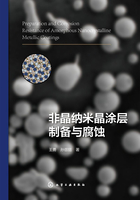
3.1 HVOF喷涂非晶涂层制备
热喷涂工艺对非晶相的形成有明显的影响。制备具有特定性能的HVOF喷涂涂层需要对HVOF喷涂过程、工艺参数与涂层结构性能之间的关系有一定的理解。HVOF喷涂涂层的性能在很大程度上受涂层结构的影响,而涂层结构又主要取决于颗粒撞击基体瞬间的物理和化学状态,比如喷射速率、颗粒温度、熔化以及氧化程度等。这些状态参数的变化与喷涂过程中的几个主要参数相关,如氧/燃气流量比、燃气流速、喷涂距离、送粉速率和粉末颗粒粒径等,这些因素之间往往还存在交互影响。
对于HVOF喷涂,喷枪是最为重要的设备,目前采用最多的喷枪主要是JP5000和DJ2700系列。它们之间最大的差别是采用了不同的送粉方式。其中,DJ2700采用的是轴向式送粉,具有相对较高的沉积效率和较好的颗粒熔化状态。在颗粒速度方面,JP5000的颗粒速度大致在625~875m/s之间,DJ2700的则在500~825m/s之间。对于颗粒温度,DJ2700通常略高于JP5000。
在涂层制备过程中,除喷涂方法和原始粉末外,喷涂工艺参数是影响涂层结构和性能的主要因素,其中氧气、燃气的流量、喷涂距离和送粉速率等参数对涂层的组织和性能影响较大。HVOF喷涂的送粉速率一般为20~80g/min,粉末粒子尺寸在5~45μm之间,喷涂距离在150~300mm之内。不同氧/燃气流量比对涂层的氧化状况、颗粒温度和熔化状态、涂层的致密度均有一定的影响[1,2]。喷涂距离的改变对颗粒的温度和速率也很敏感[3,4],进而影响孔隙率的变化。另外,送粉速率及颗粒尺寸决定颗粒的传热特性和加速行为[5],不同尺度粒子的熔化行为和速度是不同的[6]。这些工艺参数影响着颗粒温度场和速度场,决定了焰流和粉末粒子之间的动量和热量传输,进而影响涂层的各种性能[7]。因此,要想获得高质量的涂层须系统研究这些喷涂工艺参数对涂层结构与性能的影响。一直以来,对HVOF喷涂参数对涂层力学性能和电化学腐蚀行为影响的研究比较多,包括不锈钢涂层、陶瓷涂层和金属涂层[8,9]等。这些研究结果表明,燃气流速、送粉速率和喷涂距离极大地影响涂层的沉积结构。在喷涂形成的层状间隙处的金属氧化物恶化了涂层的化学均匀性,进而降低腐蚀性能。一般来说,腐蚀性能随氧化物含量的增加而降低。对于常规的金属涂层,高的孔隙率也是涂层腐蚀性能降低的关键因素,因为这些孔隙的存在有利于一些侵蚀性阴离子如Cl-的入侵,引起局部腐蚀。另外,利用热喷涂方法制备较厚非晶涂层时,晶化现象是很难避免的,从而导致非晶涂层中析出纳米晶相,这些晶化产物的存在可进一步提升涂层的硬度和强度。
对于非晶合金来说,由于其优异的耐蚀性是基于无晶界或位错的非晶结构,因此,非晶形成能力(GFA)是制备非晶纳米晶涂层首先考虑的因素。当然,非晶纳米晶涂层的腐蚀性能除与氧化物含量、孔隙率有关外,还与非晶含量密切相关。HVOF喷涂参数可以改变颗粒的冷却速率,所以也影响非晶形成能力。通常来说,一方面,高温时喷涂状的颗粒易发生氧化致使其化学成分不均匀,成分的不均匀性导致其化学成分偏离形成非晶的最佳成分,所以会降低非晶形成能力。另一方面,高温和高的颗粒速率又有利于形成致密的涂层结构[10]。这就面临一个问题,非晶含量和孔隙率两个相互矛盾的因素对腐蚀性能的影响如何去平衡?进而获得耐蚀性最优的非晶纳米晶涂层。迄今为止,只有极少量的研究集中于HVOF喷涂参数和非晶纳米晶涂层性能之间的关系。因此,进一步研究非晶结构和孔隙率对于非晶纳米晶涂层腐蚀性能的影响具有重要的实际意义。
下面主要介绍氧/燃气流量比(O/F)和送粉速率两个喷涂参数对铁基非晶纳米晶涂层结构、腐蚀性能和硬度的影响。
3.1.1 HVOF喷涂涂层制备过程
利用电磁感应炉,按名义成分配比(原子分数)的纯金属元素熔炼制备Fe54.2Cr18.3Mo13.7Mn2.0W6.0B3.3C1.1Si1.4母合金。熔炼之前,先进行配料。通过计算,将欲制备的母合金按成分进行元素配比称重,精确到0.1mg。非晶粉末通过工业气雾化法制备。工业气雾化法的反应条件为:控制过热度为98~102℃,真空度5Pa,雾化压力20MPa;粉末粒度主要集中在30~60μm。雾化设备主要由感应、加热、雾化喷粉、粉末收集与真空系统组成。真空度达到3~5Pa时,加热去除氧化皮后的母合金至完全熔化状态,然后,将熔体通过喷嘴释放到雾化腔体中。此时,高压(约8.1MPa)氩气在喷嘴末端将熔体雾化成小液滴,这些小液滴在腔体中快速冷却形成不同粒度的粉末。用不同目数的筛子对粉末进行筛分。通常,粉末被筛分成<45μm粒度范围。
采用美国Metco公司的DJ2700超音速热喷涂设备。基体材料选用304不锈钢。喷涂距离为225mm,喷涂厚度均为500μm,其他改变的喷涂参数见表3⁃1。
喷涂过程包括:喷涂前应进行物理处理,去除电焊疤、油灰、油渍、大块的氧化皮等杂物,可依据不同情况采用机械清理、擦拭和溶剂去油等方法清除;待喷涂表面应采用手工或机械方法去除毛刺和尖锐棱角,并打磨圆滑。然后进行化学清洗除油,除油后,经喷砂或喷丸除锈,其等级应达到GB 8923.4—2013规定的Sa 2.5级。严格按照喷涂工艺进行操作,每道喷涂完后待表面冷却至60℃以下,方可进行第二道喷涂,喷涂过程中要对每次喷涂质量进行检查。
表3⁃1 HVOF喷涂参数

