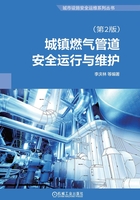
第四节 焊接质量检验
一、焊接缺陷分析
焊接时产生的缺陷可分为外部缺陷及内部缺陷两大类。外部缺陷用眼睛和放大镜进行观察即可发现,而内部缺陷则隐藏于焊缝或热影响区的金属内部,必须借助特殊的方法才能发现。
1. 外部缺陷
(1)焊缝尺寸不符合要求 焊缝的熔宽和加强高度不合要求,宽窄不一或高低不平,这是由于操作不当等原因造成的。
(2)咬边 咬边是由于电弧将焊缝边缘吹成缺口,而没有得到焊条金属的补充,使焊缝两侧形成一凹槽,如图3-12所示。使焊缝造成咬边的主要原因是由于焊接时选用的焊接电流过大,或焊条角度不正确。咬边经常发生在立焊、横焊或角焊的两侧。

图3-12 咬边
咬边的存在减弱了接头工作截面,并在咬边处形成应力集中。燃气管道和燃气储罐的焊缝不允许存在咬边。
(3)焊瘤 焊接过程中熔化金属流溢到加热不足的母材上,这种未能和母材熔合在一起的堆积金属叫做焊瘤,如图3-13所示。产生焊瘤的主要原因是电流太大、焊接熔化过快或焊条偏斜等,尤其是角焊缝更容易出现焊瘤。

图3-13 焊瘤
(4)烧穿 一般发生在薄板结构的焊缝中,是绝对不允许存在的。烧穿的原因是电流过大、焊接速度太慢或装配间隙太大。
(5)弧坑未填满 焊接电流下方的液态熔池表面是下凹的,所以断弧时易形成弧坑。它减少了焊缝的截面,使焊缝强度降低,因此必须填满弧坑。
(6)表面裂纹及气孔 这类缺陷会减小焊缝的有效截面,造成应力集中,并影响焊缝表面形状。
外部缺陷较容易被发现,应及时修补,有时需将缺陷铲(刨)去后重新补焊。
2. 内部缺陷
常见的内部缺陷是未焊透、夹渣、气孔和裂纹。
(1)未焊透 有根部未焊透、中心未焊透、边缘未焊透、层间未焊透等几种类型。未焊透使接头强度减弱,受力时可能产生裂纹。对重要结构,未焊透处必须铲除后重新补焊。
未熔透产生的原因可能是坡口角度和间隙太小,钝边太厚;也可能是焊接速度过大;焊接电流过小或电弧偏斜,以及坡口表面不洁净。未焊透常和夹渣一起存在。未熔合也属于未焊透,其原因是电流过大。
(2)夹渣 焊缝金属冷却过快,一些氧化物、氮化物或熔渣中个别难熔的成分来不及自熔池中浮出而残留于焊缝金属中形成夹渣。多层焊时,前一层的焊渣未清理干净也会形成夹渣。夹渣与气孔一样会降低焊缝强度。
(3)气孔 气孔是由于在焊接过程中形成的气体来不及排出,而残留在焊缝金属内部所造成的。气孔可能是单个存在,也可能成网状、针状,后者更为有害。气孔的存在减小了焊缝工作截面,降低了接头强度与致密性。避免产生气孔的措施是保证焊条或焊剂充分干燥,工件和焊丝没有铁锈、油污等,加强对焊缝的保温使之缓慢冷却。
(4)裂纹 裂纹发生于焊缝或母材中,可能存在于焊缝表面或内部,是最危险的缺陷。裂纹削弱了工作截面,不仅造成应力集中,而且在动荷作用下,即使微小裂纹,也很容易扩展成宏观裂纹,导致结构整体的脆性破坏。因此绝对不允许裂纹存在。
当发现有裂纹时,可在两端钻孔,防止其扩展。然后用风铲或碳弧气刨将它清除干净,重新补焊。
二、焊接接头性能鉴定
1. 化学成分分析
化学分析的目的是检查焊缝金属的化学成分,经常被分析的元素有碳、锰、硅、硫和磷等,必要时还对焊缝中的氢、氧或氮的含量作分析。
2. 金相组织检查
其目的是分析焊缝及热影响区的金相组织,测定晶粒的大小及焊缝金属中各种显微氧化夹杂物、氢白点的分布情况,以鉴定该金属的焊接工艺是否正确,热处理等各种因素对焊接接头机械性能的影响。
3. 机械性能试验
通过拉伸试验、弯曲试验测定焊接接头的机械性能。
三、无损探伤法
对于内部缺陷,可以用物理的方法在不损害焊接接头完整性的条件下去发现,因此称为无损探伤。常用的有射线法(X射线或γ射线)和超声波法等。
1. 射线探伤
(1)射线探伤原理 用X射线或γ射线透视工件进行探伤的原理相同,只是获得射线的能源不同,这两种射线都是电磁波,γ射线较X射线的波长更短。它们都具有穿透包括金属在内的各种物质的能力。射线的波长越短穿透能力越强,所以γ射线具有更强的穿透力。X射线和γ射线都能使照相底片感光。
射线穿透各种材料时被部分地吸收,材料密度越大,射线被吸收得越多,射线探伤即是利用这种不同物质对射线的吸收能力不同这一特点而进行的。
透视时,将X射线源对准要照射的部位,在焊缝背面安置底片。因焊缝有加强高部分,故厚度最大,所以对射线的吸收也最多,底片相应部分感光最弱。若焊缝中有缺陷时,因为缺陷内的气体或非金属夹杂物对射线的吸收能力远远小于金属,所以射线通过缺陷时强度衰减较小。因此底片在有缺陷的部位感光最强。底片冲洗后,可清晰地看到焊缝上相应缺陷部分的黑度要深一些,根据底片上呈现出的较深颜色的圆点、窄条或细线的形状、大小、就可直观地判断缺陷的大小、性质和数量,因此这种方法是很可靠的。
与X射线相比,γ射线探伤除可检验较厚的工件外,最主要的优点是不需要电源,适于野外操作,设备简单轻便,容易移动携带。
射线探伤所能发现的最小缺陷尺寸称为绝对灵敏度;最小缺陷的尺寸占被检工件厚度的百分比称为相对灵敏度。
由于射线在传播时发生散射绕射,所以不能发现尺寸过小的缺陷。当工件较厚时更无法显示微小缺陷。
(2)射线探伤方法 当透视大管径、平板或球形储罐等的对接焊缝时,是以射线中心来对准焊缝中心,底片放在焊缝的背面进行,如图3-14所示。
当检查内壁无法装暗盒的管子或容器的环焊缝时,可使射线以一倾斜角度透视双层壁厚,如图3-15所示。为了不使上层管壁中的缺陷投影到下层检查部位上造成伪缺陷,可将焦距缩短,使上层的缺陷模糊,从而不影响焊缝质量检验效果。

