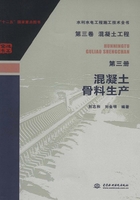
3.3 爆破作业
(1)钻爆作业的一般要求。人工骨料料场的钻爆作业是一项技术要求高,成本消耗大,对人工砂石料生产起制约作用的重要工作。人工骨料料场的钻爆作业与一般开挖工程的钻爆作业的主要区别在于对爆岩块石的粒径控制。
在人工骨料料场的钻爆作业中,爆岩块石的粒径控制尤其关键。块石粒径小,超径块少,装挖运输效率高,破碎加工容易,二次解炮费用少,但钻爆作业的成本高。块石粒径大,超径块多,虽然钻爆作业费用少,但二次解炮费用高,装挖运输效率低,破碎加工也困难。
人工骨料料场一般采用最大块石粒径的指标来控制其钻爆作业的设计。最大块石粒径,就是可以允许直接进入破碎加工工序的块石的最大边尺寸,它一般受挖掘设备的斗容,粗碎机的进料口尺寸制约,其计算方法如下。

2)按粗碎机进料口尺寸计算。为保证粗碎机正常工作,其最大边尺寸应小于粗碎机进料口的85%。常用粗碎破碎机允许最大进料粒径见表3-4。
表3-4 常用粗碎破碎机允许最大进料粒径表

