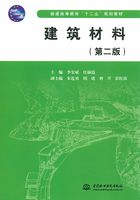
第二节 通用硅酸盐水泥
水泥是国民经济建设的重要材料之一,是制造混凝土、钢筋混凝土、预应力混凝土构件的最基本组成材料。水泥品种非常多,按其组成成分分类,可分为硅酸盐类水泥、铝酸盐类水泥、硫铝酸盐类水泥和铁铝酸盐类水泥等。水泥按其性能及用途可分为通用水泥、专用水泥和特性水泥三类。土木工程中最常用的是通用硅酸盐水泥。国家标准《通用硅酸
盐水泥》(GB175-2007/XG1-2009)对其定义、分类、组分与材料、技术要求和试验
方法等作出了相关的规定。
一、通用硅酸盐水泥的定义、分类及生产概况(一)定义
通用硅酸盐水泥(CommonPortlandCement)是指以硅酸盐水泥熟料和适量的石膏及规定的混合材料制成的水硬性胶凝材料。


(二)分类
通用硅酸盐水泥按混合材料的品种和掺量分为硅酸盐水泥、普通硅酸盐水泥、矿渣硅酸盐水泥、火山灰质硅酸盐水泥、粉煤灰硅酸盐水泥和复合硅酸盐水泥6种。各品种的组分和代号,见表26。
表2 6
通用硅酸盐水泥的组分和代号
① 本组分材料为符合标准的活性混合材料,其中允许用不超过水泥质量8%且符合标准的非活性混合材料或不超
过水泥质量5%且符合标准的窑灰代替。
② 本组分材料为符合GB/T203或GB/T18046的活性混合材料,其中允许用不超过水泥质量8%且符合标准的活
性混合材料或非活性混合材料或窑灰中的任一种材料代替。③ 本组分材料为符合GB/T2847的活性混合材料。
④ 本组分材料为符合GB/T1596的活性混合材料。
⑤ 本组分材料为由两种(含)以上符合标准的活性混合材料或/和符合标准的非活性混合材料组成,其中允许用
不超过水泥质量8%且符合标准的窑灰代替。掺矿渣时混合材料掺量不得与矿渣硅酸盐水泥重复。
(三)生产概况
1.通用硅酸盐水泥的生产原料
生产通用硅酸盐水泥的原料,主要有石灰质原料、黏土质原料及少量校正原料等。石灰质原料(如石灰石、白垩、石灰质凝灰岩等)主要提供氧化钙;黏土质原料(如黏土、黏土质页岩、黄土等)主要提供二氧化硅、三氧化二铝及少量的三氧化二铁。当以上两种原料化学组成不能满足要求时,还要加入少量校正原料(如铁矿粉、黄铁矿渣、砂岩等)进行调整。
2.通用硅酸盐水泥的生产工艺
通用硅酸盐水泥的生产工艺,可以概括为“两磨一烧”,即水泥生料的配料与磨细;将生料煅烧使之部分熔融形成熟料;将熟料与适量石膏共同磨细,可制得P·Ⅰ型硅酸盐水泥;熟料加入石膏和不同种类的混合材料粉磨,可制得不同品种的其他通用硅酸盐水泥。其生产工艺流程如图21所示。
图21 通用硅酸盐水泥的生产工艺流程

二、通用硅酸盐水泥的组成材料(一)硅酸盐水泥熟料
硅酸盐水泥熟料的主要化学成分是由石灰质原料中的氧化钙(CaO)、由黏土质原料
中的氧化硅(SiO2)、氧化铝(Al2O3)和氧化铁(Fe2O3)。经过高温煅烧后,以上4种
化学成分化合为熟料中的主要矿物组成:硅酸三钙(3CaO·SiO2 ,简式为C3S)、硅酸二
钙(2CaO·SiO2,简式为C2S)、铝酸三钙(3CaO·Al2O3,简式为C3A)和铁铝酸四钙(4CaO·Al2O3 ·Fe2O3 ,简式为C4AF)。
硅酸盐水泥熟料的矿物组成和含量范围,见表27。其中硅酸三钙和硅酸二钙的总含量在70%以上,铝酸三钙和铁铝酸四钙的含量在25%左右。除了主要熟料矿物外,硅酸盐水泥熟料中还含有少量的游离氧化钙、游离氧化镁和碱等,它们的总含量一般不超过水泥质量的10%。
表2 7
硅酸盐水泥熟料的矿物组成
(二)石膏
(1)天然石膏。指符合GB/T5483中规定的G类或M类二级(含)以上的石膏或混合石膏。
(2)工业副产石膏。指以硫酸钙为主要成分的工业副产物。采用前应经过试验证明对水泥性能无害。
(三)混合材料
在生产水泥时掺入的天然或人工的矿物质材料称为混合材料,其中有天然岩矿和工业废渣。在水泥熟料中掺加一定数量的混合材料,目的是为了改善水泥的某些性能、调节水泥的强度等级、节约水泥熟料、提高水泥产量、降低水泥成本、利用工业废渣等。
混合材料按其性能不同,可分为活性混合材料和非活性混合材料两大类,其中以活性混合材料用量最大。近年来也采用兼具有活性和非活性的窑灰。
1.活性混合材料
所谓活性混合材料是指这类材料磨成粉末后,与石灰、石膏或硅酸盐水泥加水拌合后能发生水化反应,在常温下能生成具有水硬性的胶凝物质。符合 GB/T203、GB/T
18046、GB/T1596、GB/T2847标准要求的粒化高炉矿渣、粒化高炉矿渣粉、粉煤灰、
火山灰质材料都属于活性混合材料。
(1)粒化高炉矿渣。
