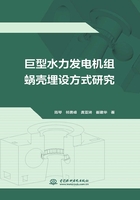
2.3 右岸电站保压浇蜗壳流道及外围混凝土结构静力分析
2003年,三峡左岸电站第一批机组投产发电。由于垫层蜗壳埋设方式具有施工方便、工期短、造价低等保压蜗壳埋设方式所难以替代的优点,2005年,经长江勘测设计研究院推荐并经长江三峡集团总公司批准,决定在右岸电站部分机组采用垫层方案。为保证机组的安全可靠运行,对垫层方案进行了进一步的研究。同时,为便于全面比较蜗壳不同埋设方式技术性能上的差别,对蜗壳采用保压埋设方式流道系统的刚、强度和外围混凝土进行三维有限元计算分析。本节为静力分析研究成果。
2.3.1 计算模型、计算条件及计算方案
1.计算模型
计算选取一个机组段,顺水流向的模拟范围为厂房上游墙的上游面(桩号20+118.0)至下游墙的下游面,高度方向的模拟范围为高程40.00~67.00m。高程40.00m处的位移全约束。止推环设置在桩号20+121.7处。直管段桩号20+118~20+123.8上半圆包垫层。
计算模型见图2.3-1~图2.3-4,模拟了混凝土、蜗壳钢板、座环、固定导叶、止推环、闷头及密封环,蜗壳钢板、闷头、密封环的厚度均按照实际厚度模拟。共划分实体单元40049个,结点47614个。

图2.3-1 计算模型(一半)

图2.3-2 蜗壳、闷头、座环、密封环

图2.3-3 蜗壳充水保压模型

图2.3-4 保压浇筑外围二期混凝土
坐标轴以机组中心为原点,x轴指向下游为正,y轴指向左岸为正,z轴竖直向上。
蜗壳保压浇筑混凝土方式是涉及蜗壳充水打压、保压浇筑外围混凝土、卸压和重新加压的复杂过程,为了尽可能真实反映保压方案的结构受力情况,计算中模拟了以下施工过程:
(1)一期混凝土及支墩的自重(图2.3-3中蜗壳以外的部分,包括上、下游墙)。
(2)蜗壳充水打压(70.00m水头,图2.3-3)。
(3)保压浇筑外围二期混凝土(图2.3-4)。
(4)卸压,拆除闷头和密封环。
(5)浇筑三期混凝土(图2.3-4中混凝土的空缺部分,位于上游墙附近)。
(6)重新加压(计算水头139.50m)。
2.材料参数
(1)混凝土:弹性模量28GPa,泊松比0.167,容重25kN/m3。
(2)钢材:弹性模量210GPa,泊松比0.3,容重78.5kN/m3。
(3)垫层:弹性模量2.5MPa,厚度为3cm,采用正交各向异性模型,只考虑法向刚度。
3.荷载
(1)蜗壳内水压力:考虑水锤作用的内水压力,机组中心高程57.00m处为1.395MPa。计及水重影响,保压水头为70.00m。
(2)结构自重:包括混凝土、蜗壳钢板、座环和固定导叶的自重。
(3)机组荷载:①定子基础负荷,共20个基础,每个基础荷载为轴向708kN,径向266kN;②下机架基础负荷,共12个基础,每个基础荷载为轴向4266kN,径向29kN;③F1为座环上的垂直力,F1=62100kN,方向向上,作用于上座环处。
(4)水轮机层楼面荷载20kN/m2。
4.计算方案
方案1:设止推环。
方案2:不设止推环。
两种方案均设置伸缩节。钢管与混凝土之间:在未包垫层的区域,混凝土与钢板之间按摩擦接触考虑,摩擦系数取为0.25。
5.成果整理断面
如图2.3-5所示,截取以下13个断面整理计算成果:
断面1:进口段,x=-18.0m。
断面2:进口段,x=-12.7m。
断面3:进口段,x=-9.8m。
断面4:进口段,x=-6.4m。
断面5:进口段,x=-3.2m。
断面6:θ=0°。
断面7:θ=45°。
断面8:θ=90°。
断面9:θ=135°。
断面10:θ=180°。
断面11:θ=225°。
断面12:θ=270°。
断面13:θ=293°。
其中,坐标轴原点位于机组中心,θ为水平面上与y轴的夹角,断面1~断面6为直管段。以上各断面内的混凝土特征点位置见图2.3-6。

图2.3-5 典型断面位置示意图

图2.3-6 断面内特征点位置示意图
2.3.2 计算成果
1.蜗壳变形
充水打压(70.00m水头)时,主要是横断面内沿径向的变形,横河向(y向)和垂直方向(z向)的位移渲染见图2.3-7,卸压前后的位移之差和重新加压前后的位移差见图2.3-8。

