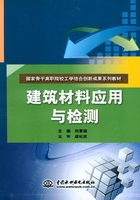
任务3.1 通用硅酸盐水泥的认识
任务导航:
任务内容及要求

水泥是一种粉状材料,它与水拌和后,经水化反应随着时间的进行浆体由稀变稠,最终形成坚硬的水泥石。水泥水化过程中还可以将砂、石等散粒材料胶结成整体而形成各种水泥制品。所以水泥不仅大量应用于水利水电工程中,还广泛应用于工业与民用建筑、交通、道路与桥梁工程和国防建设等工程。
根据国家标准水泥命名原则的规定,将水泥分为三大类别。具体分类见表3.1。
表3.1
水泥按性能和用途分类

3.1.1 通用硅酸盐水泥的组成材料
通用硅酸盐水泥由硅酸盐熟料、适量石膏及规定的混合材料而制成的水硬性胶凝材料。其中硅酸盐熟料是由石灰石、黏土和铁矿粉按照一定的比例配合,经过磨细、煅烧后形成。通用硅酸盐水泥的生产过程可简化为四个字:“两磨一烧”。其生产流程如图3.1所示,工艺设备如图3.2所示。

图3.1 通用硅酸盐水泥的生产工艺流程示意图

图3.2 水泥生产线工艺设备示意图
3.1.1.1 熟料
通用硅酸盐水泥熟料由主要含CaO、SiO2、Al2O3、Fe2O3的原料,按适当比例磨成细粉烧至部分熔融所得以硅酸钙为主要矿物成分的水硬性胶凝物质,即主要为硅酸三钙
3CaO·SiO2、硅酸二钙2CaO·SiO2、铝酸三钙3CaO· Al2O3、铁铝酸四钙4CaO·
Al2O3·Fe2O3四种矿物。其中硅酸钙矿物不小于66%,氧化钙和氧化硅质量比不小
于2.0。
3.1.1.2 石膏
在水泥生产过程中加入适量石膏可以延缓水泥的凝结时间,以满足使用的要求。但是石膏掺量不宜过高,否则会导致水泥石膨胀性破坏。
所加入的石膏可以是天然石膏和工业副产石膏。天然石膏应符合GB/T5483中规定的G类或M类二级(含)以上的石膏或混合石膏。工业副产石膏是以硫酸钙为主要成分的工业副产物。采用前应经过试验证明对水泥性能无害。
3.1.1.3 混合材料
生产水泥时,为了改善硅酸盐水泥的某些性能或调节水泥强度等级,在水泥熟料中掺入人工或天然矿物材料称为混合材料。混合材料分为活性混合材料和非活性混合材料。
1.活性混合材料
活性混合材料是具有水硬性或潜在水硬性的矿物材料,它能够与水泥水化产物发生化学反应。不但可以改善水泥的某些性能,扩大使用范围,而且还能充分利用工业废渣。
常用的活性混合材料有粒化高炉矿渣、粒化高炉矿渣粉、粉煤灰、火山灰质混合材料。
2.非活性混合材料
非活性混合材料是指在水泥中主要起填充作用,而又不损害水泥性能的矿物材料。非活性混合材料经过磨细后,掺加到水泥中,可以调节水泥强度,节约水泥熟料,提高水泥产量,降低水泥成本,降低水泥的水化热。
常用的非活性混合材料主要有磨细的石灰岩、砂岩及其他活性指标低于国家标准规定的活性混合材料。
通用水泥按照混合材料的品种和掺量分为硅酸盐水泥、普通硅酸盐水泥、矿渣硅酸盐水泥、火山灰硅酸盐水泥、粉煤灰硅酸盐水泥和复合硅酸盐水泥。各品种的代号和组分应符合表3.2的规定。
表3.2
通用硅酸盐水泥的代号和组分
%

续表

a 本组分材料为符合通用硅酸盐水泥(GB175—2007)5.2.3的活性混合材料,其中允许用不超过水泥质量8%且
符合通用硅酸盐水泥(GB175—2007)5.2.4的非活性混合材料或不超过水泥质量5%且符合通用硅酸盐水泥
(GB175—2007)5.2.5的窑灰代替。
b 本组分材料为符合GB/T203或GB/T18046的活性混合材料,其中允许用不超过水泥质量8%且符合通用硅酸
盐水泥(GB175—2007)第5.2.3条的活性混合材料或符合通用硅酸盐水泥(GB175—2007)第5.2.4条的非
活性混合材料或符合通用硅酸盐水泥(GB175—2007)第5.2.5条的窑灰中的任一种材料代替。c 本组分材料为符合GB/T2847的活性混合材料。
d 本组分材料为符合GB/T1596的活性混合材料。
e 本组分材料为由两种(含)以上符合通用硅酸盐水泥(GB175—2007)第5.2.3条的活性混合材料或/和符合通
用硅酸盐水泥(GB175—2007)第5.2.4条的非活性混合材料组成,其中允许用不超过水泥质量8%且符合通用硅酸盐水泥(GB175—2007)第5.2.5条的窑灰代替。掺矿渣时混合材料掺量不得与矿渣硅酸盐水泥重复。
3.1.2 通用硅酸盐水泥的水化、凝结硬化
3.1.2.1 水化
通用硅酸盐水泥遇水后,各熟料矿物与水发生复杂的物理、化学反应,并释放热量,这一过程称为水化,其反应式如下:
3CaO·SiO2+6H2O═══3CaO·2SiO2 ·3H2O(胶体)+3Ca(OH)2 (晶体)2CaO·SiO2+4H2O═══3CaO·2SiO2 ·3H2O+Ca(OH)2 (晶体)
3CaO·Al2O3+6H2O═══3CaO·Al2O3 ·6H2O(晶体)
4CaO·Al2O3·Fe2O3+7H2O═══3CaO·Al2O3·6H2O+CaO·Fe2O3·H2O(胶体)
通用硅酸盐水泥熟料中各主要矿物的水化特性见表3.3。
表3.3
通用硅酸盐水泥熟料中各主要矿物的水化特性

