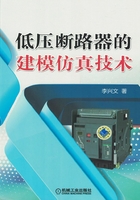
2.5 旋转双断点塑壳断路器操作机构的仿真与优化设计
进入新世纪之后,国外著名低压电器公司纷纷推出了新一代低压断路器产品,如ABB公司的TMAX系列和施耐德公司的NS系列,在触头系统的设计上都采用了旋转式双断点型式,不仅可以很容易做成模块,导电部分连接非常可靠,而且明显提高了分断能力,在塑壳断路器的产品结构设计上可以说是一次重大的突破。
利用ADAMS软件建立的额定电流为630A的旋转式双断点塑壳断路器机构动力学模型及其简化模型如图2-33所示。
图2-33 旋转双断点断路器动力学模型及其简化模型图
a)断路器模型 b)简化模型
低压塑壳断路器的操作机构是典型的五连杆机构。由触头支架f、下连杆g、上连杆h、跳扣k、锁扣m、操作手柄1和分断弹簧等部分组成。当处于图示合闸位置时,分断弹簧虽有贮能,但因下连杆g和上连杆h处于挺直状态(死区位置),C点固定不动,下连杆g、上连杆h、触头支架f和机构构成四连杆机构,处于稳定静止状态,此时触头完全闭合。当手动分合闸时,分断弹簧将随着手柄的转动而受到拉升并储能,当弹簧力的作用线与上连杆h重合时,处于最大位能状态,一旦超过上连杆h,在弹簧力的作用下,下连杆g将推动触头快速运动至闭合或打开位置;当短路电流引起锁扣m转动,在分断弹簧作用下,跳扣k绕O2轴顺时针转动,C点成为活动点,同时下连杆g、上连杆h脱离死区,于是变成五连杆机构。因为五连杆机构有两个自由度,触头继续分断,同手柄位置无关。
2.5.1 影响断路器机构运动速度的主要因素
通过对连杆机构模型的分析,可知影响断路器机构运动速度的因素有三方面:
1)分断弹簧的刚度系数,它对于分断速度的影响最明显。
2)以O1为参考点,轴A、B、C、O2的位置对分断速度的影响。
3)在轴的位置确定后,杆件质量发生变化时对分断速度的影响。
增大分断弹簧刚度系数可以提高断路器的分断速度。分断弹簧在50N/mm、55N/mm和60N/mm的刚度系数下,动触头达到最大打开角度所用时间分别为6.62ms、6.38ms和6.18ms,分断时间逐渐减小,分断过程中角速度测量曲线如图2-34所示。但是随着弹簧刚度系数的增大,手动合闸需要的合闸力也会随之增大,仿真结果表明,在上述三个刚度系数下所需的手动合闸力分别为76N、84N和92N。可见,通过提高刚度系数来提高分断速度是以手动合闸力的增大为代价的,所以单纯提高刚度系数是不可取的,要兼顾对手动合闸力的影响。
图2-34 不同刚度系数下的分断过程角速度曲线
改变连杆机构的长度以及他们的相互位置关系可以改变运动速度,本次优化机构的主要工作就是从这方面入手。以图2-33中轴A、B、C、O2的x、y坐标为单独的设计变量,首先进行设计研究(Design Study)。
结合实际,对每个设计变量设定好变化范围,通过设计研究来观察其对角速度的影响情况,结果见表2-9。
表2-9 轴的位置设计研究结果
从表中可以看出,变量DV_3、DV_4和DV_8的敏感度相对较大,即轴B的x坐标和轴B、轴O2的y坐标对分断过程的平均角速度影响较大。可以进一步对这几个变量进行调整,进行优化分析(Optimization)以获得进一步的优化设计结果。
对此旋转式双断点断路器进行优化时,目标函数取动触头的平均角速度最大化;设计变量为在以上设计研究中敏感度较大的变量DV_3、DV_4、DV_8;约束关系为变量在规定的范围内变化。通过ADAMS软件的优化分析,在考虑三个变量同时变化的情况下,经过优化设计的迭代运算,找到每个变量的最优点,使动触头的平均运动角速度从5678.33deg/s提高到6162.84deg/s,提高幅度为8.55%,触头达到最大打开角度所用时间由6.38ms缩短到5.78ms,减小了0.6ms。优化前后的角速度曲线对比如图2-35所示。
