种板料柔性成形技术。它采用液态的水、油或黏性物质作为传力介质,代替凹模和凸模,使坯料在传力介质的压力作用下,贴合凸模或凹模而成形,是用于形状复杂、强度高、成形性能差的材料的理想成形方法。液压成形已用于钢板和铝合金板成形。
内高压成形(Tube Hydro-Forming,THF)是在钢管内增加轴向力和内压力制造空心闭合截面结构部件的技术,适合于用碳钢、特殊钢、不锈钢、铝合金、铜合金等材料制造的几何形状复杂的空心件(如变径管、空心变截面梁)。其原理是:先将管材置于一定形状的模具中,在管件内部加入高压流体(目前主要以水为主),辅以轴向施加压力补偿,把管料压入模具腔体内成形。其成形所需的液压力一般约200MPa,特殊状况下甚至高达400MPa。其成形原理及成形后的零件形状如图1-26所示。内高压成形已在汽车A柱、B柱、仪表板横梁、车顶梁、侧门横梁、车架、散热器托架和发动机托架零件上应用。

图1-26 金属管液压成形原理与成形后零件
1—管坯 2—上模 3—轴向压头 4—零件 5—下模
内高压成形技术和传统的金属板冲压点焊成形相比具有如下特点:
1)一次成形,避免了连接。汽车上使用管件液压成形的空心结构件可使质量减小20%~30%。
2)减少半成品零件数量。在成形过程中可一次加工出如发动机托架、顶盖板架、门框等大型复杂形状工件。与冲压焊接件相比,副车架零件由6个减少到1个;散热器支架零件由17个减少到10个。
3)降低模具费用。仅需要一套模具,而冲压后再焊接则需要多套冲压模具。
4)减少后续机械加工和组装焊接量。以散热器支架为例,焊接点由174个减少到20个,制造道次由13道减少到6道,生产效率提高66%。
5)提高强度、刚度及疲劳特性。成形过程中液体具有冷却作用,使工件被“冷作强化”,获得比一般冲压加工更高的工件强度。
6)降低生产成本。某公司对已应用的产品进行分析,管件液压成形件比冲压焊接件成本平均降低15%~20%,模具费用降低20%~30%。
7)创新性。应用于新产品设计开发。
(2)激光拼焊板 拼焊板技术主要用于汽车工业,近几年发展很快。拼焊板技术原来是为解决板材宽度不足的问题的,目前则大量用于将不同强度和不同厚度或不同表面处理状态的零件毛坯通过激光焊连成一体,然后一次冲压成形,减小了模具数量和后续工序数,提高了效率,保证了零件生产和装配质量,减少了材料消耗,减小了质量,也有利于今后的回收。例如,一辆汽车采用拼焊板后零件的质量可降低24%,零件数减少19%,焊点数减少49%,生产时间降低21%。
拼焊板技术是目前满足车身零部件各部位功能要求、材料选择、板材尺寸、焊缝位置、成本、质量、强度和稳定性的综合优化的有效工艺技术。拼焊板的焊接方法有激光焊、电阻辊压焊、感应焊和电子束焊等。激光拼焊是目前较受欢迎的一种。它利用激光的高能量熔化钢板,达到焊接的目的,具有疲劳强度高、焊缝硬度增加、影响范围小、焊缝窄、表面平、接头塑性好、焊接时间短、成本稍低等优点,但设备投资较高。
目前,大部分车门内板都应用了激光拼焊技术,如图1-27所示。其关键技术包括板材厚度和材料品种的选择、焊缝位置的确定、冲压成形工艺成败的分析等。
图1-28所示为激光拼焊板与基板成形极限图,图中数据分别为钢板厚度与屈服强度。
可见,由于焊缝的存在,材料变形受到牵制,主应变明显降低。对于平面应变状态极限点,基板的主应变达44%,而拼焊板只有30%,说明焊缝处的成形性较母材降低,因此,焊缝位置应避开几何突变处以防主应变过大。从安全区的变形余裕度看,最大应变为14%,距离30%尚有16%的安全余裕度。
此外,变厚度板材轧制技术可有效避免不同厚度板材焊缝偏移及开裂问题。若将拼焊板或变厚度板用于热冲压成形还可进一步提高其成形性和冲击强度,可用于汽车A/B柱及防撞梁。
(3)托克斯(TOX)连接
托克斯连接是可塑性薄板的不可拆卸式冲压点连接技术。采用托克斯气液增力缸式冲压设备及托克斯标准连接模具,在一个气液增力的冲压过程中,依据板件本身材料的挤压塑性变形,而使两个板件在挤压处形成一个互相镶嵌的圆形连接点,由此将板件点连接起来(图1-29),该工艺与点焊及铆接工艺在性能、费用、工艺过程等方面的对比见表1-4。