粒化高炉矿渣是在高炉冶炼生铁时,为了使铁矿石易于熔融,常加入一定量的石灰石作为助熔剂。在高温下石灰石分解出的氧化钙与铁矿石中的黏土质废渣化合,生成含有硅酸盐和铝酸盐的熔融矿渣,浮在铁水的表面,这些矿渣经骤冷处理,可成为质地疏松、多
孔的细小颗粒,称为粒化高炉矿渣。粒化高炉矿渣的主要化学成分为二氧化硅、三氧化二铝和氧化钙,大约占90%以上,另外还有少量的氧化镁和三氧化二铁及其他杂质。
(2)粉煤灰。
粉煤灰是火力发电厂以煤粉作燃料,煤粉在锅炉中燃烧后,由收尘器从烟气中收集的灰粉,它属于火山灰质混合材料的一种,为密实球形玻璃质结构,其化学成分主要是活性二氧化硅和活性三氧化二铝,其性质与火山灰质混合材料基本相同。
(3)火山灰质混合材料。
凡天然或人工的以氧化硅、氧化铝为主要成分的物质材料,本身磨细加水拌合并不硬化,但与气硬性的石灰混合后,再加水拌合,则不但能在空气中硬化,而且在水中继续硬化的,称为火山灰质混合材料。
天然的火山灰质混合材料有火山灰、凝灰岩、浮石、沸石岩、硅藻土和硅藻石等;人工的火山灰质混合材料有烧黏土、煤矸石、粉煤灰、煤渣、页岩灰、硅质渣等。火山灰质混合材料按其活性成分及组成结构,又可分为含水硅酸质、火山玻璃质和烧黏土质混合材料。
2.非活性混合材料
凡不具有活性或活性很低的人工或天然的矿物质材料,磨成细粉后与石灰、石膏或硅酸盐水泥加水拌合后,不能或很少生成水硬性的胶凝物质的材料,称为非活性混合材料。掺加非活性混合材料的目的主要是起填充作用、增加水泥产量、降低水泥强度等级、降低水泥成本和水化热、调节水泥的某些性质等。
常用的非活性混合材料有:活性指标分别低于 GB/T203、GB/T18046、GB/T
1596、GB/T2847标准要求的粒化高炉矿渣、粒化高炉矿渣粉、粉煤灰、火山灰质混合材料;石灰石和砂岩,其中石灰石中的三氧化二铝含量应小于等于2.5%。
3.窑灰
窑灰是从水泥回转窑窑尾废气中收集的粉尘,应符合JC/T742的规定。窑灰的性能介于活性混合材料与非活性混合材料之间,主要组成物质是碳酸钙、脱水黏土、玻璃态物质、氧化钙,另外还有少量的熟料矿物、碱金属硫酸盐和石膏等。
(四)助磨剂
水泥粉磨时允许加入助磨剂,其加入量应不超过水泥质量的0.5%,助磨剂应符合
JC/T667的规定。
三、通用硅酸盐水泥的技术要求(一)化学指标
通用硅酸盐水泥化学指标,见表28。(二)碱含量(选择性指标)
碱含量是指水泥中氧化钠(Na2O)和氧化钾(K2O)的含量。近些年来,很多混凝土发生了碱集料反应,即水泥中的碱和集料中的活性二氧化硅反应,生成膨胀性的碱硅酸盐凝胶,导致混凝土开裂。因此,当使用活性骨料时,要使用低碱水泥。水泥中碱含量按Na2O+0.658K2O计算值表示。若使用活性骨料,用户要求提供低碱水泥时,水泥中的碱含量应不大于0.60%或由买卖双方协商确定。

表2 8
通用硅酸盐水泥的化学指标
① 如果水泥压蒸试验合格,则水泥中氧化镁的含量(质量分数)允许放宽至6.0%。
② 如果水泥中氧化镁的含量(质量分数)>6.0%时,需进行水泥压蒸安定性试验并合格。③ 当有更低要求时,该指标由买卖双方确定。
(三)物理指标1.凝结时间
凝结时间是水泥从加水拌合开始,到水泥浆失去可塑性所需的时间。凝结时间分为初凝时间和终凝时间。初凝时间是从水泥加水到水泥浆开始失去塑性的时间;终凝时间是从水泥加水到水泥浆完全失去塑性的时间。
国家标准规定,水泥凝结时间用凝结时间测定仪进行测定。试样用标准稠度水泥净浆,实验温度控制在20±3℃,湿度大于90%。硅酸盐水泥的初凝时间不小于45min,终凝时间不大于390min。普通硅酸盐水泥、矿渣硅酸盐水泥、火山灰质硅酸盐水泥、粉煤灰硅酸盐水泥和复合硅酸盐水泥初凝时间不小于45min,终凝不大于600min。
水泥的凝结时间在施工中具有重要意义。初凝不宜过快是为了保证有足够的时间在初凝之前完成施工等各工序的操作;终凝不宜过迟是为了能尽早完成凝结硬化,以利于下一道工序及早进行。
2.安定性
水泥的安定性是指水泥在凝结硬化过程中体积是否均匀变化的性能。如果水泥在凝结硬化过程中产生均匀的体积变化,则其安定性合格,否则为安定性不良。水泥安定性不良,会使水泥制品、混凝土构件产生膨胀性裂缝,影响工程质量,甚至引起严重的工程事故。
引起水泥安定性不良的原因有3个:
(1)熟料中游离氧化钙过多。水泥熟料中含有游离氧化钙,其中部分过烧的氧化钙在水泥凝结硬化后,会缓慢与水生成氢氧化钙。该反应体积膨胀,使水泥石发生不均匀体积变化。
(2)熟料中游离氧化镁过多。水泥中的氧化镁在水泥凝结硬化后,会与水生成氢氧化镁。该反应比过烧的氧化钙与水的反应更加缓慢,且体积膨胀,会在水泥硬化几个月后导致水泥石开裂。
