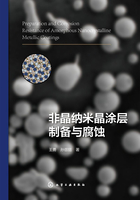
2.1 非晶合金在中性和酸性溶液中腐蚀
自19世纪70年代开始,Fe⁃Cr非晶合金优异的耐蚀性已经受到人们的广泛关注。众多研究者已经通过改善成分以及添加合金元素优化钝化膜的结构,开发出一系列耐蚀性优异的铁基非晶合金。高耐蚀性主要源自无晶界和位错等缺陷存在的非晶结构以及钝化膜中强耐蚀元素的富集。在含氯离子介质中,Fe⁃Cr⁃Mo非晶合金在热的浓HCl溶液中可自发发生钝化[1],在12mol/L HCl溶液中阳极极化至1.0V(Ag/AgCl)也无点蚀现象发生[2]。100℃时,在4mol/L NaCl溶液中可自发钝化且具有较宽的钝化区间和较小的钝化电流密度[3]。早期报道,FeCrMnMoWBCSi非晶合金在天然海水(NaCl)[4]和1mol/L HCl[5]溶液中具有优异的钝化稳定性能,但其腐蚀性对酸性腐蚀介质更敏感。合金中的合金元素(如Mo、Mn、W等)是影响其钝化性能的主要因素,但目前这些元素的添加对于其耐蚀和耐磨性能的影响还不是很清楚。因此,研究铁基非晶合金在酸性和中性两种不同介质中的腐蚀行为,有助于进一步理解其腐蚀机理,即H+和Cl-作用。但二者之间系统的比较研究甚少。
在硫酸盐溶液中,早期的研究多集中于浓H2SO4介质的腐蚀行为,如FeCrPC[3]、FeSiB[6]和FeCSiBPCrAl[7]等非晶合金在浓H2SO4介质中均呈现出较好的钝化稳定性。合金成分(如Cr[3,7],P[3])和表面结构[6]起关键作用。一般来说,浓H2SO4介质是一种弱氧化剂,但其氧化能力随浓度增大而增强。Pardo[8]等研究表明,在5mol/L浓H2SO4介质中FeSiBNbCu晶体材料耐蚀性优于非晶材料,主要是因为晶体中晶界、第二相等晶体缺陷处易形成腐蚀产物,进而抑制腐蚀介质的侵蚀过程。而在稀H2SO4介质中,普通的晶体材料(如不锈钢[9]、Fe⁃Cr合金[10])的耐蚀性则远低于非晶材料。对于晶化的FeCuNbSiB非晶合金,非晶相的形成则提高了其在0.1mol/L H2SO4介质中的耐蚀性[11]。因此,非晶结构的出现可能有益于提高材料在稀H2SO4介质中的耐蚀性。然而,对铁基非晶合金在稀H2SO4介质(浓度小于1mol/L)中腐蚀行为的系统研究较少。与其他非晶合金相比,开发FeCrMnMoWBCSi非晶合金的初衷是基于高的玻璃形成能力和优异的力学性能,次之是优异的腐蚀性能,况且其成分不同于传统的非晶合金体系,对此类成分的铁基非晶合金在酸性和中性硫酸盐介质中的腐蚀行为还未见于报道。
本节主要研究FeCrMnMoWBCSi非晶合金在两种酸性(0.5mol/L HCl,0.25mol/L H2SO4)和中性(0.5mol/L NaCl,0.25mol/L Na2SO4)介质中的电化学腐蚀行为和钝化膜特征。电化学腐蚀行为包括:动电位极化曲线、电化学阻抗谱、恒电位极化曲线(i⁃t曲线)和Mott⁃Schottky曲线。钝化膜的特征通过X射线光电子能谱(XPS)和原子力显微镜(AFM)来表征。
2.1.1 非晶合金制备
(1)合金制备过程
将按名义成分配比(原子分数)的纯金属元素(Fe:99.9%,Cr:99.9%,Mo:98.5%,Mn:99.7%,W:99.9%,FeB:99%含20.06%B,C:99.9%,Si:99.9%)在Hechigen公司Edmund Bühler真空电弧炉中熔炼制备Fe54.2Cr18.3Mo13.7Mn2.0W6.0B3.3C1.1Si1.4(质量分数)母合金铸锭。该电弧熔炼系统采用钨电极和水冷铜坩埚。真空度一般控制在5×10-3Pa,随后充入约0.05Pa的高纯氩气作为保护气体,并辅以预熔钛球吸氧进一步纯化保护气体。为确保母合金铸锭的均匀性,一般要反复翻转熔炼8次以上。
非晶合金条带(ribbon)样品通过熔体急冷法获得,所用设备为德国Hechigen Edmund Bühler真空单辊急冷装置。其铜辊直径为250mm,辊面宽40mm,常用可调转动频率为0~50Hz(对应辊面线速度为0~39m/s)。真空抽气系统由机械泵与扩散泵构成。腔体真空度达到预定值后,充入高纯氩气形成保护气氛。一定质量的块状铸锭样品在石英管中感应加热至熔融态并在压差作用下由喷嘴喷出,在旋转的铜辊上快速凝固形成薄带状样品。在熔体急冷制备薄带过程中,通过对铜辊的转速、喷嘴尺寸、喷嘴与辊面间隙、熔体温度以及喷射压差等参数的调节可以控制条带样品的厚度、宽度和表面质量。对于铁基条带,采用35m/s辊速、方形喷嘴(2mm×4mm)、过热度200K和0.04MPa压差,可以获得良好成型性的完全非晶态条带,所得条带厚度为40μm,宽度约2mm。
(2)合金性能测试
X射线衍射(X⁃ray diffraction,XRD)分析在日本产Rigaku D/max2400衍射仪上进行,采用Cu Kα射线源(λ=0.1542nm),扫描速度为4°/min。条带样品选取自由面(空冷面)测量。
条带样品的玻璃化转变和晶化行为是在德国Netzsch⁃404C型高温差示扫描热量分析仪(differential scanning calorimeter,DSC)上测试完成的。所需样品质量为10mg左右,装填于氧化铝坩埚内,预抽真空至0.1Pa后通入流动的高纯氩气保护。升温和降温速率均采用20K/min。玻璃化转变温度(Tg)定义为玻璃化转变吸热平台最陡处的切线与基线的交点所对应的温度;晶化起始温度(Tx)定义为第一个晶化峰最陡处的切线与基线的交点所对应的温度。
样品的显微结构观察是在荷兰FEI Tecnai F30高分辨透射电镜(high resolution transmission electron microscope,HRTEM)上完成的。由于Ni50Nb50条带样品宽度小于2mm,制作成长度为3mm、宽度方向2mm的小样品,然后用细砂纸将厚度研磨至约40μm,用铜环镶嵌,最后在离子减薄仪上进行低温减薄。为消除氩离子轰击引入结构假象,需要采用小电流减薄。一般得到符合TEM观察要求的样品要减薄10h以上。
腐蚀性能测试在PAR 2273上进行。电化学实验参考GB/T 24196—2009《金属和合金的腐蚀 电化学试验方法 恒电位和动电位极化测量导则》和GB/T 18590—2001《金属和合金的腐蚀 点蚀评定方法》。条带样品在进行动电位极化行为测试前均需经过1500⋕以上的砂纸精细打磨,随后用石蜡混合松香封样,经过酒精或丙酮清洗、蒸馏水清洗等一系列准备过程。三电极系统采用辅助电极(铂电极)、工作电极(样品)和参比电极(饱和甘汞电极,SCE,下文未标明电位均为相对于SCE电极的电位值)。为消除液接电势影响,饱和甘汞电极与溶液间用鲁金毛细管连接(毛细管与试样表面距离为毛细管直径2倍为宜)。
琼脂⁃饱和KCl盐桥制备过程:向烧杯中加入3g琼脂和97mL蒸馏水,使用水浴加热法将琼脂加热至完全溶解。然后加入30g KCl充分搅拌,KCl完全溶解后趁热用滴管或虹吸将此溶液加入已事先弯好的玻璃管中,静置待琼脂凝结后便可使用。
测试时主要考察不同[H+]变化和阴离子种类对铁基非晶合金腐蚀性能的影响,具体溶液配比见表2⁃1~表2⁃3。
表2⁃1 不同[H+]和0.25mol/L[HSO4-/S
-]溶液配比(名义浓度)

