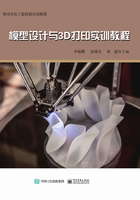
环节二 信息收集
为全面认识3D打印FDM技术,同学们需要掌握相应的知识和能力,其思维导图如图1-1所示。

图1-1 初识3D打印FDM技术思维导图
一、FDM打印原理简介
FDM打印又称为熔融挤出成型,是一种高性能的快速成型工艺。该工艺是继光固化快速成型和叠层实体快速成型工艺后的另一种应用比较广泛的快速成型工艺方法。该工艺方法以美国Stratasys公司开发的FDM制造系统的应用最为广泛。Stratasys公司自1993年开发出第一台FDM1650机型后,先后推出了FDM2000、FDM3000、FDM8000,以及1998年推出了引人注目的FDM Quantum机型,FDM Quantum机型的最大造型体积达到600mm×500mm×600mm。此外,该公司推出的Dimension系列小型FDM三维打印设备得到市场的广泛认可,仅2005年的销量就突破了1000台。国内的清华大学与北京殷华公司也较早地进行了FDM工艺商品化系统的研制工作,并推出熔融挤压制造设备MEM 250等。
FDM工艺原理图如图1-2(a)所示,材料在喷头内被加热熔化,喷头沿零件截面轮廓和填充轨迹运动,同时将熔化的材料挤出,材料迅速固化,并与周围的材料黏结。每一个层片都是在上一层上堆积而成的,上一层对当前层起到定位和支撑的作用。随着高度的增加,层片轮廓的面积和形状都会发生变化,当形状发生较大变化时,上层轮廓就不能给当前层提供充分的定位和支撑作用,这就需要设计一些辅助结构——“支撑”,对后续层提供定位和支撑,以保证成型过程的顺利实现,如图1-2(b)所示。

图1-2 FDM打印原理
FDM打印工艺不用激光热源,使用、维护简单,成本较低。用石蜡成型的零件原型,可以直接用于石蜡铸造。用ABS制造的原型因具有较高强度而在产品设计、测试与评估等方面得到广泛应用。近年来又开发出PC、PC/ABS、PPSF等更高强度的成型材料,使得该工艺有可能直接制造功能性零件。基于FDM打印工艺优点,该工艺发展极为迅速,目前FDM系统在全球已安装快速成型系统中的份额大约为30%。
二、FDM打印的技术特点
1.不采用激光热源,维护简单,成本低
成本是决定成型工艺能否适用于3D打印的一个重要因素。多用于概念设计的3D打印机对原型精度和物理化学特性要求不高,低成本是其能否广泛推广的决定性因素。
2.塑料丝材,清洁,更换容易
与其他使用粉末和液态材料的工艺相比,丝材更加清洁,易于更换、保存,不会在设备中或附近形成粉末或液体污染。
3.后处理简单
仅需几分钟到一刻钟剥离支撑后,原型即可使用。而现在应用较多的SLA、SLS、3DP等工艺均存在清理残余液体和粉末的步骤,并且需要进行后固化处理,需要额外的辅助设备。这些额外的后处理工序有两个缺点:一是容易造成粉末或液体污染;二是增加了几个小时的时间,不能在成型完成后立刻使用。
4.成型速度较快
一般来讲,FDM工艺相对于SLA、SLS、3DP工艺来说,速度是比较慢的。但针对三维打印应用,它也有一定的优势。首先,SLA、SLS、3DP都有层间过程(铺粉/液,挂平),因而它们一次成型多个原型时速度很快,如3DP可以做到1小时成型25mm左右高度的原型。三维打印机成型空间小,一次成型1~2个原型,相对来讲,它们的速度优点就不甚明显了。其次,3D打印机对原型强度要求不高,所以FDM工艺可通过减小原型密实程度的方法提高成型速度。通过试验,具有某些结构特点的模型,最高成型速度已经可以达到60cm3/h。通过软件优化及技术进步,预计可以达到200cm3/h的高速度。
5.材料性能优势
FDM打印所采用的材料中,ABS原型强度可以达到注塑零件的1/3。2019年又发展出PC、PC/ABS、PPSF等材料,强度已经接近或超过普通注塑零件,可在某些特定场合(试用、维修、暂时替换等)下直接使用。虽然直接金属零件成型(近年来许多研究机构和公司都在进行这方面的研究,是当今快速原型领域的一个研究热点)的材料性能更好,但在塑料零件领域,FDM工艺是一种非常适宜的快速制造方式。
三、FDM打印设备及辅助工具
完成FDM 3D打印的硬件设备主要有桌面级3D打印机、计算机,其中计算机配置应能够流畅运行SolidWorks 2018软件,常见的FDM 3D打印机如图1-3所示。除了基本装备,还需要准备表1-1所列的工具或耗材。
表1-1 工具与耗材表


图1-3 FDM 3D打印机
四、FDM打印的成型材料
FDM 3D打印的成型材料一般是热塑性丝状材料,如蜡丝、ABS、PC、PP等,如图1-4所示。
表1-2所示为目前FDM 3D打印使用较多的几种材料,从表中可以看出:不同的材料有着不同的成型温度、不同的收缩率及不同的性能等。除了这些常用的材料,FDM 3D打印使用的材料还有俗称聚纤维的PPSF/PSU、PEI塑料ULTEM9085及水溶性材料,PPSF/PSU是所有热塑性材料中强度最高、耐热性最好、抗腐蚀性最高的材料,呈珀色,热变形温度接近190℃;PEI塑料ULTEM9085强度高、耐高温、抗腐蚀,热变形温度在150℃左右,收缩率仅为0.1%~0.3%,稳定性极好。