(3)石膏掺量过多。当石膏掺量过多时,水泥硬化后,在有水存在的情况下,石膏会继续与固态的水化铝酸钙反应生成高硫型水化硫铝酸钙(即钙矾石),体积约增大1.5倍,

引起水泥石开裂。
国家标准规定,水泥的安定性可采用沸煮法检验。沸煮法又包括试饼法和雷氏法两种。试饼法是将标准稠度的水泥净浆做成试饼,标准养护24h后在水中沸煮3h,用肉眼观察其表面是否有裂纹,用直尺检查是否有翘曲现象,两者均无的水泥称为安定性合格。雷氏法是测定水泥浆在雷氏夹中沸煮硬化后的膨胀值,其膨胀量在规定值内的为安定性合格。当试饼法和雷氏法两者结论有矛盾时,以雷氏法结论为准。
沸煮法只能检验水泥熟料中游离氧化钙过多的情况,而对游离氧化镁、石膏过量不适用。国家标准规定,在水泥生产中要严格控制游离氧化镁和石膏的含量,其中氧化镁和三氧化硫的含量在化学指标中已作定量限制。
3.强度
水泥的强度是指水泥胶结能力的大小,这是评价水泥质量的重要指标,也是划分水泥强度等级的依据。
国家标准《水泥胶砂强度检验方法(ISO法)》(GB/T17671—1999)规定,采用软
练胶砂法测定水泥强度。该方法是由按质量计的1份水泥、3份中国ISO标准砂,用0.50的水灰比拌制的一组塑性胶砂,制成40mm×40mm×160mm的试件,将试件连模一起在湿润条件下养护24h,脱模后在标准温度(20℃±1℃)的水中养护,分别测定3d和28d的抗压强度和抗折强度,根据测定结果对照国家标准,确定硅酸盐水泥的强度等级。
各类、各强度等级水泥的各龄期强度,见表29,其中代号R表示早强型水泥。
表2 9
通用硅酸盐水泥各龄期的强度要求
4.细度(选择性指标)
水泥的细度是指水泥颗粒的粗细程度,它直接影响水泥的性能和使用。水泥颗粒越细,水泥与水接触面积越大,水化越充分,水化速度越快。所以,相同矿物组成的水泥,其细度愈大,早期强度愈高,凝结速度愈快,析水量愈少。
试验研究表明,水泥颗粒粒径在45μm以下,才能充分水化,在75μm以上,水化则不完全。水泥细度提高,可使水泥混凝土的强度提高,工作性能得到改善,但在空气中的硬化收缩性增大,使混凝土发生裂缝的可能性增加。此外,细度提高导致粉磨能耗增加,成本提高。
硅酸盐水泥和普通硅酸盐水泥的细度以比表面积表示,其比表面积不小于300m2/kg;矿渣硅酸盐水泥、火山灰质硅酸盐水泥、粉煤灰硅酸盐水泥和复合硅酸盐水泥的细度以筛余率表示,其80μm方孔筛筛余率不大于10%或45μm方孔筛筛余率不大于30%。
5.水泥的水化热
水泥与水接触发生水化反应时所放出的热量,称为水泥的水化热。水泥的大部分水化热在凝结硬化的初期放出,如硅酸盐水泥,1~3d龄期内水化放热量为总热量的50%,7d龄期为75%。水化热的大小和释放速率,主要取决于水泥熟料的矿物组成、混合材料种类和数量、水泥的细度、外加剂的种类、养护条件等因素。一般水泥强度等级高,水化热大;水泥颗粒细,水化速度快;掺速凝剂时,其早期水化热多。
冬季施工,水化热有利于水泥的正常凝结硬化,防止产生冻害;而大体积混凝土施工,高水化热是不利的,容易产生温度应力裂缝。
6.密度与堆积密度
硅酸盐水泥的密度一般为3.1~3.2g/cm3,普通硅酸盐水泥、复合硅酸盐水泥略低,矿渣硅酸盐水泥为2.8~3.0g/cm3,火山灰硅酸盐水泥、粉煤灰硅酸盐水泥为2.7~2.9g/cm3。水泥堆积密度除与矿物组成、细度有关外,主要取决于堆积的紧密程度。一
般堆积密度为900~1200kg/m3,紧密状态下可达1600kg/m3。
水泥的密度、堆积密度是比较重要的两个物理指标,在进行混凝土、砂浆配合比设计和水泥贮运时都必须用到。
四、通用硅酸盐水泥的水化、凝结硬化与性能及应用
水泥与水发生的反应称为水泥的水化。通用硅酸盐水泥的水化过程及水化产物相当复杂,各种熟料矿物水化以及与混合材料的水化互有影响。
(一)硅酸盐水泥的水化
在硅酸盐水泥的水化过程中,就目前的认识,铝酸三钙立即发生水化反应,而后是硅酸三钙和铁铝酸四钙也很快水化,硅酸二钙水化最慢,生成了水化产物,并放出热量。水泥熟料单矿物水化反应式如下:
2(3CaO·SiO2 )+6H2O═══3CaO·2SiO2 ·3H2O+3Ca(OH)2 2(2CaO·SiO2 )+4H2O═══3CaO·2SiO2 ·3H2O+Ca(OH)2
3CaO·Al2O3+6H2O═══3CaO·Al2O3 ·6H2O
4CaO·Al2O3·FeO+7H2O═══3CaO·Al2O3·6H2O+CaO·Fe2O3·H2O

