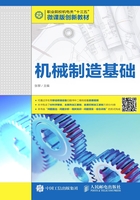
第1章 金属的力学性能
【学习目标】
知识点
1.理解金属的常用力学性能指标的含义及计算方法。
2.理解金属的常用力学性能对材料的应用范围和产品质量及工艺性能的影响。
3.了解常用物理性能和化学性能对材料的应用范围和产品质量及工艺性能的影响。
技能点。
1.掌握常用力学性能指标硬度测试方法及其应用。
2.了解强度、塑性、冲击韧度及疲劳极限等力学性能指标的测试方法及其应用。
3.能根据机件或工具的工作条件,分析对其制造材料力学性能的要求。
金属材料之所以被广泛地应用在各个领域,是由于它具有许多优良的性能。金属材料的性能包含使用性能和工艺性能两个方面。使用性能是指金属材料在使用条件下,表现出来的性能,它包括力学性能、物理性能和化学性能等。使用性能的好坏,决定了它的使用范围和使用寿命。工艺性能是指金属材料在加工制造过程中适应加工的性能,它包括铸造、锻压、焊接、热处理及切削加工性能等。工艺性能直接影响零件加工后的工艺质量,是选材和制订零件加工路线时必须考虑的因素之一。这里主要介绍金属的力学性能。
金属在加工或服役过程中,都要承受各种不同外力的作用,当外力超过一定限度时,金属就会发生变形,甚至断裂。金属的力学性能是指金属在外力作用下抵抗变形与断裂的能力及发生变形的能力。这种能力的大小与强弱需要用力学性能指标来衡量和比较,常用的力学性能指标有强度、塑性、硬度、韧性及疲劳极限等。
|1.1 强度与塑性|
问题提出
在现代桥梁设计制造中,金属悬索桥和斜拉桥是最为常见的结构形式,它不仅具有用料省、自重轻的特点,而且,还可以实现其他桥梁无法达到的大跨度结构。虽然我们现有的知识和能力,还不足以独立完成一座桥梁的设计工作,但通过对金属材料强度、塑性等力学性能的学习,可以使我们对其中金属工作组件的力学性能要求有一些初步的了解。
图1-1为悬索桥(吊桥)的结构示意图,试分析设计人员是如何保证桥梁的承载安全的?

图1-1 悬索桥结构示意图
问题分析
从图1-1中可以看出,悬索桥的桥体重量主要依靠“主索”(也称悬索或大缆)和“吊索”(也称吊杆)吊拉,主索和吊索的承载能力是关键因素,它们在使用过程中不能产生变形,更不能发生断裂。主索和吊索的截面尺寸过小不能满足使用要求,截面尺寸过大又造成材料浪费,所以必须要进行精确设计和计算,其设计依据就是所选用材料的强度和塑性等力学性能指标。
相关知识
一、载荷、变形与应力
1.载荷
金属材料在使用和加工过程中所受到的各种外力统称为载荷,用符号F表示。载荷按其作用的性质不同,可分为静载荷、冲击载荷及交变载荷3种。
静载荷是指大小和方向不变化或变化缓慢的载荷,如钢丝绳吊起货物过程中所承受的载荷;在很短时间内作用于金属材料上的载荷称为冲击载荷,如冲床的冲头、风动工具等;交变载荷是指载荷大小,甚至方向随时间发生变化的载荷,如齿轮、弹簧等。
2.变形
金属材料受到载荷作用而产生的几何变形和尺寸的变化称为变形。变形分为弹性变形和塑性变形。随载荷的存在而产生、随载荷的去除而消失的变形称为弹性变形。载荷去除后仍不能恢复的变形称为塑性变形。
3.应力
金属材料在受到外力作用时,其内部作用着与外力相对抗的力,称为内力。单位面积上的内力称为内应力,内应力能够准确地反映金属材料内部的受力状态,因此,强度指标都是用应力表示的。生产中最常用、最基本的金属力学性能指标——屈服强度、抗拉强度、塑性等均是通过单向静拉伸试验测定的。
二、金属室温静拉伸试验
单向室温静拉伸试验是在试样两端缓慢施加载荷,使试样的工作部分受轴向拉力,引起试样沿轴向伸长,直至拉断为止。它是应用最广泛的金属力学性能试验方法之一。
1.拉伸试样
试验表明,所用试样的形状和尺寸及加工质量对其性能测试结果有一定影响。为了测定金属材料或零部件的拉伸性能并使金属材料拉伸试验的结果具有可比性,拉伸试样的形状和尺寸及取样和制样应符合《金属材料室温拉伸试验方法》(GB/T 228—2010),常用拉伸试样如图1-2(a)所示。图中d0是圆形截面试样的直径,L0为试样的有效工作部分称为原始标距。根据原始标距(L0)与圆形截面试样直径(d0)之间的关系,试样分长比例试样(L0=10d0)和短比例试样(L0=5d0)两种。拉伸试验时,一般优先选用短比例试样。
2.拉伸曲线
试验前应先检查试样外观是否符合要求。试样原始标距一般采用细划线或细墨线进行标定。拉伸试验机一般用液压万能试验机或电子万能试验机。
将拉伸试样安装在材料试验机上,缓慢且均匀施加轴向力 F,观察并测定试样在外力作用下的变形过程,直至试样断裂为止。外力F与试样绝对伸长量之间的关系曲线称为力-伸长曲线。力-伸长曲线形象地描绘出材料的变形特征及各阶段受力与变形间的关系,可由该图形的形状来判断材料特性与塑性好坏,断裂时的韧性与脆性程度及不同变形情况下的承载能力。在拉伸试验时,利用试验机的自动绘图器可绘出力-伸长曲线。图 1-2(b)所示为低碳钢力伸长曲线(F-ΔL曲线),图中纵坐标为拉伸力F,横坐标是绝对伸长量ΔL。

