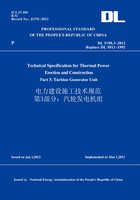
4.9 Cylinder Covering
4.9.1 For cylinder covering,the working area shall be controlled and enclosed,and irrelevant personnel must not enter the area.Working personnel on turbine shall wear coverall without button.Tools for covering shall be registered and kept by designated person,and be counted and verified before closing the casing.Tools brought to the casing shall have provision against dropping.
4.9.2 Before final cylinder covering,a trial covering shall be done after fitting all internal parts,trial covering can be done respectively for double-shell casing,provided that all bolts on inner cylinder split shall be tightened before trial covering of outer cylinder.The following work shall be done during trial covering:
1 Measuring the radial clearance between steam seal carrier ring,diaphragm carrier ring,diaphragm and casing.
2 After tightening the inner cylinder,diaphragm carrier ring and steam seal carrier ring bolts and fitting the thrust pads,turn the rotor to check by hearing,and there shall be no abnormal noise inside the casing.
3 I&C measuring elements inside the casing shall be trial fitted.
4.9.3 Before turbine covering,the following work shall have been completed to requirements,and the installation records and signatures shall be complete:
1 Pad block adjustment has been completed,and anchor bolts have been tightened.
2 Adjustment of soleplate longitudinal and transversal sliding pins,casing vertical pins and claw transversal pins has been completed and recorded.
3 Gap adjustment for inner cylinder claw,longitudinal and transversal sliding pins and axial locating pins has been completed and recorded.
4 The casing horizontal joint surfaces gap complies with specification.
5 The journal ellipticity and non-cylindricity of turbine rotors,coupling radial and ending run out,thrust collar run out and rotor bending comply with specification and are recorded.
6 The casing horizontal up-rising inclination and the rotor up-rising inclination before and after connection of condenser with casing have been recorded.
7 Load distribution and recording have been done for casing to the specification of manufacturer.
8 The center position of turbine rotor at steam seal and oil baffle cavity and the center of rotor shaft system comply with manufacturer requirements.
9 Diaphragm center adjustment has been completed and recorded.
10 Rotor and casing have been relatively positioned,and the locating positions have been marked and their values recorded.
11 The clearance of steam seal and flow passage complies with manufacturer requirements and has been recorded.
12 Axial clearance pushing check,measurement and locating have been done for turbine rotor in actual closed condition,and they shall comply with manufacturer design requirements and be recorded.
13 Flange heating device leakage test complies with specification and has been recorded.
14 All alloy steel parts inside the casing have been rechecked with spectrum method and comply with specification.
15 Hardness and spectrum re-check has been done for high temperature fasteners,and they comply with manufacturer requirements and have been recorded.
16 Thermal pipes with influence on casing geometric dimensions,shaft system center,flow passage clearance and steam seal clearance have been connected.
17 The inside of casing,pipe sections and steam chamber has been thoroughly cleaned,and the pipe ends and instrument sockets and plugs have been enclosed.
18 The drain ports inside casing are well through and I&C elements have been fitted to place.
4.9.4 The work of cylinder covering shall comply with the following provisions in addition to the provisions in 3.3.9:
1 All equipment parts required in covering shall be counted and checked to specification in advance,and be put in a neat manner to sequence.
2 Working tools shall be registered one by one,and be counted again after completion of covering.
3 It shall be ensured that inside the casing is clean and free of sundries,the joint surfaces are smooth,all openings and passages shall be through and parts to be blocked or isolated shall be enclosed.
4 Part joints of the casing shall be coated with high temperature anti-seize agent according to design requirements.
5 Parts that may get loose inside the casing shall be finally locked before covering.
6 After tightening the inner cylinder,diaphragm carrier ring and steam seal carrier ring bolts and fitting the thrust pads,turn the rotor and there shall be no frictional noise inside the casing.
7 When the upper casing is lifted,the horizontal up-rising inclination of upper casing joint surface and lower casing shall be the same,guiding rods coated with oil shall be fitted during covering,and be checked from time to time,the casing shall be lowered homogeneously without jamming.
8 The high temperature anti-bite agent on casing horizontal joint surfaces shall be applied when the upper casing has approached lower casing in a homogeneous and continuous manner,and after covering,this agent shall be able to spread over the whole joint surfaces.
9 The locating pins shall be driven into the pin holes during initial contact of upper and lower casing joint surfaces before the slings are released.
10 The whole work process of covering shall be continuous without interruption from the lifting of the first part of inner cylinder up to locating of upper casing,or up to covering of the outer upper casing for a double-shell structure casing.
11 After completion of covering,the rotor shall be turned again to check if there is any abnormal noise.
4.9.5 For an inner cylinder supported by upper claws,the following provisions shall be complied with when the temporary lower claw support is changed to upper claw support:
1 The permissible deviation of casing center variation is 0.03mm.
2 The total number of claw pads must not exceed 3 and they shall be in close contact,free of gap when checked with a 0.05mm feeler gauge.