水泥熟料矿物中,硅酸三钙和硅酸二钙水化产物为水化硅酸钙和氢氧化钙,水化硅酸钙不溶于水,以胶粒析出,逐渐凝聚成凝胶体(CS H凝胶),氢氧化钙在溶液中很快达到饱和,以晶体析出;铝酸三钙和铁铝酸四钙水化后生成水化铝酸三钙和水化铁酸钙,水化铝酸三钙以晶体析出,水化铁酸钙以胶粒析出,而后凝聚成凝胶。
由于在硅酸盐水泥熟料中掺入了适量石膏,石膏与水化铝酸三钙反应生成了高硫型的
水化硫铝酸钙(3CaO·Al2O3 ·3CaSO4 ·31H2O),以针状晶体析出,也称为钙矾石。当
石膏耗尽后,部分高硫型的水化硫铝酸钙晶体转化为低硫型的水化硫铝酸钙晶体(3CaO·
Al2O3·CaSO4·12H2O)。水泥中掺入适量石膏,与C3A起反应,调节凝结时间,如不
掺入石膏或石膏掺量不足时,水泥会发生速凝现象。
各种水泥熟料矿物的水化特性,见表210。
表2 10
硅酸盐水泥熟料矿物的水化特性
由表29可知,水泥中各熟料矿物的含量,决定着水泥某一方面的性能,当改变各熟料矿物的含量时,水泥性质即发生相应的变化。例如,提高熟料中C3S和C3A的含量,可以制得快凝快硬的水泥;减少C3A和C3S的含量,而提高C2S的含量,可以制得水化热低的水泥。
综上所述,硅酸盐水泥与水作用后,生成的主要水化产物有:水化硅酸钙、水化铁酸钙凝胶体,氢氧化钙、水化铝酸钙和水化硫铝酸钙晶体。在完全水化的水泥石中,水化硅酸钙凝胶约占70%,氢氧化钙晶体约占20%,高硫型水化硫铝酸钙和低硫型水化硫铝酸
钙约占7%。
(二)硅酸盐水泥的凝结硬化
水泥用适量的水调和后,最初形成具有可塑性的浆体,随着时间的延长,水泥浆逐渐变稠失去塑性,但尚不具有强度的过程,称为水泥的“凝结”。随后产生明显的强度并逐渐发展成为坚硬的水泥石,此过程称为水泥的“硬化”。水泥的凝结硬化是人为地划分的,实际上是一个连续的复杂的物理化学变化过程。
水泥浆体由可塑态,逐渐失去塑性,进而硬化产生强度,这样一个物理化学变化过程,从物态变化可以分为四个阶段(即初始反应期、潜伏期、凝结期和硬化期)来描述。
水泥加水拌和,未水化的水泥颗粒分散在水中,成为水泥浆体,如图2 2(a)所示。水泥颗粒的水化从其表面开始,水和水泥一接触,水泥颗粒表面的水泥熟料先溶解于水,然后立即与水开始反应,或水泥熟料在固态直接与水反应,形成相应的水化物,水化

物溶解于水。由于各种水化物的溶解度很小,水化物的生成速度大于水化物向溶液中扩散的速度,一般在几分钟内,水泥颗粒周围的溶液成为水化物的过饱和溶液,先后析出水化硅酸钙凝胶、水化硫铝酸钙、氢氧化钙和水化铝酸钙晶体等水化产物,包在水泥颗粒的表面。在水化初期,水化物不多,包有水化物膜层的水泥颗粒之间还是分离的,因此水泥浆具有可塑性,如图2 2(b)所示。
图22 水泥凝结硬化过程示意图
(a)分散在水中未水化的水泥颗粒;(b)在水泥颗粒表面形成水化产物膜层;
(c)膜层增厚并互相连接;(d)水化产物进一步增多,填充毛细孔隙
1—水泥颗粒;2—水;3—凝胶;4—晶体;5—未水化的水泥颗粒内核;6—毛细孔
水泥颗粒不断被水化,随着水化时间的延长,新生水化物增多,使包在水泥颗粒表面的水化物膜层逐渐增厚,颗粒间的空隙逐渐缩小,而包有凝胶体的水泥颗粒则逐渐接近,以至相互接触,在接触点借助于范德华力,凝结成多孔的空间网络,形成凝聚结构,如图2 2(c)所示。凝聚结构的形成,使水泥浆开始失去可塑性,也就是水泥达到初凝,但此时还不具有强度。
随着以上过程的不断进行,固态的水化物不断增多,颗粒间的接触点数目不断增加,结晶体和凝胶体互相贯穿形成的凝聚———结晶网状结构不断加强。而固相颗粒之间的空隙(毛细孔)不断减小,结构逐渐紧密,使水泥浆体完全失去可塑性,达到能担负一定荷载的强度,此时称为水泥的终凝,由此开始进入硬化阶段,如图2 2(d)所示。
水泥的水化与凝结硬化是从水泥颗粒表面开始进行的,逐渐深入到水泥的内核。初始的水化速度较快,水化产物增长较快,水泥石的强度提高也快。由于水化产物增多,堆积在水泥颗粒周围,水分渗入到水泥颗粒内部的速度和数量大大减小,水化速度也随之大为降低,多数水泥颗粒内核很难完全水化。因此,硬化的水泥石中是由水化产物(凝胶体和晶体)、未水化的水泥颗粒内核、水(自由水和吸附水)和孔隙(毛细孔和凝胶孔)组成的非均质体。
(三)影响水泥凝结硬化的因素
水泥的凝结硬化过程,也就是水泥强度发展的过程。为了正确使用水泥,并能在生产中采取有效措施,调节水泥的性能,必须了解水泥凝结硬化的影响因素。影响水泥凝结硬化的因素,除矿物成分、细度、用水量外,还有养护时间、环境的温湿度以及石膏掺量等。
1.水泥矿物成分的影响
