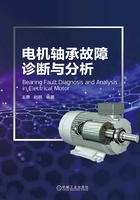
第一节 基于电机轴承设计参数的检查与分析方法
对轴承本身的运行状态的检查在电机轴承使用的全生命周期中起着至关重要的作用。对轴承出现故障表现的电机进行检查,首先要确定检查哪些因素,然后将轴承的表现和状态与这些因素进行联系,找到现象的相关证据,从而确定故障原因和纠正方法。这些检查方法是对电机轴承应用技术的应用,是建立电机运行状态参数与实际应用情况之间逻辑关系的过程。事实上,电机轴承上述的这些检查主要就是针对电机轴承的设计参数展开的。
这个检查过程也主要沿着电机轴承生命周期的进程进行,从工况、设计、制造、运输、使用等诸多方面进行检查和验证。本节仅仅就电机设计参数检查的方法本身以及检查的对象进行介绍,涉及的具体技术内容将在第四章中详细阐述。
一、电机工作工况的检查
电机轴承系统的设计是在电机结构设计阶段就完成的工作。在进行结构设计的时候电机工程师要明确设计要求、边界条件。对于轴承而言就是要明确如下一些因素:
· 电机的安装方式;
· 电机轴承的受力情况;
· 环境温度;
· 电机的负荷状态;
· 电机的工作制;
· 其他工况环境因素。
当电机轴承出现故障的时候,进行故障诊断的第一步就是了解电机周围的工作条件,以确认是否与设计初衷相符合。
首先,如果电机周围的工作条件与设计时给出的电机工作条件一致。此时我们需要检查电机设计人员所选择的轴承是否可以满足这些工作条件,是否存在未考虑到的因素。此时的故障原因就会指向设计结构本身。
第二,当电机实际工作条件与设计给定不符的时候。通常这样的故障诊断需要了解工况条件与设计给定不符的原因。如果是设计时被漏掉,就需要重新考虑这个漏掉的因素;如果是实际工况出现的不可避免的偏差,就需要考虑进行一些弥补性工作。
上面两种情况,究其本质都是首先要检查电机实际的工作条件与设计意图指向的给定工作条件之间是否存在差异,以及存在差异的原因。这是电机轴承故障诊断的第一步,也是十分重要的一步。电机设计工程师只能根据设计给定的条件进行设计计算和校核,当实际工况偏离给定工况时,原来的设计就不一定适用。此时的表现就是电机故障。对应于轴承就是轴承故障。而事实上这并非轴承出了问题,而是这样的轴承以及轴承结构设计不能满足新的工作条件。此时如果不对周围环境进行研究,盲目追究轴承本身质量问题,是没有任何意义的。
典型案例1. 卧式电机被立式安装后轴承的发热和噪声
某电机厂生产的卧式电机被客户立式安装。对于一些电机而言,这样的安装使用会导致轴承在应用的时候出现发热现象。事实上,当对于卧式电机的设计,所有的电机转子重力等都是轴承的径向负荷,而当电机处于立式安装的时候,所有的转子重力都成为固定端轴承的轴向力(参照本书第四章第三节相关内容)。对于一些小型电机,由于轴承本身承载能力存在余量,此时问题不大。但是对于稍大一些的电机,这个轴向力很有可能严重影响轴承寿命。这种情况下表现出故障的电机往往是固定端轴承发热,非固定端轴承出现噪声。有时候两种状况同时发生,有时候出现两者之一。此时既不是电机轴承系统设计本身的问题,也不是轴承质量问题,而是实际工况与设计给定工况的不符。出现这种情况必须更改电机轴承系统设计以适应实际工况。对于小型电机,即便此时轴承没有故障表现,但是轴承本身的寿命(尤其是固定端轴承)将比卧式安装的电机短。
典型案例2. 钢厂运输辊电机的轴承噪声