3 Materials of pads shall comply with manufacturer requirements.
4.9.6 For an outer cylinder supported by upper claws,the following provisions shall be complied with when the temporary lower claw support is changed to upper claw support:
1 The shift of cushion blocks shall be done after covering and all bolts on outer cylinder horizontal joint surfaces have been tightened.
2 During inlaying or shifting upper claw pads,a dial gauge shall be used to monitor the change of claw position,and the permissible deviation is 0.03mm.
3 The cushion block load bearing surfaces shall be in good contact,and there shall be no gap when checked with a 0.05mm feeler gauge.
4.9.7 The cold spring of casing horizontal joint surfaces bolts shall follow the provisions below:
1 The cold spring shall start from the middle of casing,and bolts shall be tightened symmetrically on left and right in turn.All bolts shall be tightened to equal torque,and after cold tightening of all bolts,a check shall be made in the above sequence,to confirm conformity with manufacturer requirements.
2 The casing horizontal joint surfaces shall be tight.
3 In cold spring,nuts must not be tightened with a hammer,and motor-driven,pneumatic and hydraulic tools with torque indication and without impact can be used.
4.9.8 The hot spring of casing horizontal joint surfaces bolts shall follow the provisions below:
1 Bolts shall be locked manually with spanner in cold state,and after confirming there is no gap on nut,washer and casing plane,the relative positions of nuts and casing shall be marked,the nut rotation arc length be determined according to the bolt extension provided by manufacturer,and the rotation position after hot spring be marked on the casing.
2 Special tools shall be used for heating up the bolts,bolts shall be heated evenly,and direct baking of threaded part shall be avoided.
3 Hot spring of bolts shall be in the same sequence as in cold spring,and hot spring shall be completed one time after heating.If the specified values are not reached in one time,the bolts shall be heated up again after their complete cooling.
4.9.9 After completion of turbine covering,the washers of linking bolts at soleplate and claws shall be checked,and they shall be able to slide freely when pushed with a hand.
4.9.10 Installation of HP inner cylinder steam admission pipe shall comply with the following provisions:
1 The inside and interlayer of steam admission pipe must be cleaned,the flanges shall be flat and smooth,without radially through groove.
2 The inner and outer circles and planes on both sides of the sealing ring and its groove shall be smooth and free of burr.
3 The sealing ring shall have good elasticity and can meet fitting requirements when fitted.
4 The total clearance a on both sides of sealing ring fitting with groove should be 0.08mm-0.11mm,as shown in Fig.4.9.10,and the total clearance on both sides over the whole circumference shall be homogeneous.

Fig.4.9.10 Schematic diagram of HP steam admission pipe sealing ring
1-outer sealing ring;2-inner sealing ring;3-steam admission pipe;4-sleeve;5-adjusting ring;6-shield ring
5 The connection dimensions on both ends of sealing ring opening shall be correct for fitting,and the gap for that fitted into the inner cylinder nozzle chamber sleeve should be 1.50mm.
6 Special tools shall be used to fit sealing rings,the expansion of their opening shall not exceed the maximum permissible value,and if the sealing rings on casing have been completed and fitted in factory,their completeness and soundness shall be confirmed.
7 Care shall be taken to prevent damage of sealing rings when the steam admission pipe is inserted into inner cylinder steam chamber.
8 It is not necessary to fit and measure again a fitted steam admission pipe.
4.9.11 Installation of the crossover between HP and IP casing and LP casing shall comply with the following provisions:
1 Before installation,the crossover welds shall be subject to oil leak test and conform to specification,and the inside shall be clean without sundries.
2 Trial fitting of crossover shall be done after locating of casing,and its coupling shall be free of external stress.
3 In the installation of crossover compensation device and its linkage,adjustment shall be made to the cold spring value and linkage pre-deviation value required by manufacturer.
4 After completion of crossover installation and adjustment,the shipping fixing pin on compensation device shall be removed,and the crossover shall be able to extend and retract freely.
4.9.12 If the turn is to be uncovered again after official covering,the following provisions shall be complied with:
1 Approval shall be obtained.
2 Hot spring bolts must not be loosened by force,they can be loosened only after heating them with special tool to the extent that the bolt extension has exceeded hot spring value;if they cannot be loosened after the first heating,heating can be done again only after their complete cooling.
3 Before lifting,guide rods shall be mounted,and lubricant shall be applied on the rods.
4 Before lifting,the upper casing shall be lifted homogeneously with the upper casing lifting bolts,to separate the horizontal joint surfaces,and during lifting,the casing shall be kept horizontal and the four corners shall rise homogeneously,monitoring dial gauges shall be fitted at the couplings on both ends of the rotor,to prevent carrying any lower part or damaging the rotor.
5 For a turbine unit after operation,uncovering should be done after it has been cooled to room temperature.