图1-4 FDM 3D打印的成型材料
表1-2 FDM 3D打印常用成型材料

五、FDM打印的基本工艺过程
FDM技术加工的每个产品,从最初的造型到加工完成的基本工艺过程如图1-5所示。

图1-5 FDM 3D打印的基本工艺过程
1.成型件的三维建模
三维模型数据是成型件真实信息的虚拟描述,它将作为快速成型系统的输入信息,所以在加工之前要先利用计算机软件建立好成型件的三维模型。三维建模软件主要有SolidWorks、Pro/E、UG等,它们都具有很好的通用性。
2.三维模型的近似处理
由于成型零件通常具有比较复杂的曲面,为了便于后续的数据处理和减小计算量,需要将三维模型存储为STL格式进行近似处理,由于生成STL格式文件方便、快捷,且数据存储方便,目前这种文件格式已经在快速成型制造过程中得到广泛的应用。
3.三维模型数据的切片处理
采用切片软件,对近似处理后的模型进行切片处理,提取出每层的截面信息,生成数据文件,再将数据文件导入FDM打印机中,切片时切片的层厚越小,成型件的质量越高,但加工效率变低;反之则成型质量低,加工效率提高。
4.FDM打印
FDM打印机在数据文件的控制下,打印头按照所获得的每层数据信息逐层扫描,一层一层地堆积,最终完成整个成型件的加工。
5.后处理
打印完成后,取出成型件,对其进行去支撑、打磨、抛光等处理,进一步提高打印的成型质量。
拓展
3D打印的发展与类型
1.3D打印的发展过程
很早以前就有“增长”这种制造方式,3D打印技术的基本原理是基于离散的增长方式成型原型或制品。在历史上,其根源可以追溯到早期地形学工艺领域。其早期工艺发展如下。
1892年,J.E.Blanther在其美国专利中曾建议用叠层的方法来制作地图模型。该方法指出将地形图的轮廓线压印在一系列的蜡片上并沿轮廓线切割蜡片,然后堆叠系列蜡片产生三维地貌图。
1902年,Carlo Baese在他的美国专利(# 774549)中,提出了用光敏聚合物制造塑料件的原理,这是现代第一种快速成型技术——“立体平板印刷术”(Stereo Lithography)的初始设想。
1940年,Perera提出了在硬纸板上切割轮廓线,然后将这些纸板粘成三维地形图的方法。
1964年,E.E.Zang进一步细化了该方法,建议用透明纸板制作地貌图,且每一块均带有详细的地貌形态标记。
1972年,K.Matsubara提出在上述方法中使用光固化材料,将光敏聚合树脂涂覆到耐火颗粒上形成板层,光线有选择地投射或扫射到这个板层,将规定的部分硬化,没有扫描或没有硬化的部分被某种溶剂溶化,用这种方法形成的薄板层随后不断地堆积在一起形成模型。
1976年,P.L.DiMatteo进一步明确提出,这种堆积技术能够用来制造普通机加工设备难以加工的曲面,如螺旋桨、三维凸轮和型腔模具等。在具体实践中,通过铣床加工成型沿高度标识的金属层片,然后粘接成叠层状,采用螺栓和带锥度的销钉进行连接加固,制作成型腔模,如图1-6所示。

图1-6 由DiMatteo制作的型腔模叠层模型
1977年,W.K.Swainson在其美国专利中提出,通过选择性的三维光敏聚合物体激光照射直接制造塑料模型工艺,同时Battelle实验室的R.E.Schwerzel也进行了类似的工作。
1979年,日本东京大学T.Nakagawa教授等开始用薄板技术制造出实用的工具,如落料模、成型模和注射模等。特别值得一提的是,T.Nakagawa教授提出了注射模中复杂冷却通道的制作可以通过这种方式得以实现。
1981年,H.Kodama首先提出了一套功能感光聚合物快速成型系统,应用了3种不同的方法制作叠层。
2.常见的3D打印工艺
根据所使用的材料和建造技术的不同,目前应用比较广泛的方法有如下4种。
(1)光固化成型法:其英文名称为Stereo Lithography Apparatus,即采用光敏树脂材料通过激光照射逐层固化而成型,可缩写为SLA。
(2)叠层实体制造法:其英文名称为Laminated Object Manufacturing,即采用纸材等薄层材料通过逐层粘接和激光切割而成型,可缩写为LOM。
(3)选择性激光烧结法:其英文名称为Selective Laser Sintering,即采用粉状材料通过激光选择性烧结逐层固化而成型,可缩写为SLS。
(4)熔融沉积制造法:其英文名称为Fused Deposition Modeling,即采用熔融材料加热熔化挤压喷射冷却而成型,可缩写为FDM。
3.不同打印方式的差异
每一种打印方式都各有特点,其成型到制造成本都有较大差异,因此其往往适应不同的应用场合。详细的工艺差异如表1-3所示。
表1-3 不同3D打印的工艺差异