图2.3-7 蜗壳充水打压时的位移渲染(单位:mm)

图2.3-8 蜗壳位移的变化(位移的绝对值,单位:mm)
充水打压时,蜗壳直管段向左侧偏移,最大偏移量位于直管段高程54.00m附近(第一个支墩外侧),横河向的最大位移达到21mm,同时还伴随着垂直方向的向下位移,最大值约为11mm。卸压前后,此处的位移变化达到12mm,说明卸压后钢管的回退量大,从而造成大的间隙量,重新加压后蜗壳变形空间相对就大,与加压前相比最大位移差也为12mm。这种变化过程也可以从图2.3-9的断面6处蜗壳变形中反映出来。

图2.3-9 断面6蜗壳变形图
充水打压时,蜗壳底部在支墩之间的变形要大于支墩处的变形,因此卸压后的间隙量也会大于支墩处。
蜗壳充水时的位移主要由两方面因素组成:平均水压力引起的沿径向的均匀膨胀位移和水重引起的沿竖向的向下位移,分别与蜗壳的环向刚度和竖向刚度有关。由于钢管很薄,竖向刚度要远小于环向刚度,因此当充水打压的水头较低时,在直管段的较大变形主要是由水重和蜗壳自重引起的,表现在其顶部为11mm的向下位移。
计算模拟了施工过程,蜗壳变形呈现出一定的不均匀性,从而在蜗壳和混凝土之间的间隙的变化和传压上也会体现出这种不均匀性。
表2.3-1和表2.3-2给出前述施工过程的第(6)步(即重新加压后相对于加压前)的蜗壳及座环的切向位移,用于反映蜗壳绕机组中心竖轴的扭转变形。
表2.3-1 典型断面管腰部钢板与混凝土的切向相对位移 单位:mm

注 表中数值为重新加压前后的变化,切向相对位移以顺水流方向为正。
表2.3-2 座环切向位移 单位:mm

从表2.3-1和表2.3-2可看出,在内水压力作用下,蜗壳存在绕机组中心竖轴的扭转变形,且主要在蜗壳的左半部分(断面1~断面8)。不设止推环(方案2),管腰部钢板与混凝土的切向相对位移,断面1处的最大值达到3.96mm,而设止推环(方案1)在相同部位仅为0.38mm,减小了约3.6mm,在断面6、断面7、断面8处切向相对位移分别减小2.45mm、1.71mm和1.04mm,座环上(下)环板的切向位移分别减小0.34mm(0.18mm)、0.18mm(0.18mm)和0.08mm(0.12mm)。因此,止推环对减小蜗壳绕轴心的切向位移作用明显。
2.钢板与混凝土的接触状态
蜗壳卸压后和重新加压前,蜗壳钢板与混凝土间间隙见图2.3-10和表2.3-3。

图2.3-10 方案1 重新加压前蜗壳钢板与混凝土之间的间隙(单位:mm)
表2.3-3 方案1(设止推环)蜗壳钢板与混凝土之间的间隙 单位:mm

卸压后,蜗壳钢板与混凝土之间大部分为脱开状态,在支墩处闭合。最大间隙位于直管段高程54.00m附近的外侧,达到9~10mm。顶部最大间隙量为1.6mm左右,底部最大间隙量位于直管段支墩之间(断面3),超过3mm。除直管段外,间隙量为腰部>顶部>底部。重新充水至127.00m水位后,大部分闭合或间隙量很小。
在不同水位下,方案1蜗壳钢板与混凝土之间的传压见表2.3-4。
表2.3-4 方案1(设止推环)蜗壳与混凝土间的传压 单位:MPa

由于施工过程中蜗壳变形的不均匀性,造成卸压后蜗壳钢板与混凝土之间的间隙分布的不均匀性。但重新充水后传压分布的不均匀性要小,只在底部支墩处传压稍大。这是因为,重新充水后蜗壳沿着卸压时的路径反向变形,在127.00m水位时回到接近于卸压前70.00m水头的状态,此时,除底部支墩处有一定的传压(约0.5MPa)外,其他区域传压较小。然后蜗壳与混凝土联合承担剩余的水压力。
作用全部荷载后,蜗壳和混凝土之间的传压一般为0.6~0.7MPa,约占全部水压(1.395MPa)的45%,底部支墩处稍大,为0.8~0.9MPa。钢管进口段顶部包垫层,传压小,底部为摩擦接触,传压超过1.0MPa。
不设止推环方案的传压见表2.3-5,与表2.3-4比较可见,在进口段的传压稍大于设止推环方案,其他区域数值接近。
3.混凝土应力
表2.3-6和表2.3-7分别列出方案1和方案2的各典型断面特征点混凝土环向应力。典型断面最大主应力分布线见图2.3-11~图2.3-15。
表2.3-5 方案2(不设止推环)蜗壳与混凝土间的传压 单位:MPa

