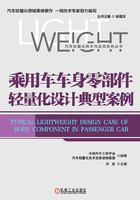
2.1 热冲压技术简介
汽车工业中,在保证安全性的前提下,为了达到减重和环保的目的,车用高强钢和超高强度钢板以其强度高的特点受到广泛关注,已经成为满足汽车减重和保证碰撞安全性的重要材料。随着钢材强度的提高,传统冷冲压方法导致高强钢成形过程中易发生开裂、回弹等情况,成形件的形状与尺寸稳定性较差,不宜生产汽车设计所需要的结构复杂零件。为了解决高强钢钢板难以冷成形的问题,热冲压成形的技术逐渐发展并被汽车工业应用。
早在20世纪80年代初期,萨博汽车公司首先将高强钢热冲压技术应用于萨博9000车型上,生产出第一批热冲压成形汽车零件,使得热冲压成形技术在汽车的应用上迈出了第一步。
2008~2010年,国外大约有110条热冲压生产线,主要分布在美国、德国、日本、以及法国、西班牙、瑞典等国家。中国仅5条生产线,分别是长春BENTLER、上海昆山GESTAMP、上海BENTLER、上海嘉定COSMA及上海宝钢。热冲压生产线大多由瑞典AP&T公司及德国Shuler公司提供,这两家公司几乎垄断了全球所有的热冲压成形生产线市场。随着热冲压成形技术的不断发展,国内热冲压生产线的数量也不断上升。
2006年,华晨汽车与宝钢通力合作,开发了自主品牌首个量产热冲压成形B柱,应用在“中华尊驰”和“中华骏捷”出口车型上,提高了碰撞安全性能。之后,越来越多的车型应用了热冲压B柱。
热冲压成形(Hot Stamping,Press Hardening)是将钢板加热到奥氏体化温度以上,快速移动到模具上,高温坯料在模具内被冲压成形的同时完成淬火的一种工艺。
热冲压零件是采用热冲压工艺制造的零件。通常,热冲压后还需要进行激光切割、抛丸(若是裸板的情况下)等处理。目前,已经有模具热切边、无切边或少切边等新工艺在开发中。
(1)适用于热冲压成形零件的钢板特性
适用于热冲压成形零件的钢板,主要是低碳微合金硼钢体系,其特性如下:
1)常温状态下,材料的微观组织为铁素体/珠光体混合组织,抗拉强度为400~600MPa。
2)热冲压成形中,板材经奥氏体化(900~950℃,保温3~10min)后,流动性能好,塑性变形能力大幅提高。
3)热冲压成形后,材料发生马氏体相变,抗拉强度提升到1500MPa及以上。
4)相对冷冲压成形,热冲压成形的接触条件对板料成形的影响作用显著提升。板料与模具的接触时序和接触状态差异不仅会影响其冷却相变过程,还将引起温度梯度,温度低的区域变形抗力高,而温度相对较高的区域变形抗力低,易引发应变集中,造成局部失效。
5)热冲压零件在高温下成形,零件表面存在氧化,表面质量控制要求高,不易起皱和破裂,基本没有回弹,尺寸稳定性比较好。
(2)热冲压成形技术的原理
首先将高强钢钢板(图2-1状态1)置于850~950℃的加热炉中加热,保温3~10min,使高强钢钢板完全均匀奥氏体化(图2-1状态2);然后送入带有冷却系统的模具中在高温下进行冲压成形,材料在该温度下仅有约200MPa的强度和高于40%的伸长率,成形性能极好,可成形为形状复杂的零件;之后保压、快速冷却淬火,使奥氏体转变成马氏体(图2-1状态3),构件的强度有很大提高,其抗拉强度可达到1500MPa左右,屈服强度可达到1000MPa左右。

图2-1 热冲压成形技术原理
HF—热成形钢
在实际生产过程中,热冲压成形过程通常有两种工艺:直接工艺与间接工艺,如图2-2所示。在图2-2a所示的直接工艺中,将钢板置于加热炉中加热一段时间,而后将其转移到带有冷却系统的模具中,经过冲压成形和模内淬火等工序后制成热冲压工件。这种直接工艺主要用于生产形状简单而且变形程度较小的工件。在图2-2b所示的间接工艺中,首先对钢板进行冷冲压预成形及切边工序处理,再将其放入加热炉中加热,最后经过热冲压及淬火得到高强度的热冲压钢板。间接工艺主要用于生产一些形状比较复杂或拉深深度较大的工件。
随着热冲压成形技术的不断发展,直接成形工艺不断替代间接工艺,目前车身上用热成形零件95%以上都可采用直接成形工艺进行生产。生产线工艺流程为:料片拆垛→双料检测、打标→加热炉上料→料片加热→压力机上料→成形、保压淬火→压力机下料。辅助工艺包括前处理工艺:进料检验和落料/堆垛;后处理工艺:激光切割、抛丸防锈处理、零件检验等。

图2-2 热冲压成形工艺分类
(3)热冲压成形工艺的优点
与传统冷冲压成形工艺相比,热冲压成形工艺有如下诸多优点:
1)成形性好。高温下材料成形性好,可用于成形复杂结构零件。
2)回弹小,零件尺寸精度高。高温下成形没有回弹,消除了回弹对零件形状的影响,可实现高精度成形,这是常规冷冲压成形无法比拟的。
3)需要模具数量少,成本低,周期短。可将冷冲压成形需要多道工序、多套模具才能成形的零件一次成形,还可将几个冷冲压件合成一个件一次成形。
4)得到超高强度的车身零件,从而减小零件厚度,减少车身加强板、加强筋的数量,并提高车身的碰撞性能,实现车身重量的有效减轻。目前,已经研制出1.8~2.0GPa级别零件。
5)所需压力机吨位小。高温下材料变形阻力小,成形力小,热冲压压力机吨位一般在1200t以内,冷冲压成形压力机在2500t以上,因此可以大幅削减设备投资,减少能耗。
(4)热冲压成形有待解决的问题
热冲压成形工艺有诸多优点的同时,也存在一些有待解决的问题:
1)模具复杂。模具设计、加工难度大,制造及调试周期长,模具及其配套工装价格高,维护成本大。
2)工作环境相对较差。非镀层钢板热冲压后会产生氧化皮。
热冲压成形技术克服了传统冷冲压工艺成形困难、回弹严重以及容易开裂等诸多问题,已在欧、美等国汽车企业和国内汽车企业大范围应用。热冲压成形件主要应用于车身结构中对强度要求高的零部件,如图2-3所示。

图2-3 典型的热冲压成形件
从2013~2016年的欧洲白车身会议(ECB)的统计来看,热冲压成形技术的应用比例在提高,热冲压成形零件占车身重量比率情况如表2-1所示。
表2-1 热冲压成形零件占车身重量比率情况

(续)