某电机厂为某钢厂生产运输辊驱动电机,其大致结构如图3-1所示。钢厂为电机厂给出的工况条件是运输辊承受比较大的径向负荷,运输辊和电机通过联轴器连接,电机采用卧式安装。此时电机厂的工程师将运输辊的大径向负荷计入了电机轴承需要承受的负荷(电机轴承负荷计算将在第四章第二节中介绍)。因此对这个电机采用了一柱一球结构。前端使用圆柱滚子轴承,后端使用深沟球轴承。最后电机运行的时候驱动端轴承出现比较大的噪声,同时有部分轴承有发热现象。
但是根据下面这个系统进行受力分析不难发现,运输辊上的大径向负荷是被两个运输辊轴承承担的,而在联轴器连接的电机里,电机仅仅承受转子重力和联轴器重力的径向负荷。这个负荷并不大,且驱动端轴承和非驱动端轴承受力差别也不是非常大。完全可以使用两个深沟球轴承的结构。现场使用的圆柱滚子轴承在这样的小负荷下运行,面临着不能达到轴承所需最小负荷的风险。一旦出现这种情况,滚动体在轴承内部就不能形成良好的滚动,从而出现滑动等不良状态,产生噪声以及发热。

图3-1 运输辊系统受力图
从上面分析可以看到,这个电机的设计是按照轴端承受大的径向负荷的要求设计的,实际工况与这个假设并不相符。此处的“轴承噪声”“轴承发热”等故障现象,并非电机或者轴承质量问题,而是工况与设计假设的不符。
二、电机轴承系统设计的检查
在确认了电机实际工况的条件后,电机轴承系统设计的检查工作主要目的是检查电机轴承系统的设计是否合理,并满足工况需求。通常工程技术人员是在电机轴承出现故障现象或者报警时进行这一步检查。事实上,这个检查进行得越早、越彻底,越有利于避免故障的发生。
电机轴承系统的检查主要包括如下几个方面:
第一,轴承选型检查。电机轴承的选型检查包括检查对轴承本体的选择和对轴承后缀的选择。此时需要检查根据设计给出的各项负荷状态的情况选择合适的轴承类型。然后检查原设计是否根据环境温度选择合适热处理等级的轴承本体、保持架类型、合适的密封件,以及根据工作状况选择合适的轴承游隙。同时对于密封轴承还需要根据工况进行密封件选择和润滑脂选择。
第二,所选电机轴承负荷能力的检查。这个检查的主要目的是检查所选择的轴承是否能够满足实际工况负荷。这其中包括轴承实际承受负荷的方向和负荷的大小。比如轴承承受轴向负荷,那么NU和N系列的圆柱滚子轴承就不能被选用。对于轴承承受负荷的大小,除了考虑轴承能承受的最大负荷能力之外还要考虑轴承所需要承受的最小负荷。
第三,电机轴承配置的检查。电机轴承系统轴承配置的检查和工况检查,以及负荷能力检查之间紧密联系,这些工作有时候都是连带一起进行的。电机轴承配置的检查主要是检查电机轴承系统中所选择的轴承的布置方式是否满足工况需求。比如,定位端、浮动端配置是否明确,定位端、浮动端轴承选择,定位方式的选择,预负荷的选择等。
第四,电机轴承、轴承室部位各个尺寸设计的检查。当电机轴承出现故障表现的时候,工程技术人员也需要对电机轴承以及轴承室的各个部分尺寸进行检查。这项检查的工作包含尺寸公差的检查,以及形状位置公差的检查。在设计检查计算环节,尺寸检查的目的不是针对工件本身加工质量的检查,而是图纸中这个尺寸选择是否合理、是否正确。比如公差是否选择正确、预负荷尺寸计算是否正确、O形环相关尺寸选择是否恰当等。
第五,电机轴承的润滑设计检查。对于电机轴承润滑方案设计的检查包含两大方面,一是润滑脂选择是否恰当。考虑电机轴承工作的温度、转速、负荷等情况对电机轴承选择合适的润滑脂是设计中的工作,也是对设计进行检查中的一个重要环节;二是润滑油路设计是否恰当。没有好的油路设计,即便选择正确的润滑,也无法实现良好的润滑性能。
典型案例3. 弹簧预负荷不足导致的电机轴承噪声过大
