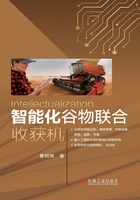
1.5 新型玉米割台
1.割台螺旋推运器
割台螺旋推运器由螺旋和伸缩扒指两部分组成。螺旋将割下的谷物推向伸缩扒指,扒指将谷物流转过90°纵向送入倾斜输送器,由输送链耙将谷物喂入滚筒,如图1-10所示为割台螺旋推运器。

图1-10 割台螺旋推运器
1—主动链轮 2—左调节杆 3—螺旋筒 4—螺旋叶片 5—附加叶片 6—伸缩扒指
7—检视盖 8—右调节杆 9—扒指调节手柄
割台螺旋的主要参数有内径、外径、螺距和转速等。
内径的大小应使其周长略大于割下的谷物茎秆长度,以免被茎秆缠绕。现有机器上多采用直径300mm。
螺旋叶片的高度应该能够容纳割下的谷物,通常情况下采用的叶片高度为100mm,因而螺旋外径多为500mm。
为了保证螺旋对谷物的输送和提高输送的均匀性,螺距值S一般都在600mm以下,多数联合收获机上取460mm。也可用经验公式S=(0.8~1)D来计算,式中D为螺旋外径。
为了保证谷物的及时输送,需要一定的螺旋转速。由于谷物只是占有螺旋叶片空间的一小部分,一般在150~200r/min的范围内。
2.伸缩扒指
伸缩扒指安装在螺旋筒内,由若干个扒指(一般为12~16个)并排铰接在一根固定的曲轴上。工作时,要求扒指转到前下方时,具有较大的伸出长度,以便向后扒送谷物。当扒指转到后方时,应缩回螺旋筒内,以免回草,造成损失。扒指外端与割台底板的间隙应保持在10mm左右。
3.割台的升降和仿形装置
联合收获机作业时,要随时调节割茬高度,要经常进行运输状态和工作状态的相互转换。所以,割台必须能很方便地升降。现代联合收获机都采用液压升降装置,操作灵敏省力,一般要求在3s内完成提升或下降动作。为避免割台强制下降造成的损坏和适应地形的需要,割台升降液压缸均采用单作用式液压缸。因此,割台下降时是靠自重将油液从液压缸压回贮油箱实现的。当油泵停止工作时,只要把分配阀的回油路接通,割台就能自动降落。这一点在使用安全上十分重要,需要将支撑支好,以免割台突然下降造成事故。
为了提高联合收获机的生产率,保证低割和便于操纵,现代联合收获机都采用仿形割台,即在割台下方安装仿形装置,使割台随地形起伏变化,以保持一定高度的割茬。目前,生产上使用的割台仿形装置有机械式、气液式和电液式三种。
1.5.1 割台整体结构
新型谷物收获机割台主要由割台支撑架、折叠机构、9组摘穗辊组合、导轨、滑块、搅龙、导轨支撑架、液压缸和护板组成。导轨安置在导轨支撑架上,9组摘穗辊组合安置在导轨上,每两组摘穗辊组合之间安装一个液压缸,割台支撑架分为三部分,两两之间通过折叠机构连接,折叠机构通过液压缸和中间割台支撑架连接,搅龙分为三段,每一段对应一部分割台支撑架。导轨支撑架分为左、中和右三部分,平行放置但不共线,左右两端分别分布有两组摘穗辊组合,中间分布有5组摘穗辊组合,最左端的摘穗辊组合连接到左端导轨支撑架的最左端,滑动的时候可带动左端的导轨支撑架一起滑动,使左端导轨支撑架可以收到中间部分的内侧,右端的导轨支撑架亦是如此,均可收到中间部分的内侧,具体结构如图1-11所示。割台设置有一组摘穗辊组偏置液压缸,9组摘穗辊可以在此液压缸的带动下同时移向割台一侧。
每组摘穗辊由一个液压马达提供动力,同时搅龙的动力也由液压马达提供,谷物割台被设计成为可折叠结构,此结构的设计充分满足了在割台折叠的过程中,谷物割台中各部分互不干涉。

