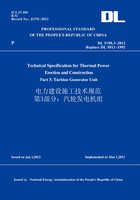
4.7 Installation of Equipment in Flow Passage
4.7.1 Inspection and installation of nozzles shall comply with the following provisions:
1 There shall be no crack,casting sand,overlap or oily dirt in appearance check.
2 The joint surfaces of nozzle block with nozzle slot or steam chamber shall be checked with coloring method,and the contact area shall be over 75%,there shall be no through defect on sealing surface,and the joint surfaces between unassembled nozzles and the gap between the nozzle block end face locating keys and pins shall not be greater than 0.04mm.The assembled nozzles or nozzle blocks shall be tight without looseness,and the nozzle block steam outlet shall be flush.
3 After tightening of the single-head bolts for nozzles,a gap no less than 1.00mm shall be ensured from the bolt threaded bar end to the bottom of threaded hole,the tightening torque and elongation of bolts shall comply with the manufacturer requirements and be recorded,and the bolts and pins shall be fixed by spot welding before cylinder covering.
4 For nozzle mounting,the joint surfaces shall be evenly coated with high temperature anti-seize agent.
4.7.2 Inspection of diaphragm and diaphragm carrier ring before installation shall comply with the following provisions:
1 The diaphragms and diaphragm carrier rings shall be free of damage,paint or rusty dirt,the contact surfaces shall show metallic luster,and cast iron diaphragms shall have no defect such as crack,casting sand or porosity.
2 In appearance check,stationary blades shall be free of crack,casting sand,overlap or looseness,and the edges shall be flat,without curling or protrusion.There shall be holes on hollow stationary blades.
3 The shroud seals shall be complete without missing,free of curling,and with sharp and thin edges.
4 Gap inspection of diaphragm and diaphragm carrier ring horizontal joint surfaces shall comply with the following provisions:
1)It shall be less than 0.05mm with the HP and IP diaphragms and diaphragm carrier rings in free state.
2)It shall be less than 0.10mm with the LP diaphragms and diaphragm carrier rings in free state,and less than 0.05mm after the bolts are tightened.
3)It shall be less than 0.05mm for cast steel diaphragm in free state.
4)It shall be less than 0.10mm for cast iron diaphragm in free state,and less than 0.05mm on inclined section.
5 The fitting gap of the pins and keys locating the upper and lower diaphragms and diaphragm carrier rings and the corresponding holes and slots should be 0.05mm-0.08mm.
6 The expansion gap between diaphragm,diaphragm carrier ring and cylinder shall comply with requirements on drawings.Diaphragm claw shims shall be in close contact and not exceed three,and the shim material shall meet the requirements for working temperature.
7 Drain holes shall be provided on lower diaphragm and diaphragm carrier ring as required on the drawings of manufacturer,and proper drain shall be ensured when the diaphragm and diaphragm carrier ring are set to place.
8 Stationary blade carrier ring,diaphragm and diaphragm carrier ring,steam seal strip and seal carrier ring shall be marked with steel stamp as per turbine proper number,and the installation position shall be marked.
9 The axial play of stationary blade carrier ring,balance piston steam seal carrier ring and gland seal carrier ring shall comply with the manufacturer requirements,and it should be 0.15mm-0.25mm for HP casing and 0.40mm-0.50mm for LP casing when there is no requirements from the manufacturer.
4.7.3 Centering for diaphragm shall comply with the following provisions:
1 The final alignment of diaphragm centers shall be performed after completion of the following work:
1)Installation of the pipe section from HP and IP lower outer cylinder to extraction check valve and the first support or hanger.
2)Connection and locating of HP and IP combined valve and lower casing.
3)Connection of LP casing with condenser.
4)Other work that may result in change of the casing center and up-rising inclination.
2 The permissible deviation of diaphragm centering tool with respect to the center position of rotor and cavity is 0.05mm.
