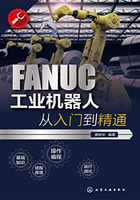
4.2 主要技术参数与选择
4.2.1 主要技术参数
(1)规格代号
谐波减速器规格代号以柔轮节圆直径(单位:0.1in)表示,常用规格代号与柔轮节圆直径的对照如表4.2.1所示。
表4.2.1 规格代号与柔轮节圆直径对照表

(2)输出转矩
谐波减速器的输出转矩主要有额定输出转矩、启制动峰值转矩、瞬间最大转矩等,额定输出转矩的、启制动峰值转矩、瞬间最大转矩含义如图4.2.1所示。

图4.2.1 输出转矩、启制动峰值转矩与瞬间最大转矩
额定转矩(rated torque):谐波减速器在输入转速为2000r/min情况下连续工作时,减速器输出侧允许的最大负载转矩。
启制动峰值转矩(peak torque for start and stop):谐波减速器在正常启制动时,短时间允许的最大负载转矩。
瞬间最大转矩(maximum momentary torque):谐波减速器工作出现异常时(如机器人冲击、碰撞),为保证减速器不损坏,瞬间允许的负载转矩极限值。
最大平均转矩和最高平均转速:最大平均转矩(permissible max value of average load torque)和最高平均转速(permissible average input rotational speed)是谐波减速器连续工作时所允许的最大等效负载转矩和最高等效输入转速的理论计算值。
谐波减速器实际工作时的等效负载转矩、等效输入转速,可根据减速器的实际运行状态计算得到,对于图4.2.2所示的减速器运行,其计算式如下。

图4.2.2 谐波减速器实际运行图
Tav=
Nav=NoavR=R(4⁃1)
式中 Tav——等效负载转矩,N·m;
Nav——等效输入转速,r/min;
Noav——等效负载(输出)转速,r/min;
nn——各段工作转速,r/min;
tn——各段工作时间,h、s或min;
Tn——各段负载转矩,N·m;
R——基本减速比。
启动转矩(starting torque):又称启动开始转矩(on starting torque),它是在空载、环境温度为20℃的条件下,谐波减速器用于减速时,输出侧开始运动的瞬间,所测得的输入侧需要施加的最大转矩值。
增速启动转矩(on overdrive starting torque):在空载、环境温度为20℃的条件下,谐波减速器用于增速时,在输出侧(谐波发生器输入轴)开始运动的瞬间,所测得的输入侧(柔轮)需要施加的最大转矩值。
空载运行转矩(on no⁃load running torque):谐波减速器用于减速时,在工作温度为20℃、规定的润滑条件下,以2000r/min的输入转速空载运行2h后,所测得的输入转矩值。空载运行转矩与输入转速、减速比、环境温度等有关,输入转速越低、减速比越大、温度越高,空载运行转矩就越小,设计、计算时可根据减速器生产厂家提供的修整曲线修整。
(3)使用寿命
额定寿命(rated life):谐波减速器在正常使用时,出现10%产品损坏的理论使用时间(h)。
平均寿命(average life):谐波减速器在正常使用时,出现50%产品损坏的理论使用时间(h)。谐波减速器的使用寿命与工作时的负载转矩、输入转速有关,其计算式如下。
Lh=Ln(4⁃2)
式中 Lh——实际使用寿命,h;
Ln——理论寿命,h;
Tr——额定转矩,N·m;
Tav——等效负载转矩,N·m;
Nr——额定转速,r/min;
Nav——等效输入转速,r/min。
(4)强度
强度(intensity)以负载冲击次数衡量,减速器的等效负载冲击次数可按下式计算,此值不能超过减速器允许的最大冲击次数(一般为10000次)。
N=(4⁃3)
式中 N——等效负载冲击次数;
n——冲击时的实际输入转速,r/min;
t——冲击负载持续时间,s。
(5)刚度
谐波减速器刚度(rigidity)是指减速器的扭转刚度(torsional stiffness),常用滞后量(hysteresis loss)、弹性系数(spring constants)衡量。
滞后量(hysteresis loss):减速器本身摩擦转矩产生的弹性变形误差θ,与减速器规格和减速比有关,结构型式相同的谐波减速器规格和减速比越大,滞后量就减小。
弹性系数(spring constants):以负载转矩T与弹性变形误差θ的比值衡量。弹性系数越大,同样负载转矩下谐波减速器所产生的弹性变形误差θ就越小,刚度就越高。
弹性变形误差θ与负载转矩的关系如图4.2.3(a)所示。在工程设计时,常用图4.2.3(b)所示的3段直线等效,图中Tr为减速器额定输出转矩。