表2⁃2 不同[H+]和0.50mol/L[Cl-]溶液配比(名义浓度)

表2⁃3 不同阴离子种类0.50mol/L[H+]溶液配比(名义浓度)

腐蚀测试前,为消除空气中形成钝化膜的影响,在-1.2V时阴极极化180s,去除表面氧化膜。测试时,首先测试开路电位(open circuit potential,OCP),当开路电位稳定后(一般3600s,100s内电位变化小于1mV)进行相关腐蚀电化学测试。动电位极化曲线(PD)扫描速率为0.167mV/s,扫描电位范围为相对于开路电位-0.25~+1.2V。电化学阻抗谱(EIS)采用10mV扰动电位,测试频率范围100kHz~10MHz。为反映钝化膜稳定性,分别测试条带在0V、0.2V、0.4V、0.6V和0.8V不同电位下的电化学阻抗谱,测试完后采用Zview阻抗谱拟合软件进行数据拟合。恒电位极化(I⁃t曲线)是在某一特定外加电位下,记录腐蚀电极之间电流随时间的变化情况。常用来反映材料表面在相应电位下溶解或钝化的过程,或用于分析亚稳点蚀的萌生、初期长大以及稳态长大等现象。为获得亚稳点蚀信息,一般外加电位选择在动电位极化曲线的钝化区间内。为进一步表征材料表面在相应电位下溶解或钝化的过程,分别测试条带在0.2V、0.4V、0.6V和0.8V下的恒电位I⁃t曲线,时间1800s。钝化膜的半导体特性可由Mott⁃Schottky曲线测得。用于测试的条带经1500⋕砂纸打磨处理后,于不同电位条件下在相应溶液中浸泡24h后形成稳定表面钝化膜。Mott⁃Schottky曲线对测试频率敏感,为了反映钝化膜的真实差异,所选频率应尽量处在电极电容稳定区段。图2⁃1展示的是铁基非晶合金表面膜的电容(C)随测试频率(f)的变化(由阻抗谱曲线导出)。可见,该合金在较大测试频率范围内(100~104Hz)电容值变化不大(从5×10-5F/cm2到3×10-5F/cm2)。Mott⁃Schottky曲线测试所选择的频率为1kHz。测试时在钝化膜形成电位区间内,沿阳极方向进行电位扫描,电位分别选择0V、0.2V、0.4V、0.6V和0.8V。为确保实验记录不受外界干扰,该测试装置安放在稳固、减震性好的实验台上。实验过程中电解池要置于恒温(约298K)水浴槽内。所有实验结果均重复至少3次,以确保结果的可靠性。

图2⁃1 电容随频率的变化曲线
XPS(X⁃ray photoelectron spectroscopy)又被称为ESCA(electron spectroscopy for chemical analysis),是表面分析的重要手段。它是以X射线为激发源检测由表面射出的光电子来获取表面丰富的物理和化学信息。采用XPS技术可表征非晶合金表面钝化膜成分及其分布。XPS测试在ESCALAB250光电子能谱测试系统上进行,采用Al靶(1486.6eV)作为X射线源。测试时,条带的自由面经一系列型号砂纸细磨后,分别在测试溶液中0.6V电位下阳极极化104s。实验中采用原位氩离子溅射逐层减薄的办法来反映表面区的详细成分分布,相应的减薄速率为0.2nm/s,减薄区域为2mm×2mm,远大于XPS探测面积(Φ=0.5mm)。Fe 2p、Cr 2p、Mo 3d、Mn 2p、W 4f、C 1s、O 1s和Cl 2p的标准键能参考NIST XPS数据库。
原子力显微镜(atomic force microscopy,AFM)成像技术是利用原子探针从无穷远处逐渐逼近材料表面时,通过建立探针尖端原子与表面原子或分子之间的相互作用力与距离之间的关系实现的。在轻敲模式(tapping mode)下,探针的震动频率会随着所接触材料的性质发生变化,根据这一性质可同时探测局部区域材料性质的差异。AFM测试在美国Molecular Imaging公司Picoplus 2500 AFM仪器上进行。探针由金属铂探头镶嵌在硅传感悬臂梁中构成,其固有振动频率为148~150kHz。采用手动光学对中探针与被检测样品。测试时,将条带用502胶粘于平整的硬树脂块表面,进行机械抛光。完成机械抛光与清洗后,用石蜡密封条带边缘并与导线相连,然后在相应溶液中浸泡7d,腐蚀后样品再进行超声清洗,准备用于AFM观察。
2.1.2 非晶结构表征
非晶合金条带样品的XRD和DSC曲线见图2⁃2。