3 When a dummy shaft is used in centering,the fitting of dummy shaft with support base shall be tight,the cavity measuring parts shall be securely mounted,no transversal displacement or axial play of dummy shaft is allowed during measurement,and in measurement,the droop arc difference of dummy shaft and rotor shall be calculated and corrected.
4 In centering with wire,a long wire through the cavity centers of HP,IP and LP bearings should be used as reference line,to determine the center position of the oil baffles,steam seals and diaphragm cavities with this as the reference.
5 When a wire is used in centering,it shall be able to trim the wire fixing device with respect to wire tightening force and position,the diameter of the wire used should not exceed 0.40mm,the tensile force of wire should be 3/4 of failure stress,and in measurement,correction shall be made to the droop arc of wire,refer to Appendix F.Any specific requirement from the manufacturer shall be implemented.
6 Centering with a laser collimator shall comply with the following provisions:
1)The permissible deviation of the laser beam in a range of 40m is 0.05mm,the laser spot shall be a circle,and the receiving target shall be securely set in the casing cavity.
2)Work with electrical welding,flame welding or use of fire should not be conducted within 2m around on-site where the laser collimator is used.
3)When the laser beam is affected by external interference to laser collimator,the output beam will be adjusted automatically to keep the reference unchanged.
7 Centering of steam seal cavity of diaphragm shall use the lower diaphragm as reference,and if the diaphragm cavity is not a circle,steam seal clearance shall be adjusted on an overall basis.
8 Lower diaphragm cavity centering in semi assembled casing state shall be corrected to the completely assembled casing state value according to requirements of manufacturer.
9 In centering for inlaid diaphragm cavity,the center value of each diaphragm shall be measured and recorded.
10 The left and right permissible deviation of diaphragm cavity center is 0.05mm for HP and IP casing and 0.08mm for LP casing;the up and down permissible deviation of diaphragm cavity center is 0.05mm,and the center is permissible to be lower.
11 When the left and right deviation of diaphragms of suspension structure is within 0.30mm,adjustment can be made by changing the suspension loop shim thickness.
4.7.4 The inspection and installation of rotary diaphragms shall also comply with the following provisions in addition to the provisions in 4.7.3 and 4.7.4 of this part:
1 The joint surfaces of the moving and stationary parts shall have no gap when checked with a 0.05mm feeler gauge.
2 The lock bolts shall be locked after completion of rotary diaphragm assembling.
3 An operation test shall be performed for rotary diaphragms before cylinder covering,and the diaphragms shall rotate flexibly,the fully open and fully close positions shall correspond to the hydraulic servomotor and comply with drawing requirements,and the indications shall be correct.
4.7.5 Inspection of steam seal carrier ring before installation shall comply with the following provisions:
1 It shall be free of defect or oily dirt in appearance check.
2 The pins on horizontal and vertical joint surfaces of steam seal carrier ring shall be tightly fit.
3 The horizontal joint surfaces of steam seal carrier ring and the vertical joint surfaces of steam seal carrier ring and casing shall be tight,and there shall be no gap when checked with a 0.05mm feeler gauge with the bolts tightened.
4 The drain holes of steam seal carrier ring shall be well through.
5 The fitting of steam seal carrier ring and cavity shall comply with drawing requirements.
4.7.6 After mounting the steam seal block with spring,the block must not be jammed in the slot and shall be able to spring back after being pressed in.
4.7.7 Installation of shunt ring in the middle of a double flow casing shall comply with the following provisions:
1 The assembling gap of shunt ring parts shall comply with manufacturer requirements and be recorded.
2 Shunt rings must not be reversed when fitted and shall have position marks.
3 The shunt ring and diaphragm contact surfaces and horizontal joint surfaces,and the bolts and nuts shall be coated with high temperature anti-seize agent.
4.7.8 Measurement of steam seal clearance shall comply with the following provisions:
1 The steam seal clearance and shroud ring seal shall be measured and recorded one by one.
2 In measuring the gland axial clearance,the circumferential direction of rotor shall be fixed,and should be in the direction with emergency governor flying hammer upward,or in the same direction as in the general assembling in factory,and the thrust collar of rotor shall be in close contact with the thrust pad working surface.