图1-2 拉伸试样和低碳钢F-ΔL曲线
由图1-2(b)可知,试样伸长量随拉力增大而增加。拉伸力在Fp以下阶段(Op段),试样在受力时发生变形,在此阶段中拉力和伸长呈正比关系,卸除拉伸力后变形能完全恢复,该区段为完全弹性变形阶段。在曲线的pe段,伸长量与拉伸力不再呈正比例关系,拉伸曲线也就不再是直线,但仍处于弹性变形阶段。一般来说p点和e点是很接近的,实际过程中p点和e点一般不易分辨。
当所加的拉伸力F超过Fe后,外力不增大或变化不大,试样仍继续伸长,开始出现明显的塑性变形。曲线上出现平台或锯齿(曲线ess'段),试验机示力盘上的主指针暂停转动或开始回转、来回摆动。现象表明试样所承受的拉力不继续增大或稍微减少的情况下试样却继续伸长,这种现象称为材料的屈服。
在曲线的 s'b段,外力增大,伸长沿整个试样长度均匀进行,继而进入均匀塑性变形阶段。同时随着塑性变形不断增加,试样的变形抗力也逐渐增加,产生形变强化,这个阶段是材料的强化阶段。
在曲线的最高点(b点),达到最大拉伸力 Fb时,试样再次产生不均匀的塑性变形,变形主要集中于试样的某一局部区域,该处横截面积急剧减小,结果就形成了所谓“缩颈”现象。随着缩颈处截面不断减小,承载能力不断下降,到k点时,试样发生断裂。
由此可知,低碳钢在拉伸力作用下的表现过程可分为弹性变形阶段、屈服阶段、均匀塑性变形阶段、缩颈(集中塑性变形阶段)和断裂阶段。正火、退火碳素结构钢和一般低合金结构钢,也都具有类似的力-伸长曲线。但工程上使用的金属材料,多数在断裂前没有明显的塑性变形。有些材料不仅没有屈服现象,而且也不产生“缩颈”现象。
3.应力-应变曲线
力-伸长曲线只代表试样的力学性质,同一种材料的力-伸长曲线中,横、纵坐标会因试样尺寸不同而各异。为了使同一种材料不同尺寸试样的拉伸过程及其特性点便于比较,以消除试样几何尺寸的影响,将力-伸长曲线的横、纵坐标分别用拉伸试样的原始标距长度 L0和原始横截面积S0去除,则得到应力-应变曲线。因坐标数值均以一常数相除,故应力-应变曲线与力-伸长曲线形状相似,但消除了几何尺寸的影响。
三、强度与强度指标
1.强度及其意义
强度是指金属材料抵抗塑性变形或断裂的能力,是工程技术上重要的力学性能指标。
材料强度的大小,通常用单位面积所受的力来表示,其单位为MPa。强度越高,相同截面积的材料在工作时所能承受的载荷就越大。当载荷一定时,选用高强度的材料,就可以减小机件的截面尺寸,从而减小其自重,对于汽车、船舶等交通运输工具的意义更加突出。
2.屈服强度
金属材料拉伸试样发生屈服现象时,力所对应的点称为屈服点。用应力表示的屈服点称为屈服强度。
屈服现象是材料在拉伸时开始塑性变形的一个标志。屈服强度可以理解为金属材料开始产生明显塑性变形的最小应力值,其实质是金属材料对初始塑性变形的抗力。
屈服强度用符号σs表示,在《金属材料 拉伸试验》(GB/T 228—2010)中,用ReL(下屈服强度)选作为屈服强度指标。计算公式如下:

式中,σs——屈服点(MPa);
Fs——试样屈服时的载荷(N);
S0——试样原始横截面积(mm2)。
有些金属材料(如高碳钢、黄铜等)在拉伸试验时无明显的屈服现象,对于这类材料用规定微量塑性伸长应力表征材料对微量塑性变形的抗力。规定微量塑性伸长应力是人为规定拉伸试样标距部分产生一定的微量塑性伸长率(如0.01%、0.02%、0.2%等)时的应力。一般用试样发生0.2%塑性伸长率时的应力,称为条件屈服强度,用σ0.2表示。GB/T 228—2010中用Rp0.2表示。
在生产实际中,绝大部分工程构件和机器零件在其服役过程中都处于弹性变形状态,不允许有明显的塑性变形产生。屈服强度是工程技术上重要的力学性能指标之一,也是大多数工程构件和机器零件选材和设计的依据。传统的设计方法,对于韧性材料以屈服强度为标准,规定许用应力[σ]=σs/n(或[σ]=ReL/n),一般安全系数n取2或更大。
3.抗拉强度
试样在断裂前所能承受的最大应力称为抗拉强度,又称强度极限,用符号σb表示,GB⁄T 228—2010规定抗拉强度符号用Rm表示,按下列公式计算:

式中,σb——抗拉强度(MPa);
Fb——试样承受的最大载荷(N);
S0——试样原始横截面积(mm2)。
抗拉强度的物理意义是韧性材料抵抗大量均匀塑性变形的能力。铸铁等脆性材料拉伸过程中一般不出现缩颈现象,抗拉强度就是材料的断裂强度。
断裂是零件最严重的失效形式,所以,抗拉强度也是工程设计和选材的主要指标,特别是对脆性材料而言。
屈服强度与抗拉强度的比值(σs/σb或ReL/Rm)称为材料的屈强比。屈强比越小,表示材料的屈服强度与抗拉强度的差距越大,即塑性越好,万一超载,由于塑性变形的产生使金属材料的强度提高而不致立即破坏,从而保证了使用中的安全性,但屈强比太小,使材料强度的有效利用率低;相反屈强比高,说明屈服强度接近抗拉强度,材料在断裂前塑性“储备”太少,对应力集中敏感,安全性能下降。合理的屈强比一般在0.6~0.75之间。
当材料受到压应力、弯曲应力及扭转应力等时,其抵抗破坏能力分别称为抗压强度(σbc或Rmc)、抗弯强度(σbb)及抗扭强度(τm)等,单位与抗拉强度相同。
四、塑性与塑性指标
1.塑性
塑性是金属材料断裂前产生塑性变形的能力。
金属材料断裂前产生的塑性变形由均匀塑性变形和集中塑性变形(缩颈)两部分组成。大多数拉伸时形成缩颈的韧性金属材料,其均匀塑性变形量比集中塑性变形量要小很多。也就是说,拉伸缩颈形成后,塑性变形主要集中于试样缩颈附近。
为比较和评定金属材料的塑性变形能力,绝大部分机械制造用钢都是采用光滑的圆试样,在静拉伸试验机上做单向静拉伸试验,根据拉断后试样的断后伸长率和断面收缩率作为鉴定塑性变形能力大小的指标。
2.断后伸长率
断后伸长率是指试样拉断后标距的残余伸长量与原始标距的百分比,用符号δ表示,GB⁄T 228—2010规定用符号A表示,其计算方法如下:

式中,δ——断后伸长率(%);
Lu——试样拉断后的标距长度(mm);
L0——试样的原始标距长度(mm)。
必须指出,同一材料的试样长短不同,测量的断后伸长率略有不同,用短试样测得的断后伸长率略大于用长试样测得的断后伸长率。长试样和短试样分别用 δ10和 δ5表示,习惯上δ10也常写成δ。
3.断面收缩率
断面收缩率是指试样拉断处横截面积的最大缩减量与原始横截面积的百分比,用符号 ψ表示,GB⁄T 228—2010规定用符号Z表示。其计算方法如下:

式中,ψ——断面收缩率(%);
S0——试样的原始横截面面积(mm2);
Su——试样拉断处的最小截面面积(mm2)。
根据断后伸长率和断面收缩率的相对大小,可以判断金属材料拉伸时是否形成缩颈。若材料的断后伸长率大于或等于断面收缩率,则该材料只有均匀变形而无缩颈现象,是低塑性材料;反之,则有缩颈现象,是高塑性材料。
任何零件都要求材料具有一定的塑性。很显然,断后伸长率(δ)与断面收缩率(ψ)越大,发生的塑性变形量越大,也就是材料的塑性越好。
塑性好的金属材料可以发生大量塑性变形而不破坏,便于通过各种压力加工方法(锻造、轧制、冷冲压等)获得形状复杂的零件或构件。例如,低碳钢的δ可达30%,ψ可达60%,可以拉成细丝,轧成薄板,进行深冲成形。而铸铁的δ和ψ几乎为零,所以不能进行塑性加工。
工程构件或机械零件在使用过程中虽然不允许发生明显塑性变形,但在偶尔过载时,塑性好的材料能在过载处产生塑性变形,由于产生形变强化使承载能力增加,而不至于突然断裂,因此比较安全。
一般情况下,强度与塑性是一对相互矛盾的性能指标。在金属材料的工程应用中,要提高强度,就要牺牲一部分塑性。反之要改善塑性,就必然牺牲一部分强度。但通过细化金属材料的显微组织,可以同时提高材料的强度和塑性。
问题落实
(1)桥梁承载安全分析。
根据以上知识,为了保证悬索和吊索在使用过程中不产生塑性变形,设计人员要以屈服点σs或屈服强度σ0.2为设计依据,根据各悬索、吊索的受力大小和所选用材料的屈服点σs或屈服强度σ0.2,确定其尺寸。计算过程如下:

由于各种桥梁所用金属材料都具有良好的塑性,在受力过大时,首先产生塑性变形,其抵抗变形抗力(即强度)会因加工硬化而自然提高,不至于发生突然断裂,保证桥梁安全可靠。
(2)在实际设计中,为了确保桥梁使用安全,还应适当增大金属材料的截面尺寸,具体办法将在相关学科中详细介绍。
综合训练
1.解释下列名词:
(1)拉伸试验;(2)屈服现象;(3)强度;(4)屈服强度;(5)抗拉强度;(6)塑性。
2.什么是金属的力学性能?金属的力学性能有哪些?
3.简述低碳钢拉伸试验的基本过程。
4.屈服强度、抗拉强度在工程上各有什么实际意义?
5.什么是塑性?衡量塑性的指标有哪些?在工程上有什么实际意义?
|1.2 硬度|
问题提出
机械制造中,各种机械金属零件和工具、模具等都要求有一定的硬度,根据工作条件不同,需要的硬度也不同。如轴承座、汽车半轴、传动齿轮、钻头、滚动轴承和表面硬化齿轮等,需要进行硬度测试,我们应该选用什么方法进行测试呢?
问题分析
硬度是衡量金属材料软硬程度的指标,是指金属材料在静载荷作用下抵抗局部变形,特别是塑性变形、压痕、划痕的能力,硬度较高的金属材料具有较强的抗磨损能力。它在一定程度上反映了材料的综合力学性能指标。硬度值的大小不仅取决材料本身的性能,而且还取决于测量方法和条件。用不同的方法测定的硬度值具有不同的意义。
与拉伸试验相比,硬度试验简单,操作迅速方便,又可直接在零件上或工具上进行试验而不破坏工件。在产品设计图样的技术条件中,硬度是一项主要技术指标。硬度的测量方法较多,生产中最常用的有布氏硬度、洛氏硬度和维氏硬度3种试验方法。
相关知识
一、布氏硬度试验
1.布氏硬度原理
布氏硬度试验是在载荷F作用下,将直径D的硬质合金球压头压入到被测金属表面,保持规定时间后卸除载荷,测量被测材料表面留下压痕的平均直径d,根据d计算出压痕面积S,最后求出压痕单位面积上承受的平均压力,以此作为被测金属材料的布氏硬度值,如图1-3所示。

图1-3 布氏硬度试验原理示意图
布氏硬度值的计算公式为

式中,HBW——硬质合金球试验时的布氏硬度值;
F——载荷大小(N);
D——球体直径(mm);
d——压痕平均直径(mm)。
布氏硬度值的单位为kgf/mm2或N/mm2,习惯上布氏硬度是不标单位的。
布氏硬度实际测试时,硬度值一般不用计算,而是用刻度放大镜量出压痕直径 d,再根据d的大小,从硬度表中查出相应的布氏硬度值。
2.布氏硬度规范
布氏硬度的表示方法为:硬度值﹢硬度符号﹢试验条件。如200HBW10/1000/30表示用10mm直径的硬质合金球压头,在1000kgf(9.807kN)作用下,保持30s(持续时间为10~15s时,可以不标出),测定的布氏硬度值为200。
在进行布氏硬度试验时,试验力F与压头直径D平方的比值(0.102F/D2)应为30、15、10、5、2.5、1中的一个。根据金属材料的种类、试样厚度及试样的硬度范围,按照表1-1的规范选择合适的试验条件,在试样尺寸允许时,应优先选用直径为10mm的球压头。
表1-1 布氏硬度试验规范