图2⁃2 非晶合金条带样品的XRD和DSC曲线
非晶单相因不存在长程结构周期性,故X射线衍射上无尖锐衍射峰,而是宽带衍射峰。可以看出,条带在2θ=40°~50°的范围内显示出漫散的衍射峰,表明其为完全非晶态结构。由于非晶合金的原子结构处于亚稳态,在升高温度时会发生晶化,向稳定状态转变。一般将合金晶化开始温度与玻璃化转变温度之间的差值定义为过冷液相区,用来衡量非晶合金的热稳定性。过冷液相区越大,非晶合金的热稳定性越大。但非晶合金晶化后,其很多优异性能会发生不利转变,如电阻升高、耐腐蚀性能下降等。但有时通过适当的工艺手段,可以制备具有更优异力学性能或软磁性能的非晶与纳米晶复合材料。如图2⁃2插图所示,非晶合金条带在加热情况下发生完全晶化现象,这种晶化是通过合金内原子扩散进行的。
图2⁃3中代表性地展示了铁基非晶合金的暗场像[图2⁃3(a)]与相应的选区衍射图谱[图2⁃3(a)插图]以及高分辨相[图2⁃3(b)]。对于非晶合金样品,TEM暗场像中未能观察到明显的衬度差别,选区电子衍射花样由较宽的晕和弥散的环组成,没有表征结晶态的任何斑点和条纹,其高分辨像则未呈现出晶体结构的规则点阵衬度,这些特征均表明实验获得的条带为完全非晶态样品。

图2⁃3 典型的非晶合金(a)TEM暗场像与选区衍射图谱及(b)高分辨相
2.1.3 电化学腐蚀行为
非晶合金条带在不同介质中的动电位极化曲线和电化学阻抗谱如图2⁃4所示。由图2⁃4(a)可知,在硫酸盐溶液中,非晶条带的钝化电流密度对于溶液中[H+]的变化很敏感,随[H+]的降低,从1×10-5A/cm2(0.4mol/L [H+])升高至2×10-5A/cm2(0.1mol/L [H+])。在所有介质中的点蚀电位或过钝化电位均为1.0V,反映出条带在这些溶液中具有相同的抵抗局部腐蚀的能力。条带在H2SO4溶液中具有最低的钝化电流密度(约5×10-6A/cm2),而在Na2SO4溶液中的钝化电流密度(约6×10-5A/cm2)值则最高。图2⁃4(b)表示的是非晶条带在含氯介质中钝化电流密度随[H+]变化的关系。与在硫酸盐溶液中的趋势相反,在含氯介质中条带的钝化电流密度随[H+]的增加而增加,在NaCl溶液中具有最低的钝化电流密度(1×10-5A/cm2),在HCl溶液中则最高(6×10-4A/cm2)。
图2⁃4(c)反映的是非晶合金条带在含相同[H+]及不同种类阴离子溶液中的极化曲线,可以看出,溶液中S和Cl-的出现影响了非晶合金的钝化性能,增加了钝化电流密度。
图2⁃4(a')~(c')反映的是极化曲线相对应的电化学阻抗谱。电化学阻抗谱的高频区域可以体现电极电化学反应阻抗大小,根据高频区的容抗弧大小,可以判断耐蚀性大小,较大的容抗弧反映出条带具有更优的耐蚀性。由图可知,电化学阻抗谱的测试结果与极化曲线结果相一致。
图2⁃5表示的是条带在0.6V恒电位条件下在相应溶液中电流随时间响应的i⁃t曲线。所记录的i⁃t曲线上有许多电流的瞬间波动,或称之为电流暂态峰(current transient)。一般来说,每一个电流暂态峰都表现为腐蚀电流的急剧增大,随后在一定时间内又回落到背底电流水平。电流增大的过程对应于合金氧化物的溶解,电流回落过程则为氧化物的形成过程。从图2⁃5(a)~(d)可以得出,在所有溶液中,起始电流急剧降低,这种电流的急剧下降说明钝化膜的形成和生长速度快于其溶解速度。随后逐渐趋于平稳(稳态电流密度,iss),说明钝化膜的形成在整个测试时间内无明显的破裂现象发生。而较低的iss值则反映出钝化膜具有较高的稳定性。如图2⁃5(a)~(d)所示,条带在Na2SO4溶液中的iss高于其在H2SO4溶液中的iss值,而在HCl溶液中的iss则高于其在NaCl溶液中的iss值。在Na2SO4和HCl溶液中,高电位(0.6~0.8V)下的iss值增加幅度更大,具有更高的iss值。

图2⁃4 非晶合金在不同介质中的动电位极化曲线和电化学阻抗谱[(a')(b')(c')]
依据文献[12],电流增大的过程对应于亚稳点蚀的长大,电流回落过程则为点蚀的再钝化,其相应所需时间分别称作点蚀长大时间(pit growth time)和再钝化时间(repassivation time),总时间为点蚀的寿命(life time);电流最大值与背底电流差值称为暂态峰高度(transient height)。很明显,在HCl溶液中,非晶条带发生明显的点蚀现象[图2⁃5(c)]。

图2⁃5 非晶合金在不同溶液中的i⁃t曲线(含双对数形式)
电流密度随时间变化的响应也可以表示为[13]:
lgi=lgA-Klgt(2⁃1)
式中,i为测试的电流值密度;A为常数;K为双对数i⁃t曲线下降段的斜率;t为点蚀形核时间。K=-1表明形成致密且保护性强的钝化膜,而K=-0.5则表明形成的钝化膜较疏松且多孔[14]。
图2⁃5(a')~(d')为条带在不同钝化电位下不同溶液中的双对数i⁃t曲线,由曲线计算的不同电位下的K值和点蚀形核时间t见表2⁃4。由表2⁃4可以看出,在所有测试电位下,K值均高于-0.5,说明形成的钝化膜比较疏松。在H2SO4和NaCl溶液中,K值基本处于同一数值,反映出非晶条带在两者溶液中所形成的钝化膜疏松程度差别不大。类似的钝化膜也出现在Na2SO4和HCl溶液中。0.8V时,在HCl和NaCl溶液中的t值分别为178s和106s,较低的t值说明点蚀的形核容易,非晶条带在HCl溶液中极易形成点蚀。
表2⁃4 K值和t值随电位变化值