某电机厂生产的一批电机出现批量性噪声问题。通过噪声诊断判断与轴承预负荷相关,检查与负荷计算(请参考本书第四章相关内容)没有问题。但是现场出现弹簧预负荷没有压紧的情况。电机厂认为是工件加工问题。后来检查所有工件尺寸均符合要求。最后发现工程师在计算弹簧剩余长度(压缩后长度)的时候,并未将轴向尺寸链的累积公差计入,刚好这一批工件都偏向于某一偏差,最终导致弹簧预负荷不足的情况。对症下药,问题得以解决。
这个案例中所有的核查都是基于设计参数和工况参数进行的,同时主要是对电机轴承应用技术的综合运用,在诸多参数中抽丝剥茧找到症结。
典型案例4. 电机油路设计的断头路问题
某电机厂一批电机出现加入补充润滑脂之后轴承温度过高的现象。现场检查发现:端盖如图3-2所示,这个端盖的油路有进油口,但是没有排油口。当加入润滑脂的时候,多余的润滑脂无法排出,轴承内部润滑脂过多从而导致轴承运转过程中出现温度过高的现象。

图3-2 无排油口端盖的不良设计
另外国内一些电机厂为了美观起见,有意缩小排油口直径,导致排油不畅,进而出现补充润滑脂之后的轴承温度过高现象。
电机的结构图纸中也蕴含着很多设计参数,对这些设计参数的检查在这个案例中起到了关键作用。
综上所述,电机轴承轴系统的检查就是为了检查电机在设计阶段可能出现的疏漏。是排除(或者确定)电机轴承故障与设计相关的因素的工作过程。这个过程需要对电机轴承知识、电机结构知识以及实际工况知识的熟练掌握和应用。
三、电机轴承安装工艺的检查
在对电机轴承故障进行诊断和分析的过程中,必须排除或者确定电机轴承的安装工艺等方面因素对轴承造成的影响。这个过程是基于故障轴承的线索对电机轴承的安装工艺进行检查,并非是按照现有的工艺文件对实际安装过程进行检查。这部分检查的内容包括对电机安装工艺合理性以及实际操作行为导致结果的确认。当然,在这部分检查中还包含对相关零部件的质量检查。
电机安装工艺的检查主要包含以下一些方面:
对轴、轴承室的尺寸公差进行检查。一般在进行电机轴承故障诊断与分析的时候,都是在轴承和电机已经完成安装之后,根据故障提示再进行检查。此时一般轴承已经安装到轴上面,轴的尺寸已经没法检查了。有时候对怀疑有故障的轴承需要进行拆卸,之后可以对轴的尺寸进行一些检查。需要明确的是,此时轴已经经过安装,因此尺寸会发生一些变化,对测量尺寸结果的评估需要考虑这个变化。从这里可以看到,在安装前轴尺寸的测量和记录是十分有必要的,因为一旦出现后续故障需要进行分析,这些记录就可以拿出来作为一些判断的依据。
另一方面,对疑似故障的轴承的轴承室进行测量是有必要的。一般的卧式内转式电机,轴承室的配合为过渡配合,因此可以在最小损伤的情况下进行拆卸然后测量其尺寸。
对轴与轴承、轴承与轴承室的配合尺寸进行检查:根据前面对轴或者轴承室测量的结果。判断轴承与其安装部件之间的配合情况。当然实际故障诊断与分析的过程中,我们需要考虑检查设计本身是否有问题。因此第一步是检查图纸上这些部分的配合选择是不是正确。然后检查实际工件,判断其尺寸是否存在与图纸设计不符。由此可以判断是设计时配合选择不当,还是工件不合格带来的问题。
对轴承室的形状位置公差进行检查:一般的电机厂对轴,以及轴承室的尺寸公差都有一定的质量控制。但是对于这些工件的形状位置公差的控制就不如尺寸公差控制那么严谨。事实上形状位置公差与电机轴承运行表现之间的联系十分紧密,是很多电机轴承故障的根源。本书第四章将介绍现场实用尺寸公差简易测量方法。
