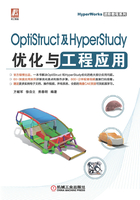
第4章 尺寸优化
4.1 尺寸优化技术简介
4.1.1 尺寸优化基本概念
提到尺寸优化(size optimization),很多人会想到以壳单元的厚度作为设计变量,这大大低估了尺寸优化的作用,实际上尺寸优化更应该叫作参数优化。在OptiStruct模型定义中的某些数字字段,比如壳单元的厚度、梁截面的面积和惯性矩、弹簧单元的刚度、质量点的质量、载荷的大小等,都可以作为设计变量。往往在确定这些参数时,已经进入产品设计的中后期,故尺寸优化多用于详细设计阶段的方案改进。
为了增加尺寸优化的灵活性,在OptiStruct中并不是直接选择某一数值作为设计变量,而是首先定义设计变量,然后在设计变量和属性数值之间创建一个函数关系,这个关系叫作设计变量-属性关系(DVPREL1)。最简单的就是线性关系,其表达式为

式中,p表示属性中要优化的字段;C0 为常数;di为设计变量;Ci表示每个设计变量前的线性系数。
式(4-1)中,如果要优化壳单元属性中的厚度T,只需一个设计变量d1 ,并且设置C0 =0和C1 =1,则上式退化为最简单的关系,即

如果线性关系不能满足要求,则可以借助方程(DEQANT),方程中可以引用包括三角函数在内的常用数学函数,从而定义更加复杂的设计变量与属性数值之间的关系。比如在白车身截面设计中,将白车身部分结构简化为梁单元进行优化。但1D梁单元只能以截面面积、惯性矩、扭转常数为优化对象,而真实截面形状复杂,不能直接以截面的厚度、宽高尺寸作为设计变量。解决方案是以截面的厚度、宽高尺寸为设计变量,然后建立设计变量与梁单元属性中的面积、惯性矩、扭转常数之间的函数关系,把这一关系通过方程的形式引入OptiStruct中,从而达到用尺寸优化直接优化真实截面的目的。
OptiStruct进行尺寸优化的一般步骤如下。
1)准备好可正常计算的分析模型。
2)定义设计变量(DESVAR),并指定设计变量的初始值、上限和下限。
3)定义设计变量与属性数值间的关联关系(DVPREL1)。
4)定义响应(DRESP1/DRESP2/DRESP3)。
5)定义设计约束(DCONSTR)。
6)定义优化目标(DOBJ)。
下面通过一个车架尺寸优化的例子来展示基本流程。
4.1.2 实例:扭转工况下的车架厚度优化
本例展示了在一个车架模型上进行基本尺寸优化的过程。车架两侧边梁后端固定,前端左右支座中心点在Y向分别受到大小相等(1500N)、方向相反的作用力。假设钣金厚度可以在初始值上下浮动20%,要求设计出最优的钣金件厚度,在保证加载点Y向变形小于6mm和结构应力小于350MPa的情况下,使用的材料最少。车架模型如图4-1所示。模型文件中,设计约束、载荷、材料属性和载荷工况(载荷步)已经定义。

图4-1 车架模型
优化三要素
优化目标:结构质量最小化。
设计约束:左侧加载点Y向变形小于6mm;右侧加载点Y向变形大于-6mm(注意右侧加载点Y向变形为负);结构应力小于350MPa。
设计变量:前后横梁和左右边梁的厚度,共4个,每个变量的变化范围为初始值± 20%。

操作视频
操作步骤
Step 01 启动HyperMesh,设置User Profile为OptiStruct,打开模型文件CH4_frame_start.hm。进入Analysis>optimization>size>desvar子面板。
Step 02 创建设计变量。在desvar中输入设计变量名称d_left,initial value中输入变量初始值1.5,lower bound中输入变量下限1.2,upper bound中输入变量上限1.8。单击create按钮,完成创建,如图4-2所示。

图4-2 设计变量
再用同样的步骤分别创建设计变量d_right、d_front、d_rear,三个变量的初始值、上限和下限见表4-1。
表4-1 变量设置

Step 03 定义设计变量与厚度属性的关联关系。进入generic relationship子面板。在name中输入关系名dr_left。单击prop按钮,选择left_beam属性,下方按钮将会自动切换为Thickness T。单击designvars按钮,选择设计变量d_left。单击create按钮完成创建。这样就在设计变量d_left和left_beam的厚度之间建立了一个数学关系,即T=d_left,如图4-3所示。重复上述步骤,分别创建设计变量d_right、d_front、d_rear与三个壳单元属性right_beam、front、rear之间的关联关系dr_right、dr_front和dr_rear。