非晶合金条带在四种溶液中在不同电位下的电化学阻抗谱如图2⁃6所示。由图可知,所有谱图在高频区均呈现出单一容抗弧特征。条带在H2SO4和NaCl溶液中具有较大的容抗弧,与图2⁃4极化曲线的结果一致。在硫酸盐溶液中,阻抗随电位升高而增大,而在含氯介质中,阻抗则随电位的升高而呈降低趋势。图2⁃6的电化学阻抗谱也可以用图2⁃7的钝化膜界面特征来进一步分析。图2⁃7(a)表示的非晶条带在溶液中形成的钝化膜的界面特征,主要包括金属/钝化膜界面、钝化膜、钝化膜/溶液界面。
图2⁃7(b)为与钝化膜界面相对应的等效电路,其中,Rs表示溶液电阻,Rt表示电荷传递电阻,CPEdl表示与Rt并联的双电层电容,Rf表示钝化膜层的电阻,CPEf表示与Rf并联的双电层电容。由于真实的电化学体系中很难实现纯电容的条件,所以用常相位角元件CPE(constant phase element)来表示。图2⁃6所有的电化学阻抗谱均采用图2⁃7(b)的等效电路进行拟合。
图2⁃8中的实线表示经等效电路拟合的结果,从二者的吻合程度来看,所选的等效电路可以实现在多数频率范围完美拟合,说明所选的等效电路是正确的。
拟合后相应的Rt、CPEdl、Rf和CPEf值见图2⁃8。由图2⁃8可以看出,相比Na2SO4溶液来说,在H2SO4溶液中具有更高的Rt、Rf值以及更低的CPEdl值。在含氯介质中则具有相反的趋势,在NaCl溶液中具有较高的Rt、Rf值及较低的CPEdl值。这些结果说明双电层和钝化膜对于非晶合金在四种溶液中的腐蚀有至关重要的影响。需要注意的是,在图2⁃8(d)中,CPEf与Rf值的规律不是很吻合,说明钝化膜/溶液界面的特征并不能由电化学阻抗谱全部反映出来,还有待于下面进一步的实验验证。

图2⁃6 非晶合金在不同溶液中的电化学阻抗谱

图2⁃7 钝化膜的界面(a)及相对应的等效电路(b)

图2⁃8 等效电路拟合参数值
2.1.4 钝化膜的电子特征
本质上来说,钝化膜是一种高度掺杂的半导体膜,其电子的传导特性决定着钝化膜的溶解与生长。假定亥姆霍兹层电容忽略不计,可测得电极电容和电位的关系,即Mott⁃Schottky曲线,它能反映钝化膜的半导体特性。一般来说,钝化膜的电容(Cf)由三部分组成[15]:
=
+
+
(2⁃2)
式中,CM为金属/膜界面电容;CSC为空间电荷电容;Cdl为亥姆霍兹双电层电容。
由于具有较厚的空间电荷层,空间电荷电容(CSC)相比于金属/膜界面电容(CM)和亥姆霍兹双电层电容(Cdl)来说非常小,可以忽略。所以CM和Cdl的作用可以忽略不计,这样Cf即可作为CSC。1/相对于E的曲线之间应满足线性关系,可以用来反映钝化膜的半导体性质。对于n型半导体膜来说,电极电容(CSC)和电位(E)的关系满足:
=
(E-EFB-
)(2⁃3)
式中,εr为膜的介电常数(Fe⁃Cr合金εr=15.6[16]);ε0为真空介电常数(8.85×10-12F/m);e为电荷电量;ND为n型半导体膜的施主载流子密度;EFB为平带电位;k为玻尔兹曼常数;T为热力学温度。
非晶合金在四种溶液中的Mott⁃Schottky曲线如图2⁃9所示。可见,在两种酸性和中性溶液中,条带的Mott⁃Schottky曲线有着类似的形状。酸性溶液中在0.1V到0.4V之间、中性溶液中在0.2~0.6V之间为线性区间,其他部分线性不明显。低电位区段(<0.1V)的非线性可能是由于最外层钝化膜的影响,而高电位区段(>0.6V)偏离线性的原因则可能是钝化膜较高的缺陷密度。

图2⁃9 不同极化电位下非晶合金在不同溶液中的Mott⁃Schottky曲线
所有线性区的斜率均为正值,表示钝化膜在所测试条件下均为n型半导体膜。载流子密度(ND)可以由线性区的斜率拟合得出,平带电位(EFB)可以由外推至零获得。ND与EFB的表达式如下:
ND=(
)-1(2⁃4)
EFB=E0-(2⁃5)
式(2⁃5)中,E0为=0所对应的电位值。
Mott⁃Schottky曲线线性区的斜率随电位升高而降低,说明载流子密度(ND)随电位升高而增加。图2⁃9的载流子密度计算结果见图2⁃10。非晶合金在中性溶液(Na2SO4和NaCl)中具有较低的ND值。在含氯介质中,这种结果与极化曲线(图2⁃4)、i⁃t曲线(图2⁃5)以及电化学阻抗谱(图2⁃6)结果一致。这说明在含氯介质中,载流子密度大小对钝化膜的稳定性起着关键的作用。
在硫酸盐溶液中,载流子密度大小与电化学测试结果不相一致,说明在此类腐蚀介质中,钝化膜结构中的载流子密度并不是影响腐蚀的唯一因素。所以除了钝化膜结构因素外,很有必要对膜层的成分进行详细分析。

图2⁃10 由Mott⁃Schottky曲线计算所得载流子密度(ND)值
2.1.5 钝化膜的成分和结构表征
图2⁃11是铁基非晶合金在四种溶液中形成的钝化膜的XPS测试的全谱扫描,主要的谱线有Fe 2p、Cr 2p、Mo 3d、Mn 2p、Cl 2p、W 4f、C 1s和O 1s等。

图2⁃11 非晶合金在不同溶液中形成钝化膜的XPS全谱扫描
部分C元素来自表面污染层,以C 1s对应的结合能284.6eV为基准校正其他谱线位置。由图2⁃11的峰强度可见,钝化膜主要由Fe、Cr和Mo元素组成,峰强度沿H2SO4、HCl、NaCl和Na2SO4溶液顺序依次减弱。
腐蚀后未经溅射表面典型的Fe 2p、Cr 2p和Mo 3d精细谱峰如图2⁃12所示。Fe 2p谱由两套彼此分开的2p3/2和2p1/2谱峰构成,每个谱峰实际上是包含了金属态和氧化态子峰(主要为Fe3+和Fe2+)。Cr 2p3/2和Cr 2p1/2谱峰分别由金属态Cr0以及氧化态Cr3+和Cr6+子峰构成。