注:压力为丙烷90psi,氧气150psi,空气105psi。1psi=6894.76Pa。
为了对比研究,制备了非晶条带(ribbon),条带样品通过熔体急冷法获得,所得条带厚度为40μm,宽度约2mm。
腐蚀性能测试在PAR Model 2273工作站上进行,采用三电极系统,工作电极为用环氧树脂封装的涂层。环氧树脂E44 100g,增塑剂(邻苯二甲酸二丁酯)5g,固化剂(乙二胺)8g。配制时环氧树脂和增塑剂先混合均匀,浇注前后加固化剂,24h后备用。腐蚀实验介质为1% NaCl溶液,包括开路电位测试(Eoc)、动电位极化曲线、循环极化曲线和电化学阻抗谱。开路电位监控时间为24h。利用日本JMS⁃6301 SEM观察喷涂涂层的组织结构和表面形貌。涂层样品的XRD在Rigaku D/max2400衍射仪上进行。涂层孔隙率在德国Leica MEF⁃4金相显微镜上用图像分析软件进行。用PerkinElmer DSC⁃7型高温差示扫描热量分析仪测试条带、涂层的DSC曲线。利用维氏显微硬度计MVK⁃H3对涂层进行显微硬度值测试,载荷300g,加载10s。
3.1.2 涂层喷涂结构和形貌表征
O/F比在喷涂过程中具有非常重要的影响,主要与涂层的熔化状态、氧化程度和孔隙率相关。不同O/F比(O/F=3.9、4.2、4.5和4.8)所制备涂层的表面及侧面特征见图3⁃1。由图可知,O/F比极大地影响了涂层的微观组织结构。未熔颗粒随O/F比的增加而呈降低趋势,见图3⁃1中(a)、(d)、(g)和(j),这主要与燃气和喷涂颗粒之间的热传递过程相关。实际上,O/F比是影响涂层质量的关键因素。O/F比太低时,未熔颗粒数量较多[图3⁃1(a)和(d)],从抛光后的表面也可以清晰看出一些未熔颗粒,见图3⁃1中(b)和(e)。O/F比太高时,容易引起颗粒氧化[图3⁃1(j)]。氧化对非晶结构的形成极为有害。
由图3⁃1中(b)、(e)、(h)和(k)中的灰色氧化物区域可以看出,氧化程度随O/F比的增加而增加。另外,涂层的孔隙率水平随O/F比的变化规律与未熔颗粒相似,随O/F比增加而降低,见图3⁃1中(b)、(e)、(h)、(k)和图3⁃1中(c)、(f)、(i)、(l)。因此,可以得出,涂层C4具有最低的孔隙率,但氧化程度最高。