图1-27 采用激光拼焊技术的车身侧壁零件

图1-28 激光拼焊板与基板成形极限图
FLD0—应变为0的平面应变点 εmin—次应变

图1-29 托克斯连接原理图
表1-4 三种连接方式比较

二、车身生产自动化与柔性制造技术的应用
随着电子技术、计算机技术、机器人技术和人工智能技术的迅速发展,车身制造技术也进入了快速发展阶段。汽车消费市场需求的个性化和多样化,使汽车制造过程从传统的单一品种、大批量生产向多品种、中小批量生产转化。生产的批量性特点趋于复杂,安装零件的品种、数量进一步增多,对零部件的接收、保管、供给、装配作业指导等都提出了新的要求。
1.机器人技术
随着机器人的功能和控制技术的发展,机器人被广泛地应用到了各汽车公司的生产线上。机器人的使用,不仅减轻了工人的劳动强度,使装配厂里的人数大大减少,还可以减少故障和事故的发生,提高劳动生产率。如英国罗孚集团的装配厂使用的风窗玻璃安装系统,装备了带有激光器的机器人、摄像机和电子计算机。首先,摄像机确定车身位置,然后按照控制器的指令,两台机器人举起准备好的风窗玻璃送到检查工位,检查工位上配备的视觉系统计算机检查风窗玻璃的形状和尺寸,在风窗玻璃与所要求的参数相适应时,机器人即可将风窗玻璃安装到窗框中。国内的一些汽车公司也将机器人技术应用到了汽车车身制造和装配线上,图1-30所示为车身冲压自动化线,图1-31所示为车身焊接自动化线,图1-32所示为汽车装配机器人。

图1-30 车身冲压自动化线

图1-31 车身焊接自动化线

图1-32 汽车装配机器人
2.柔性生产装配线
柔性生产装配线是指能够同时满足一个或多个系列汽车产品生产要求,可以灵活改变夹具及运行方式,以适应无法预知的产品更新变化后的同类汽车产品装配需要的生产线。因此,企业要利用一次改造在一个相当长的时期内满足日益变化的多种车型混线生产的要求,同时又具有高的生产率,唯一的途径就是采用可以满足大量生产要求的柔性装配线。图1-33所示为德国宝马汽车公司的柔性装配线。柔性装配线不仅能满足和适应生产工艺和产品迅速变化的要求,还可以节省人力,提高产品质量。柔性装配线具有以下特点:

图1-33 宝马汽车柔性装配线
1)灵活的运行速度,可以适应不同生产节拍要求。
2)积放功能,使装配工时具有弹性。
3)被输送的产品能在任意位置停止,以满足不同产品、不同装配内容的不同操作要求,并便于实现自动化装配。
4)具有可编程操作控制系统。
5)夹具具有灵活的装夹方式和支撑方式,能适应多品种的装配要求。
在汽车装配生产中,柔性装配输送线的主要形式有积放式悬挂输送机、自动葫芦输送机和滑撬式输送系统。
3.模块化装配
模块化装配不仅可以大大减少总装线上的装配时间、降低生产成本、提高产品的可靠性,而且便于实现自动化装配,图1-34所示为模块化装配线。德尔福公司是模块化供应的倡导者和领先者,德尔福公司首先提出了模块化的新概念,并率先向奔驰公司在美国生产的M级车供应前座舱模块。模块化装配结构一般包括:
1)车门模块。在车门分装线上,以内板为中心将门锁、玻璃、玻璃升降器及密封护板等用螺栓安装于其中部,再将其与车门外把手、车门铰链、密封条及玻璃滑轨安装在一起,形成车门模块,然后再将其装到车身上。
2)仪表板模块。在模块骨架上安装仪表板、空调、离合器踏板、制动踏板及转向柱等,分装好后检查仪表和开关的技术性能,然后装到车身内。
3)底盘部件模块。将分装好的发动机和变速器总成、前悬架总成、后悬架总成、传动轴、排气管、油箱等底盘部件在线下合装好后,再装入车身。
4)车头模块。指安装于车身前端覆盖件上的前照灯、防雾灯、喇叭、发动机舱盖锁和散热器罩等。

图1-34 模块化装配线
三、车身尺寸精度与质量控制技术
车身精度主要是指车身零件的尺寸精度、几何精度和装配精度。也就是说,除了零件的外形精度要求外,还须有安装硬点的装配尺寸精度要求。尤其是作为装配基础的部件,如地板总成、门内板分总成等,是车身其他部件或总成的装配基础。装配尺寸精度是由装配夹具来保证的,必须严格控制装配夹具的尺寸精度,这样才能保证车身总装后的尺寸精度,如门与门框的配合间隙、车身表面零件接缝处的齐平度等。所有零件的设计公差和装配调整公差都要制定得合理。有关车身工艺分块、产品定位参考点(主控制点)的逐级设计及车身制造精度分解体系等技术方法的掌握都至关重要。每个零件的设计、制造、检测和装配都要努力做到在统一的定位参考系统下进行,这样才能够保证车身的整体精度。可见,提高车身产品尺寸精度必须从产品设计开始,并贯穿于整个产品开发过程。图1-35所示为国内某整车生产厂的车身制造激光在线测量系统,采用机器人式在线检测装置对焊接车身部件进行100%非接触式激光测量,对生产过程的工艺状态进行实时掌控,从而实现对产品质量的过程控制。

