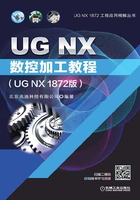
1.9 走刀路线的选择
在数控加工中,刀具(严格说是刀位点)相对于工件的运动轨迹和方向称为加工路线,即刀具从对刀点开始运动起,直至结束加工程序所经过的路径,包括切削加工的路径及刀具引入、返回等非切削空行程。走刀路线是刀具在整个加工工序中相对于工件的运动轨迹,不但包括了工序的内容,而且也反映出工序的顺序,它是编写程序的依据之一。确定加工路线时首先必须保证被加工零件的尺寸精度和表面质量,其次应考虑数值计算简单、走刀路线尽量短、效率较高等。
工序顺序是指同一道工序中各个表面加工的先后次序。工序顺序对零件的加工质量、加工效率和数控加工中的走刀路线有直接影响,应根据零件的结构特点和工序的加工要求等合理安排。工序的划分与安排一般可随走刀路线来进行,在确定走刀路线时,主要考虑以下两点。
(1)对点位加工的数控机床,如钻床、镗床,要考虑尽可能使走刀路线最短,减少刀具空行程时间,提高加工效率。
如图1.9.1a所示,按照一般习惯,总是先加工均布于外圆周上的八个孔,再加工内圆周上的四个孔。但是对点位控制的数控机床而言,要求定位精度高,定位过程应该尽可能快,因此这类机床应按空程最短来安排走刀路线,以节省时间,如图1.9.1b所示。

图1.9.1 走刀路线
(2)应能保证零件的加工精度和表面粗糙度要求。
当铣削零件外轮廓时,一般采用立铣刀侧刃切削。刀具切入工件时,应沿外轮廓曲线延长线的切向切入,避免沿零件外轮廓的法向切入,以免在切入处产生刀具的刻痕而影响表面质量,保证零件外轮廓曲线平滑过渡。同理,在切离工件时,应该沿零件轮廓延长线的切向逐渐切离工件,避免在工件的轮廓处直接退刀影响表面质量,如图1.9.2所示。
铣削封闭的内轮廓表面时,如果内轮廓曲线允许外延,则应沿切线方向切入或切出。若内轮廓曲线不允许外延,则刀具只能沿内轮廓曲线的法向方向切入或切出,此时刀具的切入切出点应尽量选在内轮廓曲线两几何元素的交点处。若内部几何元素相切无交点时,刀具切入切出点应远离拐角,以防刀补取消时在轮廓拐角处留下凹口,如图1.9.3所示。

图1.9.2 外轮廓铣削走刀路线

图1.9.3 内轮廓铣削走刀路线
对于边界敞开的曲面加工,可采用两种走刀路线。第一种走刀路线如图1.9.4a所示,每次沿直线加工,刀位点计算简单,程序少,加工过程符合直纹面的形成,以保证母线的直线度;第二种走刀路线如图1.9.4b所示,便于加工后检验,曲面的准确度较高,但程序较多。因此曲面零件的边界是敞开的,没有其他表面限制,所以边界曲面可以延伸,球头铣刀应由边界外开始加工。

图1.9.4 曲面铣削走刀路线
图1.9.5a、b所示分别为用行切法和环切法加工凹槽的走刀路线,而图1.9.5c是先用行切法,最后环切一刀光整轮廓表面。所谓行切法是指刀具与零件轮廓的切点轨迹是一行一行的,而行间的距离是按零件加工精度的要求确定的。环切法则是指刀具与零件轮廓的切点轨迹是一圈一圈的。这三种方案中,图1.9.5a所示方案在周边留有大量的残余,表面质量最差;图1.9.5b所示方案和图1.9.5c所示方案都能保证精度,但图1.9.5b所示方案走刀路线稍长,程序计算量大。

图1.9.5 凹槽的走刀路线
此外,轮廓加工中应避免进给停顿。因为加工过程中的切削力会使工艺系统产生弹性变形并处于相对平衡状态,进给停顿时,切削力突然减小会改变系统的平衡状态,刀具会在进给停顿处的零件轮廓上留下刻痕。为提高工件表面的精度和减小表面粗糙度,可以采用多次走刀的方法,精加工余量一般以0.2~0.5mm为宜。而且精铣时宜采用顺铣,以减小零件被加工表面粗糙度的值。