图3⁃1 不同O/F比所制备涂层的SEM表面及侧面特征(数字表示孔隙率)
(a)~(c)O/F=3.9;(d)~(f)O/F=4.2;(g)~(i) O/F=4.5;(j)~(l)O/F=4.8
(a)(d)(g)(j)喷涂态表面;(b)(e)(h)(k)抛光表面;(c)(f)(i)(l)涂层侧面
不同送粉速率所制备涂层的表面及侧面特征见图3⁃2。送粉速率对涂层微观结构也具有同样重要的影响。由图3⁃2可知,送粉速率对涂层结构的影响与O/F比正好相反。未熔颗粒[图3⁃2中(a)、(d)、(g)和(j)]和孔隙率[图3⁃2中(c)、(f)、(i)和(l)]随送粉速率增加而增加,氧化程度[图3⁃2中(b)、(e)、(h)和(k)]则随之降低。
3.1.3 涂层物相分析
不同喷涂参数制备涂层的XRD图谱见图3⁃3。对于不同O/F比和送粉速率制备的涂层,XRD图谱均在40°~50°间呈现出一个漫散射峰,并伴随有个别尖锐峰。说明所制备的涂层主要为非晶结构,并含有少量纳米晶体相。形成这些纳米晶体相的原因是在制备涂层时,后

图3⁃2 不同送粉速率所制备涂层的SEM表面及侧面特征(数字表示孔隙率)
(a)~(c)20g/min;(d)~(f)30g/min;(g)~(i)40g/min;(j)~(l)50g/min
(a)(d)(g)(j)喷涂态表面;(b)(e)(h)(k)抛光表面;(c)(f)(i)(l)涂层侧面
序喷涂过程中的热量对基体局部有加热的作用。这种局部加热是涂层制备过程中不可避免的,尤其在涂层厚度增加的情况下。所以制备非晶涂层时,适当的厚度控制是保证涂层优异耐蚀性能的前提。图3⁃3(a)示出O/F比对涂层XRD的影响。随O/F比的变化,涂层中的非晶相含量差别不是很明显,只能通过DSC曲线来计算具体的非晶相含量值。由图3⁃3(b)可以看出,送粉速率过大时,晶体峰更为尖锐,说明过高的送粉速率不利于非晶相的形成。送粉速率过大,较多的未熔颗粒会在高温下发生晶化,致使涂层晶化相形成的概率也增大。
图3⁃4为不同喷涂参数所制备涂层的DSC曲线。由图可知,条带具有明显的固⁃固相变的放热峰。涂层中的放热峰积分面积明显低于条带,说明涂层中确实存在一定量的晶体相。通过比较晶化峰的热流积分面积,可估算出涂层中非晶相含量的多少。通过计算,涂层非晶相的含量对O/F比和送粉速率敏感。对于涂层C4、C3、C1和C2,非晶相含量分别为65.4%、70.6%、75.5%和78.9%;对于涂层C5、C4、C7、C6,非晶相含量分别为60.4%、65.4%、73.0%和78.1%。可见,涂层C2(O/F比=4.2)和C6(送粉速率=40g/min)具有最高的非晶相含量,说明在这两个工艺参数条件下,可以实现最大程度的非晶结构形成。

