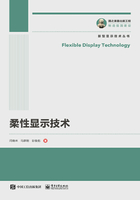
4.1 柔性工艺概要
柔性显示工艺目前可以套用现有的刚性显示板对板(Sheet to Sheet,S2S)量产工艺,加快可弯曲显示屏的商品化。现有曲面手机、折叠手机的柔性显示屏制作的主流工艺,均为使用涂覆柔性薄膜的载体玻璃,采用硬板量产制程,最后将载体玻璃分离的方法。柔性薄膜可以是金属薄膜、塑料薄膜、弹性体薄膜等,主流柔性薄膜是聚酰亚胺(PI)塑料薄膜。柔性显示的长远目标是实现卷对卷(Roll to Roll,R2R)、全溶液、非真空制程,降低柔性显示的制造成本。
柔性显示的制作,除柔性衬底的选择和处理外,还面临在柔性衬底上成膜、对柔性面板进行切割和封装等工艺难题。现有的硬式面板的制造流程采用化学气相沉积法、物理气相沉积法、溅射沉积法等工艺,在玻璃基板上沉积半导体与导体薄膜,再利用曝光、显影技术搭配刻蚀工艺制备组件各部的细微图案。OLED的有机发光材料以蒸镀方式沉积,搭配金属掩模,达到RGB三原色子像素的定位,其中金属掩模对位精度需达±5μm。刚性显示采用玻璃盖板加上封装胶的传统封装方式,柔性显示则采用一层或多层薄膜封装方式。
柔性显示技术的产业化推进,离不开索尼、三星、LG等公司的技术研发和产品引领。2010年,日本索尼公司推出了一款4.1英寸OTFT(有机薄膜晶体管)驱动的全彩 OLED 屏,该屏的屏幕厚度只有 80μm,可缠绕在半径为4mm的圆柱体上。2012年,韩国 LG公司研发出一款6英寸柔性E-ink显示屏,这款显示屏质量只有14g,与相同尺寸的玻璃屏相比更薄、更轻。2013年,三星公司和 LG 公司均发布了可弯曲屏幕 OLED 电视,通过屏幕弯曲增强了画面的景深效果,创造出更加逼真的视觉体验。随后,三星公司于2014年发布Galaxy Note Edge手机,开创柔性显示在手机产品的应用。随着柔性显示技术的进一步发展,柔宇、三星、华为等公司先后发布了可折叠手机,将柔性显示屏幕从静态曲面提升到了全新的动态弯曲高度。
日本精工爱普生与索尼公司是柔性显示技术的先驱,这两家公司使用转移工艺(Transfer Process),在玻璃基板上制作低温多晶硅薄膜晶体管(Low Temperature Poly-Silicon Thin Film Transistor,LTPS TFT)后再转贴到塑料基板上。精工爱普生公司运用自己发展的 Surface Free Technology by Ablation/Annealing(SUFTLA)技术剥离 TFT 阵列与玻璃基板,通过两次转贴贴到塑料基板上。索尼公司用氢氟酸(HF)将玻璃基板刻蚀去除后,通过两次转贴贴到塑料基板上。使用转移工艺的好处是所有步骤均为已成熟制程,但工序较多且使用过的玻璃基板无法回收,因此生产成本较高。
韩国三星公司首先将聚酰亚胺柔性薄膜固着在载体玻璃上,然后在柔性薄膜上制作 LTPS TFT 并进行 OLED 相关工序,最后通过激光剥离技术将柔性薄膜及其上制作的TFT、OLED等器件从玻璃基板上一同剥离下来,形成柔性显示屏幕。和刚性 OLED 显示屏幕工艺路线相比,除增加柔性薄膜涂覆、剥离工艺外,此流程的核心技术还包括低于450℃的LTPS TFT工艺、更具柔性的OLED薄膜封装工艺、柔性屏模组工艺等。
随着柔性屏的技术突破,在载体玻璃上涂覆柔性薄膜的硬板工艺成为目前主流的工艺路线。作为未来柔性显示工艺方向的 R2R 技术,目前可弯曲AMOLED制程各主要步骤皆已有R2R的验证,包括R2R溅镀与蒸镀(导电层、介电层及有机层沉积)、R2R化学沉积(半导体薄膜沉积)、R2R微影(组件各部图案化)、R2R 涂布与喷涂(各层材料的溶液涂布与图案化)、R2R 薄膜封装等。
然而,多数采用R2R步骤的柔性屏尚无法量产,并且其加工面积仍远小于硬式面板制程的加工面积。原因除R2R技术尚未成熟外,还有材料性质尚未最佳化,以及喷涂(喷墨、网印和压印等)图案化精准度不佳。因此,在R2R工艺开发上,除设备的持续开发外,各种新颖材料与图案化技术(可涂布式金属氧化物半导体、可涂布式有机半导体、可涂布式导电薄膜、可涂布式有机发光材料、非真空式薄膜封装技术和自组装技术等)将是决定性的因素。