图2⁃12

图2⁃12 Fe 2p、Cr 2p和Mo 3d精细谱峰
Mo 3d谱由彼此交叠的3d5/2和3d3/2谱峰构成,主要包含金属态Mo0以及氧化态Mo4+和Mo6+子峰。金属态Fe和Mo的谱峰强度相对其氧化态较高,说明钝化膜内层或界面上有部分未完全氧化的Fe和Mo存在。另外,Fe 2p、Cr 2p和Mo 3d精细谱峰在酸性介质(H2SO4、HCl)中的强度高于其在中性介质(Na2SO4、NaCl)中的强度,说明在两者介质中所形成的钝化膜的成分有差异。
为了详细分析非晶合金在不同溶液中形成钝化膜的特征,给出钝化膜以及金属基体中各金属元素和氧的浓度分布,如图2⁃13所示。每种元素的含量根据其峰值的面积计算。与基体相比,钝化膜中的Fe、Cr和Mo的含量急剧下降。另外,钝化膜厚度的差异可根据氧元素的分布[17]简单定量确定。由图2⁃13可知,合金表面的O含量随深度增大急剧下降,若将O含量下降到最表面层一半处定为钝化膜厚度,则非晶合金在酸性介质中的钝化膜厚度约为2nm,而在中性介质中的钝化膜厚度则为4nm。

图2⁃13 非晶合金在不同溶液中表面层各组元的深度分布
钝化膜中主要合金化元素Fe、Cr和Mo的XPS谱峰形状也随溶液的不同产生变化(见图2⁃14),尤其是各种价态元素的含量存在差异。由图2⁃14(a)可知,未经氩离子溅射时,钝化膜的谱峰在酸性和中性溶液中明显不同。在酸性溶液中,所有的Fe、Cr和Mo的XPS谱峰形状相似,但峰强度不同,如条带在H2SO4溶液的峰强度高于其在HCl溶液中。同时,相似的情况也出现在中性溶液中,条带在NaCl和Na2SO4溶液中具有相似的峰,但其在NaCl溶液中峰强度稍高。经氩离子溅射20s和40s后,峰形状差异明显减小,但峰强度稍有不同,见图2⁃14(b)和图2⁃14(c)。说明钝化膜表层中元素的分布不同,钝化膜内层中的分布则趋于一致。各元素峰值的不同,说明元素各种价态的含量不尽相同。
用XPSpeak分峰软件,将图2⁃14各个元素的峰值进行分峰计算,可以得到元素中每个价态的含量。通过计算,元素价态含量随钝化膜深度变化的规律见图2⁃15。可以看出,所有溶液中形成的钝化膜均由Fe2+/Fe3+、Cr3+/Cr6+和Mo4+/Mo6+氧化物构成。在酸性溶液中,Fe2+/Fe3+、Cr3+/Cr6+和Mo4+/Mo6+的比例明显高于其在中性溶液中的比例,说明酸性溶液中形成的钝化膜主要富集低价态的Fe2+、Cr3+和Mo4+氧化物。


图2⁃14 不同溶液对非晶合金表面层中Fe、Cr、Mo、Mn、W和O状态的影响
1—0.25mol/L H2SO4;2—0.25mol/L Na2SO4;3—0.50mol/L HCl;4—0.50mol/L NaCl

图2⁃15 非晶合金表面层各组元状态及分布示意图
2.1.6 AFM表面形貌观察
图2⁃16示出非晶合金在不同溶液中浸泡7d后表面的AFM形貌图像。
从平面图看,由于腐蚀后样品表面存在一些抛光造成的微小划痕,在腐蚀过程中划痕区域更易溶解而延迟钝化,导致最终腐蚀表面划痕显得更加明晰。从三维图总体上来看,条带在H2SO4和NaCl溶液中表面腐蚀后形貌变化不明显,表面粗糙度分别为Ra=20.80Å和Ra=21.12Å。尤其在H2SO4溶液中,条带表面绝大部分区域较平整,说明处于良好的钝化状态。条带在Na2SO4和HCl溶液中的表面形貌则显得粗糙,表面粗糙度分别为Ra=29.16Å和Ra=44.02Å,说明在此二者溶液中形成更多的腐蚀产物。另外,沿划痕方向出现一些细小尖锐峰,其中在HCl溶液中局部钝化膜破坏更为严重。需要指出的是,条带在含氯介质中腐蚀后表面出现个别较大的尖锐峰,这可能是腐蚀产物在点蚀形核处累积的结果。

图2⁃16 非晶合金在不同溶液中浸泡7d后合金表面AFM形貌图像
2.1.7 非晶合金钝化特征及腐蚀机理
(1)钝化膜稳定性
一般来说,非晶合金的耐蚀性取决于钝化膜的保护性。钝化膜起阻挡合金表面与腐蚀介质接触的作用。从极化曲线结果(图2⁃4)看,条带在H2SO4和NaCl溶液中钝化电流密度最小。钝化电流密度对[H+]很敏感,在硫酸盐溶液中随[H+]增加而减小,而在含氯介质中则随[H+]增加而增加。这说明条带在H2SO4溶液中形成的钝化膜稳定性优于其在Na2SO4溶液中,而在HCl溶液中形成的钝化膜稳定性则低于其在NaCl溶液中。电化学阻抗谱(图2⁃6)结果与极化曲线结果相一致,条带在H2SO4和NaCl溶液中阻抗最大。而且,在硫酸盐溶液中,阻抗随电位升高而增加,在含氯介质中则呈现出相反的趋势,说明在硫酸盐溶液中形成的钝化膜更稳定。外加电位和Cl-对钝化膜稳定性也有一定影响。电位的施加可以影响点蚀坑的形成,在高电位条件下,一些再钝化的亚稳点蚀被重复激活,损伤累积到一定程度导致蚀坑形成,发生点蚀。点蚀一旦发生,高的电位有利于其迅速长大。Cl-引起钝化膜点蚀的机理目前还没有定论。多数认为,Cl-发生迁移,与金属/膜界面发生作用引起点蚀[18],或者Cl-化学吸附在氧化物表面,参与反应并形成络合物,加速溶解过程的进行[19]。所以,在含氯介质中,随电位升高,Cl-的迁移和反应作用相应增强,导致钝化膜稳定性急剧下降,腐蚀性能下降。
图2⁃17为非晶合金条带在H2SO4和HCl溶液中[H+]与钝化电流密度的关系图。