图4.2.3 谐波减速器的弹性变形误差
等效直线段的ΔT/Δθ值K1、K2、K3,就是谐波减速器的弹性系数,它通常由减速器生产厂家提供。弹性系数确定时,便可通过下式,计算出谐波减速器在对应负载段的弹性变形误差Δθ。
Δθ=(4⁃4)
式中 Δθ——弹性变形误差,rad;
ΔT——等效直线段的转矩增量,N·m;
Ki——等效直线段的弹性系数,N·m/rad。
谐波减速器弹性系数与减速器结构、规格、基本减速比有关,结构相同时,减速器规格和基本减速比越大,弹性系数也越大。但是薄饼形柔轮的谐波减速器,以及我国GB/T 30819—2014标准定义的减速器,其刚度参数有所不同,有关内容详见后述。
(6)最大背隙
最大背隙(max backlash quantity)是减速器在空载、环境温度为20℃的条件下,输出侧开始运动瞬间,所测得的输入侧最大角位移。我国GB/T 30819—2014标准定义的减速器背隙有所不同,详见国产谐波减速器产品说明。
进口谐波减速器(如哈默纳科)刚轮与柔轮的齿间啮合间隙几乎为0,背隙主要由谐波发生器输入组件上的奥尔德姆联轴器(Oldham’s coupling)产生,因此,输入为刚性连接的减速器,可以认为无背隙。
(7)传动精度
谐波减速器传动精度又称角传动精度(angle transmission accuracy),它是谐波减速器用于减速时,在图4.2.4的任意360°输出范围上,其实际输出转角θ2和理论输出转角θ1/R间的最大差值θer衡量,θer值越小,传动精度就越高。传动精度的计算式如下:
θer=θ2-(4⁃5)
式中 θer——传动精度,rad;
θ1——1∶1传动时的理论输出转角,rad;
θ2——实际输出转角,rad;
R——谐波减速器基本速比。
谐波减速器的传动精度与减速器结构、规格、减速比等有关;结构相同时,减速器规格和减速比越大,传动精度越高。

图4.2.4 谐波减速器的传动精度
(8)传动效率
谐波减速器的传动效率与减速比、输入转速、负载转矩、工作温度、润滑条件等诸多因素有关。减速器生产厂家出品样本中所提供的传动效率ηr,一般是指输入转速2000r/min、输出转矩为额定值、工作温度为20℃、使用规定润滑方式下,所测得的效率值;设计、计算时需要根据生产厂家提供的如图4.2.5(a)所示的转速、温度修整曲线进行修整。
谐波减速器传动效率还受实际输出转矩的影响,输出转矩低于额定值时,需要根据负载转矩比α(α=Tav/Tr),按生产厂家提供的如图4.2.5(b)所示的修整系数Ke曲线,利用下式修整传动效率。