图3-14 对接焊缝的透视示意图
1—射线束 2—前遮铅板 3—后遮铅板 4—底片

图3-15 通过双层壁的透照方法
对于DN<200的管子环焊缝,可使射线一次透过整个环焊缝,在底片上得到椭圆形的影像(见图3-16)。为使底片清晰,可适当加大焦距。

图3-16 小直径管子的透照法
射线探伤时,与射线束平行并具有一定尺寸的缺陷容易被发现,如未焊透、夹渣、气孔等,而与射线束成一定角度的倾斜裂纹或极细小的裂纹则难以发现。
(3)射线探伤的缺陷判断
1)未焊透(未熔合):根部未焊透表现为规则的连续或断续的黑直线,宽度较均匀、位置处于焊缝中心。坡口部分的未熔合表现为断续的黑直线,位置多偏离焊缝中心、宽度不一致、黑度不太均匀。多层焊时各层间的未熔合表现为断续条状,如为连续条状则不会太长。
2)夹渣:多为不规则的点状或条状。点状夹渣显现为单个黑点、外形不规则、带有棱角、黑度较均匀;条状夹渣显现为宽且短的粗条状;多层焊时层间的夹渣是与未熔合同时存在。
3)气孔:显现为黑色小斑点、外形较规则,多为近似圆形或椭圆形,其黑度一般是中间较深,边缘渐浅,斑点分布可能是单个、密集或链状。
4)裂纹:多显现为略带曲折、波浪状黑色细条纹,有时也成直线细纹,轮廓较分明,中间稍宽,端部尖细,一般不会有分枝,两端黑度较浅逐渐消失。
判断焊接质量时,应注意排除底片上的伪缺陷。
2. 超声波探伤
频率高于20kHz的声波称为超声波,是一种超声频的机械振动波。超声波在各种介质中传播时,会在两种介质的界面产生反射和折射,也会被介质部分地吸收,使能量衰减。超声由固体传向空气时,在界面上几乎全部被反射回来,即超声波不能通过气体与固体的界面。如金属中有气孔、裂纹或分层等缺陷,因缺陷内有空气存在,超声波传到金属与缺陷边缘时就全部被反射回来。超声波的这种性能可用于探伤。
当超声波在被检测工件中传播时,碰到缺陷和工件底部就大部分被反射,自工件底部及缺陷处反射的超声波行经的路程不同,故反射回来的时间也有先后之分,据此即可判断该处是否存在缺陷。利用脉冲法探伤不能发现表面缺陷这是它的一个缺点,超声波探伤可测工件最大厚度达10mm。
超声波探伤灵敏度高、速度快、设备轻便灵巧,不用冲洗照片、对人体无害,因此,应用越来越广乏。它的主要缺点是对缺陷尺寸的判断还不够精确,而且辨别缺陷性质的能力较差。因此在生产中与射线探伤配合使用。