一般在零件图样和工艺文件上标注材料要求的布氏硬度时,不规定试验条件,只需标出要求的硬度值范围和硬度符号,如200~230HBW。
3.布氏硬度的应用及优缺点
布氏硬度试验法的优点是试样上压痕面积较大,能较好反映材料的平均硬度值,数据比较稳定,重复性好。
缺点是测试麻烦,压痕较大,对材料表面的损伤也较大,不适合测试成品件及薄件材料。布氏硬度适用于铸铁、非铁金属及经过退火、正火及调质处理的钢材,特别是对于软金属,如铝、铅、锡等更合适。
二、洛氏硬度试验
1.洛氏硬度原理
洛氏硬度试验是采用顶角为120°的金刚石圆锥体或一定直径的钢球为压头,以规定的试验力将其压入试样表面。试验时,先加初试验力,然后加主试验力,压入试样表面,经过规定的保持时间后,卸除主试验力,在保留初试验力的情况下,以残余压痕深度计算硬度的试验方法。其原理如图1-4所示。

图1-4 洛氏硬度试验原理示意图
为了保证压头与试样表面接触良好,试验时先加初始试验力F1,在试样表面压入深度为h1,并以此作为测量的标准。然后加上主试验力F2,其总试验力F=F1+F2,此时压头压入深度为h2。经规定的保持时间,卸去主试验力F2,仍保留初试验力F1,试样弹性变形的恢复使压头略微上升一段距离至h3,此时压头受主试验力F2作用压入的深度为h(h=h3−h1)。
洛氏硬度值是以残余压痕深度h大小确定,压痕深度h越大,硬度越低;反之则硬度越高。为了照顾习惯上数值越大,硬度越高的概念,一般用一个常数k减去压入深度h作为硬度值,并以0.002mm的压痕深度为一个硬度单位。由此获得的硬度值称为洛氏硬度值,用符号HR表示。计数公式如下:

式中,HR——洛氏硬度值;
k——常数,用金刚石圆锥体作压头时k=100;用钢球作压头时k=130;
h——残余压痕深度(mm)。
布氏硬度试验时,一般均由硬度计的指示器上直接读出。
2.洛氏硬度规范
为了能用同一硬度计测量从软到硬或薄厚试样的材料硬度,需要采用有不同的压头和载荷组成的A、B、C、D、E、F、G、H、K等9种洛氏硬度标尺,此外还有6种表面洛氏硬度,共15种。最常用的是A、B、C三种标尺,分别记作HRA、HRB、HRC,其中洛氏硬度C标尺应用最广。
洛氏硬度不标单位,是一个无量纲的力学性能指标,表示方法是将硬度值写在硬度符号前面。例如,50HRC表示用C标尺测定的洛氏硬度值为50。洛氏硬度各标尺之间没有对应关系,洛氏硬度试验条件及应用范围如表1-2所示。
3.洛氏硬度的应用及优缺点
洛氏硬度试验方法是目前应用最广泛的硬度测试方法。它的优点是测量迅速简便,压痕较小,可用于测量产品件;缺点是由于压痕较小,测得的硬度不够准确,数据重复性差。因此,在测试金属的洛氏硬度时,需要选取不同部位测试3次,取其平均值为该材料的硬度值。
表1-2 常用3种洛氏硬度的试验条件及应用范围

三、维氏硬度试验
1.维氏硬度原理
维氏硬度试验原理与布氏硬度试验原理相似,也是根据压痕单位表面积上的试验力大小来计算硬度值,不同的是维氏硬度采用相对面夹角为136°的正四棱锥体金刚石作压头,试验原理如图1-5所示。
试验时,以选定的试验力将压头压入试样表面。经规定的保持时间后,卸除试验力,测量压痕对角线长度,可计算出压痕表面积,压痕单位表面积所承受的平均压力即为维氏硬度值,用符号HV表示。计算公式如下:

式中:HV——维氏硬度,不标单位;
F——试验力(N);
S——压痕面积(mm2);
d——压痕两对角线长度平均值(mm)。

图1-5 维氏硬度的试验原理示意图
在实际测试时,维氏硬度值不用计算,而是用测微计测出压痕对角线的长度,计算出平均值后,再根据d的大小查GB/T 4340.1—2009附表,即可求出所测硬度值。
2.维氏硬度规范
维氏硬度试验所用的试验力根据试件的大小、薄厚及其他条件选择,常用试验力在49.03~980.7N(5~100kgf)范围内。
维氏硬度的表示方法与布氏硬度相同,在符号HV的前面写硬度值,试验条件写在符号的后面,若试验力保持时间为10~15s时,可以不标出。如640HV30/20表示在30 kgf(294.2N)试验力作用下,保持20s测得的维氏硬度值为640。
3.维氏硬度的应用及优缺点
维氏硬度的优点是试验载荷小,压痕较浅,适用范围宽,测试范围在5~3000HV,可以测定从极软到极硬的各种金属材料,尤其适于测量零件表面淬火层及化学热处理的表面层等。同时维氏硬度只用一种标尺,材料的硬度可以直接通过维氏硬度值比较大小,不存在布氏硬度试验力F与球体直径 D之间关系的约束,也不存在洛氏硬度那样不同标尺的硬度无法统一的问题。维氏硬度的缺点是对试样表面要求高,压痕对角线长度测量比较麻烦,不适于大批测试。
问题落实
1.测量硬度值
(1)测量轴承座的硬度值
轴承座通常用灰铸铁制造,一般直接在铸态下使用,本身硬度不高,且组织不均匀,应采用布氏硬度测量其硬度值。一般情况下,该材料的硬度值在200HBS左右。
(2)测量传动齿轮和汽车半轴的硬度值
传动齿轮和汽车半轴常采用中碳钢制造,组织均匀致密,经最终热处理后硬度相对较高,应采用洛氏硬度HRC测量其硬度值。成品零件的硬度值一般在50HRC左右。
(3)测量滚动轴承的硬度值
滚动轴承(内外套圈)用碳的质量分数较高的专用钢制造,组织致密,硬度较高,其硬度值同样采用洛氏硬度HRC测量。成品硬度应在60HRC以上。
(4)测量钻头的硬度值
钻头一般用碳的质量分数较高的专用钢制造,组织致密,硬度很高,应采用洛氏硬度HRC测量其硬度值。成品硬度应在65HRC左右。
(5)测量表面硬化齿轮的硬度分布
有的齿轮常用低碳钢制造,采用表面硬化的热处理方法,使齿轮表面一层得到较高的硬度,而心部仍保持较低的硬度,以满足其使用性能的要求。可用维氏硬度测量其表面硬化层的硬度值,具体硬度值取决于表面硬化方法。
2.比较硬度大小
几种工件的硬度测量方法并不是完全相同的,应换算成同一种硬度和标尺。以上实例中,可将轴承座的布氏硬度HB换算成洛氏硬度HRC,按经验法进行如下换算。
同一种材料的3种硬度HB、HRC、HV值,在数字上大致呈现下列关系:HRC≈1/10HB,HB≈HV。在进行材料间硬度比较时,若硬度相差较大,可直接近似换算比较。如以上实例就能满足这一条件,即轴承座的硬度值大致为20HRC。比较结果为:轴承座硬度<齿轮硬度<滚动轴承硬度<钻头硬度。
综合训练
1.解释下列名词:
(1)布氏硬度;(2)洛氏硬度;(3)维氏硬度。
2.试说明布氏硬度、洛氏硬度与维氏硬度的试验原理,并比较三种试验方法的应用范围及优缺点。
3.现有如下零件和材料需测定硬度,试说明选用何种硬度试验方法为宜。
(1)高速钢刀具;(2)淬火钢;(3)灰铸铁;(4)仪表小黄铜齿轮;(5)硬质合金。
|1.3 冲击韧性与疲劳极限|
问题提出
1.普通铸铁结构件,在静载荷作用下并不容易破坏,而一旦受到碰撞或冲击,很容易产生裂纹甚至断裂,但钢就不易产生裂纹和断裂。
2.一条普通钢丝,在一点附近的两侧用手捏紧,经少量次弯曲是不会断裂的,但经反复多次弯绕,最后是可以折断的。
以上是众所周知的两个实例,这些现象说明了什么问题?金属材料在不同性质载荷作用下有哪些不同的性能表现?在机械设计、加工和使用过程中如何正确运用?
问题分析
以上两个实例反映了同一个问题,即金属材料在不同性质载荷作用下的抵抗能力是不同的,也就是说表现出不同的力学性能。金属材料在使用和加工过程中所承受的载荷往往是比较复杂的,不仅有静载荷,也有冲击载荷或交变载荷,也可能同时受到多种载荷的作用。因此,必须研究金属材料在不同性质载荷作用下的力学性能和评价方法。拉伸试验和硬度试验都属于静载荷试验,下面对冲击载荷试验和疲劳载荷试验及其相应的性能指标进行学习。
相关知识
一、冲击韧性
1.冲击载荷和冲击韧性
在很短时间内作用在金属材料上的载荷称为冲击载荷。冲床的冲头、锤锻杆、风动工具、锤子等,它们是利用冲击载荷工作的;而在其他很多情况下,则要尽量避免受到冲击载荷的作用,如在刀具的切削过程中以及汽车行驶通过凹坑等。
冲击载荷与静载荷的主要区别在于加载时间短,加载速率高,应力集中,使金属材料的变脆倾向增大,因此冲击载荷对材料的破坏效应大于静载荷。
金属材料在冲击载荷作用下抵抗破坏的能力,或者说在断裂前变形吸收能量的能力叫冲击韧性,它是金属材料力学性能的重要指标。常用冲击韧度来衡量金属材料冲击韧性的好坏,但习惯上,韧性和韧度不加严格区分。
金属的冲击韧性随加载速度的提高,温度的降低,应力集中程度的加剧而下降。冲击韧性试验,就是综合应用较高冲击速度和缺口试样的应力集中,来测定金属从变形到断裂所消耗的冲击能量的大小,即韧性的高低。
2.冲击试验
工程上常用一次摆锤冲击试验来测定材料抵抗冲击载荷的能力,即测定试样在冲击载荷作用下被折断而消耗的冲击吸收能量K,单位为J(焦耳)。
(1)冲击试样
标准中冲击试样有夏比U型缺口和夏比V型缺口两种试样类型。选择试样类型的原则应根据使用材料的产品技术条件、材料的服役状态和力学特性,一般情况下,尖锐缺口和深缺口试样适用于韧性较好的材料。铸铁或工具钢等脆性材料常采用无缺口冲击试样。
(2)冲击试验机
冲击试验机有手动和半自动两种。通过更换摆锤,冲击试验机的标准打击能量为300J 和150J,打击瞬间摆锤的冲击速度应为5.0~5.5m/s。根据需要,也可使用其他冲击能量试验机。
(3)一次摆锤冲击试验