对安装过程的检查:电机轴承的安装根据不同的轴承形式、大小有不同的方法。确保使用正确的方法是避免在安装过程中对轴承造成伤害的关键。在安装过程中如果对轴承造成一定的伤害,轴承往往在后续运行中会表现为振动噪声超标,或者发热。这些伤害如果严重的话,轴承在装机之后的测试中就可以被察觉。但是如果这些伤害比较轻微,就会成为轴承运行的潜在风险。很多投入使用一段时间的轴承出现故障,当拆开轴承的时候就会发现一些与安装处置不当相关的失效形貌。这时候往往会对疑似故障的轴承进行失效分析,根据轴承表面形貌的特征,推断可能的轴承安装处置不当,此时除了更换轴承已经没有别的补救方法。而这种初期受到轻微伤害的轴承在出厂时,如果不使用专门的测试设备,有时候微弱的异常信号会被忽略。不论安装过程对轴承造成的伤害严重与否,判断安装布置是否恰当的前提是了解正确的电机轴承安装布置方法,具体内容可以参照本书第四章第六节相关内容。
对润滑脂填装的检查:电机轴承故障诊断与分析时,工程技术人员在对设计的检查中应该已经检查了润滑脂的选择问题、油路设计问题等。对轴承安装工艺的检查工作中,主要是检查是否将前述问题得以逐一落实。比如,润滑脂添加的量是否正确,添加位置是否正确,添加方法是否正确等因素。
对轴承预负荷实施部分的检查:很多轴承都会使用弹簧对轴承施加一定的预负荷。通常在电机轴承中应用的弹簧包括柱弹簧和波形弹簧等。不论是柱弹簧还是波形弹簧,都要保证在安装使用之后有正确的压缩量。弹簧变形量过大或者过小都会导致轴承预负荷异常,从而导致电机轴承运行的故障表现。
对轴承质量进行检查。虽然轴承是标准件,其质量相对稳定,但是对电机轴承进行故障诊断与分析的过程中,也不排除对轴承质量的检查。对轴承的检查通常就是对轴承各个零部件的尺寸等进行测量,对密封件进行检查。有的厂可能还配备轴承振动测试仪,这个测试仪可以检查轴承内部的一些质量情况。
四、电机储运、使用、维护状态和工况的检查
电机检验合格出厂之后,被运输到使用单位,在投入使用过程中对出现故障的电机轴承进行诊断和分析就需要检查电机的储运过程、使用过程,以及维护过程的诸多环节。
首先,电机的储存和运输过程的检查。很多电机厂会出现一些电机在出厂时候各项检测均为合格,但是运输到客户投入使用之前就发现轴承振动或者噪声超标。在两次检查之间,电机和轴承唯一经历的就是运输过程。因此就需要对这一个过程进行检查,看是否有对轴承造成伤害的不当运输包装方式。这一部分的详细表征、诊断与处置请看到第九章相应内容。
第二,检查电机储存是否得当。当电机长期放置在仓库里储藏的时候,电机轴承不转,电机轴承负荷区固定,受重力影响润滑脂重新分布。这些都会对轴承造成不利影响。本书第十章将展开细节介绍。
第三,电机轴承使用工况的检查。合格的电机投入使用,会经历电机的安装过程。在这个过程中,电机的安装情况是否正确,是否有对中不良,地脚是否安装坚固稳妥等都是这个环节需要做的检查。
第四,电机轴承运行过程中的维护工作检查。一般电机轴承投入使用,其中维护工作量最大的就是补充润滑脂。电机投入运行的补充润滑脂工作需要按照正确的补充润滑脂方法,将正确的润滑脂以正确的补充润滑量添加到轴承的正确位置。这一系列动作都需要有明确可靠的流程和方法。具体方法请参考本书第四章。
五、电机轴承状态检查的顺序与优先级
在进行电机轴承故障诊断与分析的时候,我们需要对前面所述的所有电机轴承相关因素进行检查。在实际工况中,当电机轴承出现故障的时候,工程师往往不可能对所有环节逐一不漏地进行检查。很多时候都会根据故障提示的现象,在庞大的检查网络中寻找最有可能的路径,大胆求证、小心推断,用最高的效率找到问题点的所在。但是能够这样做的前提是电机工程师在自己的知识体系里有一个完整的知识网络,面对轴承故障的时候是在这个知识网络里寻求答案的过程。所谓有经验的工程师就是可以在这个庞大的网络的基础上做出“稳、准、狠”的判断。
我们试图将前面的检查网络绘制成思维脑图,如图3-3所示。

图3-3 电机轴承状态检查