图3⁃3 不同参数制备涂层的XRD图谱

图3⁃4 不同参数制备涂层的DSC曲线
3.1.4 涂层显微硬度
不同参数条件下制备涂层的显微硬度如图3⁃5所示。可见,涂层的硬度随O/F比和送粉速率的变化也呈现出一定的规律性变化。随O/F比的增加,硬度从842HV增加至932HV。但增加程度不同,在O/F=4.2之前增加幅度较大,后随O/F比增加趋于平稳。相反,随送粉速率的增加,硬度则一直呈降低趋势。相似的是,在送粉速率小于40g/min时,硬度降低幅度较小,超过40g/min时则呈急剧下降趋势。

图3⁃5 涂层硬度随喷涂参数的变化
3.1.5 电化学腐蚀行为
涂层在1% NaCl溶液中浸泡24h的开路电位(Eoc)如图3⁃6所示。

图3⁃6 涂层在1% NaCl溶液中的开路电位(Eoc)
经过0.3h浸泡后,所有涂层的Eoc基本上呈现降低趋势,主要是由于涂层表面氧化物在Cl-作用下发生溶解所致。随后,所有涂层的Eoc均发生一定的波动,并最终趋于一稳定值,涂层在Eoc达到稳定之前的波动主要与膜层的溶解和形成过程相关。这些膜层的溶解和形成过程则与膜层的结构和介质的浸入间存在一定联系,也间接受喷涂参数的影响。由图3⁃6可见,涂层C2和C6表现出较高的Eoc值(分别为-0.20V和-0.21V),说明在O/F比为4.2和送粉速率为40g/min时所制备的涂层膜层较致密,抵抗溶解的能力较强。
在1% NaCl溶液中,不同涂层的动电位极化曲线和电化学阻抗谱见图3⁃7。可见,不同参数制备涂层的过钝化电位都较高(不低于1.0V),且相差不大,说明在1% NaCl溶液中涂层具有较高的局部腐蚀抗力。但钝化电流密度则对O/F比和送粉速率敏感。由图3⁃7(a)可知,涂层的钝化电流密度沿C2、C3、C4和C1的顺序依次增加,而送粉速率则沿C6、C4、C5和C7的顺序呈增加趋势[图3⁃7(b)]。所有涂层的钝化电流密度(约10-5A/cm2)均远高于条带(约10-6A/cm2),说明孔隙的存在恶化了涂层的均匀腐蚀抗力。所有阻抗谱只呈现出半圆弧(即高频容抗弧)特性,大的容抗弧半径说明涂层具有较高的耐蚀性,所有阻抗谱结果与极化曲线结果相一致。

图3⁃7 不同涂层在1% NaCl溶液中的动电位极化曲线和EIS图谱
不同参数制备涂层的点蚀抗力可以用循环极化曲线来评价,见图3⁃8。由图3⁃8可知,涂层C2和C6循环极化曲线回滞环最小,说明在O/F比为4.2和送粉速率为40g/min时所制备的涂层相比其他参数所制备的涂层,具有更优异的抗点蚀能力。
3.1.6 HVOF喷涂参数影响
在HVOF喷涂过程中,颗粒飞行状态主要与火焰的温度、气体流速和气体成分有关,而火焰的特性则又取决于喷涂参数。实际上,O/F比是影响颗粒飞行状态最重要的因素,并最终影响涂层的质量。HVOF喷涂时,原料颗粒被送入由氧气和燃气燃烧所产生的高速气流中。如果O/F比稍低,火焰温度达不到颗粒熔化的温度,导致颗粒不能完全熔化,但较高的O/F比又会引起颗粒过热。氧气流的增加可以促进颗粒的熔化。高的O/F比会引起颗粒氧化,因为完全熔化的颗粒暴露于高温气氛中会继续与氧气反应。这就不难理解为什么涂层的氧化程度随O/F比的增加而增加。