图1-35 车身制造激光在线测量系统
1.车身制造“2mm工程”
(1)概述 车身工程是个庞大而复杂的系统工程,从设计到制造的每个阶段都影响车身的综合尺寸精度。例如,车身设计的尺寸偏差,冲压工艺参数、模具磨损、回弹等形成的冲压件尺寸偏差,装配夹具定位、夹紧元件磨损或夹具设计不合理形成的装配件尺寸偏差,焊接规范不合理或材料性能问题带来的焊接变形等,都会影响车身的综合尺寸精度。
为满足大量生产时零部件的互换性并满足客户对产品的要求,车身产品尺寸精度问题一直困扰汽车行业。尤其是在当今结构轻量化的要求下,为了减小质量,略有超载或制造偏差时,就可能丧失功能,失去安全性和耐久性。例如,车门与门框的配合偏差直接影响车门的关闭性能和密封性,引发风噪声,影响外观,进而影响产品价值,失去市场竞争力。20世纪80年代末,美国轿车车身的综合尺寸偏差为7~8mm,明显低于日本的2mm水平,因此失掉了近30%的国内市场份额。在这种情况下,20世纪90年代初,美国开展了车身制造“2mm工程”研究,在短短三年内就使车身制造水平赶上了世界先进水平,制造偏差缩减到2mm,迅速夺回了市场份额。
汽车产品“2mm工程”就是从系统的观点出发,对汽车产品采用车身制造综合误差指数,即六倍标准差“6σ”来控制车身制造质量,从而用最经济的制造成本提高汽车产品的整体质量。这个综合误差指数不是车身制造质量测量数据的实际偏差,而是车身制造尺寸稳定性指标系统分析后的综合评价。目前,国外汽车企业不但在整车制造上应用“2mm工程”的原理,而且在零部件制造上也应用“2mm工程”的原理。可以说该工程是一个国家制造业技术水平的综合反映。
“2mm工程”的本质是建立数据驱动的制造质量控制体系,通过对制造数据建模分析来识别车身制造尺寸偏差源,保证车身制造工艺的稳定性,最终提高整车的配合精度。其核心是采用先进的车身测量技术,建立从冲压工艺、加工装备到装配过程协调一致、高效的测量系统,并通过数据分析和积累,将人为的经验管理上升到科学管理。
(2)“6σ”质量工程 在三坐标测量机(Coordinator Measuring Machine,CMM)坐标测量系统中,一批白车身上,同样的一个尺寸检测点所测得的数据可被认为是一个随机变量,并且大量的实践经验与理论分析表明,测量偏差服从正态分布。若随机变量x服从正态分布,则x的概率密度为:

式中 μ——均值,;
σ——标准差。

f(x)曲线(图1-36)有如下特点:
1)曲线对称于x=μ。
2) f(x)最大值在x=μ处,为。
3)在(-∞,μ)内单调递增,在(μ,+∞)内单调递减。

图1-36 尺寸数据的正态分布
经过计算,分别在μ附近σ、2σ、3σ范围内对f(x)积分,有下面的等式:

式(1-3)表明,在正态分布下,几乎所有的点都落在6σ的范围内。
因此,如果产品某检测点名义尺寸为x0(=μ),按正态分布的原则,其公差可取为±3σ,如图1-37所示,分等级如下:
1)|x-x0|≤Δx/3为A级精度,约占68.3%(优)。
2)Δx/3<|x-x0|≤2Δx/3为B级精度,约占27.2%(良)。
3)2Δx/3<|x-x0|≤Δx为C级精度,约占4.2%(合格)。
4)|x-x0|>Δx为D级精度,约占0.3%(不合格)。
可见,σ是衡量测量数据稳定性或重复性的重要参数。“2mm工程”的实质就是控制6σ≤2mm。

图1-37 测量数据等级分布特性
2.车身产品尺寸管理
为了保证产品质量,各大汽车公司都设有尺寸管理部门,其主要任务是将客户对产品质量的要求转变为尺寸目标,包括总体尺寸和精度(Global Dimensioning and Tolerance,GD&T),将精度目标分派到各级,制订定位参考策略并进行精度优化等。
车身制造精度问题从产品的开发阶段就要考虑。从设计到制造的每个工艺过程,都要围绕总目标(例如“2mm工程”)加以落实,才能保证车身的总体装配精度。这就要求设计部门、生产部门和质量检验部门协同起来进行产品尺寸管理,共同开发创建产品的质量体系。