随着水化反应的进行,水泥组成材料中的石膏与部分水化铝酸钙反应,生成难溶的水化硫铝酸钙(也称为钙矾石)的针状晶体,最早生成的水化硫铝酸钙包裹着部分熟料,阻挡了熟料与水的接触,从而延缓了水泥的凝结时间。
综上所述,通用硅酸盐水泥水化反应后,生成的水化产物有胶体和晶体,其结构称为水泥凝胶体。水化产物水化硅酸钙约占50%、氢氧化钙约占25%、水化硫铝酸钙约占7%。水化产物水化硅酸钙和水化铁酸钙为胶体,水化铝酸钙、水化硫铝酸钙和氢氧化钙为晶体。
3.1.2.2 凝结硬化
通用硅酸盐水泥的凝结硬化分为三个阶段:初凝、终凝与硬化。
初凝:随着水化反应的进行,水泥浆体逐渐失去流动性和部分可塑性,此时尚未具有强度,此状态即为初凝。

终凝:当水化反应不断深入并加速进行时,水泥浆体将产生越多的凝胶和晶体水化物,各颗粒交错连接成网,最终使得浆体完全失去可塑性,并具有一定的强度。此状态即为终凝。
图3.3 水泥石结构示意图
A—未水化水泥颗粒;B—凝胶体;C—晶体;D—毛细孔(毛细孔内水);E—凝胶孔
硬化:当水化反应进一步进行,水化产物随着时间的延续也增加,水泥浆体的网络结构更加致密,强度大大提高,并逐渐变成坚硬的水泥石(其结构如图3.3所示),此即硬化。
水泥的水化和凝结硬化过程是连续的。水化是
凝结硬化的前提,而凝结硬化是水化的结果。凝结标志着水泥浆失去流动性而具有了塑性强度,硬化则表示水泥浆固化后的网状结构具有一定的强度。
3.1.2.3 影响水泥石强度发展的因素
1.熟料矿物组成
由于各矿物的组成比例不同、性质不同,对水泥性质的影响也不同。C3A的水化和凝结硬化速度最快,是影响水泥凝结时间的主要因素,加入石膏可延缓水泥凝结,但石膏掺量不能过多;当C3S和C3A含量较高时,水泥凝结硬化快、早期强度高,水化放热量大。熟料矿物对水泥性质的影响是各矿物的综合作用,不是简单叠加,其组成比例是影响水泥性质的根本因素,调整比例结构可以改善水泥性质和产品结构。
2.水泥细度
水泥细度是指水泥颗粒的粗细程度,其影响水泥的水化速率、凝结硬化等性质。因为水泥的水化是从颗粒表面逐步向内部发展的,颗粒越细小,其表面积越大,与水的接触面积就越大,水化作用就越迅速越充分,使凝结硬化速率加快,早期强度越高。但水泥颗粒过细时,硬化时会产生较大的体积收缩,同时水分蒸发产生较多的孔隙,会使水泥石强度下降。因此,水泥的细度要控制在一个合理的范围。
3.拌和用水量
通常水泥水化时的理论需水量大约是水泥质量的23%左右,但为了使水泥浆体具有一定的流动性和可塑性,实际的加水量远高于理论需水量,不参加水化的“多余”水分,
使水泥颗粒间距增大,会延缓水泥浆的凝结时间,并在硬化的水泥石中蒸发形成毛细孔,拌和用水量越多,水泥石中的毛细孔越多,孔隙率就越高,水泥的强度越低,硬化收缩越大,抗渗性、抗侵蚀性能就越差。
4.养护湿度、温度
水化反应是水泥凝结硬化的前提。因此,水泥加水拌和后,必须保持湿润状态,以保证水化进行和获得强度增长。若水分不足,会使水化停止,同时导致较大的早期收缩,甚至使水泥石开裂。提高养护温度,可加速水化反应,提高水泥的早期强度,但后期强度可能会有所下降。硅酸盐水泥的水化硬化较快,早期强度高,若采用较高温度养护,反而还会因水化产物生长过快,损坏其早期结构网络,造成强度下降。因此,硅酸盐水泥不宜采用蒸汽养护等湿热方法养护。
5.养护龄期
水泥的水化硬化是一个长期不断进行的过程。随着养护龄期的延长,水化产物不断积累,水泥石结构趋于致密,强度不断增长。由于熟料矿物中对强度起主导作用的C3S早期强度发展快,使硅酸盐水泥强度在3~14d内增长较快,28d后增长变慢,长期强度还有增长。
6.储存条件
水泥应该储存在干燥的环境里。如果水泥受潮,其部分颗粒会因水化而结块,从而失去胶结能力,强度严重降低。即使是在良好的干燥条件下,也不宜储存过久。
3.1.3 通用硅酸盐水泥的特性及应用
通用硅酸盐水泥是建筑工程中用途最广,用量最大的水泥。通用硅酸盐水泥的成分及
特性见表3.4。
表3.4
通用硅酸盐水泥的成分及特性

续表

以上六种通用硅酸盐水泥的特性,也决定了其用途,其适用范围见表3.5。
表3.5
通用硅酸盐水泥的选用

续表