图3⁃8 涂层在1% NaCl溶液中的循环极化曲线
涂层的孔隙率随O/F比的增加而降低。高的O/F比增加了喷枪燃烧室的压力,从而引起高的颗粒速率。当颗粒速率增加时,由于颗粒动能的增加致使颗粒之间触碰的概率增加[10]。另外,孔隙率随颗粒温度的升高而降低[11,12],最终形成比较致密的涂层结构。但同时,涂层中形成的氧化物与周围基体金属间的热膨胀系数不同,易形成分层现象,且氧化物往往比较脆。
另外,非晶相含量对O/F比也非常敏感。O/F比较低时,由于低温和低的颗粒冷却速率,形成的非晶相含量较低。增加O/F比提高了热传递效率,颗粒可以更有效地加热,非晶相形成增多。当O/F比增加至较高的值时,由于颗粒的温度和速率处于比较高的水平,先前形成的涂层易暴露于高温环境中,热量传递不及时,降低了冷却速率,所以不可避免地发生了晶化。除此之外,O/F比增加时,氧化程度增加,氧化改变了涂层的化学成分,也影响涂层非晶相的临界冷却速率。
送粉速率也与热传递和喷涂过程中颗粒的冲击行为相关。当送粉速率低至20g/min时,只有少量的粉末被送入喷枪,粒子相对来说能获得更多的热量,颗粒熔化状态较好,熔滴粒子扁平行为提高,从而降低涂层孔隙率,同时氧化程度也相应提高了。当送粉速率为50g/min时,结果恰恰相反,颗粒熔化状态差,大量的未熔粒子出现在涂层结构中,未熔颗粒的出现致使涂层孔隙率的提高。结合上述结果可知,当送粉速率为40g/min时,多数颗粒熔化状态比较好,氧化程度低,这也与其他学者的部分结果相一致[13,14]。
所用的燃气为丙烷,其燃烧反应式如下:C3H8+5O23CO2+4H2O,氧气和燃气的平衡计量比为5。在喷涂过程中,为了减轻涂层的氧化程度,氧气和燃气流量比通常低于5。然而,如果氧气和燃气流量比太小,飞行颗粒将得不到充足的热量,其熔化状态不够理想。本实验得出最佳O/F比为4.5,相似的是,Maranho[15]也通过实验得出,用丙烷作为燃气其最大的火焰温度是O/F比为4.5时所获得的。考虑到非晶相含量以及腐蚀性能,在O/F=4.2时制备的涂层C2具有最高的耐蚀性和最高的非晶含量。这说明最佳的喷涂表面状态并不能完全体现涂层的综合性能。从表面看,颗粒熔化状态良好的喷涂形貌,仍掩盖不了内部由于热传递不良而造成的氧化现象。因此,C2表面虽包含个别未熔颗粒,但绝大多数熔化状态良好的颗粒使其具有最佳的性能。综合来看,涂层孔隙率低、氧化程度小。同样,在送粉速率为40g/min时所制备的涂层C6具有相似的表面形貌,呈现出最佳的性能。
3.1.7 非晶结构对腐蚀性能的影响
不同参数制备涂层的腐蚀性能主要与涂层微观结构相关联。一般来说,孔隙率的增加会降低涂层的腐蚀性能,如HVOF喷涂SUS316L涂层[8]、Inconel涂层和Ni基非晶涂层[9]。按照这个规律,高O/F比和低送粉速率制备的涂层C4和C5孔隙率最小,应该具有最高的耐蚀性能,即最低的钝化电流密度。但这种推论与本文目前的实验结果不相一致,低孔隙率的涂层反而具有较高的钝化电流密度。因此,对HVOF非晶涂层来说,涂层的耐蚀性不仅与孔隙率有关。事实上,除了孔隙率外,涂层的非晶相含量对腐蚀性的影响也不容忽视。非晶材料与一般晶体材料相比的优势,就是缺少晶界和位错等晶体缺陷的存在。为了综合反映孔隙率和非晶含量两者对腐蚀性能的影响,特将二者综合于图3⁃9中。图3⁃9示出了喷涂参数与孔隙率、非晶相含量和钝化电流密度之间的关系曲线。
由图3⁃9可知,孔隙率较高时,涂层的钝化电流密度受孔隙率的影响较大,比如涂层C1(孔隙率1.51%)和C7(孔隙率1.32%)都具有非常高的钝化电流。而当孔隙率较低时(尤其低于1.21%),非晶相含量则起主要作用,钝化电流密度随非晶相含量的增加而降低。孔隙率和钝化电流密度之间存在一个临界值,也就是说可以实现二者之间对于腐蚀性能的平衡关系。