在不同型号的低压断路器中,虽然操作机构的原理是相同的,但杆件形状有很大的不同,所采用的材料也可能不同,所以杆件的质量也是不同的。因此,以图2-33中的杆件f(动触头)、g(下连杆)、h(上连杆)和k(跳扣)的质量为设计变量,进行如上述所介绍的设计研究。各杆件的质量根据杆件本身质量的大小在不同的范围内变化,研究它们对分断过程角速度的影响。表2-10为杆件质量对角速度影响的设计研究结果。
图2-35 优化前后分断过程的角速度曲线
表2-10 杆件质量设计研究结果
从表2-10中可以看出:
1)下连杆的质量对分断过程角速度的影响最弱。
2)跳扣的质量对分断过程角速度的影响较弱。
3)上连杆和动触头的质量对分断过程角速度的影响最大,应注意采取适当措施,减轻其质量。
2.5.2 旋转双断点塑壳断路器触头卡住机构的研究分析
在前文中已经提到,随着电流的增加,当电动斥力足以克服触头预压力时,动触头将被斥开一定角度,若此时操作机构动作不及时,还未带动动触头开始运动,触头将有可能由于霍尔姆力的消失和触头弹簧的作用下发生回落甚至重新闭合而造成熔焊。为了解决这一问题,卡住机构应运而生。
本节以额定电流为250A的旋转双断点塑壳断路器某一种卡住机构为研究对象,建立多体动力学模型,仿真分析了卡住机构的运动过程,并且进行了实验验证,最后分析了卡住机构的可靠性。
图2-36 触头卡住机构模型
触头卡住机构模型如图2-36所示,断路器触头系统的动触头通过可动轴和固定轴以及触头弹簧安装在主轴上;一组通过固定轴安装在主轴的支撑件,该组支撑件上具有月牙形轨道槽,可动轴安装在支撑件的月牙形轨道槽内,并可沿着月牙形轨道槽运动。
如图2-37所示,在电气线路中出现短路电流时,可使断路器的动触头在短路电流产生的电动斥力下迅速斥开,并卡住支撑件的月牙形轨道槽的末端,有效地防止了动触头跌落,提高了断路器的限流效果。
图2-37 动触头卡住前后对比
a)合闸状态 b)卡住状态
为了仿真验证断路器卡住机构的可行性,不考虑脱扣器的作用,当较大的短路电流到来时,动导电杆在电动斥力的作用下迅速斥开到卡住位置,并在卡住机构的作用下不会跌落。由于机构没有脱扣过程,所以动导电杆不能复位,始终处于卡住状态。
将短路电流(预期20kA)、霍姆力动态特性和洛伦兹力动态特性作为机构动力学仿真的输入,导入到ADAMS软件中,进行卡住机构运动过程的仿真分析,仿真结果如图2-38所示。
图2-38 卡住机构运动过程的仿真结果图
由图2-38中可以看出:
0-t1时间段中,触头压力不为0,动静触头依然接触没有分开,电动斥力为洛伦兹力和霍姆力之和,即F斥=FL+FH。
t1-t2时间段中,随着电流的增加,电动斥力足以克服触头预压力,触头压力为0,动静触头分开,霍姆力消失,即F斥=FL。t2时刻动触头被斥开至最大角度,由于卡住机构作用,动触头不会发生回落现象,此时动触头被斥开的开距为18mm。
t2-t3时间段中,随着电流的减小,电动斥力不断减小,直至t3时刻电动斥力减小至0,动触头在卡住机构的作用下基本保持开距为18mm,进而验证了卡住机构设计的合理性。
为了实验验证卡住机构的可行性,本节以未带脱扣器的250A旋转双断点MCCB为实验对象,对其开断过程进行了实验研究,并取预期短路电流为15kA和20kA,实验方法如2.3.1中所述。图2-39和图2-40为试验波形。