(2)爆破器材的选择。
1)常用爆破器材的种类。常用爆破器材按其作用特点和作用范围分为起爆药、猛性炸药和发射药三类,工程爆破中主要使用起爆药和猛性炸药两类爆破器材。
爆破工程中的任何药包,都必须借助于起爆器材,并按照一定的起爆过程来提供足够的起爆能量,才能根据工程需要的先后顺序,准确而可靠地爆破。
不同的起爆方法,采用不同的起爆器材,而起爆方法的发展又与爆破技术的进步密切相关。例如,我国冶金矿山,20世纪50年代初,大都采用火雷管起爆法和导爆索起爆法,主要器材是火雷管、导火索和导爆索等;60年代,随着大爆破、地下深孔爆破、露天台阶深孔爆破、光面爆破、微差爆破和预裂爆破等技术的发展,普遍推广电起爆法,各种类型的电雷管相继出现;70年代末、80年代初,随着新型起爆器材导爆管的出现,非电导爆管起爆系统在全国各大矿山得到推广使用,并相继研制成功了一些相应的器材。目前非电导爆管起爆系统在冶金矿山占据主导地位。
雷管是起爆器材中最重要的一种,根据其内部装药结构的不同,分为有起爆药雷管和无起爆药雷管两大系列。两大系列中,根据点火方式的不同,有火雷管、电雷管和非电雷管等品种;在电雷管和非电雷管中,都有秒延期、毫秒延期系列产品;毫秒雷管已向高精度、短间隔系列产品发展。国家爆破器材主管部门已淘汰了火雷管和普通电雷管,常用的主要有磁电雷管和非电雷管。
导火索是点燃火雷管的配套材料,它能以较稳定的速度连续传递火焰,引爆火雷管。导火索以粉状或粒状黑火药为芯药,直径为2.2mm左右。导火索的喷火强度和燃速,是保证火雷管起爆可靠、准确和安全的主要条件。国产普通导火索的燃速为100~125m/s,它是一项重要的质量标准。燃速发生变化的导火索不得使用。导火索在燃烧过程中,不得有断火、透火、外壳燃烧或爆燃等现象发生。每盘导火索长度一般为250m。
导爆索的作用主要是传递爆轰,引爆炸药,其爆速为6500~7000m/s。导爆索本身不易燃烧,相对地讲是不敏感的,需用工业雷管才能引爆。其引爆其他炸药的能力,在一定程度上决定于芯药和每米导爆索的药量。导爆索按包缠物的不同可分为线缠导爆索、塑料皮导爆索和铅皮导爆索;按用途分有普通导爆索、震源导爆索、煤矿导爆索和油田导爆索;按能量分有高能导爆索和低能导爆索。普通导爆索是目前产量最大、应用范围广的一个品种。
导爆管是一种新型传爆器材,具有安全可靠、轻便、经济、不受杂散电流干扰和便于操作等优点。它与击发元件、起爆元件和连接元件等组合成起爆系统。因为,起爆不用电能,故称为非电起爆系统。目前,在我国冶金矿山应用广泛。导爆管是用高压聚乙烯熔挤拉出的空心管子,外径为2.95mm±0.15mm,内径为1.4mm±0.1mm,管的内壁涂有一层很薄且均匀的高能炸药,药量为16~20mg/m。
2)炸药的选择。常用的猛性炸药主要有TNT、乳化炸药、浆状炸药、铵油炸药和铵锑炸药等。
硝酸铵类炸药:硝酸铵本身是一种爆炸材料,在适当条件下可以产生爆炸。硝酸铵本身感度低、具有较强的吸湿性和结块性,其常作为氧化剂与燃烧剂及其他成分组成混合猛性炸药。这类炸药通称硝铵类炸药。硝铵类炸药可分为铵油炸药、铵梯炸药、露天铵梯炸药、铵松蜡炸药、含水炸药等系列。
含水炸药:为了克服硝铵类炸药密度小和易结块的缺点,将水添加到这类炸药混合物中,使体系胶凝,制成密度较高的浆状炸药。这种炸药在有水条件下爆破能获得成功。在浆状炸药的启示下,又陆续研究成功了水胶炸药、乳化炸药、重铵油炸药等含水炸药,从根本上解决了炸药的防水问题。
专用炸药:在一般工业炸药很难完成或在特定的环境和条件下完成爆破时采用,如光爆炸药、煤矿许用炸药等。
(3)梯段爆破。梯段爆破(也称台阶爆破)通常是在一个事先修好的台阶上进行,每个台阶有水平和倾斜两个自由面,爆破作业是在水平面上进行。由于其作业空间不受限制,可以采用大型穿孔、采装和运输设备,其爆破效率较高,是目前工程爆破的主要方法之一。台阶爆破按孔径、孔深的不同,分为深孔台阶爆破和浅孔台阶爆破。通常将钻孔直径大于50mm、钻孔深度大于5m的称为深孔,反之,则称为浅孔。
1)台阶爆破的参数确定。露天深孔爆破参数包括:孔径、孔深、超深、底盘抵抗线、孔距、排距、堵塞长度和单位炸药消耗量等。
①孔径。露天深孔爆破的孔径主要取决于钻机类型、台阶高度和岩石性质。人工骨料料场常用的深孔直径有76~80mm、100mm、150mm、170mm等几种。
②孔深和超深。孔深由台阶高度和超深确定。目前,我国深孔爆破的台阶高度为10~15m。超深是指钻孔超出台阶底盘标高的那一段孔深,其作用是降低装药中心的位置,以便有效克服台阶底部阻力,避免或减少留根底,以形成平整的底部平盘。我国的矿山超深值一般为0.5~3.6m,后排孔的超深值一般比前排小0.5m。
③底盘抵抗线。底盘抵抗线与炮孔直径、炸药威力、岩石可爆性、台阶高度和坡面角等因素有关,一般情况下,底盘抵抗线Wd是台阶高度H的0.6~0.9倍。
④孔距和排距。相邻炮孔之间的距离称为孔距,相邻两排炮孔之间的距离称为排距。确定孔距和排距,通常是以每个炮孔允许装入的炸药量为依据,再每个炮孔所负担的爆破体积,最后得出排距,孔距用式(3-3)计算:

在多排孔微差爆破中,一般炮孔排距为底盘抵抗线的0.9~0.95倍。
⑤堵塞长度。炮孔堵塞长度是指装药后炮孔的剩余部分作为填塞物充填的长度。合理的堵塞长度对改善爆破效果和提高炸药利用率具有重要作用。一般情况下,堵塞长度为钻孔孔径的20~30倍,或为抵抗线的0.7~1.0倍。
⑥每孔装药量。每孔装药量是以炮孔爆破一定体积岩石所需的炸药量计算确定的,即:

多排孔爆破时,第一排炮孔装药量计算见式(3-4)。从第二排起,其装药量应适当加大:

其余符号意义同前。
单位体积炸药消耗量q与岩石的可爆性、炸药特性、自由面条件、起爆方式和块度要求有关,可按表3-5取值。
表3-5 深孔台阶爆破单位炸药消耗量q值

2)装药结构和起爆顺序。装药结构是指炸药在装填时的状态。在露天深孔爆破中,分为连续装药结构、分段装药结构、孔底间隔装药结构和混合装药结构等。
起爆顺序变化可以改变炮孔爆破方向,增大孔距,相应减小起爆抵抗线或排距,增大炮孔密集系数,创造新的自由面,增加爆破后岩石碎块之间的挤压、碰撞几率,实现再次破碎,以改善爆破效果,降低爆破地震效应。同时,可减小毛料大块率,增加经济效益。
深孔台阶爆破微差起爆顺序有多种形式,常见的有矩形布孔排间微差起爆、矩形布孔对角微差起爆、矩形布孔V形微差起爆、矩形布孔横向掏槽起爆、三角形布孔排间微差起爆、三角形布孔对角微差起爆和三角形布孔V形微差起爆等。
(4)预裂爆破和光面爆破。预裂爆破是在主爆区爆破之前,沿开挖边界钻一排密集炮孔,装入小直径药卷,爆破后形成贯穿裂缝。主爆区爆破时预裂缝能在一定范围内减小主爆孔的爆破地震效应,控制其对保留岩体的破坏影响,使之获得平整的开挖壁面。
爆破参数的确定。预裂爆破的主要参数是不耦合系数、炸药品种、线装药密度以及孔径和孔间距等。影响爆破参数选择的主要因素是岩石的物理力学性质和地质构造。
1)炮眼直径。一般应根据工程性质及其对爆破质量的要求和设备等条件进行选择。小直径钻孔对周围岩石破坏范围小,预裂面形状容易控制,易于取得较好的效果,在采石场一般取60~120mm孔径。
2)孔距。孔距越小则预裂带壁面光滑平整效果越好。孔距一般采用孔径的8~12倍,最高可为17倍。
3)预裂孔与缓冲孔的排距。预裂孔与缓冲孔的排距一般取孔距的1.2~1.5倍。
4)孔深和超深。正常情况下,预裂爆破形成的预裂面比孔底要超深0.5~1.0m。如果此超深对基岩的破坏为工程所不允许,则应适当提高孔底高程,或者孔底高程不变,在孔底0.5~1.0m处不装炸药,用柔性材料作垫层,或者充填岩粉。
5)不耦合系数。采用不耦合装药结构主要是降低炸药爆炸的初始压力,使孔壁周围的岩石不受破坏。不耦合系数将随岩石极限抗压强度的增加而下降,一般取2~4。
6)装药结构和堵塞。人工石料场的边坡控制爆破中,预裂孔一般采用间隔装药结构形式,间隔控制在10~30cm范围内;孔口堵塞长度通常取炮孔直径的12~20倍。
(5)超径石的处理。
1)浅孔爆破。超径大块石常用的处理方法是浅孔爆破,一般按2m3/m布孔,孔径32~50mm,爆破单耗在0.06kg/m3之内。此方法简单、快捷,易于操作。
2)充水爆破法。充水爆破也是和浅孔爆破一样需在大块石上钻炮孔,经过防水处理的炸药和长约200~300mm的一段导爆索放入灌水的炮孔中。由于在水中爆炸的冲击波压力约为空气中的200倍。因此,炸药能量的利用率高,药耗低,碎石的飞散少,不影响20~40m以外的其他工作。
3)破石锤。近年来,国内外已广泛采用风动和液压破石锤处理超径大块石,并取得良好效果如三峡水电站、小浪底水电站工程。液压与风动相比,具有轻巧、冲击功大、低噪声(不超过80~84dB)、少污染、安全等优点。