图1-6 一次摆锤冲击试验原理图
一次摆锤冲击试验原理如图1-6所示,试验时,将标准试样置于试验机支座上(缺口背向摆锤冲击方向),把质量为m的摆锤抬升到一定高度H1,然后释放摆锤、冲断试样,摆锤冲断试样后由于惯性继续运动到H2。冲击过程中如果忽略各种能力损失(空气阻力及摩擦等),摆锤的位能损失mgH1−mgH2=mg(H1−H2)就是冲断试样所需要的能量,即是试样变形和断裂所消耗的功,称为冲击能量K,即

U型缺口试样和V型缺口试样的冲击能量分别表示为KU和KV,其单位为J。冲击吸收能量的大小直接由试验机的刻度盘上读出。
用试样缺口处的横截面积S去除KU和KV,可得到材料的冲击韧度指标,用符号αk表示,αk=K/S,其单位为kJ/m2或J/cm2。αk与K相比并没有明确的物理意义,只是一种数学表达方法。所以,现在大多用冲击吸收能量K作为材料韧性的判据。
冲击吸收能量K或冲击韧度αk越大,材料的韧性越好,越可以承受较大的冲击载荷。一般把冲击吸收能量低的材料称为脆性材料,而将冲击吸收能量高的材料称为韧性材料,脆性材料断裂前无明显塑性变形,韧性材料在断裂前有明显的塑性变形。
对于同一种材料,随着温度的降低,韧性材料可以转变为脆性材料,使韧性材料变为脆性材料的温度称为韧脆转变温度。韧脆转变温度决定了金属材料的使用温度。
一般来说,强度、塑性两者均好的材料,冲击韧度也好。
二、疲劳极限
1.疲劳现象
(1)交变载荷和循环应力
工程中许多零件和构件都是在交变载荷下工作的,如曲轴、连杆、齿轮及弹簧等。交变载荷是指大小、方向随时间变化的载荷,其在单位面积上的平均值为变动应力。交变应力可分为规则周期变动应力(也称循环应力)和无规则随机变动应力。
生产中工件正常工作时其变动应力多为循环应力,循环应力中大小和方向都随时间发生周期性变化的应力称为交变应力。例如,轴运转时轴颈上一点的应力大小、方向随时间发生周期性变化;内燃机工作时缸盖螺栓承受的应力大小发生变化,而方向无变化;车轮在地面上滚动时,轮缘受不平地面的偶尔冲击,承受的应力在一定范围内呈无规则变化。轴颈、缸盖、轮缘等承受的应力属于循环应力。
(2)金属疲劳概念
金属材料在受到交变应力或重复循环应力时往往在工作应力小于屈服强度的情况下突然断裂,这种现象称为疲劳断裂。疲劳断裂是金属零件或构件在交变应力或重复循环应力的长期作用下由于累积损伤而引起的断裂现象。疲劳断裂与在静载荷作用下的断裂不同,不管是脆性材料还是韧性材料,疲劳断裂都是突然发生的,事先均无明显的塑性变形,很难察觉到,危险性大,甚至造成严重事故。据统计在失效机械零件或构件中,大约有60%以上属于疲劳破坏。
2.产生疲劳的原因
产生疲劳的原因一般认为是在零件应力高度集中的部位或材料本身强度较低的部位。例如,原有裂纹、软点、脱碳、夹杂、刀疤等缺陷处,在循环应力反复作用下产生疲劳裂纹,并随着应力的循环周次增加,裂纹不断扩展,使零件承受载荷的有效面积不断减小,最后当减小到不能承受外加载荷的作用时,发生突然断裂。因此,零件的疲劳失效过程可分为疲劳裂纹的产生、疲劳裂纹的扩展和断裂3个阶段。
3.疲劳曲线和疲劳极限
研究疲劳问题时,需要测定疲劳曲线。大量试验表明,金属材料所承受的最大应力 σmax越大,则断裂前所经受的循环周次N(定义为疲劳寿命)越小,如图1-7所示。这种最大应力σmax与疲劳寿命N的关系曲线称为疲劳曲线,或称S-N曲线。