水泥的矿物组成成分及各组分的比例,是影响水泥凝结硬化的最主要因素。如前面所述,不同矿物成分单独和水反应时,所表现出来的特点是不同的。如水泥中提高C3A的含量,将使水泥的凝结硬化加快,同时水化热加大。一般来讲,若在水泥熟料中掺加混合材料,将使水泥的抗侵蚀性提高,水化热降低,早期强度降低。
2.水泥细度的影响
水泥颗粒的粗细直接影响水泥的水化、凝结硬化、强度增长及水化热等。这是因为水泥颗粒越细,其总表面积越大,与水的接触面积也越多,因此水化迅速,凝结硬化也相应加快,早期强度较高。但是,水泥颗粒如果过细,易与空气中的水分及二氧化碳反应,致使水泥不宜久存,过细的水泥硬化时产生的收缩也较大,水泥磨的越细,消耗能量多,成本较高。
3.石膏掺量的影响
石膏称为水泥的缓凝剂,主要用于调节水泥的凝结时间,是生产水泥不可缺少的组分。水泥熟料在不加入石膏的情况下,与水拌和会立即产生凝结,同时放出热量。其主要原因是由于熟料中C3A很快溶于水中,生成一种具有促凝作用的铝酸钙水化物,使水泥不能正常使用。
石膏起缓凝作用的机理是:水泥在水化时,石膏很快与C3A作用产生很难溶于水的水化硫铝酸钙(钙矾石),它沉淀在水泥颗粒表面形成保护膜,从而阻碍了C3A的水化反应并延缓了水泥的凝结时间。
石膏的掺量太少,缓凝效果不显著,过多掺入石膏,其本身会生成一种促凝物质,反而使水泥产生快凝。适宜的石膏掺量,主要取决于水泥中C3A的含量和石膏中SO3的含量,同时也与水泥细度及熟料中SO3的含量有关。石膏掺量一般为水泥重量的3%~5%,具体掺量应通过试验确定。若水泥中石膏掺量超过规定的限量时,会引起水泥强度的降低,严重时会引起水泥体积安定性不良,使水泥石产生膨胀性破坏。
4.养护条件的影响
养护环境有足够的温度和湿度,有利于水泥的水化和凝结硬化过程,有利于水泥的早期强度发展。如果环境湿度十分干燥时,水泥中的水分蒸发迅速,导致水泥不能充分水化,同时硬化也将停止,严重时会使水泥石发生裂缝。通常,养护时温度升高,水泥的水化速度加快,早期强度发展也快。若在较低的温度下(>0℃)硬化,虽强度发展较慢,但其最终强度不受影响。当温度低于0℃以下时,水泥的水化反应停止,强度不但不会增长,甚至会因水结冰而导致水泥石结构破坏。
5.龄期的影响
水泥的水化、凝结硬化是一个较长时期内不断进行的过程,随着水泥颗粒内各熟料矿物水化程度的提高,凝胶体不断增加,毛细孔不断减少,使水泥石的强度随龄期增长而增加。实践证明:水泥一般在7d内的强度发展最快,28d内的强度发展较快,28d以后增长缓慢。
6.拌和用水量的影响
在水泥用量不变的情况下,增加拌和用水量,会增加硬化水泥石中的毛细孔,降低水
泥石的强度,同时延长水泥的凝结时间。所以在实际工程中,水泥混凝土调整其流动性大小时,应在不改变水灰比的情况下,增减水泥浆的用量。为了保证混凝土的耐久性,还规定了最大水灰比和最小水泥用量。
7.外加剂的影响
硅酸盐水泥的水化、凝结硬化受C3S、C3A的制约,凡对C3S和C3A的水化能产生影响的外加剂,都能改变硅酸盐水泥的水化、凝结硬化性能。如加入适量促凝剂(CaCl2、Na2SO4等)就能促进水泥的水化、凝结硬化,提高早期强度。相反,掺加缓凝剂(如木钙、糖蜜类等)就会延缓水泥的水化、凝结硬化,影响水泥早期强度的发展。
(四)硅酸盐水泥的特性与应用
硅酸盐水泥的特性与其应用是相适应的,硅酸盐水泥具有以下特性与应用:
(1)凝结硬化快,强度高。由于硅酸盐水泥熟料中硅酸三钙和铝酸三钙含量高,所以硅酸盐水泥凝结硬化快,早期和后期强度高,主要用于重要结构的高强混凝土、预应力混凝土和有早强要求的混凝土工程。
(2)抗冻性好。由于硅酸盐水泥凝结硬化快,早期强度高,适合冬期施工。因为强度和密实度高,所以抗冻性好,因此适用于寒冷地区和严寒地区遭受反复冻融的混凝土工程。
(3)耐磨性好。由于硅酸盐水泥强度高,密实因此耐磨性好,可应用于路面和机场跑道等混凝土工程中。
(4)抗碳化性能好。由于硅酸盐水泥凝结硬化后,水化产物中氢氧化钙浓度高,水泥石的碱度高,再加上硅酸盐水泥混凝土的密实度高,开始碳化生成的碳酸钙填充混凝土表面的孔隙,使混凝土表面更密实,有效地阻止了进一步碳化。
(5)耐腐蚀性差。由于硅酸盐水泥熟料中硅酸三钙和铝酸三钙含量高,其水化产物中易腐蚀的氢氧化钙和水化铝酸三钙含量高,因此耐腐蚀性差,不宜长期使用在含有侵蚀性介质(如软水、酸和盐)的环境中。
(6)水化热高。由于硅酸盐水泥熟料中硅酸三钙和铝酸三钙含量高,水化热高且释放集中,不宜用于大体积混凝土工程中。