图1-11 割台整体结构

图1-12 割台折叠前的结构
由于9行割台的宽度较大,将割台设计为可折叠形式,割台全部展开的总宽度为4550mm,左右两边的折叠部分的宽度为860mm,折叠功能通过两个液压缸的伸缩来实现,折叠结构的设计简单巧妙,成本低,方便实用,并且可以在割台折叠过程中避免出现死点位置,使整个过程更加平稳,折叠前、后的效果如图1-12和图1-13所示。搅龙的转动由位于割台中间部分的马达通过链轮带动调节,搅龙由于折叠的需要也做了分段的结构设计,并设计了合理的对接结构,在两边的割台都处于折叠状态的时候,中间段的割台也可以进行收割工作。
每组摘穗辊组合包括两个摘穗辊、摘穗辊护板和摘穗辊齿轮箱,摘穗辊组合如图1-14所示,图1-14a为目前已加工组装完成的摘穗辊组合实物图。每个摘穗辊组合下面连接4个滑块,放置于割台支撑架所铺设的导轨上,滑块和导轨选择了CSK公司的LMG30H型号,导轨宽度为28mm,滑块宽度为60mm,每组摘穗辊组合的重力大约为800N,平均分配到4个滑块上,每个滑块承受的重力为200N,远小于滑块的最大承重50kN,充分满足了滑块的受力要求。滑块连接导轨均置于导轨支撑架上,9组摘穗辊组合在导轨支撑架上的装配实物如图1-15所示。

图1-13 割台折叠后的效果图

图1-14 摘穗辊组合
a)摘穗辊组合实物图 b)摘穗辊组合三维图
传统的割台传动方式已经无法运用于本设计中,目前市面上的割台传动方式一般都是从割台一侧开始传递给所有的齿轮箱,每个齿轮箱再带动相对应的摘穗辊转动,在这里由于摘穗辊组合是左右可以调节间距的,因此需要更改传统的传动方式,改为每一个辊子组安装一个提供摘穗辊转动和拨禾器转动的马达,马达连接一链轮,动力通过链轮传递给齿轮箱,齿轮箱同时带动两个辊子向内侧转动。

图1-15 摘穗辊组合的装配实物
与传统的谷物割台的设计不同,本设计将割台上的9组摘穗辊模块化,做成了9组摘穗辊组合,每两个组合之间连接一个液压缸使得摘穗辊两两之间可以在液压缸行程范围内左右移动。而后将摘穗辊组合全部直线排开安置在工字形导轨上,导轨下端铺设在导轨支撑架上。在收获机到达工作地块后,将谷物收获机停在收获区一侧,此时割台上安置的摄像头开始采集田间谷物植株的照片,采集到的照片在计算机上进行图像预处理,并进行谷物植株位置的判定。计算机通过处理计算出田间谷物的种植株距后,将得到的最终距离值传递给PLC(可编程逻辑控制器),PLC控制器通过控制割台液压阀的开合来控制割台进行折叠动作、调节行距动作和整体偏移动作。调节好行距以后,便可以开启马达,末端液压马达通过变速器带动摘穗辊和拨禾器工作,起动收获机开始进行收获工作。
1.5.2 割台关键结构
1.摘穗辊支撑板和搅龙的对接结构设计
摘穗辊组合支撑板的作用是支撑9组摘穗辊组合并方便摘穗辊组合和导轨的连接。为了有更高的强度和稳定性,该支撑板左侧的上板面连接一对滑块,右侧的下板面连接一对滑块,这样可以使滑块始终承受摘穗辊组合带来的压力作用,而不会受到向上的拉力,充分地保证了滑块的寿命。摘穗辊支撑板实物如图1-16所示。该支撑板虽然设计简单,但是对于割台行距可调起到了很重要的作用。

图1-16 摘穗辊支撑板实物图
在折叠过程中,搅龙也随着割台的折叠而做了断开的设计,它通过一个特殊的对接结构来实现,具体结构如图1-17所示,保证了在割台全部展开的时候搅龙可以正常工作,同时又方便折叠。搅龙的直径为121mm,厚度为5mm,使用了轴承座来支撑中间段的搅龙,左右各使用两个轴承座来支撑,稳定性强。这个特殊的对接结构在对接母头部分做了内置的弹簧芯,保证了搅龙无论旋转到任何角度进行对接时都不会产生刚性碰撞,对接结构的公头部分做成锥形,充分保证搅龙的左右两侧和中间部分可以顺利对接。

图1-17 搅龙对接结构
a)对接结构公头 b)对接结构母头 c)对接效果
2.抽拉式导轨支撑架的设计
割台的导轨支撑架采用的是一种抽拉结构,如果割台的中间段和两边段都简单地铺设导轨,由于割台需要折叠,必定存在导轨接缝,接缝的对接精度要求非常高,不然会阻碍滑块在导轨接缝处的自由滑动。但是由于谷物收获机的使用环境及农机精度不高的局限性,精度无法保证,这样就会存在滑块无法正常滑动的问题,而这种特殊的抽拉式导轨支撑架就可以很好地解决这个问题。
抽拉式导轨支撑架被设计为三段,其中左右两段可以被收进中间段内,中间段是固定在割台支撑架上不动的,左右两段可以实现抽拉。摘穗辊在导轨架上的分布是对称的,其中两组摘穗辊分布于左端的导轨支撑架上,右端也分布有两组摘穗辊,中间段导轨支撑架分布有5组摘穗辊。最左端和最右端的摘穗辊组合分别被焊接在可以活动的两个导轨支撑架上,在滑动的时候可以带动导轨支撑架一起活动,如图1-18所示为导轨支撑架。