图2⁃17 非晶合金在酸性介质中[H+]与钝化电流密度的关系(考虑活度系数)
在H2SO4溶液中,钝化电流密度随[H+]增加急剧下降(接近线性关系),说明[H+]对条带在H2SO4溶液中腐蚀具有至关重要的作用。在HCl溶液中,在[H+]处于0.1~0.3mol/L时,条带的钝化电流密度与[H+]关系不大。当[H+]超过0.3mol/L时,钝化电流密度随[H+]增加急剧升高,[H+]=0.3mol/L可以作为其腐蚀加剧的门槛值或临界值。文献也有相似的结果报道,如Fe在酸溶液浓度较低时溶解速率很低[20],而在高浓度含氯酸中溶解速率加剧[21]。在含氯酸中,F、Cr2+和C
氧化物的溶解速率首先与H+活度相关。某些学者认为,高的[H+]催化了Fe的阳极溶解过程[24]。在高的[H+]和[Cl-]条件下,H+通过静电吸引卤素离子,导致金属的溶解增加。
(2)钝化膜的结构和半导体特性
合金的钝化性能主要取决于其表面氧化物的形成和溶解过程,即形成钝化膜的结构、厚度以及成分等。首先,钝化膜的结构是影响膜层稳定性的主要因素。由电流随时间响应i⁃t曲线结果(图2⁃5)可知,非晶合金在H2SO4和NaCl溶液中形成的钝化膜致密度较高,而在Na2SO4和HCl溶液中形成的钝化膜比较疏松多孔。疏松的钝化膜有利于一些侵蚀性的阴离子渗透到膜层内,恶化其腐蚀性能。这似乎可以解释条带在H2SO4中耐蚀性好而在Na2SO4中耐蚀性差,以及在HCl中耐蚀性差而在NaCl中耐蚀性好的原因。需要注意的是,S和Cl-两种阴离子在溶液中的不同作用并未考虑。另外,膜层中缺陷的多少也是影响钝化膜稳定性一个非常重要的因素。
从Mott⁃Schottky曲线(图2⁃9和图2⁃10)的结果看,不同溶液中所形成钝化膜的半导体特征不尽相同。对于铁基非晶合金,钝化膜的半导体特征与其钝化膜的稳定性之间存在一定联系。一方面,载流子密度越高,钝化膜的导电性越高[25,26]。一旦发生钝化,一些阳离子或阴离子穿透氧化物层变成整个腐蚀反应的控制步骤。离子导电成为决定钝化电流密度最主要的因素。因此,高的载流子密度将引起高的钝化电流密度。另一方面,普遍的观点认为,载流子密度越低,钝化膜发生点蚀的倾向越小[27]。如图2⁃10所示,在H2SO4溶液中形成的钝化膜中的载流子密度最高,意味着离子在此钝化膜中容易穿透且发生点蚀的倾向大。还有一个影响钝化膜稳定性的因素是这些迁移载体的扩散能力。不考虑载体的种类,Macdonald[28]认为这些载体是钝化膜中存在的一些缺陷,包括阳离子空位、阴离子空位和阳离子间隙位置等。根据其提出的点缺陷模型[28],在n型半导体中,主要的载体是氧空位(oxygen vacancies),这些氧空位在金属/氧化物界面形成。目前实验已经证实在Fe⁃Cr合金的氧化物结构中存在氧空位[29]。
载流子密度随外加电位的升高而升高,表明相应的氧空位缺陷随电位升高而增加,所以钝化膜的保护性将降低。根据此规律,含氯介质中的钝化电流密度符合载流子密度的变化规律。与在NaCl溶液中不同的是,非晶合金在HCl溶液形成的钝化膜具有最高的缺陷浓度,再加上HCl溶液中疏松的钝化膜结构,这些都有利于提高Cl-的渗透作用,导致腐蚀性能急剧下降,所以其钝化电流密度最大。也就是说,在含氯介质中,钝化膜的结构对其钝化或腐蚀行为起着决定性的作用。但在硫酸盐溶液中,与Na2SO4溶液相比,非晶合金在H2SO4溶液形成的钝化膜具有最高的缺陷浓度,这与其在H2SO4溶液中的钝化电流密度最小不相符。所以,除了钝化膜的结构因素之外,钝化膜的成分以及不同的腐蚀机理都可能是影响非晶合金在硫酸盐介质中腐蚀行为的主要因素。
(3)钝化膜的厚度和成分
除了钝化膜结构之外,钝化膜的厚度和成分也是影响其稳定性的重要因素。众多研究者都对钝化膜的成分进行了系统的研究。一般来说,铁基非晶合金高的耐蚀性来源于富Cr的钝化膜。在酸性硫酸盐介质中,Cr可以抑制Fe的过钝化溶解[30]。多数学者得出,Fe⁃Cr合金在0.5mol/L H2SO4溶液中形成的钝化膜主要成分为富集Cr3+化合物层(Cr2或FeCr2
)。其他研究者则认为主要由Cr6+化合物(Cr
或Cr2
)组成。实际上,不仅仅是Cr,钝化膜中的Mo也是促使形成钝化膜层[34]的主要物质。Kannan[35]认为316L不锈钢在H2SO4溶液中形成的钝化膜主要成分为富Mo和富Cr氧化物。添加适量的Mo可以极大地提高钝化膜的均匀性和稳定性,其中Cr的存在是必不可少的合金元素[36]。在钝化形成过程中,Mo可以通过抑制Cr的溶解来提高腐蚀抗力。对于钝化膜中含Mo化合物的存在形式,目前还有一定争议。在酸性溶液中,普遍认为钝化膜中含Mo化合物主要以Mo4+种类(Mo
或MoO(OH
)和少量的Mo6+种类(Mo
或Mo
)形式存在。而在中性或碱性溶液中,也出现了像Mo6+种类(HMo
或Mo
)和少量Mo3+种类(Mo
)等形式。目前为止,对于Mo、Cr氧化物在钝化膜稳定性中的作用还不是很明确。
由图2⁃13可知,非晶合金在两种酸中形成的钝化膜厚度比较薄(约为2nm),这主要与H+的还原作用和铁氧化物在酸性溶液中的溶解特性相关[42]。一般来说,厚的钝化膜抵抗溶解的能力要强于薄的钝化膜。非晶合金在HCl溶液中形成的钝化膜薄于其在NaCl溶液中形成的钝化膜,符合其在含氯介质中的腐蚀行为。但在H2SO4溶液中,薄的钝化膜则与高的腐蚀抗力相矛盾,这意味着在硫酸盐溶液中,除了上述的钝化膜的结构和厚度外,还有影响其腐蚀行为的其他决定性因素,如钝化膜的成分。
图2⁃15示出了钝化膜中各阳离子含量随膜深度的变化规律。从图中可以得出,在酸性溶液和中性溶液中所形成的钝化膜成分不尽相同。在Na2SO4和NaCl溶液中,外层钝化膜中的氧化物则主要以高价态的Fe3+、Cr6+和Mo6+氧化物为主,内层则主要由低价态的Fe2+、Cr3+和Mo4+氧化物组成。这说明钝化膜主要是一种双层结构,外层是含高价态氧化物的缺陷层,低价态氧化物组成了膜的内层(见图2⁃18),也与文献中双层钝化膜模型一致[43]。在H2SO4和HCl溶液中,钝化膜成分不同,外层和内层钝化膜均以低价态的Fe2+、Cr3+和Mo4+氧化物为主。这主要是由于在酸性溶液中,表面高价态的Fe3+(Fe2O3)[44]、Cr6+(Cr)[33],Mo6+(Mo
)[38]物质容易发生优先溶解,致使低价态的氧化物富集于膜层外层。根据氧化物键能的不同,优先溶解顺序遵循Fe3+、Cr6+和Mo6+氧化物顺序。对于316L不锈钢,在H2SO4溶液中由于H+加速阳极溶解过程,优先溶解的结果使得膜层中Fe氧化物含量下降而Cr氧化物含量增加[35]。
不同价态的氧化物对钝化膜的稳定性有一定影响。通过非原位光谱技术(ex⁃situ spectroscopic)可知,稳定的钝化膜主要由低价态的Cr3+[Cr2或Cr(OH
]而不是高价态Cr6+(Cr
)物质组成。调制反射光谱(modulation reflectance spectroscopic)的研究结果也支持上述观点[49]。最近XPS的结果也反映出在H2SO4溶液中稳定的钝化膜主要由低价态Cr3+氧化物组成[50]。富Cr钝化膜的过钝化溶解源自高价态Cr(Cr2
)物质的溶解。对于膜层中Mo种类来说,膜外层高价态的Mo6+(Mo
)物质具有阳离子选择(cation selective)作用,发生优先溶解。高价态Mo6+物质的溶解增加了阳极电流密度,进而降低了腐蚀性能[40]。在缓冲溶液中(pH=1~13),随着pH升高,钝化膜的稳定性降低,主要原因是形成高价态易溶的Mo6+(HMo
和Mo
)物质。对于低价态的Mo4+氧化物来说,难溶的Mo4+氧化物维持了Fe⁃Cr非晶合金高的钝化性能[37]。Mo可以形成保护性极强的Mo4+[Mo
、MoO(OH
]物质阻挡腐蚀介质与材料接触,这种均匀的膜层减小了腐蚀的活性区域,从而降低溶解速率。这也可以解释本文的实验结果,在H2SO4溶液中,正是由于膜层外表低价态的Cr3+和Mo4+氧化物的存在,使钝化膜的保护性增强,提高了膜层的稳定性。但这种成分的差异在HCl溶液中并不符合腐蚀规律,说明钝化膜成分差异影响了条带在硫酸盐溶液中的腐蚀行为,而膜层结构方面的差异则是影响非晶合金在含氯介质中腐蚀行为的关键因素。这主要是由于二者阴离子在腐蚀过程中的作用和腐蚀机理不同所致。
(4)腐蚀机理
腐蚀机理主要与钝化膜的特性和腐蚀介质相关。铁基非晶合金的腐蚀也不例外,与介质中的阴离子(如HS/S
、Cl-和OH-)密切相关。不同溶液中这些阴离子在合金表面吸附的程度不尽相同。
零电荷电位(potential of zero charge,Epzc)是金属/溶液界面电荷为零时的电位值,可以用来反映材料表面吸附阴离子的量。此时,电极/溶液界面上不会出现由剩余电荷引起的离子双电层,一般认为,不存在紧密层和分散层,仅仅表示电极表面剩余电荷为零时的电极电位,而不表示电极/溶液相间的电极或绝对电极电位的零点。零电荷电位可以反映氧化物覆盖电极表面电荷随电极电位变化的情况[51]。零电荷电位测量有两种方法:一是电毛细曲线法,曲线中表面张力最大值所对应的电位即为零电荷电位。此方法较为准确,只适用于液态金属,如汞、汞齐和熔融态金属。二是微分电容法,曲线上微分电容最小值所对应的电位即为零电荷电位,该法是目前最为精确的方法。此法可用于固态金属,溶液越稀,微分电容最小值越明显。对于氧化物覆盖的电极,零电荷电位与其半导体性质中的平带电位(flatband potential,EFB)间也存在关联性。由于表面电荷变化,无能带弯曲(band bending),所测量的平带电位EFB即为零电荷电位。
由极化曲线所测试的腐蚀电位(Ecorr)和由Mott⁃Schottky曲线所计算得到的平带电位(EFB,即为零电荷电位Epzc)如表2⁃5所示。可以看出,所有的腐蚀电位均低于零电荷电位,说明在自腐蚀电位时,合金表面吸附了大量的阴离子而带负电荷。也可采用(Epzc-Ecorr)差值来反映吸附电荷量的多少。很明显,在Na2SO4溶液中,Epzc-Ecorr差值大(0.934V),阴离子吸附驱动力强,吸附的量也要远高于其在H2SO4溶液(Epzc-Ecorr=0.434V),说明有更多的阴离子吸附在合金表面。但在HCl和NaCl溶液中,二者的差值并不大,基本处于同一数量值,说明在含氯介质中,Cl-在合金表面吸附量相当。一些XPS结果也证实了在钝化膜外层HS/S
和C
的存在。
表2⁃5 腐蚀电位(Ecorr)与平带电位值(EFB)