(7)耐热性差。硅酸盐水泥混凝土在温度不高时(100~250℃之间),尚存的游离水使水泥水化继续进行,混凝土的密实度进一步增加,强度有所提高。当温度高于250℃时,水泥中的水化产物氢氧化钙分解为氧化钙,如再遇到潮湿的环境,氧化钙熟化体积膨胀,使混凝土遭到破坏。当水泥受热约300℃时,水泥石中的部分结晶体水化物开始脱水,体积收缩,强度开始下降。温度达700~1000℃时,强度降低很多,甚至完全破坏。因此,硅酸盐水泥不宜应用于有耐热性要求的混凝土工程中。
(五)掺混合材料通用硅酸盐水泥的性能及应用
Ⅰ型硅酸盐水泥不掺混合材料,Ⅱ型硅酸盐水泥仅掺少于5%的混合材料,因此它的水化主要为硅酸盐水泥熟料及适量石膏与水发生的水化反应。普通硅酸盐水泥的混合材料掺量也相对较少,对水化影响不大,其性能与硅酸盐水泥接近。
其他掺混合材料通用硅酸盐水泥因混合材料掺量较大,硅酸盐水泥熟料先水化,即硅
酸三钙和硅酸二钙与水反应会生成水化硅酸钙凝胶和氢氧化钙,其中的氢氧化钙再与混合材料中活性的SiO2及Al2O3发生水化反应,称为“二次水化反应”。通常,掺入较多的混合材料会使水泥的水化速度减慢,对水泥的早期强度有影响;另外,发生的“二次水化反应”会降低水泥石中氢氧化钙的含量,对水泥性能会有较大的影响。水泥中掺入不同的混合材料,因水化反应有一定差异,水泥性能会有较大的差别。
1.矿渣水泥、火山灰质水泥、粉煤灰水泥的共同特点
(1)凝结硬化速度慢,早期强度低,但后期强度较高。由于这3种水泥的熟料含量较少,早强的熟料矿物量即相应减少,而“二次水化反应”在熟料水化之后才开始进行,因此这3种水泥的凝结硬化慢、早期强度低,均不适合有早强要求的混凝土工程。
(2)抗腐蚀能力强。3种水泥水化后的水泥石中,易遭受腐蚀的成分相应减少,其原因:一是“二次水化反应”消耗了易受腐蚀的Ca(OH)2 ,致使水泥石中Ca(OH)2的含量减少;二是这3种水泥中熟料含量少,水化后水化铝酸钙的含量也相应减少。因此,这3种水泥的抗腐蚀能力均比硅酸盐水泥和普通水泥强。适宜水工、海港等受软水和硫酸盐腐蚀的混凝土工程。
当火山灰质水泥采用的火山灰质混合材料为烧黏土质和黏土质凝灰岩时,由于这类混合材料中活性Al2O3多,使水化产物中水化铝酸钙含量增多,其含量甚至高于硅酸盐水泥。因此,这类火山灰质水泥不耐硫酸盐腐蚀。
(3)水化热低。这3种水泥中熟料含量少,因而放热量高的矿物成分C3S和C3A含量就少,因此这3种水泥水化放热速度慢,放热量低,适宜大体积混凝土工程。
(4)硬化时对温湿度敏感性强。
这3种水泥水化时对养护温度很敏感,低温情况下凝结硬化速度显著减慢,不宜进行冬季施工。而在湿热条件下(如采用蒸汽养护),可明显加快“二次水化反应”的速度,凝结硬化速度可大大加快,可获得比硅酸盐水泥更为明显的强度增长效果,所以适合于采用蒸汽养护的混凝土预制构件厂。
(5)抗碳化能力差。这3种水泥的水化产物中Ca(OH)2较少,水泥石的碳化速度较快,对防止混凝土中钢筋的锈蚀不利;又因碳化会造成其他水化产物的分解,使硬化的水泥石表面产生“起粉”现象。所以,这3种水泥不宜用于二氧化碳浓度较高的环境。
(6)抗冻性差。由于这3种水泥掺入了较多的混合材料,水泥的强度等级有所降低;且水泥需水量增加,水分蒸发后造成毛细孔通道粗大和增多,对混凝土抗冻不利,因此这三种水泥不宜用于严寒地区,特别是严寒地区水位经常变动的部位。
2.矿渣水泥、火山灰质水泥、粉煤灰水泥各自具有的特点
(1)矿渣水泥的耐热性好,保水性差,干缩较大,抗渗性差。由于硬化后,矿渣水泥石中的氢氧化钙含量减少,且矿渣本身又耐热,因此矿渣水泥耐热性好,适宜用于高温环境。而由于矿渣水泥中的矿渣不容易磨细,其颗粒平均粒径大于硅酸盐水泥的粒径,且磨细后具有尖锐棱角,因此矿渣水泥保水性差、易泌水、抗渗性差。
(2)火山灰质水泥具有较高的抗渗性。由于火山灰质水泥密度较小,水化需水量较大,其拌和物不易产生泌水,硬化后的水泥石较密实。因此火山灰质水泥具有良好的抗渗性,适用于有抗渗性要求的混凝土工程中。

另外,火山灰质水泥在干热条件下容易产生干缩裂缝。同时,在干燥空气中,火山灰质水泥石中水化硅酸钙与二氧化碳反应,在硬化的水泥石表面生成碳酸钙和二氧化硅等粉状物质,此现象称为“起粉”。在实际混凝土工程中,为防止火山灰质水泥形成干缩裂缝和起粉,应加强养护,并适当延长保湿时间。因此火山灰质水泥不适合于干燥环境中的混凝土工程。
(3)粉煤灰水泥的抗裂性较好。由于粉煤灰具有独特的球形玻璃态结构,吸附水的能力差,粉煤灰水泥的标准稠度需水量小(与矿渣水泥和火山灰质水泥相比),因此干缩小、抗裂性好,适用于有抗裂性要求的混凝土工程中。
复合硅酸盐水泥是掺两种或两种以上混合材料的水泥,其性能取决于所掺混合材料的种类、掺量及相对比例,使用时应针对工程的性质加以选用。