图4-3 创建变量关系
Step 04 创建设计响应。
① 创建左侧加载点的Y向位移响应disp_left。进入Analysis>optimization>responses面板。在response中输入响应名disp_left,单击response type下方的小三角,从弹出的列表中选择响应类型static displacement。单击nodes按钮,选择左侧加载集中力的节点(位于Z轴负向)。选择位移分量为dof2,类型选择该节点的Y向位移分量。单击create按钮,如图4-4所示。

图4-4 位移响应
② 重复以上步骤,选择右侧加载点,创建右侧加载点的Y向位移响应disp_right。
③ 创建应力响应stress。在response中输入响应名stress。单击response type下方的小三角,从弹出的列表中选择响应类型static stress。单击右侧的props按钮,在弹出的列表中选择下面4个属性,单击select按钮,如图4-5所示。von mises(应力类型)默认为z1,单击前方小三角切换为both surfaces,表示壳单元上下表面的应力值都考虑在内。单击create按钮,即创建4个component中所有壳单元上下表面的应力响应,如图4-6所示。

图4-5 属性选择

图4-6 应力类型选择
④ 创建质量响应mass。在response中输入响应名mass。单击response type下方的小三角,从弹出的列表中选择响应类型mass。右侧按钮保持为total不变,表示选择整个模型的质量。单击create按钮,即创建模型质量响应mass,如图4-7所示。

图4-7 质量响应
Step 05 定义设计约束。
① 创建左侧加载点的Y向位移约束dc_left。进入Analysis>optimization>dconstraints面板。在constraint中输入约束名dc_left。单击response按钮,从弹出的响应列表中选择disp_left,下方将会出现loadsteps按钮。单击loadsteps按钮,在弹出的界面中勾选工况torsion,单击select按钮。勾选lower bound复选框,在后面的文本框中输入-6。单击create按钮,即定义左侧加载点的Y向位移大于-6的约束,如图4-8所示。

图4-8 位移约束
② 重复上述步骤,创建右侧加载点Y向位移小于6mm的约束dc_right。注意约束名为dc_right,响应选择disp_right,定义上限upper bound=6。
③ 创建应力约束。在constraint中输入约束名dc_stress。单击response按钮,从弹出的响应列表中选择stress,下方将会出现loadsteps按钮。单击loadsteps按钮,在弹出的界面中勾选工况torsion,单击select按钮。勾选upper bound复选框,在右方的文本框中输入350。单击create按钮,即定义壳单元应力小于350MPa的约束,如图4-9所示。

图4-9 应力约束
Step 06 定义优化目标。在Analysis>optimization>objective面板左侧选择min,response选择mass。单击create按钮,最小化质量的优化目标定义完成,如图4-10所示。

图4-10 优化目标
Step 07 提交计算。
① 在File下拉菜单中选择Save As命令,弹出Save file对话框,选择保存数据的路径,并输入文件名CH4_frame_opt_done.hm,单击Save按钮。
② 在Analysis面板中选择OptiStruct面板。在input file文本框内已经有默认的.fem文件保存路径,如果希望更改,单击save as按钮后修改即可。在options文本框中输入计算控制选项,如-out,将会把.out文件的信息直接显示出来。单击OptiStruct按钮,开始计算并弹出HyperWorks Solver View对话框。

图4-11 HyperWorks Solver View对话框
③ 单击Results按钮,将会打开HyperView并自动载入计算结果。也可手动从开始菜单打开HyperView,选择结果文件CH4_frame_opt_done_des.h3d进行载入。
Step 08 查看优化结果。
① 单击云图按钮,进入云图面板。单击动画工具条中的最后一步按钮
,将结果切换到最后一个迭代步,单击Apply按钮,即可画出优化后各区域的厚度云图如图4-12所示。

图4-12 车架尺寸优化结果
② 单击按钮进入测量面板,如图4-13所示,单击Add按钮,选择结果为Elemental Con-tour,单击Elements按钮,然后在图形窗口中分别在4根梁上选择一个单元,即可显示出优化后各component的厚度,如图4-14所示。

图4-13 测量面板

图4-14 测量优化后的车架尺寸
拓展:思考以下问题。
1)实际应用中由于成本或工艺的限制,板厚的选择是有限的。假设板厚只能在0.8~2.5之间,且只能以0.1mm为最小变化单位,如何解决?
2)如果左右边梁的厚度必须保持一致,该如何解决?如果制造工艺要求前横梁厚度比左右边梁厚度大0.5mm,可以设置吗?
3)打开计算的.out文件观察一下,优化计算收敛了吗?是达到什么要求以后收敛的?