图1-7 疲劳曲线
曲线表面,金属材料所受循环应力的最大值σmax越大,则疲劳断裂前所经历的应力循环周次越低。当应力低于某值时,材料经受无限次循环应力也不发生疲劳断裂,此应力称为材料的疲劳极限,用σr表示。通常,材料的疲劳极限是在对称弯曲疲劳条件下测定的,对称弯曲疲劳极限记作σ−1。
不同材料的疲劳曲线形状不同,对于一般低中强度钢,疲劳曲线上有明显的水平部分,疲劳极限有明确的物理意义,如图1-7所示。当σb<1400MPa,能经受住107周次旋转弯曲而不发生疲劳断裂,就可凭经验认为永不断裂,相应的不发生断裂的最高应力称为疲劳极限。而对于非铁金属、高强度钢和腐蚀介质作用下的钢铁材料,它们的疲劳曲线上没有水平部分。这类材料的疲劳极限定义为规定循环周次不发生疲劳断裂的最大循环应力值,称为条件疲劳极限,又称为疲劳强度,记作σr(N)。一般规定高强度钢、部分非铁金属的规定循环周次取108,腐蚀性介质作用下的钢铁材料取106,钛合金取107。
问题落实
(1)金属材料在不同性质载荷作用下的性能表现是不同的,必须对其受力状态进行全面分析,合理确定设计和选材依据。
(2)铸铁的抗压强度和减震性较高,可以承受一定静载荷的作用,但抗拉强度及塑性、韧性非常低,承受冲击载荷的能力也很低,所以,在受到碰撞或冲击作用时,很容易产生裂纹甚至断裂,主要用来制造一些机座、箱体、壳体等;而高碳钢强度、硬度高、耐磨性好,但是塑性、韧性较差,所以多用于受摩擦的零件;相比而言,一般低碳钢的强度、硬度较低,而塑性和韧性比较高,抗冲击能力远远好于铸铁,适用于承受较大冲击载荷的机件。
需注意的是,在实际生产中还要考虑冲击载荷大与小的问题。在大能量冲击载荷作用下,要求材料具有一定的冲击韧度αk;而小能量冲击作用时应提高材料的强度和塑性,不可盲目追求高冲击韧度,否则,会损失材料的强度,反而降低零件的使用寿命。
(3)任务提出中,钢丝所受的载荷为交变载荷,金属材料在交变载荷作用下,尽管交变应力小于其抗拉强度甚至屈服点,但经较长时间作用后仍然可能发生断裂现象。因此,承受交变载荷的机械零件应以疲劳强度σ-1作为设计依据。
疲劳破坏是机械零件失效的主要形式,任何行业都有严格的设备保养、维护和检修制度,对设备进行定期检查、维护和维修,不仅可以保证设备的使用功能、延长其使用寿命,而且,还可以及时检查零件的疲劳损伤情况,防止事故的发生。
综合训练
1.解释下列名词:
(1)冲击载荷;(2)冲击韧性;(3)冲击吸收能量;(4)韧脆转变温度;(5)疲劳极限;(6)条件疲劳极限。
2.试举出几个脆性大和韧性好的材料实例。
3.什么是金属的疲劳?简述疲劳断裂的特点。
|小结|
金属的力学性能是指金属在外力作用下抵抗变形与断裂的能力及发生变形的能力。常用的力学性能指标有强度、塑性、硬度、韧性及疲劳极限等。
一、强度和塑性
强度是金属材料抵抗塑性变形和断裂的能力。常用的强度指标有屈服强度和抗拉强度,分别用σS或σ0.2和σb表示,单位均为MPa。
塑性是金属材料在外力作用下,断裂前产生永久变形的能力。塑性指标用断后伸长率和断面收缩率来表示,其符号分别为δ和Ψ表示。
金属的强度和塑性指标可由拉伸实验测得。
二、硬度
硬度是在金属表面的局部体积内抵抗塑性变形能力,即表示材料的软硬程度。硬度试验方法很多,最常用的有布氏硬度试验方法、洛氏硬度试验方法和维氏硬度试验方法3种。
硬度测试方法简单,可直接在原材料、零件或工具表面上测试,因而应用十分广泛。
三、冲击韧性与疲劳极限
1.冲击韧性
冲击韧性是金属材料在冲击载荷作用下抵抗破坏的能力,一般是通过一次冲击弯曲试验的方法测量的。把冲击吸收能量与试样缺口处的横截面积的比值称为冲击韧度,用符号αk表示。
2.疲劳极限
疲劳极限是指金属材料在循环应力作用下,抵抗疲劳破坏的能力,用σ−1表示。疲劳极限是在循环应力作用下机件的设计依据。