将掺混合材料通用硅酸盐水泥的性能特点及适用、不适用范围汇总见表211。
表2 11
其他品种通用硅酸盐水泥的性能及适用、不适用范围
五、通用硅酸盐水泥的选用
以上6种通用硅酸盐水泥,广泛应用在我国混凝土及钢筋混凝土工程中。针对一些混凝土及钢筋混凝土工程,在选用水泥时,应考虑混凝土的工程结构特点及工程所处环境,在满足上述条件下尽量降低成本。关于通用水泥的选用,见表212。

表2 12
通用水泥的选用
六、水泥石的腐蚀与防止(一)水泥石的腐蚀
通用硅酸盐水泥硬化后形成的水泥石,在正常的环境条件下,有较好的耐久性。但当水泥石长期处于有某些腐蚀性介质环境中时,会引起水泥石强度降低,严重的甚至引起混凝土的破坏,这种现象称为水泥石的腐蚀。
水泥石的腐蚀主要有:软水腐蚀、酸性腐蚀、盐类腐蚀和强碱腐蚀等。1.软水腐蚀(溶出性侵蚀)
软水腐蚀又称淡水侵蚀或溶出性侵蚀。雨水、雪水、蒸馏水、工业冷凝水及含重碳酸盐很少的河水及湖水都属于软水。当水泥石长期与这些水分相接触时,水泥中的氢氧化钙最先溶出(每升水中能溶解氢氧化钙1.3g以上)。在静水及无压力水作用下,由于周围的水易被溶出的氢氧化钙所饱和而使溶解作用停止,溶出仅限于结构的表面,所以影响不大。但是,若水泥石在流动的水中或有压力的水中,溶出的氢氧化钙不断被冲走。由于石灰浓度的继续降低,还会引起其他水化物的分解溶解。侵蚀作用不断深入内部,使水泥空隙增大,强度逐渐下降,使水泥石结构遭受进一步破坏,以致全部溃裂。
溶出性侵蚀的强弱程度,与水质的暂时硬度(每升水中重碳酸盐含量以CaO计为10mg时)有关。当水质较硬时,氢氧化钙的溶解度较小,同时水中的重碳酸盐与水泥石中的氢氧化钙反应,生成几乎不溶于水的碳酸钙,沉积在水泥石的孔隙内,不仅起到密实的作用,而且还可阻止外界水的渗入和内部氢氧化钙的溶出。其化学反应方程式为:
Ca(OH)2+Ca(HCO3 )2═══2CaCO3+2H2O
在实际工程中,将与软水接触的水泥构件事先在空气中硬化一定时间,形成碳酸钙外壳,可对溶出性侵蚀起到防止作用。
2.碳酸性腐蚀
在工业污水、地下水中常溶解有较多的二氧化碳。水中的二氧化碳与水泥石中的氢氧化钙反应,所生成的碳酸钙如继续与含碳酸的水作用,则变成易溶解于水的碳酸氢钙,由于碳酸氢钙的溶失以及水泥石中其他产物的分解,而使水泥石结构破坏。其化学反应方程式为:
Ca(OH)2+CO2+H2O═══CaCO3+2H2O
CaCO3+CO2+H2O㊣㊣Ca(HCO3)2
碳酸钙与含碳酸的水进行的反应,是一种可逆反应。当水中的二氧化碳含量较多时,上述反应向右进行,将水泥石中微溶于水的氢氧化钙转变为易溶于水的碳酸氢钙,从而加速了溶解速度,使水泥石的孔隙增加。同时,由于氢氧化钙浓度的降低,也会引起其他水化物的分解,使腐蚀作用进一步加剧。
3.一般酸性腐蚀
在工业废水、地下水、沼泽水中常含有一定量的无机酸和有机酸。各种酸类对水泥石均有不同程度的侵蚀作用。它们与水泥石中的氢氧化钙作用后生成的化合物,或者易溶于水,或者产生体积膨胀,导致水泥石破坏。并且由于氢氧化钙被大量消耗,引起水泥石的碱度降低,促使其他水化物大量分解,从而会引起水泥石强度的急剧下降。
各类酸中对水泥石腐蚀作用最快的是无机酸中的盐酸、氢氟酸、硝酸、硫酸等,有机酸中的醋酸、蚁酸和乳酸等。如盐酸(HCl)和硫酸(H2SO4)与水泥石中的氢氧化钙作用,分别生成易溶于水的氯化钙(CaCl2)和体积膨胀的二水石膏(CaSO4·2H2O):
2HCl+Ca(OH)2═══CaCl2+2H2O H2SO4+Ca(OH)2═══CaSO4 ·2H2O
生成的二水石膏或者在水泥石孔隙中产生膨胀破坏,或者再与水泥石中的水化铝酸钙作用,生成高硫型水化硫铝酸钙,其破坏性更大。
4.强碱腐蚀
碱类溶液在浓度不大时,一般对水泥石没有大的侵蚀作用,可以认为是无害的。但铝酸盐含量较高的硅酸盐水泥在遇到强碱(NaOH、KOH)时,会受到侵蚀破坏。其化学反应式为:
3CaO·Al2O3+6NaOH═══3Na2O·Al2O3+3Ca(OH)2
以上反应生成的铝酸钠易溶于水。当水泥石被NaOH浸透后,又在空气中干燥,水
泥石中 NaOH会与空气中的 CO2作用,2NaOH+CO2 ═══Na2CO3+H2O,生成的
Na2CO3在水泥石毛细孔中结晶沉积,使水泥石胀裂。
5.硫酸盐腐蚀
绝大多数的硫酸盐(硫酸钡除外)对水泥石都有显著的侵蚀作用,这主要是由于硫酸盐与水泥石中的氢氧化钙起置换反应,生成硫酸钙(二水石膏),硫酸钙再与水泥石中固态的水化铝酸钙作用,生成比原体积增加1.5倍以上的高硫型水化硫铝酸钙。