图4.2.5 传动效率修整
ηav=Keηr(4⁃6)
式中 ηav——实际传动效率;
Ke——修整系数;
ηr——传动效率或基本传动效率。
4.2.2 谐波减速器选择
(1)基本参数计算与校验
谐波减速器的结构型式、传动精度、背隙等基本参数可根据传动系统要求确定,在此基础上,可通过如下方法确定其他技术参数、初选产品,并进行技术性能校验。
① 计算要求减速比 传动系统要求的谐波减速器减速比,可根据传动系统最高输入转速、最高输出转速,按下式计算:
r=(4⁃7)
式中 r——要求减速比;
nimax——传动系统最高输入转速,r/min;
nomax——传动系统(负载)最高输出转速,r/min。
② 计算等效负载转矩和等效转速 根据式(4⁃1),计算减速器实际工作时的等效负载转矩Tav和等效输出转速Noav(r/min)。
③ 初选减速器 按照以下要求,确定减速器的基本减速比、最大平均转矩,初步确定减速器型号:
R≤r(柔轮输出)或R+1≤r(刚轮输出)
Tavmax≥Tav(4⁃8)
式中 R——减速器基本减速比;
Tavmax——减速器最大平均转矩,N·m;
Tav——等效负载转矩,N·m。
④ 转速校验 根据以下要求,校验减速器最高平均转速和最高输入转速:
Navmax≥Nav=RNoav
Nmax≥Rnomax(4⁃9)
式中 Navmax——减速器最高平均转速,r/min;
Nav——等效输入转速,r/min;
Noav——等效输出转速,r/min;
Nmax——减速器最高输入转速,r/min;
nomax——传动系统最高输出转速,r/min。
⑤ 转矩校验 根据以下要求,校验减速器启制动峰值转矩和瞬间最大转矩:
Tamax≥Ta
Tmmax≥Tmax(4⁃10)
式中 Tamax——减速器启制动峰值转矩,N·m;
Ta——系统最大启制动转矩,N·m;
Tmmax——减速器瞬间最大转矩,N·m;
Tmax——传动系统最大冲击转矩,N·m。
⑥ 强度校验 根据以下要求,校验减速器的负载冲击次数:
N=≤1×104(4⁃11)
式中 N——等效负载冲击次数;
n——冲击时的输入转速,r/min;
t——冲击负载持续时间,s。
⑦ 使用寿命校验 根据以下要求,计算减速器使用寿命,确认满足传动系统设计要求:
Lh=7000≥L10(4⁃12)
式中 Lh——实际使用寿命,h;
Tr——减速器额定输出转矩,N·m;
Tav——等效负载转矩,N·m;
Nr——减速器额定转速,r/min;
Nav——等效输入转速,r/min;
L10——设计要求使用寿命,h。

图4.2.6 谐波减速器运行图
(2)减速器选择示例
假设某谐波减速传动系统设计要求如下:
① 减速器正常运行过程如图4.2.6所示;
② 传动系统最高输入转速nimax=1800r/min;
③ 负载最高输出转速nomax=14r/min;
④ 负载冲击:最大冲击转矩500N·m,冲击负载持续时间0.15s,冲击时的输入转速14r/min。
⑤ 设计要求的使用寿命:7000h。
谐波减速器的选择方法如下。
① 要求减速比:r==128.6。
② 等效负载转矩和等效输出转速:
Tav==319(N·m)
Noav==12(r/min)
③ 初选减速器:选择日本Harmonic Drive System(哈默纳科)CSF⁃40⁃120⁃2A⁃GR(见哈默纳科产品样本)部件型谐波减速器,基本参数如下。
R=120≤128.6
Tavmax=451N·m≥319N·m
④ 转速校验:CSF⁃40⁃120⁃2A⁃GR减速器的最高平均转速和最高输入转速校验如下。
Navmax=3600r/min≥Nav=12×120=1440 (r/min)
Nmax=5600r/min≥Rnomax=14×120=1680 (r/min)
⑤ 转矩校验:CSF⁃40⁃120⁃2A⁃GR启制动峰值转矩和瞬间最大转矩校验如下。
Tamax=617N·m≥400N·m
Tmmax=1180N·m≥500N·m
⑥ 强度校验:等效负载冲击次数的计算与校验如下。
N==1190≤1×104
⑦ 使用寿命计算与校验:
Lh=7000=7000×
×
=7610≥7000
结论:该传动系统可选择日本Harmonic Drive System(哈默纳科)CSF⁃40⁃120⁃2A⁃GR部件型谐波减速器。