随着液压挖掘机的迅速发展,液压破石锤将具有更大的发展前途。液压破石锤可安装在液压反铲挖掘机的斗臂上,在料场各个梯段的作业面巡回破碎超径大石,清理作业面,以保证挖掘连续作业;也可装在特制的臂架上,布置在粗碎车间的受料仓附近,处理来料中的超径石。根据国外资料,用破石锤破碎1.5~2.0m3的大块石,费用约为钻爆的20%~60%。
(6)爆破安全技术。
1)爆破个别飞散物控制。爆破个别飞散物(旧称爆破飞石)是指爆破时个别或少量脱离爆堆飞得较远的碎石块。爆破飞石往往会造成人员、设施的伤亡或损坏。造成飞石的原因主要是选择爆破参数不合理、单耗过大、过量装药、抵抗线过小、起爆顺序不合理、岩体有薄弱面、填塞长度不够、填塞质量不好等。控制爆破产生飞散物的主要措施有:
爆破设计合理,药室、炮孔位置测量验收严格,是控制飞散物事故的基础;装药前应认真校核各药包的最小抵抗线,如有变化,必须修正装药量,不准超装药量。
避免药包位于岩石软弱夹层,以免从这些薄弱面冲出飞散物;慎重对待断层、软弱带、张开裂隙、成组发育的节理、溶洞、采空区、覆盖层等地质构造,采取间隔堵塞、调整药量、避免过量装药等措施。
保证堵塞质量,不但要保证堵塞长度,而且保证堵塞密实,堵塞物中避免夹杂碎石。
采用低爆速炸药,不耦合装药、挤压爆破和毫秒起爆等,可以起到控制飞散物的作用。多排爆破时要选择合理的延期时间,防止因前排带炮(后冲),造成后排最小抵抗线大小与方向失控。
有特殊要求,需严格控制飞散物时,应对爆破体采取覆盖或防护措施。
2)爆破振动的控制。爆破引起的振动,会造成周围地面及地下建筑物和构筑物的振动,这种现象称为爆破地震效应。达到一定强度的振动会造成建(构)筑物的破坏,从而有必要对地震效应的破坏规律以及确定爆破地震的安全距离进行细致深入研究。
爆破地震和天然地震都是迅速释放能量,以波的形式向外传播的物理过程。但两者也有很大区别,爆破震动震源浅,释放能量小,振动频率高,振动持续时间短,故其影响范围和危害程度均比天然地震小得多,并且爆破地震是人为可控的。
控制爆破震动,可采取下列措施。
严格控制爆破规模,尽量增加分段,降低最大单响药量。
合理设计微差时间间隔和起爆顺序,尽量增加爆破自由面。实践证明,间隔时间大于100ms时降震效果较明显;间隔时间小于100ms时各段爆破产生的地震波还不能显著分开。
合理选择爆破参数和单位炸药耗药量。采用预裂爆破,减弱爆破对保留区岩体的扰动和破坏。在爆破体与保护对象间设置不装药的单排(双排)防震孔,降震率达30%~50%;防震孔孔径可取35~65mm,孔间距不大于25cm。采用预裂爆破比防震孔可减少钻孔量,降震效果更好,但应注意预裂爆破产生的振动效应。
也可采取、挖减振沟等防护措施。
3)爆破安全距离。在露天岩土爆破中,除爆破个别飞散物对设备、建筑安全距离须由设计确定外,个别飞散物对人员的安全允许距离应按照表3-6执行。特别注意的是,沿山坡爆破时,下坡方向的飞石安全允许距离应增大50%。露天爆破人员的安全距离见表3-7。
表3-6 爆破个别飞散物对人员的安全允许距离表

表3-7 露天爆破人员的安全距离表