表2.3-6 混凝土特征点环向应力(方案1:设止推环) 单位:MPa

表2.3-7 混凝土特征点环向应力(方案2:不设止推环) 单位:MPa

(1)由于直管段外侧的混凝土较薄,各特征点2MPa以上的环向拉应力出现在直管段的断面1~断面6,一般位于混凝土内表面及腰部外侧,腰部外侧的最大环向拉应力达3MPa以上。断面13由于受到直管段以及自身断面内的两方面内水压力作用,也出现了2MPa以上的拉应力。断面7~断面12的环向拉应力小于2MPa。

图2.3-11 断面3混凝土最大主应力分布线图(单位:MPa)

图2.3-12 断面6混凝土最大主应力分布线图(单位:MPa)

图2.3-13 断面8混凝土最大主应力分布线图(单位:MPa)

图2.3-14 断面10混凝土最大主应力分布线图(单位:MPa)

图2.3-15 断面12混凝土最大主应力分布图(单位:MPa)
(2)两种方案的环向应力接近。在直管段,方案1的应力总体上稍小一些(断面2和断面13除外),这是因为止推环限制了其附近钢板的向外膨胀,但应力差别小于0.3MPa。其他断面的应力差别一般不超过0.2MPa。
4.蜗壳钢板及座环应力
运行期(含水击压力),断面6处(0°断面)的蜗壳钢板环向应力分布见图2.3-16,蜗壳钢板等效应力云图见图2.3-17。在支墩附近,蜗壳钢板出现环向的弯曲应力,这与打压时的蜗壳变形有关。在第一个支墩附近(断面3)的高程52m处,蜗壳外表面最大环向应力达到170MPa左右,而内表面仅为67MPa。某些断面处与座环相连的过渡板附近也有一定的弯曲应力,如断面12内外表面环向应力相差约30MPa。其他区域以膜应力为主,膜应力一般小于80MPa。两种方案的环向应力相差不大。
蜗壳打压时,大部分区域的蜗壳钢板等效应力小于80MPa,只在蜗壳鼻端与直管段交界处的局部达到200MPa以上,座环和固定导叶的等效应力最大值为145MPa。全部荷载作用后,大部分区域的蜗壳钢板等效应力小于100MPa,最大值也出现在蜗壳鼻端与直管段交界处,方案1为210MPa,方案2为260MPa,此处应力情况较复杂。在直管段上半圆存在140MPa的等效应力。
座环和固定导叶的等效应力最大值为190MPa。两种方案的应力相差不大。

图2.3-16 断面6钢板环向应力分布图(单位:MPa)

图2.3-17 运行期(含水击压力)蜗壳钢板等效应力(单位:MPa)
2.3.3 小结
通过对保压埋设方式的水轮机组蜗壳流道及外围混凝土结构进行的三维有限元静力分析,得出以下主要结论:
(1)止推环对减小蜗壳绕机组中心的扭转变形作用明显。
(2)蜗壳保压埋设方式的保压浇筑、卸压、重新加压的施工过程,造成各阶段蜗壳变形呈现出一定的不均匀性,以及卸压后蜗壳和混凝土之间的间隙分布的不均匀性。作用全部荷载后,蜗壳钢板传给混凝土的压力一般为0.6~0.7MPa,约占全部水压(1.395MPa)的45%,在底部支墩处传压较大,为0.8~0.9MPa。是否设置止推环对传压影响不大。
(3)外围混凝土2MPa以上的环向拉应力一般出现在直管段的内表面及腰部外侧,最大环向应力位于管腰部的外表面,达到3.59MPa。不设止推环(方案2)与设止推环(方案1)的应力成果接近。
(4)大部分区域的蜗壳钢板等效应力小于100MPa,最大值出现在蜗壳鼻端与直管段交界处,设止推环方案为210MPa,不设止推环方案为260MPa。座环和固定导叶的等效应力最大值为190MPa。
(5)总体而言,混凝土应力和蜗壳钢板应力满足设计要求(直管段局部混凝土拉应力较大处应加强配筋),从静力分析结果来看,70.00m水头的保压埋设方案是可行的。