3CaO·Al2O3 ·6H2O+3(CaSO4 ·2H2O)+19H2O═══
3CaO·Al2O3 ·3CaSO4 ·31H2O
高硫型水化硫铝酸钙也称钙矾石,为针状晶体,体积膨胀较大(1.5~2.5倍),对水泥石有极大的破坏作用,所以俗称“水泥杆菌”。总之,硫酸盐的腐蚀实质上是一种膨胀性化学腐蚀。
6.镁盐的腐蚀
在地下水、海水及某些工业废水中,常有氯化镁、硫酸镁等镁盐存在,这些镁盐会与水泥石中的氢氧化钙反应,生成可溶性钙盐及无胶结能力的松散物氢氧化镁,其化学反应方程式为:
Ca(OH)2+MgCl2═══CaCl2+Mg(OH)2
Ca(OH)2+MgSO4═══CaSO4 ·2H2O+Mg(OH)2
因此,硫酸镁对水泥石起镁盐和硫酸盐的双重腐蚀作用。
综上所述,从结果来看,水泥石腐蚀的类型可分为两类:一类是水泥中的某些水化产物逐渐溶失;另一类是水泥的水化产物与腐蚀性介质反应,产物或是易溶于水,或是松散无胶结能力,或是结晶膨胀。
在实际工程中,由于环境介质比较复杂,单一介质对水泥石造成的腐蚀几乎不存在,而是几种腐蚀类型同时存在,相互影响。造成水泥石腐蚀的外在原因为腐蚀性介质;内在原因包括两方面:一方面是水泥石中存在着氢氧化钙和水化铝酸钙等易腐蚀的组分;另一方面是水泥石本身不密实,内部存在很多腐蚀性介质容易进入的毛细孔通道。
(二)水泥石腐蚀的防止
实际工程中针对具体情况可采取以下防止措施。
1.合理选择水泥品种
根据侵蚀环境特点,合理选用水泥品种。如当水泥石遭受软水侵蚀时,可选用水化物中氢氧化钙含量较少的水泥(如选用硅酸三钙含量低的水泥);当水泥石遭受硫酸盐侵蚀时,可选用铝酸三钙含量较低的抗硫酸盐水泥;又如选用掺混合材料水泥,可提高水泥的抗腐蚀能力。
2.提高水泥石密实度
提高施工质量,以提高水泥石的密实度,这是防止水泥石腐蚀的重要措施。水泥石的密实度越高,其抗渗透能力越强,环境中的侵蚀介质越难渗入。因此,在施工中应合理选择水泥混凝土的配合比,尽量降低水灰比,改善集料级配,掺加外加剂等措施提高其密实度。另外,还可在混凝土表面进行碳化处理,使其表面进一步密实,也可减少侵蚀介质渗入内部。
3.表面加作保护层
当侵蚀作用较强,上述防止措施不能奏效时,可在水泥石的表面加一层耐侵蚀介质的材料,如耐酸石材、玻璃、陶瓷、沥青、涂料、塑料等。
七、水泥的验收、包装与标志、运输与储存
水泥是土木工程建设中最重要的材料之一,是决定混凝土性能和价格的重要原料,在工程中,水泥的验收、运输与储存是保证工程质量、杜绝质量事故的重要措施。
1.水泥的验收
水泥的出厂检验项目为化学指标、凝结时间、安定性和强度。检验结果符合化学指标、凝结时间、安定性和强度的规定为合格品,检验结果不符合化学指标、凝结时间、安定性和强度中的任何一项技术要求为不合格品。经确认水泥各项技术指标及包装质量符合要求时方可出厂。
2.水泥的包装与标志
水泥可以散装或袋装,袋装水泥每袋净含量为50kg,且应不少于标志质量的99%;随机抽取20袋的总质量(含包装袋)应不少于1000kg。
水泥包装袋上应清楚标明:执行标准、水泥品种、代号、强度等级、生产者名称、生产许可证标志(QS)及编号、出厂编号、包装日期、净含量。包装袋两侧应根据水泥的品种采用不同的颜色印刷水泥名称和强度等级,硅酸盐水泥和普通硅酸盐水泥采用红色,矿渣硅酸盐水泥采用绿色;火山灰质硅酸盐水泥、粉煤灰硅酸盐水泥和复合硅酸盐水泥采用黑色或蓝色。
散装发运时应提交与袋装标志相同内容的卡片。3.水泥的运输与储存
水泥在运输与储存时不得受潮和混入杂物,应按不同品种、强度等级和出厂日期分别加以标明、分别堆放、不得混装。堆放时应离墙和门窗的距离大于200mm,地面应垫高300mm以上。水泥储存时应先存先用,对散装水泥应分库存放,而袋装水泥一般堆放高度不超过10袋。不同品种、不同生产厂家的水泥不得混用。
水泥存放不可受潮,受潮的水泥表现为结块,凝结速度减慢,强度降低。对于结块水泥的处理方法为:有结块但无硬块时,可压碎粉块后按实测强度等级使用;对部分结成硬
块的,可筛除或压碎硬块后,按实测强度等级用于非重要的部位,如垫层、散水及填充墙的砌筑砂浆不能用于主体结构混凝土中。对于大部分结块的,不能作水泥用,可作混合材料掺入到水泥中,掺量不超过25%。水泥的储存期不宜太久,常用袋装水泥一般不超过3个月,因为3个月后水泥强度会降低10%~20%,6个月后降低15%~30%,1年后降低25%~40%,铝酸盐水泥一般不超过2个月。密闭保存的散袋水泥的储存期可延长。过期水泥应重新检测,按实测强度使用。