如上所述,非晶合金在Na2SO4溶液中表面吸附的阴离子量多,阴离子主要为S,另有少量的OH-;在H2SO4溶液中吸附的阴离子量较少,主要为HS
/S
。非晶合金在两种溶液中腐蚀行为的不同与Langmuir吸附等温式有关。可以确认的是,阴离子HS
/S
参与了金属的溶解过程,与阳极离子反应生成沉淀物[53]或形成电荷传递络合物[54],加速金属溶解过程。金属原子与阴离子的作用过程通常由分解步骤[式(2⁃6)、式(2⁃7)]、化学步骤[式(2⁃8)、式(2⁃10)]和电化学步骤[式(2⁃9)、式(2⁃11)]组成。
在酸性溶液中:
H2SO4H++HS
(2⁃6)
HSH++S
(2⁃7)
M+mHS[M(HSO4)m
(2⁃8)
[M(HSO4)m[M(HSO4)m
+ne(2⁃9)
通常认为式(2⁃6)完全进行,而式(2⁃7)可以被忽略(K=1.2×10-2)。
在中性溶液中:
M+mS[M(SO4)m
(2⁃10)
[M(SO4)m[M(SO4)m
+ne(2⁃11)
当金属的溶解过程被电化学步骤[式(2⁃9)、式(2⁃11)]所控制时,溶解过程的电流密度(ia)可写成:
ia=kθexp()(2⁃12)
式中,k为反应常数;θ为电极表面吸附的中间络合物的覆盖度;n为传递的电子数;F为Faraday常数,F=96485J/(mol·V));E为外加电位;R为气体常数,R=8.314J/(K·mol);T为热力学温度(T=298.15K)。
θ主要取决于阴离子浓度,阴离子浓度增加,金属的溶解速率相应增加。式(2⁃12)可重新写成以下的形式:
ia=k'Cmexp()(2⁃13)
式中,C为阴离子浓度。
当[S]较低时,不足以形成大量的中间络合物,所以腐蚀速率较低。在H2SO4溶液中,当增加[S
]后,S
吸附量增加,导致金属溶解速率增加[55]。[H+]增加后,[HS
]浓度下降,相应降低了HS
的吸附和金属的溶解速率,这与实验观察的结果一致。在稀H2SO4溶液中,对于晶体和纳米晶[56]材料,H+的出现提高了溶液的反应活性,通过优先溶解第二相(如铁铝化物中的碳化物相[57]、FeTiC合金中的铁素体相[58])、晶界或位错等缺陷部位,在金属氧化物溶解的同时,这些缺陷部位更加速了金属的溶解过程。但对于非晶材料,由于缺少优先溶解的缺陷区域,因此只发生氧化物的溶解,比如钝化膜表面高价态氧化物的优先溶解过程。图2⁃18示出了钝化膜双层结构,以及非晶合金在四种不同溶液中,阴离子吸附、钝化膜成分和结构以及腐蚀过程的信息。阴离子吸附方面,在H2SO4溶液中吸附的阴离子要少于在Na2SO4溶液中;而在两种含氯介质中阴离子吸附的量则差不多。钝化膜结构方面,在H2SO4溶液中所形成的钝化膜较Na2SO4溶液中的薄、氧空位缺陷多,但膜层致密;在HCl溶液中的钝化膜膜层与NaCl溶液相比也比较薄、缺陷多,但膜层比较疏松。钝化膜成分方面,在H2SO4和HCl两种酸中形成的钝化膜成分一致,由于在H+作用下的优先溶解,膜表面由低价态的Cr3+(Cr2O3)和Mo4+(MoO2)氧化物组成。其中,S
和Cr
复合后使膜层产生两极化,加速了去质子化过程,致使内层Cr2O3膜层的生长[2],形成的Cr2O3是维持钝化的主要原因。在Na2SO4和NaCl两种中性溶液中的钝化膜则符合钝化膜的双层结构,表面富含高价态的氧化物,内层则由低价态的氧化物组成。非晶合金在H2SO4和Na2SO4溶液中具有不同腐蚀行为的主要原因,在于阴离子HS
/S
的吸附行为,这种吸附机制则又主要依靠于钝化膜的成分因素。
在HCl和NaCl两种溶液中,Cl-在其表面吸附的量相差不大。由图2⁃11的XPS结果可知,Cl-存在于钝化膜层,也参与了钝化膜的形成。与上述HS/S
的吸附机制不同,Cl-主要以渗透机制参与反应过程,这种渗透过程则主要取决于膜层的结构因素。由于Cl-半径小,穿透性强,对于局部腐蚀和阳极溶解过程有极为重要的影响。Cl-可在局部区域优先与一些氧化物结合[59],可以渗透到膜层内部占据氧空位(O2-)的位置,见图2⁃18。一旦氧空位被Cl-占据,空位处的负电荷减少,必然会引起空位数量的增加[25],进而导致膜层中载流子密度的增加。同时,Cl-还可以迁移并在金属氧化物界面发生反应[60],Cr比较容易与Cl结合形成氯化物(MClx)[61]。一般来说,所形成的固体氯化物往往引起氧化物膜层的体积膨胀,导致膜层机械破裂[62],从而致使点蚀快速渗透入基体金属内部,发生局部腐蚀。图2⁃16中非晶合金在含氯介质中腐蚀后的AFM图中的尖锐峰也可以反映这种点蚀破坏的明显性。