图1-18 导轨支撑架
a)割台导轨支撑架的侧面 b)抽拉式导轨支撑架的局部 c)导轨支撑架和摘穗辊支撑板的连接图
3.摘穗装置的分析和计算
摘穗装置采用的设计沿用了传统的两对反向且均向内转动的摘穗辊。每个摘穗辊的结构均分为两段,包括锥体部分和一小段圆柱体部分。其中锥体部分的锥体上带有螺旋的凸起,其作用主要是在收割谷物的时候将谷物秸秆向摘穗辊内部牵引,摘除谷物的工作主要是在中段进行。摘穗辊工作区位于圆柱体部分,它的表面是凸起的棱,也叫挤压板。当茎秆由前段被输送进入工作段后,在两个摘穗辊同向转动时,谷物被摘落。在这个过程中,摘穗辊有很多重要的参数需要科学合理地设计,比如若摘穗辊倾角过大则可能会在收获时漏掉谷物果实;若一组中的两个摘穗辊间距过小,容易导致秸秆堵塞。本节针对割台在工作过程中容易出现的问题,将经验数据和理论相结合,确定合理的摘穗装置参数。
(1)摘穗辊倾角的确定 根据经验和研究得知一组摘穗辊组合中的两摘穗辊应保持平行,最好保持有一定的高度差,这里将差值定为35mm。摘穗辊轴线与水平面之间的夹角为30°~40°。根据实际经验积累得知,当这个夹角越小时,越有利于摘穗。本设计中最后确定摘穗辊轴线和水平面之间的夹角为30°。
(2)摘穗辊锥形引导头顶角的确定 摘穗辊前端有一小段锥体的部分,锥体上分布有凸起的螺旋线,这部分的作用主要是用来引导谷物秸秆进入两个摘穗辊中间。经过理论分析和经验分析,最终将顶角确定为40°,如图1-19所示。

图1-19 摘穗辊锥形引导头顶角
(3)摘穗辊的径向尺寸 摘穗辊的径向尺寸的确定,主要是依据工作条件下能否顺利地将谷物从谷物秆上挤落,则

式中,dg为与谷物果实相连的侧秆直径;dj为谷物秆的直径;δ为同一组摘穗辊组合中两摘穗辊之间的间隙;μg和μj分别为一对摘穗辊对谷物果实和谷物秆的抓取系数,通过查阅手册得知μg≈μj=0.8~1.1,由此可知:(3~4.5)(dg-δ)≥D≥(3~4.5)(dj-δ),得到100≥D≥72,根据经验得知,摘穗辊直径太大容易降低收获效率,本设计中取直径大小为75mm。
(4)摘穗部分轴向尺寸的确定 摘穗辊的轴向尺寸一般是根据谷物的长势来确定的,需要提前统计并查阅一棵谷物秆最高处的果实和最低处的果实之间的距离。设计的最终目的是保证在正常工作时,可以将最低的谷物果实和最高的谷物果实都顺利摘下来,摘穗辊轴向尺寸的确定如下
Lmin=Lgsinβ
式中,β为摘穗辊轴线和水平面之间的夹角;Lg为最高的果实和最低的果实之间的距离。根据经验得知:Lg=600~1000mm,本设计取Lg为1000mm,得Lmin为500mm。最终通过理论分析并结合实际经验得到工作部分的长度L为600mm。由于锥形引导头顶角为40°,得到锥形引导头的长度为≈137mm,两摘穗辊的高度差为35mm,摘穗辊轴线与水平面之间的夹角为30°,两摘穗辊的长度差为70mm,则最终定一组摘穗辊长度为737mm和807mm。
(5)摘穗辊转速的确定 摘穗辊线速度应保持在合理的范围内,如果线速度过低,谷物秆和摘穗辊之间容易发生相对的滑动;如果线速度过高,会降低收获的效率。通常我们取顶圆的线速度在3.4~3.8m/s,摘穗辊线速度v取3.5m/s,则

(6)材料的选择 材料为HT200灰铸铁。