3 The axial clearance of steam seal can be measured with a wedge feeler gauge on both sides of lower steam seal.
4 The left and right radial clearance of steam seal shall be measured with a feeler gauge,the top and bottom clearance can be measured by sticking plaster or pressing a fuse,and when the fuse pressing method is used,the shaft seal block shall be fixed temporarily.
5 The radial and axial clearance of steam seal shall comply with manufacturer requirements,relevant data provided by manufacturer must not be arbitrarily modified erection on-site,if the steam seal clearance data are not in line with manufacturer requirements,manufacturer shall make clear instruction and give approval.
4.7.9 Adjustment shall be made as specified below if the steam seal radial clearance is off-spec:
1 In case of excessively large radial clearance of steam seal,the load bearing contact position of steam seal block in the cavity may be trimmed,refer to Fig.4.7.9(a).

Fig.4.7.9 Schematic diagram of steam seal
2 For excessively small clearance,the steam seal strip edge can be trimmed or machined to make it sharp,thin and smooth.
3 For steam seal block with adjusting shim,the steam seal clearance can be adjusted with shim thickness,and after adjustment,the screws shall be tightened and provision against loosening shall be made,the materials of tightening screws shall comply with requirements on drawings.
4 The recession gap d of steam seal block shall comply with drawing requirements.
5 After completion of steam seal clearance adjustment,the expansion gap of the whole ring of steam seal block shall be measured,it should be 0.20mm-0.25mm,and the two adjacent curved ends shall be in close contact.
4.7.10 Installation of adjustable steam seal shall be as shown in Fig.4.7.10,and shall comply with the following provisions:

Fig.4.7.10 Schematic diagram of adjustable steam seal
1 The steam seal groove and steam seal arc block shall be cleaned from burrs,cutting trace and oxide scale,and be ground smooth,the contact condition of sealing surfaces shall be good as checked with color coating method,and the steam seal arc block shall move freely in the T-shaped groove.
2 Before mounting the steam seal,the cavity center shall be properly adjusted,to ensure that the difference between left and right sides is less than 0.10mm;and the difference between the average of the sum of left and right gaps and the lower gap is less than 0.05mm.
3 Check that the recession gap of steam seal block in the steam seal groove and the reserved gap at the end of steam seal block comply with design requirements,and the steam seal block ends shall be in good contact when closed.
4 Before official assembling,the T-groove and sealing surface of steam seal ring shall be coated with anti-seize lubricant,special springs shall be fitted and their original length be recorded,and then springs and steam seal blocks are fit into the steam seal groove by numbers.
4.7.11 Measurement of flow passage gap shall comply with the following provisions:
1)The gap of flow passage shall comply with requirements on drawings,and the measurement records shall be compared with the ex-works records from manufacturer.
2)Before measuring the flow passage gap,the rotor shall be positioned first according to the gap value between the first stage nozzles and rotor impeller provided by the manufacturer,and during locating,the rotor thrust collar shall be in close contact with the working surface.
3)In the first measurement,the flying hammer of emergency governor shall be arranged upward;in the second measurement,it shall be turned in the rotor operation direction by 90°,and each time,the gap on both left and right sides shall be measured.
4)After final locating of rotor,the distance of the casing external steam seal end surface to the exposed precision machine surface on the rotor shall be taken as the basis for axial locating of casing,and the measured positions shall be marked.
4.7.12 The minimum axial clearance of governor stage and the upper half of turning diffuser ring can be measured by pushing the turbine rotor forward and backward.During the measurement,parts that may prevent turbine rotor forward and backward movement shall be removed,and care shall be taken to prevent damaging the equipment.
4.7.13 The final record of rotor axial play shall be the data measured at the time of I&C setting axial displacement indication after the upper casing has been assembled.
4.7.14 If the flow passage clearance and steam seal axial clearance are not up to specification,the manufacturer shall determine how to solve the problem.