图3⁃9 喷涂参数与孔隙率、非晶相含量和钝化电流密度的关系
由上述实验还可得出,涂层C2和C6具有最优的点蚀抗力,说明涂层的点蚀抗力也受O/F比和送粉速率的影响。通常,涂层的点蚀抗力与其化学成分相关。非晶涂层高的点蚀抗力源于其均匀且无缺陷的非晶相结构,这些非晶结构对Cl-的点蚀不是很敏感。而喷涂参数对涂层点蚀抗力的影响则与所沉积涂层成分的多样性相关。涂层中未熔颗粒的出现,导致涂层成分的不均匀性,从而降低了涂层的点蚀抗力。另外,高的氧化物含量也改变了涂层的化学成分,最终也降低了涂层的点蚀抗力。
3.1.8 HVOF喷涂参数对硬度的影响
硬度是铁基非晶涂层应用于冲蚀环境必须要考虑的一个指标。Liu[10]认为含多孔隙及未熔颗粒的涂层具有较高的硬度,而由图3⁃5的显微硬度结果可知,高O/F比和低送粉速率所制备涂层的硬度较高。事实上,颗粒的喷涂状态、孔隙率和纳米晶的析出等都会影响涂层的硬度分布。首先,涂层硬度随颗粒温度和速率的升高而增大[4]。颗粒温度和速率则随O/F比增大而升高,O/F比增大后,熔融状态良好的颗粒更易于与基体结合,涂层更均匀且致密。就送粉速率来说,在送粉速率较低时,少量的颗粒可以获得更多的热量,最终导致颗粒温度和速率增加。其次,涂层的硬度也与未熔颗粒的含量、孔隙率和氧化物夹杂量相关,尤其是孔隙率[6]。低的硬度是由于孔隙率和未熔颗粒的出现,孔隙率对于力学性能是非常有害的。从图3⁃5还可以看出,当氧/燃气比(O/F比)高于4.2(即孔隙率高于1.21%)时,涂层的硬度增加幅度明显,而O/F比低于4.2时硬度的增值幅度不太明显。这些结果表明,在孔隙率较高时,低硬度主要来自孔隙率的影响。反之,在高O/F比和送粉速率时制备涂层的孔隙率较低,所以具有较高的硬度值。除此之外,涂层制备过程中形成的纳米晶相,如碳化物、硼化物和氧化物等,也极大地提高了涂层的硬度。纳米晶体相的含量越高,可能对涂层硬度的贡献越大。
可以得出,涂层的耐蚀性和硬度与喷涂参数之间存在内在联系,通过优化喷涂工艺参数可以实现对其耐蚀和耐磨性的平衡。应该注意的是,上述耐蚀性或硬度的结果只是基于单一喷涂参数的影响规律。为了反映O/F比和送粉速率对涂层腐蚀性能的综合影响规律,在O/F比为4.2(C2)和送粉速率为40g/min(C6)条件时,所制备涂层(C0)的极化曲线如图3⁃10所示。

图3⁃10 工艺参数优化后的动电位极化曲线
可见,两个参数制备的涂层的钝化电流密度明显小于单一参数制备的涂层,说明其耐蚀性要优于单一参数制备的涂层。从目前结果来看,通过优化O/F比或/和送粉速率,可以实现耐蚀性的提高,对于耐磨性的提高也有一定的指导意义,可以为铁基非晶涂层应用于海水介质冲蚀环境提供参考。
因此,喷涂参数影响涂层微观结构。涂层孔隙率和未熔颗粒随O/F比的增加而降低,随送粉速率的增加而增加。涂层氧化物含量则呈相反趋势。喷涂参数影响涂层非晶含量,孔隙率和非晶含量与耐蚀性之间存在一临界值,当孔隙率<1.21%,非晶含量占主导,钝化电流随非晶含量降低而增加;反之孔隙率是影响涂层耐蚀性的主要因素。喷涂参数影响涂层硬度,高的O/F比和低的送粉速率时制备的涂层硬度较高。涂层中晶化相、均匀的颗粒熔化状态及低孔隙率是导致涂层高硬度的主要原因。喷涂参数影响涂层耐蚀性,涂层C2(O/F=4.2)和C6(40g/min)具有较高的开路电位、低的钝化电流密度以及高的点蚀抗力,耐蚀性能最佳。涂层点蚀抗力也与喷涂参数相关,涂层中未熔颗粒以及氧化物的出现导致涂层成分不均匀,点蚀抗力降低。