图2-39 预期短路电流15kA的电压电流波形
图2-40 预期短路电流20kA的电压电流波形
从实验波形看,两种预期短路电流下均没有发现电弧重燃现象,说明该样机卡住机构设计良好,没有回落现象,且能开断较高的额定电压。
塑壳断路器的卡住机构虽然解决了较大短路电流的动触头斥开后跌落现象,但是当短路电流较小时,动触头能够斥开但不能斥开到卡住位置,这时如果操作机构不能及时动作,动触头会发生跌落现象。即存在临界的电流,使得动导电杆处于是否卡住的临界状态。
研究发现,在分断过程中,动导电杆被斥开后能否卡住不仅与电流的大小有关,还与燃弧时间有关。假设电弧电流波形是正弦波,只需确定其峰值Im和燃弧时间t燃,即可获得电弧电流波形,如图2-41a所示。将电弧电流的峰值Im和燃弧时间t燃设为变量,通过ADAMS软件进行分断仿真,可以得到如图2-41b所示的动触头最小卡住电流的曲线。
图2-41 电弧波形和最小卡住电流曲线
a)电弧电流波形 b)最小卡住电流曲线
仿真研究表明:
1)当电弧电流波形的峰值Im小于最小斥开电流(图中A点)时,由于电弧电流较小,产生的电动斥力不足以克服触头预压力而使触头打开,只有当机构的转角超过超行程以后,在机构的带动下,动导电杆才开始运动。
2)当电弧电流波形的峰值Im和燃弧时间t燃落在最小斥开电流和最小卡住电流曲线之间(图中B点)时,产生的电动斥力克服触头预压力而使触头打开,但是触头斥开后,电动斥力不足以克服触头弹簧反力的增加,动触头不能被斥开到卡住位置,这时如果机构不能及时动作,则斥开的动触头就会向静触头方向返回发生回落现象,造成电弧电压的降低,严重情况下会使动静触头重新闭合,甚至发生触头熔焊。这一现象会使分断过程延长,影响断路器的限流性能。
3)当电弧电流波形的峰值Im和燃弧时间t燃落在最小卡住电流曲线上方(图中C点)时,产生的电动斥力足以使动导电杆克服触头预压力和触头弹簧反力的增加而高速运动,最终动触头被斥开到卡住位置被锁住使之不能回落。
对于上述1),触头没有被斥开,分断能力取决于机构的动作速度,所以提高机构动作速度,有利于提高电弧电压上升速度,减小电弧停滞时间和加快电弧进入栅片,进而可以提高断路器的分断能力。
对于上述2),触头被斥开但存在回落现象,提高机构的动作速度,并与卡住机构合理配合,有利于减小触头回落的幅度,减小动触头跌落和熔焊的几率,提高断路器的限流性能和分断性能。
对于上述3),触头被斥开到卡住位置而被卡住,此时触头弹簧的拉力最大,随后在操作机构的带动下动触头到终端位置时,与设在动触头行程终端的复位止挡相碰,而使这种卡住机构复位。在复位的过程中,动触头在触头弹簧的作用下会回落,因此提高机构的动作速度,有利于减小复位过程中触头回落的幅度,减小电弧重燃的概率。
在上述仿真的基础上,加上电磁脱扣器的作用,即可进行断路器分断过程的仿真。图2-42和图2-43示出了20kA和150kA分断过程仿真结果。可以发现,卡住机构在复位过程中,如果主轴动作不及时,动触头可能会发生回落现象。
t1时刻:动触头刚刚被斥开。
t2时刻:动触头刚刚被斥开到卡住位置。
t3时刻:动触头行程终端的复位止挡相碰。
t4时刻:动触头开始回落。
t5时刻:动触头完全复位,之后与机构同步转动。
图2-42 20kA分断仿真结果
图2-43 150kA分断仿真结果
为了减小动触头回落带来的不利影响,设计复位止挡位置较高,即动触头与其相碰是开距为22mm。20kA分断过程动触头没有发生大的回落,是由于燃弧时间较长,触头受电动斥力作用时间较长。