图2⁃18 钝化膜双层结构(a)和不同溶液中形成钝化膜特征及阴离作用(b)示意图
对于非晶合金在HCl和NaCl两种溶液中不同的腐蚀行为,主要与H+的催化阳极(如Fe[63]、Cr[23])作用相关。H+的催化过程如下:
M+Cl-MClads+e(2⁃14)
MClads+H+MClH+ (2⁃15)
MClH++Cl-MCln+H++e (2⁃16)
MClnMn++nCl- (2⁃17)
式(2⁃15)为反应的速控步,如果吸附中间体遵循Langmuir吸附等温式,则式(2⁃15)可表示成:
ia=kCClCHexp()(2⁃18)
式中,CCl、CH分别表示Cl-和H+浓度。
这个反应过程表明,金属在HCl溶液中的腐蚀过程取决于Cl-和H+的浓度。H+的出现加速了金属的溶解,但同时Cl-的渗透过程也与H+密切相关,因为H+的局部酸化可以加速随后的点蚀过程[64]。另外,钝化膜越薄,Cl-越易穿透膜层。在HCl溶液中,所形成的钝化膜具有较高的缺陷密度以及疏松的膜层结构,这些结构方面的因素是导致非晶合金在其中低腐蚀抗力的主要原因。
因此,铁基非晶合金在酸性和中性溶液中呈现出不同的腐蚀行为,钝化电流密度对[H+]敏感。在硫酸盐溶液中,钝化电流密度随[H+]增加而降低,在H2SO4溶液中具有比Na2SO4溶液更低的钝化电流密度。在含氯介质中则呈相反趋势,钝化电流密度随[H+]增加而增加,在NaCl溶液中的钝化电流密度则低于HCl溶液。外加电位和Cl-的存在影响了钝化膜的稳定性。在酸性溶液中形成的钝化膜结构、厚度和成分不同于在中性溶液中。在酸性溶液中,钝化膜层较薄,且表面富集低价态的Fe2+、Cr3+和Mo4+氧化物。在含氯介质中,钝化膜的稳定性主要取决于膜层的结构特性,如膜层致密性、缺陷密度等。
与在NaCl溶液不同的是,在HCl溶液中形成的膜层疏松多孔且含较多的缺陷,加上Cl-的浸透机理,促使了Cl-浸透入膜层内部,导致点蚀倾向增加。由于H+的阳极催化作用,最终导致合金在HCl溶液中腐蚀性能下降。在硫酸盐溶液中,由于S遵循吸附机理,钝化膜的成分对于腐蚀过程起着重要作用。HS
、S
等阴离子在合金表面吸附,与金属溶解反应形成电荷转移络合物,加速了腐蚀过程。在H2SO4溶液中,H+阳极催化致使表面高价态氧化物优先溶解,表面富集稳定性和保护性强的低价态Cr3+和Mo4+氧化物,保证了膜层在H2SO4溶液中的稳定性,从而使其具有比在Na2SO4溶液中更优的耐蚀性。