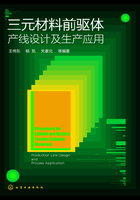
第2章 三元前驱体的结晶操作方式
2.1 概述
在制备不同类型的三元正极材料时,往往需要采用不同粒度分布的三元前驱体。例如制备压实密度较大的二次颗粒三元正极材料时,需采用粒度分布较宽的大粒径三元前驱体;制备单晶型的三元正极材料时,需采用粒度分布较窄的小粒径三元前驱体;制备动力型的二次颗粒三元正极材料时,往往希望各颗粒的性质较为均一,则需采用粒度分布较窄的大粒径三元前驱体。因此在三元前驱体制备过程中获得期望粒径及粒度分布的产品至关重要。几种典型三元前驱体产品的粒径及粒度分布如表2-1。
表2-1 三元前驱体产品的典型粒度数据

第1章介绍的表征粒度分布宽度的计算公式较为烦琐,为了简化计算,常用径距来表征粒度的分布宽度。径距越大,粒度分布越宽,反之则粒度分布越窄。径距(Span)采用式(2-1)进行计算:

从表2-1中几种典型的三元前驱体产品粒度数据来看,宽粒度分布的径距在1左右,窄粒度分布的径距在0.8以下。要得到要求粒径及粒度分布的产品,必须清楚其颗粒的形成机理。
根据第1章的分析,三元前驱体的制备是一种结晶操作,故三元前驱体属于晶体颗粒。晶体颗粒的形成是通过晶体的成核、长大而成,但三元前驱体的沉淀速率较快,其晶体通常比较细小,为微、纳米级别,这些微细晶粒由于比表面较大而无法单独存在,会自发地聚结在一起形成二次颗粒,所以三元前驱体属于二次晶体颗粒,它的粒径大小和粒度分布由这些二次颗粒的大小及百分含量来表征。
二次颗粒的粒径及粒度分布和晶体的成核速率、生长速率、聚结速率有关。根据第1章的介绍,当搅拌强度一定时,晶体的成核速率和过饱和度以及固含量有关;晶体的生长速率和聚结速率也和过饱和度相关。第 1 章曾给出各种速率与过饱和度的关系,如式(2-2)~式(2-4)。



式中,B为晶体的成核速率;KN为晶体与搅拌强度、温度有关的成核速率常数;S为过饱和度;MT为固含量;G为晶体的生长速率;KG为晶体的生长速率常数;A为晶体的聚结速率;KA为晶体的聚结速率常数。
从式(2-2)~式(2-4)可看出,三者的速率均和过饱和度呈正相关的关系,但对饱和度的敏感度不同,且都要对过饱和度进行竞争。当过饱和度很高时,成核速率对过饱和度最敏感,成核速率较大,会新生成很多的晶核。这时由于晶体成核消耗了过多的过饱和度,溶液的过饱和度减小,生长速率就会变小,生成的一次晶体就会变得细小,晶体表面的界面过饱和度较高,因此晶体的聚结速率就会增大。由于新生成的一次晶体数目较多,这些一次晶体不仅会在反应釜内原有的二次颗粒上聚结使晶体的粒径变大,同时也会新聚结出许多粒径较小的二次颗粒(如图 2-1)。这些小粒径的二次颗粒不仅会拉低整体的粒径值,还会使粒度分布变宽。当过饱和度较为适中时,成核速率不是很高,新生成的晶核数量较少,晶体生长速率较大,生成的一次晶体较为粗大,新生成的大部分晶体在原有的二次颗粒上聚结长大,新聚结的二次颗粒生成数目较少,这样既保证了颗粒的生长,又保证了较窄的粒度分布。因此在三元前驱体的颗粒形成过程中,要保证达到要求的粒径及粒度分布,应避免成核速率过大,防止生成的晶核数目过多。

图2-1 三元前驱体的颗粒形成过程
晶核的生成数目和成核速率有关,从式(2-2)可以看出,当反应釜内固含量不随时间发生变化时,成核速率仅和过饱和度相关。根据第1章的介绍,三元前驱体的过饱和度由式(2-5)表示。

当反应釜内搅拌分散良好,氨水浓度稳定,游离的金属离子浓度[M2+ ]可看作定值,成核速率仅和游离的OH-的浓度,即pH有关。根据式(2-5),过饱和度S可转化为式(2-6)。

式中,S为过饱和度;Kc为与温度及游离金属离子浓度相关的常数。
将式(2-6)代入式(2-2),当固含量MT不随时间发生变化时,成核速率B与pH的关系为:

式中,B为成核速率;K'N为与搅拌强度、温度以及固含量有关的成核速率常数;i为与过饱和度相关的成核速率指数。
从式(2-7)可以看出,三元前驱体的成核速率B与反应过程中的pH值成指数关系,如图2-2。当pH超过某一临界值时,成核速率会爆发增长。所以若要防止结晶过程中晶核形成数目过多,应尽量控制pH值在临界pH值以下。

图2-2 成核速率与pH值关系图
当反应釜内的固含量随时间变化时,则成核速率又增加了一个变量,成核速率由式(2-8)表示。

此时应防止高pH值与高固含量下的双重叠加效应的发生,导致晶核生成数目过多。应充分考虑两者的耦合作用,当固含量升高时,应降低pH值。
在三元前驱体反应结晶时,溶液的过饱和度是较难测量的,但可以通过反应釜内的粒度分布变化情况来判断成核速率的高低。当小粒度特征值如D10、D3、Dmin开始下降,说明有新的聚结二次颗粒出现,生成的晶核数目较多,成核速率较高。一般粒径数值下降越多,表示成核速率越高。在三元前驱体反应结晶时定时对反应釜内的粒度分布情况抽检是控制反应过程粒度分布的一种关键的辅助手段。一般使用激光粒度仪检测反应釜内物料粒度分布的变化情况。通常高精度的粒度仪的粒度检测范围为0.1~1000μm,且粒度值越小误差越大,所以有时候粒度仪的检测结果并不能反映出真实的粒度分布情况。也有些工作者采用显微镜直接观测釜内浆料颗粒,判断反应釜内物料的粒度分布变化情况,例如通过目视观察方式判断有无新的二次聚结颗粒产生,其产生量大概是多少,等等。这种靠人为目视的检测方式虽然较为直观,但往往需要操作者有丰富的粒度观测经验才能对反应釜的粒度分布变化情况作出准确的判断。
晶体颗粒的粒径及粒度分布除和晶核生成数目有关外,还和晶体颗粒的停留时间有关。晶体颗粒的停留时间是指颗粒从反应釜内产生开始直至流出反应釜所经历的时间。晶体颗粒生长到一定粒径需要经历一定的时间。晶体的生长必须要在一定的过饱和度下进行,当晶体颗粒出现在反应釜内,由于反应釜内一直有溶质供应,能够为晶体颗粒的生长不断提供过饱和条件,从而使晶体颗粒不断长大。对于单个晶体颗粒来说,晶体颗粒在反应釜内停留的时间越长,其表面不断地会有晶体聚结,粒径就会越大,反之粒径就会较小。对于反应釜内的整体颗粒来说,当各颗粒的粒径大小相差不大时,其颗粒表面的界面过饱和度大小相近,聚结速率几乎相等,当停留时间一致时,容易获得粒度分布较窄的颗粒产物;反之当各颗粒大小相差较大时,即便停留时间一致,其粒度分布也比较宽或需要经历较长的停留时间才能获得分布较窄的颗粒产物。
停留时间不仅会影响晶体颗粒的粒径及粒度分布,还会对晶体颗粒的振实密度产生重要的影响。根据第1章分析,晶体结晶一开始并不是形成最稳定的晶体形态结构,而是先形成自由能损失最小的亚稳态结构。亚稳态向稳态结构的转变也需要一定时间,在转变过程中,晶体颗粒的密实度增加,且随着颗粒粒径的增长,振实密度增加,当完全转变为稳态结构时,晶体的振实密度不随停留时间而发生变化。王伟东等[1]对三元前驱体的振实密度随反应时间变化做了实验,结果如图2-3。

图2-3 振实密度随反应时间的变化关系图[1]
综上所述,在进行三元前驱体的结晶操作时,要获得理想粒径及粒度分布的产品,应充分考虑晶核的生成数目和晶体的停留时间的影响。通常三元前驱体的结晶操作流程可分为如下几步:①向反应釜内注入一定的量的纯水作为反应底水,并加热到指定温度;②向反应釜内注入一定浓度的氨碱混合液,开启搅拌,再向反应釜内输入盐、碱、氨水溶液;③在反应过程中进行反应釜内浆料粒径及粒度分布、振实密度等过程检验。如果粒径及粒度分布、振实密度达到要求,则可作为产品排出,否则需继续反应,如图2-4。

图2-4 三元前驱体结晶操作流程图
在三元前驱体的工业结晶操作时,根据其产品产出方式的不同,可分为连续法、间歇法、半连续半间歇法三种。三种方式在结晶操作、结晶控制、产能及产品方面各有特点。下面分别对这三种方式进行介绍。